Insulation/ conductivity math help, please

I recently read one of Martin’s posts about (so-called) radiant floor heating.
It was exactly what I needed. The dream of a toasty-warm floor under bare feet is only a dream- unless the boiler runs all the time- either to keep up with a poorly insulated and/or drafty house- or if a well-insulated, tight house is overheated.
Instead, I’ll opt for mini-splits.
But I’m still curious about what the floor will feel like under bare feet (basement, Chicago area, polished concrete). Without starting a debate over hydronic heat, can someone teach me how to predict the floor temperature? Here’s the plan:
* +/- 4″ gravel (dry- or at least not saturated- due to interior perimeter drains)
* 2″ or 3″ of XPS
* vapor barrier
* 4″ concrete
Assuming soil temp. of 55F and interior air temp. of 70F (or 75F, if a 20 degree difference makes for easier math) what will the temperature of the concrete floor be?
I look forward to learning how to do this calculation.
Thank you,
Ben.
GBA Detail Library
A collection of one thousand construction details organized by climate and house part
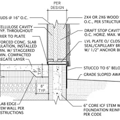
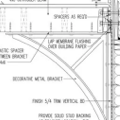
Replies
Ben,
The most important point here is that even if the concrete floor is at the same temperature as the room air (let's say, 72°F), the floor will feel cool to bare feet. That's because your skin is at 98.6°F (more or less -- actually, less, but that's another story), so the soles of your feet will be losing heat to the 72°F floor. The heat flow is noticeable, so you will say, "This floor is cool."
There is less heat flow from your bare feet to a wood floor at 72°F than to a concrete floor at 72°F, because concrete is a better conductor than wood.
Assuming that you have a continuous layer of insulation with a fairly reasonable R-value -- as you have stipulated -- then the bottom of the insulation layer is at soil temperature, and the top of the insulation is at room temperature.
So if your basement air is at 72°F, and the room has a good heat distribution system, then the ceiling, wall finishes, and concrete slab should eventually stabilize at about 72°F.
The caveat is that most heat distribution systems are imperfect, so there is some temperature stratification of the room air. Ceilings tend to be warmer than floors. But if you had a forced-air heating system and you designed your hot-air registers to direct the heat to blow across your concrete slab, the slab would be at 72°F or perhaps even at 73°F when your thermostat was set at 72°F.
FWIW: Over the full lifecycle of a basement slab (50+ years) the performance of XPS will fall to that of EPS of equal density as it's blowing agents seep out. EPS doesn't have this issue, with very stable performance over many decades. Given that EPS is generally cheaper per inch and per R, since the space for extra thickness under a slab doesn't present a higher cost or difficulty, it's generally more cost effective to put 4" of EPS than 3" of XPS, and have R16 forever instead of R15 for a few decades (if you're lucky), or 3" of EPS instead of 2" of XPS and have R12 forever instead of R10 slowly falling to R8.
The HFC blowing agents used for all XPS made in North America also come with a significant environmental impact, since they are powerful greenhouse gases (more than 1000x CO2 @ 100 years.)
From a lifecycle energy cost point of view, unless it's a radiant slab or you live in zones 3-5 2" of EPS might still be financially rational but 3" won't always be (but close in zone 5.). In zone 6 it's sane to 3" of EPS (4" as an inflation hedge), in zone 7 even 4" is fully lifecycle rational, and in zone 8 as much as 5" might be. If you go much beyond these numbers you're betting on the cost of energy being more expensive than the current cost of energy from rooftop photovoltaic solar leveraged with current technology heat pumps. (With a deep suboil temp of 55F I'm going to guess that you're in climate zone 4 or the warm edge of zone 5.)
In climate zones 1 & 2 sub-slab foam is best limited to the perimeter, since the deep subsoil temps are in the "Goldilocks Zone" of human comfort, and earth-coupling the house to the thermal mass of the subsoil works to your advantage more so than isolating it, unless you have very particular performance requirements. (A Passivehouse may need some sub-slab insulation to meet the performance specs, even though any energy saved by that foam ends up being more expensive than rooftop solar.)
Martin,
Thank you. This really helps.
I understand what you're saying about dense surfaces feeling colder than air, carpet, etc. It's like swimming in 70F water vs. walking in 70F air.
My wife is more sensitive about foot temperature than I am, but she doesn't mind the way the tile floor feels in our first floor kitchen in the summer (presumably the same as the air temperature, +/- 74F with AC); if a well-insulated basement slab will also be at room temperature, then there's not much to worry about.
Dana,
Thank you very much for chiming in about the EPS's lower cost, stable R-value, and lack of HFCs. We're near Chicago, so zone 5, but on the edge of 6.
I'm now leaning toward your recommendation of "...3" of EPS instead of 2" of XPS and have R12 forever instead of R10 slowly falling to R8".
I liked what you said about a hedge against inflation. I once heard someone at BSC say something like "figure out how much insulation you think you need, and then double it."
On the other hand, I also like this comment of yours: "If you go much beyond these numbers you're betting on the cost of energy being more expensive than the current cost of energy from rooftop photovoltaic solar leveraged with current technology heat pumps." That seems like a really bad bet.
Please excuse my ignorance, but what does this mean: "(more than 1000x CO2 @ 100 years.)"? Are you saying that the HFC blowing agents used in XPS in North America annually are 1000 times worse than 100 years of NA's CO2 emissions?
Martin, Dana, or ???,
I'd still like to learn how to do a this type of calculation for other situations (I suspect it's similar to calculating where the dew point will occur in an insulated cavity wall with rigid exterior insulation). Can you get me started with something that's no more complicated than it HAS to be?
