Insulation/framing detail questions for outbuilding

[For most recent questions that haven’t been answered, please skip ahead.]
Hello, all. This is my first post here. Not a builder, not an architect, not a scientist–just somebody who has been involved in six years so far of renovations and is gearing up for more punishment, and hoping to do this round well.
I’m intending to build a small outbuilding in my yard, south facing window with overhang, with a couple of layers of rigid foam tightly affixed to the exterior, caulked at seams, etc.. In Minneapolis, where I am, any shed that meets zoning requirements, and that’s less than 120 sf, doesn’t require too many additional expenses or hoops to jump through (I’m looking at ~96sf). The problems will mostly come down to my own skills, combined with the level of my comprehension of how to do this properly.
Rather than deal with the expense, energy, and potential moisture issues of a full concrete foundation, I intend to put this outbuilding on posts set on footers that go below the frost line. While I think I have a fair grasp on continuous insulation and vapor barrier to the walls and ceiling (don’t hold me to that, since I’ll probably come back with questions) I am scratching my head about the floor.
How do you imagine I deal with the issue of effective insulation and thermal break below the floor joists and where the posts affix to the frame? I am stumped. Am I going to need to stagger floor joists with a layer between, similar to the walls? That would seem odd. How is this floor supposed to be composed? At some point I’m not sure how I avoid piercing that outer layer, combined with some amount of continuous framing, in order to bear the load properly.
Thanks,
Minneapolis Disaster
GBA Detail Library
A collection of one thousand construction details organized by climate and house part
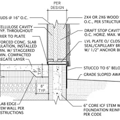
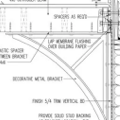
Replies
Hi Jon.
If I may ask, what are you using this out-building for?
Will it be heated?
My intention is for it to be a usable room/workspace (for someone who makes jewelry, including the occasional resin pours where she wears a ventilator and needs a sealed room). I hope for it to be well-enough insulated that I can get by with occasional heating only if it's really necessary. I get great sun on my property in the winters, and hopefully if I have sufficient thermal mass inside the space for heat collection I can see how that works out for keeping the room comfortable. But, I'll run power out to a subpanel there, and if I do need to add and use a small heating source to help out, I'd be disappointed, but I could do it.
AJ, sadly, this will be on a slope, so unfortunately your solution, which otherwise sounds pretty nice would mean building up a lot of gravel to the uphill side of a retaining wall.
Jon, I set small buildings on top of gravel that replaces any soil. In my area that kind of building needs no footing. And high winds are rare. So my way you could insulate over your pressure treated joists, then add plywood on top. If detailed right you could have wall foam meet floor and roof foam. Some kind of ACH ventilation mandatory.
What is the building use?
Do my solution with the posts. I may draw this up on Sketchup just for fun. Have an email?
...Nevertheless, the answer is to put the rigid insulation layer between joists and subfloor, then?
Is that solid enough? Glued and screwed to ... 4"+ of foam? That seems surprising. What am I missing?
Also, in terms of horizontal orientation of the floor to the walls: is it unwise if I set up the rim joist to be flush with the outside layer of wall insulation, so I can caulk/tape that bottom seam, affix the spacer rainscreen layer to both, and bring the siding just below that seam, so I can avoid devising some sort of metal flashing to go over the rim joist?
At only 8'x8' I don't think you'll see a huge potential for thermal inertia so i would look at a a very well insulated space as a suspended pole barn wrapped in foil and non-foil polyisocyanurate foam. With resin casting you are going to want to be very serious about a vent hood and make-up air. for heat I'l get one of those little under desk electric space heaters and you'll want to give serious thought about summer cooling too.
