Insulating with an old tile roof

Hi all,
Emily here. I posted last week about the insulation design for our 1914 bungalow (which has the original stucco exterior and red barrel tile roof), and got some great advice about how to insulate the kitchen walls, which are currently open. This house is located outside Boston, so climate zone 5A.
I’m posting hoping for some similarly great advice or feedback about our attic/kneewall/roofline insulation plan. I feel like we are over thinking this, but I am also very worried about inadvertently causing a catastrophe, like the roof deck failing. We have a GC, an insulation contractor, and an independent energy consultant/HERS rater who are all pretty much telling us different things. My priority is doing the right thing for the house.
Some facts:
1. The roof has wood sheathing and the aforementioned tiles. In some places along the front there is an ice and water barrier added in 2017, but mostly to my knowledge there is nothing between the wood and the tiles.
2. This being a bungalow which is effectively 1.5 stories, there are knee walls at the front and back of the house with voids behind them. There is one big kneewall void at the back and two at the front (on either side of a shed dormer). The “attic” above the second floor is very small and has historically had no access. The floor of the kneewall void in the back of the house has some old insulation under it which would be very difficult to remove. There is no eave or peak/gable venting currently.
3. The house has been heated with hydronic radiators (oil-fired boiler). We’re keeping that, but adding a ducted mini-split system. The air handler will go in the kneewall void at the back of the house, and the ducting will be in there and run through the attic.
4. After we took out the second floor ceiling (to facilitate insulation and HVAC), it became apparent there has been water coming through the tile roof cladding and soaking the wood sheathing. Not a huge amount of water; the old horsehair plaster ceiling showed no damage at all from inside the living space. But without the plaster, you can see water marks all over the wood sheathing and when it rains, there are drips in some places. We have had roofers out twice to fix it, but it’s not easy to find the problem tiles from the exterior.
The original insulation plan (from the insulation contractor) was to insulate the roofline: install baffles on the underside of the roof sheathing, net and blow cellulose into the rafter bays, cover that with 2″ rigid foam. The water situation made us think that is a bad idea.
The energy consultant suggests putting in baffles and spraying the whole roofline with closed cell foam. Similarly, we worry about water coming in from the exterior of the tiles.
So, there is a new plan, to insulate the living space (the kneewall void floors, the kneewalls, the clipped ceilings, and the attic floor). We are having trouble identifying the right materials for this – likely a combination of rock wool and loose fill, depending on location, with baffles in some places. This is also a much more involved plan and would leave our air handler and ducts in unconditioned space.
We are doing the best we can, but it’s not easy. Can anyone advise? Thank you for any thoughts.
Couple photos attached, of the underside of the roof, the interior of the second floor, and the front of the house showing the dormer.
GBA Detail Library
A collection of one thousand construction details organized by climate and house part
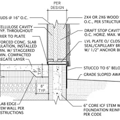
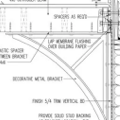
Replies
Hi Emily -
Just some quick points, since you have a lot packed in to this post:
1. lack of roofing underlayment between roof cladding and roof sheathing: I am sorry to say that to me this is a non-starter: I would be very concerned about no back-up water bulk water management for a roof. And I wonder how this is even possible at penetrations: to what are the flashings around roof penetrations connected? I would confirm for certain the lack of a roofing underlayment. Especially when you already have "untrackable" roof leak(s).
2. Current drying potential of your roof sheathing: roof sheathing boards and barrel tiles have a ton of drying potential built in. This probably explains why you have staining indicating wetting but it's drying before the moisture translates into any biological action. So long as you have such great drying potential to the exterior, you can easily airseal/insulated along the roof line, pulling your knee wall spaces into conditioned space and making the knee walls a great place for your new HVAC. I am not a big fan of either:
a. trying to air seal and insulate along the knee wall and the floor assembly at the eaves--just hard to get that continuous;
b. putting any HVAC components outside conditioned space.
Peter
Thank you Peter!
1. I will check with the roofer to confirm that there is no underlayment, but given the age of the roof, it's likely that whatever was there (besides the newer ice and water shield at the perimeter) is not in good shape. The flashing around the penetrations are in need of replacement, but they are not anywhere near the leaking areas. It is starting to become evident that no matter what we do about insulation, we may just need to accept that we may need to replace the underlayment and maybe the deck down the road. I should probably find out how much that will cost.
2. It's not 100% no biological action...there was one spot with mushrooms growing. It was right along the edge of where the ice and water barrier underlayment was added (this is where most of the leaks have turned up). But even that spot is not rotten.
