Insulating walkout basement wall
I’d like to correctly insulate an exterior wall of our walkout basement. The wall is 2×4 wood framed, sitting on a single course of concrete block, and sheathed with 1×12 boards. Home was built in the mid 50’s and we are in the twin cities, climate zone 6.
Having read various helpful articles on this site and Taunton literature, I have decided on XPS foam board over the existing sheathing to form a thermal break so as to avoid condensation in the wall cavity (with housewrap underneath the foam board for air barrier). The recommendation for a minimum R value for that thermal break has been stated at 7.5, so 1-1/2” board ought to do the trick. However, I’ve also read about thermal loss over time for XPS and since I’d be right on the line of that minimum, I’m concerned that over time I’d no longer have the fuller value of that original 7.5, this exposing us to condensation potential in the cavity.
My plan for in-cavity insulation is rockwool R15, which likewise creates a slightly greater than recommended ratio between the outside and inside cavity insulation if only using 1.5” thick foam board (R7.5). The difference in percentage is small but it’s there.
The simple solution would be to simply up-size to a 2” foam board externally as recommended, however, this poses other dimensional/space challenges with existing structural elements so not as easy a solution.
my question: could I add a thin layer of closed-cell spray foam insulation on the inside of the cavity against the backside of that sheathing in an effort to extend the thermal break insulation segment slightly and thus successfully avoid the condensation potential? Or is this quasi flash and batt solution really not a solution at all?
I will not be using an internal vapor retarder either, beyond painting the gypsum board that will finish the internal wall. On the outside, siding will be fiber cement on 1×4 rain screen over the foam board.
thanks for any insights you might share.
GBA Detail Library
A collection of one thousand construction details organized by climate and house part
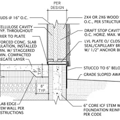
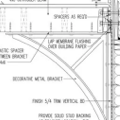
Replies
User-6985827,
First of all, can you tell us your name? (I'm Martin.)
Lots of issues here.
1. Most green builders avoid the use of XPS, which is manufactured with a blowing agent that has a high global warming potential. For more information on this issue, see "Choosing Rigid Foam."
2. Consider using polyiso instead of XPS. Polyiso has a nominal R-value of R-6.5 per inch, but many cold-climate builders assign polyiso an R-value of R-5 per inch to account for polyiso's performance in cold weather. That's the same as XPS. For more information, see "Cold-Weather Performance of Polyisocyanurate."
3. It's possible to cheat on the rules. If you decide to cheat on the rules, you might want to read these two articles:
"The Exterior Rigid Foam is Too Thin!"
"Rethinking the Rules on Minimum Foam Thickness"
4. If you do decide to cheat on the rules, and interior vapor retarder can lower your risk -- so you may want to rethink your plan about that. (You wrote, "I will not be using an internal vapor retarder.")
5. You asked, "Could I add a thin layer of closed-cell spray foam insulation on the inside of the cavity against the backside of that sheathing in an effort to extend the thermal break insulation segment slightly and thus successfully avoid the condensation potential?" The answer is, "Yes, you could. But this approach sandwiches the exterior sheathing between two low-permeance layers of foam, so it's not ideal."
Hi Martin-
I'm Stephen. Thanks for your reply and pardon the bizarre screen name! Looks like I hadn't properly set up the profile... hopefully all set now.
I'm certainly open to using the polysio and sounds like a smart vapor retarder underneath the sheetrock would be useful given your 4th point. I'd read the articles to which you've linked and some of the follow up discussion in comments as well as a few other reference points; based on then, I had decided to forgo vapor barriers/retarders and instead focus on air sealing appropriately. But again, sounds like a "smart" vapor retarder could indeed be helpful to reduce my risks for condensation during the winter.
I've focused my efforts to keep the warm and cold air separated as much as possible in both heating and cooling seasons while still operating within the confines of the existing structure.
Thanks again for the quick reply and thoughtful answers!
Well, not sure why the user name updates aren't taking....