I have an overview of these types of buildings at my web site http://www.chandlerdesignbuild.com/files/PoleBarnOutbuildingsDetail.pdf but the key is that you will find it easier and more resource efficient to build up your posts with a core of 4x4's that need only reach to a couple of feet above the floor and from the footers up you wrap them with 2x4s and 2x6s lay on your band girder and sub floor, build up the foam on top of the subfloor, a alyer of non-foil poly iso and a layer of foil poly iso followed by strapping and finish floor floating inside the exterior wall. once you get back above the foam layer you wrap the 4x4s with non-treated 2x4s and 2x6s to the level of the top of wall header. these posts can be hollow down to the level of the tp of the 4x4's about 3' off the floor so you can use them for wiring chases. With an 8x8 building you will likely need no more than a single post at each corner if you tape you'r foam carefully and use applied rafter tails (or strap your roofing on 2x4's that create your overhang above the foam) you could theoretically have these four 3.5 x 3.5 penetrations as the only break in the thermal envelope.
I have layered tongue and groove 3/4" plywood subfloor over foam. We didn't glue it but you could if you used compatible glue. Some foam and some glues don't mix. So, two layers of 2" foam taped is what you are looking at for the floor? As to structure it is not a code built home so, since I know it works, I have no problem suggesting doing the detail this way. You could have 2" sleepers over the joists so that you are screwing plywood to wood directly, but I don't think it is needed. I also think joist spacing could be more or less depending on if any heavy items are going in the shed. I go to 12" and have driven vehicles into such spacing. For just kids, 24" works and saves time and money.
What roof shape are we drawing? shed or gable ends and 5x12 pitch, or barn or? Do you have some windows picked out, size? How about doors and locations?
96sqft.... sounds like 8x12 with the 12' side facing south? Where is the slope?
Will draw this up tonight most likely.
Michael, great presentation of your work. Looks to me like an order of magnitude larger budget type of build though for what this thread is possibly to do with.
What is our budget anyway Jon?
Summer cooling in Minneapolis, for a small outbuilding? That seems nuts to me. I would think you could have a couple of open windows and be fine.
Thomas, good idea, this place is perfect size for a thru wall AC unit that also provides heat and mixes in ventilation air. Great idea. Best install price and lowest utility cost. The foam all around will make it easy to heat or cool.
Venting, heating, cooling. Three birds, one stone. And yes add a great hood system if the work being done requires it. Put in two multi gas detectors alarms not just one for back up safety. Also think about fireproofing the foam, drywall interior or plywood or something on walls. Roof and floor will have be outsulated so should be OK.
Thank you all, this is great. A couple of details, as I try to catch up:
My budget: with some help from craigslist and a little patience, I'm hoping for <$2k or so. I think I can do well under that, with the big wild card of course being the windows. The hassle of getting the electric run in a trench.... ugh... fortunately my neighborhood association has a tool rental budget allocated for every address.
Size and orientation:
================
You're correct, AJ, I'm thinking 12x8 with a long side facing south. Roof slopes up to the south, not sure precisely of the best angle offhand for Minneapolis sun penetration in the winter, maybe 2/12? I'll have to check. 8'h wall on north side.
Door: east side, inswing, and storm door (outswing) w/ glass or screen (winter/summer). There's the cross-ventilation, in conjunction with these:
Windows: two or three casements to south, depending upon what I find. I've been reviewing the triple-glazing threads--thanks so very much to this forum for those.
Ventilation:
========
If we're not talking about a moisture issue (which is a discussion above my head) but rather air quality issues related to the resin work, I am thinking occasional cross ventilation from the window and door after the pour should be sufficient. I am betting that with resin work once every couple of weeks, where it's important to not have anything blowing around and ruin the finish layer, we're looking at having no mechanical ventilation during that time (but wearing a good mask). That's how it's done now--sealing under the doors of a small room, putting on the ventilator, wiping the room down, and getting to work. So, in this outbuilding I'd assume that'd mean do the pour, leave the room alone for the setting period, and then open a window and a door for five minutes to cross-ventilate the whole place and it'd basically be all clear.
The stuff gets baked in an electric toaster oven; I figured I'd just give that its own circuit.
Cooling:
======
If you haven't spent time here, you could be surprised, but it can get pretty hot and humid here in the summer--90s and high humidity for long periods. I've never put in a wall unit. With a wall unit in, wouldn't I lose the benefit of all this sealing? Don't know how I'd put a window unit into a casement.
