Insulation levels in Florida

Hello! I’m designing a home and contemplating energy trade-offs. It’s been a while since I’ve used BEopt but it’s my tool of choice because it’s easy to use in my opinion. The results I’m getting are a little surprising so I wanted to get some opinions. I’m using the EnergyPlus v8.8.0 simulation engine that comes with BEopt v2.8.0.0.
Central Florida, 2600 sqft under air, two-story
Assume I simulated the home correctly and it meets energy guidelines for performance-based submittal (one area may be lacking but overall it passes energy code)
Light-color metal roof, steel trusses, unvented attic, R-30 open-cell spray-foam insulation under roof deck
Steel wall studs with R-20 open-cell spray foam insulation, R-3 continous rigid foam board over sheathing
Low-E, double-pane, vinyl, gas-filled 0.26 U-value, 0.21 SHGC
5ACH50 (I’m kind of ignorant on airflow)
15 SEER heat pump(s)
Getting to the point, I’m seeing really small differences in the annual energy when I change parameters. For instance if I ditch the R-3 rigid foam and reduce the roof spray foam to R-20, I only consume 255kWh/yr more. That’s about $22/yr more. Another example, if I switch the walls from R-20 to R-10 the energy consumption goes up 182kWh/yr ($16/yr).
When I think about the cost savings of cutting the spray foam material in half or skipping the installation of rigid foam, that’s a whole lot more money than the above costs for even 50 years! Am I missing something?
GBA Detail Library
A collection of one thousand construction details organized by climate and house part
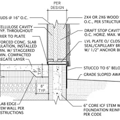
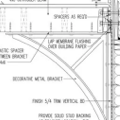
Replies
Indeed, when converted to $, many things turn out to be pretty minor. Make sure you are using whole wall R values. And be much more aggressive about air sealing. I'm curious, what is your conversion process for kWh to $?
Jon, thanks for the reply! I let BEopt calculate the assembly R-values. I got the rates from https://www.fpl.com/rates/pdf/January-rates-residential.pdf, all electric home. Your question got me to thinking more so I looked at https://www.fpl.com/rates/pdf/residential-explanation.pdf and https://www.fpl.com/rates/time-of-use.html discussing "on-peak" and "off-peak". The numbers I posted originally were "off-peak" which is somewhat inaccurate, so worst case it could be another $0.02/kWh or about $5 and $4 more, respectively.
Since you are going to use steel framing the best choice is to put all your insulation outside of the structure then decide how you will cover it.
With a steel structure take a look the local commercial construction sites around town and there cladding choices.
Around here the only contractors that work in steel are the commercial contractors and they expect very detailed plans and do not like any changes. They are proud of their work and command a higher pay. The others build pole barns fast, dirty and cheap. Pick your contractor carefully.
Given your mild climate the payback on expensive spray foam insulation will be very long.
Since you are using BEopt be sure to run “cases” for different insulation levels, windows and SEER HVAC equipment. Be sure to enter your own bid costs into BEopt as they are so often different than the default costs. BEopt will highlight the best option assuming you enter a accurate building model, fuel costs, interest rates, and climate zone.
Walta
Walter, thank you for the feedback. Unfortunately I don't have the unit installation cost data per building component to really maximize BEopts potential (or the patience to input all of that to be blunt!). I am doing parametric simulations though and I use those overall annual energy numbers. I would compare those energy costs to quotes I'm getting but the energy cost differences BEopt is showing are so low it makes adding more insulation look like a pretty poor investment. That's why I wanted a gut check from this community because y'all know building science.
Steel studs are much more thermally conductive than wood. That R20 steel 2x6 wall is really something like R10-R11 after factoring thermal bridging, about the same as a wood framed 2x4/R13 wall. It would do better with just 2" of continuous polyiso (R12) on the exterior and nothing in the stud cavities.
Just as closed cell foam between wood studs is a waste due to the performance hit from the thermal bridging, almost ANY insulation between steel studs is a waste due to the severity of that highly conductive thermal bridge.
To meet IRC 2018 code min in FL on a U-factor basis would take U0.084, or R12 "whole assembly", with the R-values of all layers and thermal bridging factored in. That could be met with just 1.5" of continuous polyiso (R9) over typical sheathing, cladding, & interior finish wall options, no cavity fill. Dropping back to 2x3 or 2x4 steel studs to accommodate the increase in wall thickness with the thicker exterior foam would have negligible effect on thermal performance.
Dana, thanks for the advice. The 2x6 R-20 steel walls in BEopt have an assembly R-value of 11.6 which lines up with what you're saying. The uninsulated 2x6 steel walls (24" o.c.) are R-3.6, so there's an improvement with the spray foam. I definitely like it for air sealing.
