Insulating Unvented Cathedral Ceiling

My wife and I are designing and building a home in Western Washington (I’m a professional structural engineer). One of the spaces is a great room with a cathedral ceiling featuring exposed trusses. Due to the configuration of the roof (specifically, an adjacent roof with a perpendicular ridge that eliminates the possibility of eave vents for approximately 3/4 of one side of the roof), I’m leaning toward an unvented assembly. I would have preferred venting it, but I don’t think the configuration of the roof will allow it.
I found a presentation Martin Holladay did in 2016 regarding cathedral ceilings online – great resource! (This is the presentation I’m referencing: http://conference2016.eeba.org/Data/Sites/2/media/presentations/Holladay-Getting-Cathedral-Ceilings-Right.pdf) Specifically, I’m currently planning to do what the presentation calls Option 1 – full closed-cell spray foam. Here in WA, the energy code allows R-38 for cathedral ceilings, so that’s my goal. I’ll have 2×8 roof framing members at 24″ OC that’ll interrupt the insulation periodically and some air space between the insulation and the gyp ceiling.
Do I need to be concerned that the 2x’s interrupting the spray foam will cause discontinuities in my thermal envelope and vapor barrier? I’m somewhat nervous about moisture collecting and causing rot of the roof sheathing. Also, do I need to be concerned that the dew point of the assembly is somewhere in the spray foam, so condensation can form in the sheathing? Or will the sheathing be able to dry to the exterior in that case, so no concern?
Are my concerns valid, or am I being overly cautious?
Any other ideas?
GBA Detail Library
A collection of one thousand construction details organized by climate and house part
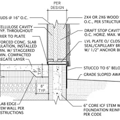
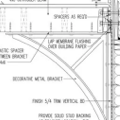
Replies
I thought I'd jump in as I'm in the process of building almost the exact same structure... just a bit thicker at 2x12 rafters.
Here's what I have learned:
Using closed cell spray foam is a great way to prevent moist vapor from getting to the sheathing. It's important that all of the contact points between the rafters and the roof sheathing are covered, but it would seem that you are planning to fill almost the whole cavity with foam, so this shouldn't be a problem. It would be pretty much impossible to have a void for the full depth of a 2x8 rafter without somebody noticing.
In my case, I am doing a "flash and batt" unvented cathedral with 4 inches of closed cell foam and 7 inches of cellulose. The 4 inches of foam ensures that the temperature on the room side of the foam remains above the dew point. There is a recommended ratio that I based my depths on, but I can't remember where I found it.
In both of our cases, it is not possible to have condensation occur within the foam as no air or vapor (the source of the potential condensate) should enter into the foam due to its closed cell construction.
The interior will be tongue and groove pine and that will allow the structure to dry to the interior if any moisture does condense in the cellulose.
In my case, my roof will be standing seam steel. My concern is what to apply to the top of the sheathing to ensure that the sheathing dries properly if it gets wet. My builder is planning blueskin. It's a bit of a paradox. The blueskin should go a long way to keeping the sheathing dry in the first place, but I do have some concern that it might slow evaporation if the sheathing does get wet.
This article is probably similar to the presentation, but it may provide some additional detail: https://www.greenbuildingadvisor.com/blogs/dept/musings/how-build-insulated-cathedral-ceiling
Can you tell us your climate zone or location? I'm assuming Zone 5b and not 6b.
Would you be open to consider exterior rigid foam?
User-6878482: did you go with a flash and batt approach as a cost-saving measure, or was there something else that pushed you that direction? I hadn't thought about Blueskin, as I was thinking my closed cell would be a suitable air barrier. But that does make me wonder what I should be putting on my roof....I was thinking 30 lb asphalt felt, as my understanding is that it wouldn't trap vapor and should allow the roof sheathing to dry to the exterior (and won't cost a ton).
Steve K: yes, that article was another source that I reviewed that makes me think simply going with closed-cell spray foam might be the most bulletproof source. I'm actually Climate Zone 4c (marine)...so we're pretty damp out here. Also, my home will be on a heavily wooded lot with tons of shade, so a perfect environment for constant moisture. I would consider exterior rigid...what do you have in mind?
Thanks to you both!
JFTorny,
I should have given my response more thought before speculating on your climate zone location.
Let me also say that I am a home owner with an interest in green building and don't have the years or decades of practical experience of the professionals who regularly post on this site.
With those caveats...
I asked about the exterior rigid foam because that approach generally seems to be the best option if your roof design is simple.
Since you are still in the planning stage, I wasn't sure why you were opting for one of the code-approved workarounds for the cathedral portion. Martin points out that while the code will allow you to substitute thinner insulation in certain circumstances, he does not think this exception is a good idea. (I assume because it puts your roof at greater risk.)
Can you design an unvented roof with 9 inches of exterior polyiso rigid foam (R-49), for example? If that is a no-go, what about combining R-10 of exterior rigid foam with R-39 of air permeable insulation installed against the underside of the sheathing.
Both these approaches would keep your sheathing above the dew point.
You also could use the flash and batt approach with R-10 of closed cell foam and R-39 of air permeable insulation applied to the underside of the sheathing. But Martin notes that this strategy has more minus than pluses. For more on why, go to https://www.greenbuildingadvisor.com/articles/dept/musings/flash-and-batt-insulation.
Worth looking at a budget minded version of PERSIST which puts exterior foam over fluffy insulated walls and ceilings. Joe Lstiburek has a couple of great articles on reasoning and basic principles - just search for BSI 001 and BSI 096. Martin has also done outstanding articles on installing exterior foam on walls and roofs, as well as getting the window and door flashing correct. I just adjusted my plans to adopt a similar method. It's different to build the eaves on after sealing and insulating the shell, but it makes sealing and insulation easier to get truly right.
JPTORNY:
The rationale to use a flash and batt was primarily because I am not all that keen on using spray foam due to the environmental impact as well as the occasional story of poor installation causing unacceptable odors.
There are some secondary benefits. First, the cost/Rvalue of cellulose is lower. Second, filling the entire space between rafters would inevitably cause some overspray, resulting in removal effort before applying the finish material. Finally, this provides a proper air and vapor barrier vs the uselessness of a polyethylene sheet or the cost and effort of installing and taping OSB.
So I wanted spray foam for its sealing properties but opted for the least amount of spray foam that I could justify. Steve has linked to the blog with the table having the appropriate ratios.
Without a thermal break, though, I can see that some condensation might form on the interior sides of the rafters. Hmmm...
(Formerly User-6878482) (Finally found the user profile section)
I'm in climate zone 6.
> standing seam steel. My concern is what to apply to the top of the sheathing
Seems like a basic building science question, but I haven't seen data. My guess is similar to walls - best is a breathable WRB and a gap to allow drainage and some air flow (with the non-moisture-retaining steel and little moisture from inside, probably very very little is needed - but more adds additional ice dam resistance).
Jon,
The problem is when you introduce an air-space directly below the roofing, It becomes subject changing temperature of the metal. It in effect becomes a condensation creator. The air gap may help dry the sheathing below, but it also spends it's time drying the moisture the gap created. When the roofing is installed directly onto the sheathing (with an underlayment of course) there is no moist air to condense.
Manufacturers began recommending metal roofs be installed this way several decades ago, and simply don't exhibit problems with their sheathing. Unless something else is wrong with the assembly, they work. I don't see any point complicating them for a theoretical gain.