Heating:
I'd hope that the electric space heater mentioned above, for a few minutes to start up the day in the winter, would be plenty.
Roof: we have a heavy snow load here, 2x10 on 16? will check. South overhang depth: not sure, will check.
Thank you again for the input, everyone.
Just wondering how much fresh air will be in this little building. Sounds like it might get stuffy to me.
Having spent a little more time looking around, I think I have a better sense of what you're talking about, as far as the unit to handle heating, cooling, and sufficient air exchange to keep the room from being stuffy.
What kind of leakage will I expect, having a through-the-wall system installed?
Revising budget accordingly....
Jon,
You have several options, including:
1. Install posts and girders. Then install joists on top of your girders. The insulation (installed between the joists) will be on top of the girders, without any thermal bridging through the posts. Be sure to do a good job of air sealing when you install a layer of plywood on the underside of your joists.
2. Install posts and girders. Then install a SIP floor.
Mr. HOLLIDAY, Are girders like beams or something different? I have heard the word but don't no what it means exactly.
Thank you, Martin, much appreciated.
However: I'm still confused about the detail at the intersection of the floor and the wall for continuous insulation--
specifically because I'm not clear how you can affix the walls to floor-on-joists to posts-and-girders securely while having continuous insulation to the exterior of that wall and floor.
Vertically speaking, girders under plywood sheathing under polyisocyanate under joists-and-insulation under subfloor, I get.
But can you describe the area inward from the rim joists, and where the wall affixes, to maintain the continuous insulation?
This is where the "beginner asking questions to experts" part comes back to bite you.
And thanks again, great site.
Jon,
You're not building a Passivhaus building, so I think you are overthinking the thermal bridging problem.
Yes, there will be a few thermal bridges near the bottom plates of your walls. I don't think it matters.
If you really want a super-duper-superinsulated shed, you can build 12-inch-thick double 2x4 walls, and fill the walls with blown-in dense-packed cellulose insulation. That solves your thermal bridging through the bottom plates.
You'll still have thermal bridging through your 3/4-inch plywood subfloor, and through the ends of your joists. If these details bother you, you can build a foam box -- there are various ways to do it -- but these high-tech details aren't usually used for a backyard shed.
Fair enough! Thanks!
.
Hi again. Spring is finally here and I'm hoping to get rolling on this in the next few weeks. Question:
Can you confirm or deny what I can expect from a couple of layers of lapped and glued polyiso boards to the exterior of the studs (plus more on the ceiling) --bear in mind this is an approx 8x16 outbuilding:
1. [ ] yes / [ ] no -- I won't need Tyvek to the exterior;
2. [ ] yes / [ ] no -- I won't need OSB/plywood to the exterior for lateral stability if the polyiso is adhered at studs and plates (and with gypsum eventually on interior of studs too);
3. [ ] yes / [ ] no -- the 1x strapping for the rainscreen and my siding will actually hold safely on the 6" of polyiso, since I don't foresee getting really long fasteners to try to hit the studs.
Thanks!
MD,
You overestimate how dense or strong polyiso is. It's foam, and can't be used structurally, either to brace a frame or to hold screws. Builders using the REMOTE or PERSIST method have installed 6" polyiso and driven very long screws from the outer furring into the studs. It's certainly something of a challenge to find the studs this way. That's why Martin suggested doing a double frame with cellulose insulation. This is much more cost effective than very thick foam insulation.
Minneapolis,
You've got to brace your walls with something more than drywall. If you aren't bracing your walls with plywood or OSB, you need to install diagonal let-in bracing or metal L-profile or T-profile strapping.
Glad I put up those questions. It was starting to sound like magic (which is why I asked). Perfectly willing to brace it normally.
Double stud wall with cellulose sounds great if I can find someone to dense-pack it reliably and affordably. The polyiso approach had the benefit of being something I could do myself. Looks like I have more reading to do.
Thanks again!
