Insulation Decisions

Zone 5-Coastal CT
Based upon my research here, talking with an energy consultant, talking with the contractor and the insulation contractor, I think I’ve come up with a modified insulation plan for my 1850’s major renovation. Of course the contractor and the insulation company wants to SPF the whole place. Huge money!
I’d appreciate any input anybody has on my plan.
1) Exterior walls-old nominal 2×4’s filled with CCSPF. Henry’s Blueskin over sheathing with attention to air leakage. Exterior insulation ruled out.
2) Attic 1 and 2-Vented-1″ CCSPF on attic floor and more in eaves below baffles. 16″-18″ blown cellulose on top. Seal all attic floor leaks first.
3) Attic 3-Conditioned for equipment on 2nd floor-6-7″ CCSPF to cover 2×6 rafters.
4) Basement conditioned, old and new concrete walls and floors- Dri-core floor 1″ from walls. 2×4 framing 1″ from walls. 1″ CCSPF on all walls and filling rim joists. 4″ FG batts in 2×4’s.
I’m still struggling with the new 2×6 walls and new flat roof areas.
Thanks
Nick
GBA Detail Library
A collection of one thousand construction details organized by climate and house part
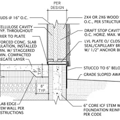
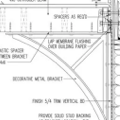
Replies
1- If you can put up blueskin, that implies you're also doing a reside. Why did you rule out exterior rigid foam? Exterior rigid foam will give you *much* better performance compared to spray foam in the walls. My preference would be at least code minimum levels of exterior rigid foam for your climate zone, plus mineral wool batts in the walls. You could save some money with high density fiberglass batts in the walls. If you're really stuck with spray foam in the walls, I would go with a full fill of open cell instead of a partial fill of closed cell. I would much prefer to NOT use spray foam in the walls at all though, and go with exterior rigid foam and batts instead, with the exterior rigid foam and/or sheathing detailed as air barriers.
2- If you air seal the attic floor the old fashioned way, there is no benefit to the 1" layer of ccSPF. Sometimes a relatively thin layer of spray foam is used against attic floors as a way to air seal with less labor, but if you're already planning to air seal with caulk and canned foam, the spray foam layer adds nothing but cost. Spray foam out at the eaves can be a good idea though, since that's usually a difficult area to access in many homes, so the spray foam there can both air seal a difficult to reach top plate as well as add some high R per inch material in the limited space available right over the top plate. In this case, you are really spray foaming the top plate, with the loose fill cellulose intended to do most of the "work" of insulating the rest of the attic floor. It looks like you're shooting for a target R value of 60 with the cellulose, which is usually a pretty good bang for the buck level of insulation for an attic floor insulated this way.
3- ccSPF makes sense if you have no way to vent the roof and have to bring the attic inside the building envelope due to mechanicals being installed in the attic. Ideally, you'd move those mechanicals, but that is usually pretty difficult to do so you're stuck. Sometimes you can build vent channels to vent the roof, then spray foam over those or use batts, but spray foam is a good option for an UNvented roof assembly like this.
4- Put rigid foam directly against the walls. If you have no moisture issues, polyiso is your best bet here, and you need R15 which is best met with 2.5" polyiso (R16). It doesn't hurt to put up two layers, in which case I'd put up a layer of 1/2" then a layer of 2" with the seams staggered and taped for both layers. If you do have moisture issues, EPS is a better choice, in which case you need 4" EPS, but I'd see if your local building department would allow R14.7 worth, which isn't quite to code, but allows for only 3.5" of EPS. GPS is another option, and would need 3" to hit R15. Insulate the rim joist area with ccSPF, and be sure to tie in the top of the rigid foam panels with the spray foam. You want at least about 3" of ccSPF here (R18), since it should be AT LEAST the same as those basement walls, and ideally about the same as the above grade exterior walls.
