Hybrid Insulation for an Unvented Roof

Climate zone 4. Scope of work is old house renovation involving the insulation of a roof area.
Please tell me if you see any problem with this method. I would like to install 3 inches of closed cell spray foam to the underside of the roof sheathing between the 2 x 6 rafters, and on the ceiling joists below the roof area install unfaced fiber glass insulation. The space between the underside of the roof at the peak side of the roof is high so I can install R38 and at the eve side I will have R19 depth as the ceiling joists are 2x6s There will be an air space between the topside of the ceiling joists and the underside of the roof. I understand that dew point and air movement are the most important issues. I also understand that a vapor barrier should not be placed on the interior room facing side or heated side. I’m not concerned about R value for code compliance however I do not want to cause a moisture trapping condition with the proposed insulation install. I assume the closed cell spray foam will stop the air movement and the fiberglass insulation will add to increasing the overall R value. Do you see any harm to this approach? The reason I do not want to use all closed cell spray foam is due to budget costs. Also the soffits are closed and no ridge vent, so there will be no venting of the roof.
Thank you!
GBA Detail Library
A collection of one thousand construction details organized by climate and house part
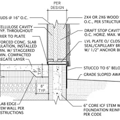
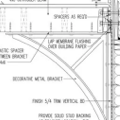
Replies
Hi Kevin,
If I understand your plan correctly, you are talking about the “flash-and-batt” method. This article provides a deep dive into the process, as well as Zone 4-specific code requirements (just 1 inch CCSF for 2×6 walls). It also addresses your concerns around moisture.
You should follow IRC code, even if not required. Specifically, do not create semi-conditioned space by splitting the location of insulation.
R806.5 Unvented attic and unvented enclosed rafter assemblies.
Unvented attics and unvented enclosed roof framing assemblies created by ceilings that are applied directly to the underside of the roof framing members and structural roof sheathing applied directly to the top of the roof framing members/rafters, shall be permitted where all the following conditions are met:
1. The unvented attic space is completely within the building thermal envelope.
Kevin - I am navigating the same scenario that you described above and curious what you decided to do. Can you provide a brief project update?
Diving into your plan for insulating that roof area in Climate Zone 4, you're playing a fine line between budget wisdom and the physics of moisture – always a tricky balance, but not impossible to navigate. Let's dissect this with a critical eye on the fundamentals of building science.
Closed-Cell Spray Foam Direct Application:
Slapping 3 inches of closed-cell foam on the underside of your roof sheathing is like putting on a high-quality rain jacket over a sweater. It's your moisture barrier and air sealer all in one. It's smart, considering your roof won't be venting traditionally with the soffits and ridge sealed up. This foam is your first defense against moisture sneaking in and setting up shop where you don't want it – right at that critical interface where the outside world meets your indoor comfort zone.
Layering Up with Fiberglass:
Throwing unfaced fiberglass insulation beneath, directly on those ceiling joists, to bulk up your R-value is like adding another layer under that rain jacket for extra warmth. The closed-cell foam up top does the heavy lifting against air and moisture, allowing the fiberglass to sit comfortably underneath, boosting insulation without worrying about becoming a sponge for moisture – because, remember, that foam is keeping things tight.
Navigating the Air Gap:
Now, having an air gap between the ceiling joists and the underside of the roof without traditional venting might raise some eyebrows. But in your case, if the closed-cell spray foam is applied correctly, creating a practically impermeable barrier, you've essentially taken the attic out of the equation in terms of moisture concerns. It's a bold move but done right, it could work to your advantage, especially with no mechanicals up there to worry about.
Concerns on the Radar:
You've got to watch for any signs of moisture finding its way into this assembly, though. With a setup like this, any moisture that does get in (and let's be real, water has a way of finding a path) needs a way out, or it'll be trouble. However, with the closed-cell foam in place, the risk is significantly mitigated.
To Vent or Not to Vent:
Adding a ridge vent without soffit vents or a pathway for air to enter and exit might not solve any problems and could introduce unnecessary complexity. Given your sealed approach, focus on ensuring that closed-cell layer is impeccable.
Wrapping Up:
Your hybrid approach of high-quality closed-cell for air and vapor control with budget-friendlier fiberglass to boost R-value is a calculated choice. It shows you're weighing the essentials – air movement, moisture control, and thermal resistance – within the constraints of a real-world budget. Just ensure that foam is applied with no corners cut; its performance is key to the success of your insulation strategy.
In essence, you're crafting a tailored suit of armor for your home – using the best materials where they count most and reinforcing everywhere else as best as the budget allows. Keep a keen eye on that moisture management, and you might just get the best of both worlds: performance and cost-effectiveness.