Hi again.
I'm disappointed to say I haven't found an especially competitive quote yet for dense-pack cellulose so I'm going to give the polyiso with long screws a shot. Looking forward to trying it even though I'm sure my neighborhood is going to learn a lot of new curses from me.
Question: If I set a portion of this outbuilding (approx 3' of the uphill wall) into a slope and backfill with gravel, how does that change my framing needs, and my extra moisture barrier needs? For one thing I know I'll have plywood there, but beyond that:
- The wood framing for foundations link Martin has shared in the past advises 2x8 16" o.c. but that seems like it's dealing with a much heavier load; I was figuring 2x8 24" o.c. but if I can use less lumber safely (2x6s) I'd prefer it. Any advice before I pick up the Advanced Framing book from the library?
- I've got quite a lot of a roll of roofing paper left over here from a couple years ago; if I'm applying two 2"+ layers of rigid foam to the exterior of the plywood bracing, will the paper to the interior of the foam on that side be beneficial? Or, plastic sheeting lapped and caulked? Or, will this be redundant?
Minneapolis,
1. Anyone planning on using lumber and plywood below grade needs to be very familiar with requirements for pressure-treated wood foundations. The basics: very good drainage is essential, with lots of crushed stone on all sides, and plenty of perforated drainpipe leading to daylight; all fasteners must be stainless steel.
2. You can't use polyisocyanurate below grade, so if your plan includes below-grade insulation, you should use EPS.
Noted. Thanks.
Although--with the EPS (and plastic sheeting or roofing paper?) to the exterior--I certainly hope that for the part of the wall assembly below grade, I won't actually need pressure treated studs and plywood since I should have an effective moisture barrier (I'd hope). Correct? The floor seems like a different matter and should be treated. Am I wrong?
Minneapolis,
All of your below-grade lumber needs to be pressure-treated and fastened with stainless-steel fasteners. That certainly includes any studs and plywood that extends below grade.
Neither polyethylene nor asphalt felt will prevent below-grade water from migrating to your plywood. If you want a full waterproof layer below grade, that's possible, but it will require a peel-and-stick rubberized asphalt membrane like Bituthene, plus a dimpled drainage membrane like Hydroduct. Even if you install such a waterproofing system, you still need to use pressure-treated studs and pressure-treated plywood below grade.
Will do. Thanks, Martin!
Hello again.
This question of mine from 1/31/11 is still eating at me:
"I'm still confused about the detail at the intersection of the floor and the wall for continuous insulation--
specifically because I'm not clear how you can affix the walls to floor-on-joists to posts-and-girders securely while having continuous insulation to the exterior of that wall and floor.
Vertically speaking, girders under plywood sheathing under polyisocyanate under joists-and-insulation under subfloor, I get.
But can you describe the area inward from the rim joists, and where the wall affixes, to maintain the continuous insulation?"
--Still driving me nuts. I'm not doing the cellulose. So, how the heck do I align the walls to minimize or eliminate bridging when exsulating, while still lining up the load to bear properly?
Is it ridiculous if I just lap the EPS down to be adhered over the entire face of the rim joist, and call it good?
Minneapolis,
Just build it conventionally. Your subfloor covers your joists and rim joists. You build framed walls, with the bottom plates over the rim joists. You frame your roof -- without any roof overhangs, if you want a perfect envelope. Then you install rigid foam on the exterior of your wall framing and roof framing. Walls can have plywood sheathing or no plywood sheathing, your choice -- use metal strapping for bracing if you don't have plywood. Roofs need plywood sheathing. The rigid foam on the walls extends down below the rim joists to meet the rigid foam which you installed under your floor joists.
Minneapolis,
You may be beyond the point of deciding which wall assembly to use, but if not... It took me awhile, but eventually I did find someone who would rent me a cellulose blower with umph to dense-pack. The extra cost may not be worth while with the small building you are proposing.
