Insulation in the right location? Air-seal sufficient?
I’ve been lurking on the forum for quite sometime and have spent hours and hours reading posts and comments.
I’m located in Marine 4C in Washington State and we get about 20 inches of rain a year.
We are building a 2000 sqft 2 story and want to have it well insulated.
Our Plan:
Slab on grade with 4 inches of compacted crushed rock, 6 mil poly vapor barrier, 2 inches of R10 pink rigid foam cut at 45* at the footing and going down. Then another 2 inches outside the footing going into the ground 24 inches
Walls will be advance framed 2×6 with (from the inside) 1/2 sheetrock, R23 roxul or blown cellulose, taped OSB, 4 inches of taped polyiso (1 piece, not stacked), WRB (probably Tyvek), vertical 1x4s for a rainscreen, and hardiplank or panel for cladding. Windows and doors will be “Outies”.
1st floor ceiling will be 5/8 sheetrock with roxul SnS to keep the noise transition down a bit.
2nd floor ceiling will be 5/8 sheetrock, 4 inches of taped polyiso (again, not stacked), healed trusses 24″ on center, and R49 blown in cellulose on top.
Attic access will be through a barn door in the gable end and no holes in the ceiling for lights or fans upstairs.
6 Questions:
Is my WRB between the foam and 1×4 rain screen enough? Should I put another layer between the foam and the OSB?
Should I put 1x4s going perpendicular to the trusses upstairs between the sheetrock and the 4 inch polyiso so I dont need such long sheetrock screws?
Do I need to worry about condensation between the polyiso and the bottom side of the trusses?
Do I need to worry about condensation in my wall cavity?
Since I am taping the foam and the osb (Smooth side out) do i still need to seal my framing cavities with ECOSEAL or this thing? http://www.spraysealantsgun.com/
Does this look like a decent design that should be practical and last a good many years?
Thank you for any and all input. This site has been incredible and its great to be with some like-minded people!
Noah M
GBA Detail Library
A collection of one thousand construction details organized by climate and house part
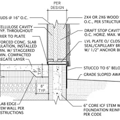
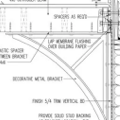
Replies
Noah,
Q. "Is my WRB between the foam and 1x4 rainscreen enough? Should I put another layer between the foam and the OSB?"
A. A wall only needs one WRB. In fact, two WRBs can be confusing, since the workers installing the window flashing might get confused about which housewrap layer is the "real" WRB. Remember, all of your flashing needs to be integrated with your WRB. For more information on this topic, see Where Does the Housewrap Go?
Q. "Should I put 1x4s going perpendicular to the trusses upstairs between the sheetrock and the 4 inch polyiso so I dont need such long sheetrock screws?"
A. That method is called "strapping the ceiling." It is routine in New England, and I think it is a good idea. Don't forget to tape the seams between the sheets of polyiso.
Q. "Do I need to worry about condensation between the polyiso and the bottom side of the trusses?"
A. No. The paint on the drywall and the polyiso itself are both vapor retarders. (Some types of polyiso have foil facing, which is a vapor barrier.) Moreover, the bottom side of your trusses are connected to the vented attic, so everything on the exterior side of the polyiso can dry readily to the attic.
Q. "Do I need to worry about condensation in my wall cavity?"
A. No. The usual advice applies: "Pay attention to airtightness."
Q. "Since I am taping the foam and the OSB (smooth side out), do I still need to seal my framing cavities with ECOSEAL or this thing? http://www.spraysealantsgun.com/?"
A. It's up to you to determine how far to go with your air sealing efforts. No matter where you decide to create your air barrier, conscientious application of your details is more important than where you put the air barrier. The best way to meet an airtightness target is to use a blower door. If the blower door result tells you that you've met your target, you're done.
Q. "Does this look like a decent design that should be practical and last a good many years?"
A. Your approach is well above average for Climate Zone 4. In fact, some observers might question whether the measures are all cost-effective. That said, if you want above-average details, and can afford to do it, all power to you. Good luck.
Noah,
Concerning your slab insulation details: Your description is a little unclear. For guidance on insulating slabs, see this article: Insulating a slab on grade.
Note that most green builders try to avoid the use of XPS, since XPS is manufactured with a blowing agent that has a high global warming potential. For insulating a slab, EPS is a better choice. For more information on this issue, see Choosing Rigid Foam.
A couple of things:
Expanding on Martin's comments, 2" of pink foam is R10 when performance is averaged over a handful of years, but isn't guaranteed to be more than R9 in 20 years, and in fact will eventually drop to R8.4 as it's climate-damaging HFC blowing agents leak out. Using 3" of Type-II (or denser) EPS would be R12.6 now, and R12.6 in 50 years, and is blown with low-impact pentane (most of which is recovered at the factory), not HFCs, and should run about the same price as 2" of the pink stuff.