There are definitely cheaper ways to air seal a building than 5" of open cell spray polyurethane. Wasting nearly half it's performance potential by putting it between steel framing isn't exactly "green building". Installing R20 to raise the clear-wall-R by a whopping (11.6 - 3.6=) R8 is a pretty dubious way to go.
Instead of fully penetrating 2x6 studs, installing 1x2 or 1x3 omega (or U) steel furring on both sides of a 2x6 top/bottom channel plates (staggered, not aligned) for mounting the exterior sheathing and interior gypsum would deliver much higher thermal performance using the same amount of foam, since it puts about R14 - R15 of thermal break over most of the framing, with only the top/ bottom plates and window & door framing fully penetrating the insulation layer.
Dana, I'm not able to reply directly to your last message about installing sheathing over top/bottom channels. Wouldn't this be a problem with structural sheathing? I can't say I've ever installed sheathing that didn't have fasteners along all edges and in the field into each intermediate stud.
>”Around here the only contractors that work in steel are the commercial contractors and they expect very detailed plans and do not like any changes. “
That’s a little harsh. We commercial contractors are totally ok with $$$$$change$$$$$$orders$$$$$$ ;-) I did recently complete a very small office project, probably not more than 1,200 square feet or so, with 18 change orders! That was crazy. All the trades on the job were talking about it.
Detailed plans are always a good thing though. Commercial projects are big on rigid foam on the exterior due to the steel studs, concrete floors, and steel framing. Any fiber insulation between studs in commercial buildings is usually there for sound control more than for thermal purposes.
You could use wood studs only on the exterior. I’m curious why you want steel studs on a residential project though. Commercially steel is usually used due to fire code issues, residential projects don’t usually have that requirement.
Bill
Bill, yes there will likely be commercial framers working on this house. I like steel mainly for slowing fire spread and termite prevention.
The wall facing you use will make more of a difference for fire control than the material the studs are made of. If you use 5/8” type X drywall everywhere, you will have 1 hour firewalls too — regardless of the type of stud you use. 5/8” drywall will also give flatter, stronger walls and better sound control. Put mineral wool inside for even more fire and sound control. Two layers of 5/8” on each side gives you a 2 hour firewall.
Note that for proper fire control, you need to firestop ALL wall penetrations and use fire dampers in ductwork. Now you really are getting into commercial construction stuff. You’d want automatic closers on your doors too.
My own advice would be to use 5/8” drywall everywhere which has lots of advantages over the usual 1/2” stuff used residentially, and it will add only a small additional materials cost to the project. Labor to finish 5/8” walls is no different from the labor needed to finish 1/2” walls.
Bill
+1
This is good advice. I see a steel framed building with spray foam a much higher fire risk than a wood/mineral wool assembly. Most open cell foam burns much faster than wood framing.
Bill, thanks for the information. I will try to implement some of these firestop recommendations. A major goal of this next house is to prevent and reduce fire spread. I'm far from an expert on fire ratings though. Do you have any literature that explains how 5/8" drywall with wood studs would outperform 1/2" drywall with steel studs? Maybe there isn't data that specific, but potentially there's information about wall facings being more important that inter-stud fire protection.
Matt, likewise is there anything out there to explain why open-cell spray foam is worst than a wood/mineral wool assembly? Spray foam is a very popular product and I've seen it a lot on greenbuildingadvisor.com as well as other sites, but I don't recall reading that there's a downside of increased fire spread risk. Maybe today's products have fire retardants mixed in the foam agents.
“That’s a little harsh. We commercial contractors are totally ok with $$$$$change$$$$$$orders$$$$$$ ;-) I did recently complete a very small office project, probably not more than 1,200 square feet or so, with 18 change orders! That was crazy. All the trades on the job were talking about it.”
It was not my intent to insult anyone. My point is most commercial contractors come to work with a different set of expiations than custom home builders may. My builder did not write change orders but I would guess there have been hundreds on my house.
Walta
For insulation to make a difference you need a temperature difference between inside and outside. In mild places there is just not much delta. Even when it is crazy hot outside, you have at most around 25F difference, going much over R10 makes little difference in energy use.
On the house envelope side, your best bang for your buck is focus on air sealing the house. Decent windows with proper thermal coatings (low SHGC) and most important: shading.
I would also focus on your mechanicals, get your ducts into your conditioned space and get a higher efficiency ERV. In warmer climate a heat pump water heater inside the conditioned space might also make sense.
Akos, thanks for your input. Sorry I didn't see this before. I'm glad to hear you and others confirming what I'm seeing in simulation. I will definitely focus on air sealing and the like.