But here's another thought, if cellulose insulation appeals to you. Purchase extra netting that is used to contain the cellulose, and drape it horizontally at a couple of different levels within the double stud walls, to help support looser cellulose insulation. Then pack the insulation as densely as you can with the Lowes or Home Depot-type blower. Not sure how well this would work, but might be worth a try.
Thanks, Martin and everyone.
Plan for floor assembly/EPS/vapor barrier attached.
It looks rudimentary but I hope it's readable.
All plywood and studs treated, all seams taped.
Since this will be my first project like this:
- Any obvious omissions or failures?
- Any waste/redundancies?
Thanks in advance.
Minneapolis,
The joists should sit on the beam, and the rigid foam should be attached to the underside of the joists. I don't recommend installing any rigid foam between the joists and the beam.
You need a trim board under the bottom of the wall foam to protect the foam from reflected UV light and ants.
That sounds easier and more stable. Thanks, Martin. Will do on both counts.
Two quick follow-up questions:
1) Poly/Tyvek immediately to exterior of plywood subfloor/wall sheathing makes sense?
2) Will I want plywood underneath that bottom layer of foam, too (for reflected UV and ants)?
Minneapolis,
Q. "Poly/Tyvek immediately to exterior of plywood subfloor/wall sheathing makes sense?"
A. If that's where you want your WRB, fine. Use Tyvek, not poly, and detail your flashing to the WRB. Some builders prefer to put the WRB on the exterior side of the rigid foam, or to use the rigid foam as the WRB; all three approaches can work if detailed correctly.
You don't need poly or Tyvek under your subfloor, however. Just install your subfloor with adhesive, and do a good job of air sealing the rigid foam.
Q. "Will I want plywood underneath that bottom layer of foam, too (for reflected UV and ants)?"
A. Yes, some type of protection -- plywood or OSB.
Sounds good. Thanks.
Appropriate adhesive:
Is a thick bead of PL400 acceptable for this exterior airsealing task (in addition of course to the seam taping)--both for wood-to-wood and for EPS-to-wood and EPS-to-EPS?
Or is there another adhesive that is more appropriate?
Minne D,
A good place to get decent unused windows on the cheap near Minneapolis is http://www.cannonrecovery.com/.
For a conditioned space I would avoid reusing older salvaged windows. Leave those for garages.
Thanks, J Chesnut. Yeah, I picked up six double-hungs at BMO for my last big project. For this one I might be checking there for a door.
As for windows, it looks like I'm ordering a single Cardinal 180 awning window new for this project and that'll be it. Tough to balance cost vs effectiveness but I guess it looks like it'll probably be a Integrity.
I'm posting a revised floor detail with two new questions:
1) to sew up the floor insulation question hopefully once and for all, when I figure the overall R-value for the floor, if I have 7" of rigid foam between joists foamed in, and I figure R1 per inch of wood, for R8 at those joists (ply on both sides) and something just under R35 for the foam, do I basically come to the conclusion that this floor will be good enough without the pain of adding even more foam below it? Because the interruption of the beam discussed below in (2) makes me even less excited to add it.
2) Load: I'm running 6x6 or 6x8 beams across three footers each about 8' apart. At the bottom of this slope, I'm using existing footers for my fence at the top of a retaining wall, and setting the beam across the top of the existing posts that I'll be cutting short (probably only 4" tall or so). This means that the shed will sit across the beam right under the plate at the top of the slope, but past the beam by a foot or so at the bottom (see illustration). Any reason to worry about the load path?
Hi again.
Corner bracing: does plywood in the corners for bracing follow a rule of thumb for how far it should extend?
Full sheets, every corner?
Top plate to bottom plate at the width of a 4' sheet?
All corners of each wall? Opposite corners of four walls? All corners of two walls?
One corner each of two walls?
How much bracing is good bracing so walls don't rack?
This is the 1st time I have read this thread. How often will the shed need to be heated and cooled. Is it used every day, once a week, couple of time a month? I am thinking the embodied energy will exceed the energy saved. How long would you use the shed for this purpose 10 -15 years. The next owner would use it as a garden shed and not heat/cool it.