Like the R49 attic, R10 of slab edge insulation to 24" below grade would be CODE MINIMUM (= the crummiest performance that is legal to build), which seems at odds with "...want to have it well insulated", and nowhere near the 2x+ performance upgrade that 4" of polyiso on the outside of the 2x6/R23 wall represents.
There is probably better economic to pouring the stem walls in an R20-ish (2.5" + 2.5" EPS) insulated concrete form, and dialing back the wall sheathing foam to 2" (which is still roughly 2x code-min performance), and shooting for R60-R65 in the attic (which a fairly small up-charge from R49.)
You haven't mentioned windows, but with the described house (or even the mere 2" polyiso revision) windows will be dominating the heat loss numbers. A code-min U0.32 window can be upgraded to the low U0.20s reasonably economically by specifying a double low-E argon fill double pane with a hard-coat low-E coating on surface #4, and a reasonably high SHGC coating on surface #2, with a final SHGC > 0.5 (most code-min windows are about SGHC 0.3), and a final U-factor <U0.25. This will be a much greater an more cost effective upgrade than fattening up 2" of exterior polyiso to the proposed 4".
Though there are others, one such example would be Cardinal's LoE 180 on surface #2, with i89 on surface #4, with ~1/2" of argon between the panes, which comes in at about U0.21, a 33% reduction in heat loss relative to a code-min window, but a net heat gainer due to the SHGC of ~0.6, about twice the typical code min window. This makes them net heat gainers even on "bright clouds" days, even on north facing windows.
http://www.cardinalcorp.com/source/pdf/Technical_Glass_Guide_Web.pdf
From an overfall financial sanity check point of view, see the Zone 4 & 5 rows of Table 2, p10 of this document:
https://buildingscience.com/sites/default/files/migrate/pdf/BA-1005_High%20R-Value_Walls_Case_Study.pdf
Note, those are "whole-assembly R" numbers, not center cavity. Your AF 2x6 R23 wall is about R15 whole wall, before you add in the R13 for 2" of polyiso, or R26 for 4". So even 2" would put you between the recommended R25 for zone 4 and R30 for zone 5.
Also note, the recommended R7.5 slab-edge recommendation in Table 2 for zone 4 is actually below IRC 2015 code-min R10 for Marine zone 4C:
https://up.codes/viewer/utah/irc-2015/chapter/11/re-energy-efficiency#N1102.1.2
In foggy-dew zone 4C you'll still want to go with the 0.5-ish SHGC recommended for zone 5, whereas you wouldn't in sunnier climes. You may want to tune that a bit with the surface #2 coating, but you really do want to let the sun help you out during your cool (but not really cold) 9+ months of heating season. Simulating the whole thing with BeOpt would be a good idea.
Wouldn't it be easier and a lot cheaper to skip the polyiso above the ceiling and just use more cellulose? Screwing drywall through 4" of foam will be a monumental bother, I should think. And a quick search showed 6" drywall screws are 30 cents each. I'd just increase the heel if you need more room to get to R70 with cellulose .
Stephen is right, of course! (I'd somehow spaced out on the 4" polyiso above the ceiling gypsum!) The additional performance of the R25-ish polyiso cost 3-4x as much as adding more depth to the cellulose for the same performance level.
The BA-1005 document's recommended R60 whole-ceiling-R for zone 4, which can be met with cellulose at 17.5", settled depth, 18.5-19" initial depth, so you're looking at a 20" energy heel to hit that mark. The cost adder of going to a 22" or 24" energy heel for R75-R80 (after settling) isn't huge, but might not be "worth it" in the end, depending on the actual performance goals, since even a nominal R50 with buried truss chords is already a decent performance level. Spending that money on other aspects is probably going to work out better.
There's nothing particularly environment-friendly about rigid foam, even if it's blown with low-impact blowing agents. Where it's cheap and easy to design it out, it arguably should be. Displacing rigid foam with more cellulose in the attic is a bit of a no-brainer, whereas designing it out of the wall sheathing can be more expensive and/or harder to build.
Even 2" polyiso sheathing is easier to build than 4" polyiso sheathing. If you are still shooting for higher performance than 2x6 AF/R23 + 2" polyiso, dropping back to 2x4 AF framing with 2" polyiso sheathing and adding insulating edge strips to the interior side framing to accommodate the 5.5" depth of the R23 can still get you most of the way there with a fraction of the foam:
http://www.finehomebuilding.com/membership/pdf/9750/021250059.pdf
I already have all the polyiso. I'm a roofing contractor and it came off a commercial building. I figure I might as well use it on our new house.
Noah,
Remember, to use the 4-inch thick polyiso, you'll need to have studs that are 4 inches longer than usual -- unless you like low ceilings.