Don't frame out a full studwall in the basement where it's not needed, just use 2x3s on the flat, which provides enough space for wiring (use 4" square boxes in the standard 1.5" depth, then mud rings to bring devices up flush with the finished drywall surface). You can can secure the studs to the masonry wall with long tapcons. This doesn't need to be a structural wall. Don't use batts at all, as they are always risky in basement applications like this -- rely on the rigid foam to do ALL of the work of insulating those basement walls.
I don't see any issue with your flooring plan.
Bill
I did 3" of exterior foam on my addition, then renovation. So many benefits, one of which on the renovation is that it meets energy code as is and means that interior can be left in place. On the addition, I just extended the insulation to the footing, although we don't have termites here to eat it up.
Thank you Bill.
1) I received a lot of push back from my GC on exterior insulation because of the cost of re-trimming out the new windows, doors, eaves and gable ends. I too would prefer exterior foam and interior batts, but he scared me off because of price.
2) The ceilings will be new and therefore so will the penetrations for lights etc. If it looks like I can do it your way, I will. I like the cost savings.
3) I agree it's the easiest way. The equipment will only be serving the second floor anyway and there's really no way to run ducts from the basement up there.
4) The old concrete walls, some of which are rubble rock walls, are spalling. There's no indication of water intrusion, but it's clear moisture has weeped in the past. I thought the CCSPF would be a good way to secure the wall and the moisture while killing two birds with one stone. I hear you on the bats in the studs though. I was just going for cost savings again.
Maybe I could do 1" CCSPF and then 1" of Polyiso, then the 2x3's?
Thank you for your input.
Nick
1- Your GC might just not like working with exterior rigid foam. Oftentimes pushback from contractors is because they aren't familiar with something "new" or "different". There is a lot of "this is how we've always done it here" in the trades, which is an issue that comes up periodically on GBA when someone is trying to do a high efficiency construction project using new materials and methods. Generally anything 2" or less doesn't really complicate the exterior all that much, so you might try having some more discussions here.
2- Box over the light fixtures with one of the purpose-made insulation boxes, or just build some out of rigid foam. This will simplify any work in the future if you ever have to do any work on the light fixture, and it will let you air seal better than just relying on the "AT" (AirTight) rating of the fixtures -- which is wishful thinking anyway, I like to call them "leaks less" fixtures.
4- Don't try to put rigid foam over spray foam -- you'll never have a flat/even enough surface on the spray foam to make this type of installation work out. Much better would be to build out 2x4 studwalls in this case, with the studs an inch or so off the wall, then ccSPF over the wall and partially filling the studwall, making sure to fully fill the gaps between the backs of the studs and the masonry wall. 3" of ccSPF gets you around R18, and would still leave you about 1.5" for wiring in a wall built like this. I would still not use batts, as I don't like using batts in basement applications.
You could do a hybrid project, using rigid foam against the basment walls where possible, and spray foam in other areas. With careful placement of materials, you could still keep an even finished wall surface this way. Note that I'd only do this if you could do things consistently, such as rigid foam on ALL of one wall, then spray foam on ALL of a second wall, etc. I wouldn't try to randomly mix spray foam and rigid foam sections on the same wall, since it would greatly complicate the construction process.
Bill
"1) I received a lot of push back from my GC on exterior insulation because of the cost of re-trimming out the new windows, doors,"
Is Zip R off the able for the 2x4 walls? It would be way cheaper than ccSPF+blueskin and much higher assembly R value. If you are getting new windows, I can't see what the issue would be. At the gable ends it is easy to add an inch or two as part of the re-roof.
"4) The old concrete walls, some of which are rubble rock walls, are spalling. There's no indication of water intrusio"
I think your basement plan with ccSPF+fluffy is the best option in that case.
" new 2×6 walls"
The cheapest way to increase the R value of your 2x6 wall is to bump it up to 2x8. Outside of that any of the high density batt is your best value.
"new flat roof areas"
I'm assuming this a cathedraled roof. This depends on the roofing contractor. If they are used to working with exterior rigid (which most are) your best option is an unveted roof with enough rigid above the deck for condensation control and batts under. After that, the simplest is to spray foam. If you have the height, spray foam and batt can work but usually the cost delta to a full SPF roof is pretty small if not a big area.