For ac have you considered a portable unit, not a window ac but a unit that uses a tube put through a window or other opening. The unit itself is inside
Its a little late at this point but given that could laminate I beams/floor joists have been used. Another option would be a floor truss which could also be stood up for wall. Either option would minimize thermal bridging.
A guy could dense pack the insualtion with a rented machine. Not something I wouldnt want to do with a house or larger building but could be done on a small building.
For construction I would picture a shed of the type that is built on skids but in this case beams/girders which ever term you want to use. Normally the bottom of the floor joists are not closed in but in this case closed it in to allow insualtion.
Hi Robert, thanks for writing. Yep, even though this workshop/outbuilding will probably be used almost daily, it's probably true that --since it's new construction-- the embodied energy will exceed the energy saved, compared to me making the space to seal off a room in my existing basement and putting a ventilation system in there for the resin pours so that we don't have to breathe it throughout the house.
But, since the outbuilding is underway and there are stacks of unused polyiso sitting at a nearby lumberyard waiting for me, and I'm interested in learning how to do this by actually doing it with tips from more experienced people, I hope you'll understand.
If you're interested in weighing in on more recent details to minimize extra plywood and lumber usage (corner bracing, ceiling/roof assembly) and other questions that I'll undoubtedly have, that's great. Any thoughts on post #46, from 8/19/2011?
For your little shed use let-in metal bracing or do the same with a piece of lumber. Normally both ends of each wall. I would use some free scrap metal lumber banding if trying to go low cost.
Search let-in bracing. Go to Lowes and browse the building books. There are books dedicated to just building a shed. They sell plans too.
Airline ticket and cold IPAs awaiting.... Have framing guns will travel.
Hi. New question. Since making the box isn't the hard part, but detailing the connections to that box through/around foam is a little confusing--I have a question about the roof connection. Regarding that sandwich of rigid foam between the ceiling joists and the rafters in the roof, and how the two connect:
Since the top side of the ceiling joists of this box are going to be covered with several layers of rigid foam, can I lay sleepers (affixed with long screws) across the top of two of the edges of that foam, to affix my rafters for the roof? Will that be stable enough, sitting on approx 7"-8"of foam? Is there a better way to detail it so I can stack another layer? Any thoughts on this detail would be great. Think heavy snow load. Thanks in advance for your input.
MD
I dont fault you for moving the prduction out of the house and never implied that you should have it in the house.
When I talk of embodied energy I am speaking of the energy to make the insualtion.
Fiberglass insulation requires high temp furnaces to create the fiberglass. Foam insualtion products are petroleum based so in addition to the energy used to manufacture they are also made of petroleum. Embodied energy would also include energy to mine or extract raw material as well shipping of raw materials and finished products.
Cellulose is a recycled material. It is usually produced near where it is being used so shipping embodied energy is low.
Unless you are getting recycled foam it will have a high embodied energy content. Cellulose will have a much lower embodied energy content.
Robert, understood and agreed. Based on what's up with this foam, I don't feel bad about using it.
Any thoughts on a stable ceiling-to-roof connection, when they are separated by a few layers of foam?
---------
Hi all. Currently, my plan is to frame the roof as though the roof itself is a freestanding post and beam structure, and secure its posts to the sides of the exterior wall foam on the exsulated box that is the shed. The posts will sit right over the piers. So, the box is basically going to be hugged by four posts, and 2x12s.
On the plus side, this should bypass the issue of wondering how to secure the roof assembly to the ceiling assembly without worrying about compression or racking in high winds, but on the other hand, it seems extraordinarily lumber-heavy and redundant to set up four posts and cross beams to the outside of a box that should be able to handle the load of a stiff roof but for the connection problem that's been bugging me.
So, as usual, sound counterproposals for the roof connection issue are welcome. Thanks
Just a quick bump to say many thanks to all who have weighed in, on and off the board, so far. Nice meeting some of you.