But setting that aside...are you saying you think it's OK to airseal and insulate along the roofline and not worry about the water from the outside on the roof deck because it will dry back out to the exterior? If so, what material would you use? Foam (open or closed cell?) and baffles? Or batts or nets/loose fill?
THANK YOU for your advice. I consider myself to be a smart person and a capable researcher, but there are so many variables here.
Air sealing kneewalls adequately is a fool's errand (having played the starring role of "fool" more than once...).
This should definitely be insulated at the roof line, and with the leak factor in mind it should be vented with at least 2" of vent gap, not the code-min 1".
Are the rafters full dimension 2" x 10"?
"Vented with at least 2" of vent gap," meaning 2" of air gap between the sheathing and the roof side of the insulation? What materials would you use?
The eave soffits are not adequately vented, but they do have a lot of holes in them (i.e. you can see spots of light when you look at them from inside). The energy consultant said that rather than installing big soffit vents right now, we could put in larger gable end vents up top, does that sound workable? (Since it's a tile roof, peak vents are not in the cards.)
Editing to respond to your question - yes I believe the rafters are full dimension 2x10.
With full dimension 2x10s and 2" of air between the insulation and roof deck you have 8.0" to work with. The baffles need to be water proof to manage any bulk water incursions/drips, but installing 3" of HFO blown closed cell foam on a thin baffle would give you R20-R21, leaving 5" of space for 1.8lbs fiberglass for another R21-R22 and R41-R44 total, with considerable dew point margin at the foam/fiber boundary, but it would still need at least a class II vapor retarder on the interior. Using Intello Plus as both vapor retarder and blowing mesh it saves a layer.
Since pre-made insulation baffles are designed for milled rafters they don't really fit well into the half-inch narrower space. Half-inch foil faced polyiso cut to a more appropriate width held off from the roof deck with strips of 2" thick foam as vent-depth spacers can work, displacing a half inch of the spray foam.
If you're feeling confident, reducing the vent gap to 1.5", with 3" HFO blown closed cell foam it would leave 5.5" of space, sufficient for R23 rock wool batts, which would be cheaper than mesh blown fiberglass, with a total R in the mid-R40s. It would still need an interior side vapor retarder, but you could use thinner and much cheaper Certainteed MemBrain rather than Intello since it doesn't have to withstand the pressures of dense-packing. (I'd personally be inclined to go this route.)
Alternatively 4" of HFO blown closed cell and a 2" vent gap would put it at R27-R28 for the foam, and 4" of 1.8lbs fiberglass another R17 and R44-R45 total, and no concern at all about vapor retardency. (But using MemBrain as the interior side air barrier is cheap enough to be worthwhile insurance for it's variable vapor retardency.)
For gable vents to work it needs at least a micro-attic near the top. Tile roofing is inherently ventilated on the exterior side of the deck, so it doesn't need much as long as it's low-permeance to the interior.
Thank you thank you, this is very detailed and so helpful! I had been much more worried about drying from the outside in, and less about vapor coming from the inside out.
Our energy consultant recommended open cell over the baffles...do you recommend closed cell because of the superior R value or something else?
Open cell works great in a vented cathedralized roof if the roof never leaks, but can take on quite a bit of liquid if/when it does. Given that you know the roof leaks sometimes, it has to be planned for.
While I'm not a big fan of closed cell foam, it is waterproof to liquid water- any chronic or incidental leaks would run down hill toward the eaves and never soak through. But it uses more than twice the amount of polymer per R of half-pound open cell foam and the cheaper HFC blown stuff is putting powerful greenhouse gases into the environment, (unlike the more expensive HFO blown goods).
The higher R/inch of both rock wool & closed cell foam relative to open cell also adds up enough to matter at your joist depths. At 9" of thickness with a code-minimum 1" vent gap you would only be at R33 with open cell foam, which is on the skimpy side for New England. To hit a code-min R49 takes over 13" of open cell foam, which has to be done in three lifts with cooling periods between passes for both fire safety and quality reasons.
To be sure 9-10" of open cell foam would be substantially cheaper than any of the solutions I've suggested here. 10" of open cell foam (R37-R38 ish) is usually under $4 per square foot- a bit less than the cost of 3" of HFO blown closed cell (R21) or 4" of the climate damaging HFC blown closed cell (R24).
Thank you again Dana. This has been so helpful. It is looking like we will be going with the closed cell/rock wool combo, although I was mistaken about the joist depths - we only have room for 3.5" of rock wool. But it seems everyone agrees this is the best approach for a mildly unreliable roof (although the roofer tells me it's actually over all in good shape, which is reassuring).