Again, thanks for all your helpful advice and wisdom.
Ben
Re the 1000x comment: that's per pound of gas ( CO2 or blowing agent), not for the total amount emitted.
If you want a quick and dirty estimate of the floor surface temperature, you can approximate the r value between the floor surface and the room as R-1. Then, if you have R-12 of EPS, and let's say R-2 for the soil (it is really hard to come up with a good approximation for the soil so that is to acknowledge that there's some smallish effect there). The fraction of the temperature difference that is across any of those is equal to the fraction of the r value. So with 15 degrees and a total r value of 15 there's just 1 degree difference between the room and the floor. If you had R8 foam, then it's 1/11*15 = 1.36/degrees. Or if you get R 27 foam, it goes down to 0.5/degrees.
The summertime floor temperature doesn't really help much to gain confidence about winter comfort. In the summer, a slightly cool feeling surface feels good ... (the cool breeze across my feet right now feels great...) but in the winter the same thing is unpleasant. So you might want wood, carpet, or linoleum over a wood subfloor.
Ben,
You wrote, "I'd still like to learn how to do a this type of calculation for other situations."
Charlie took a stab at it. I'll try as well, and I'm going to disagree with Charlie.
The main determinant of the temperature of a slab -- assuming that you have a continuous layer of insulation under the slab -- is the indoor thermostat setting. If you turn up the thermostat, the temperature of the concrete slab will eventually increase. If you turn down the thermostat, the temperature of the concrete slab will eventually decrease.
The reason is simple: the concrete is indoors. It is inside your thermal envelope, just like your kitchen countertop. So the determining factor is your thermostat setting.
I think you are confusing this question (about the temperature of the slab) with a heat flow calculation.
The heat loss formula for determining transmission losses through floors, roofs, and walls is Q = A • U • ΔT. In other words, the rate of heat flow through a building assembly (in Btu/h) is equal to the area of the assembly (in ft²) times the U-factor (in Btu/ft² • hr • F°) of the assembly times the ΔT (in F°).
The greater the delta-T, and the thinner the insulation, the faster the heat loss. This formula will allow you to calculate the rate of heat loss through your slab (in Btu/h) if you are interested in doing so.
Charlie-
Good point about a slightly cool surface feeling good in summer- but not in winter. I've noticed that- and been curious about it. Our thermostat is set about the same year-round, and yet in the winter my wife puts on socks and sweaters. I wondered if it could be a humidity difference (drafty, poorly insulated house = much dryer in winter), or the temp. of the drafts themselves (in summer, air infiltration is 80F - 90F, but in winter it's 20F - 30F), or if there's a psychological angle. After the renovation, our basement will be tight and well insulated, and we don't expect the slab to vary more than a degree or so from winter to summer. And yet, like you, I think the polished concrete floor will feel pleasant under bare feet in summer- and less so in winter. If so, my wife will have to put on socks!
And thank you for your "quick and dirty" method to compute the floor temperature.
Martin-
I probably AM confusing something. That would not be completely unlike me.
Your explanation and Charlie's both make sense and yield similar results with R-12 sub-slab insulation. Charlie said the slab would be 1 degree colder than room temperature; you said it would be the same as room temperature.
However, with much less insulation (like R-2), but keeping the same soil temp of 55F and room temp of 70F, your predictions diverge- and neither lines up with my intuition: Charlie's method (with R-1 for the air boundary layer and R-2 for the soil boundary layer) predicts a slab surface temp of 67F. Martin, (if R-2 sub-slab insulation counts as a thermal envelope) it sounds like your predicted slab surface temperature is still room temperature.
I think the slab would be cooler- closer to the subsoil temperature. This is based on my observation that poorly insulated walls feel cold in winter and warm in summer. They don't just require more energy to maintain the desired temperature; they actually feel colder (or warmer) than the room temperature.
It may be merely theoretical. I suspect it's a moot point- as I plan to insulate adequately- and you both predict that in such a case the slab will be the same (or nearly the same) temperature as the room.
Thank you both for attempting to educate me. I really appreciate it.
Ben
Ben,
You're right, of course, that the closer your insulation layer gets to R-0, the cooler the concrete slab will be in winter.
That said, the type of heating distribution system matters.
If the insulation is R-0, embedded hydronic tubing will still keep the slab warm. In fact, the less insulation, the warmer the slab.
If you have a forced air system set up so that the hot air blows horizontally across the floor, you might still end up with a warm slab. The point is that the heat distribution system will pump more and more heat into the room, until the thermostat setpoint is achieved.
If your hot air registers are mounted high on a wall, they will, of course, be less effective at warming the slab.
Here at GBA, we usually recommend above-code levels of insulation. The higher the R-value of your thermal envelope, the more stable the temperature of your interior surfaces -- whether these surfaces are drywall or concrete.
When it comes to predicting the slab temperature, the factors I've listed -- the thermostat setpoint and the type of heat distribution system -- are as important as, or more important than, the R-value of the sub-slab foam.
Right on. It all makes sense.
I take your comments about heat distribution very seriously. They remind me of something I learned(wow- 20 years ago?) when I worked with glass and aluminum storefronts and curtainwalls: Customers don't like condensation on their glass. They often mistakenly think it's a water leak- and even when it isn't, it can run down the glass and damage finishes below (sills, kneewalls). The factors to predict/ prevent such condensation had to do with temperature differential, interior humidity, and... sufficient airflow on the interior surface of the glass!
As always, thank you for the good info.
Ben