We had a wall-raising party last Saturday morning. Currently, the wall framing and ceiling joists are up, and our polyiso boards are stacked and waiting for us here in the yard: walls will have a total of 5.5"--a layer of 3" and a layer of 2.5". I think we've got 9" in three layers ready for on top of the ceiling.
The floor assembly is built with 7" polyiso inside, sprayfoamed tight and adhered shut, with 1.5" pink foam board & treated plywood beneath.
I ended up ordering a few rolls of 3M 8067 yesterday--shipping FedEx even though 3M is here in town (nobody seems to carry it, nor most others I've asked about).
I'm still going back and forth on my roof connection decision--a not-insignificant detail. I hate the idea of perforating a nice neat stack of insulation on the roof with framing to hold the roof on. I could do a freestanding roof structure over it instead, but we're right up against the maximum height allowed by ordinance. Without the ordinance, I'd do the clear span solution and not think twice about it. But the girders under the rafters may just add too much height that way.
That aside, although it's going slowly because I'm a novice building evenings and weekends, and I really need to get some scaffolding over here, it's been a good learning experience so far. Thanks, everybody, for allowing me to pick your brains and try this out for myself. Eventually I'll see about putting up a picture or two.
One day into getting these walls covered in two layers of polyiso, let me just say: man oh man, do I ever wish we'd gotten it dense-packed with cellulose instead. It's an adventure! Next time.
MD,
Could you elaborate on your experience installing polyiso, and why you wish you'd chosen to dense-pack instead?
Hi, TJ. Sure. It'll be brief.
First, as far as the implementation goes, I'm spending a lot of time up high, fussing around with the exterior. It's a longer drop to the street than I'd like.
Second, it's frankly disgusting. I don't like having polyiso shavings and dust in my garden--I eat from these beds--nor do I enjoy dealing with various adhesives and spray foam more than necessary. It's true I would have had to deal with fussy sealing and adhesives to the interior at some point, but if nothing else, again, it's not a very tough fall off a ladder to the interior.
Third, even with a good deal on the polyiso, it does appear that dense-packing to the same R-value would have been cheaper. At the time I was calling around for bids, I wasn't getting very convincing responses that I would have gotten a competent installation, but since that time, a few members of this forum who are local to my area have worked with a dense-pack installer and I trust they vetted that installer well.
The proof will be in the pudding--I'll know better what I think of it when it's all buttoned up--and maybe I'll be happy with the airtightness and comfort level. But with the benefit of a little hindsight: although I was looking forward to the hands-on experience, I probably would have been happy to have paid out slightly less and have both materials and install taken care of in the deal.
Hey Jon,
I thought this was a good thread.
I bet you are glad this is just a small simple structure.
Buildability matters.
Yep! Thanks, John.
Important progress report from my co-builder, as we gear up to put the roof on this weekend:
"A school bus full of kindergartners just stopped in front of the hut as I was working to ask me if I was building a playhouse."
https://fbcdn-sphotos-a.akamaihd.net/hphotos-ak-snc7/s720x720/388504_10150361139396331_525716330_8629682_985936925_n.jpg
Just popping in to reaffirm John Brooks's "buildability matters" upthread.
Very glad these braces for the roof assembly are up on either end--they took nine people to move and set upright on the beams, right over the piers.
As I think almost every day: next time, I'd do cellulose (in this case, as pertains to trusses).
As I expected to happen sooner or later, as I was leaving for work today the building inspector came by to check on things following an anonymous complaint (from my next door neighbors). The dude has inspected a lot of my work over the past few years. Not only did he declare my work fine after examining it (in terms of zoning) and checking my permit and zoning papers, but he signed off on my basement remodel and my pergola. It ended up being very convenient. I'll have to thank my neighbors next time I see them.
Concrete floors can cause mold so that is a valid concern. I have been in houses that were constructed too fast after the pad was poured and it was actually humid in the house. I recently built a smaller shed but I put the shed foundation on concrete piers so that it would be high and dry. I did a video on my website about how to build a shed foundation. http://newbuildingideas.com/how-to-build-a-shed-foundation
I hope this helps someone. ~Blessings.