Insulating under footings?

Hello, I’m building a house for my parents in northern British Columbia. We are shooting for a superinsulated and air tight building. It’s will be a story and a half, on an ICF foundation crawl space.
Planning on doing the GWB, 2×6 (structural/utillity chase, with either dense-pack cellulose or rock wool batts),1/2″ ply (taped to become the vapor/pressure boundary) with a 12″ Larson truss on the outside of that (dense-pack cellulose), then WRB, rainscreen, Hardiplank.
Planning on beefing up the ICFs with 6″ of EPS on the outside, with also 6″ of EPS under the slab.
Trying to figure out if the thermal bridge of the footing up the foundation wall is something worry about, or if having the EPS underslab wrap up to meet the interior side of the ICF wall is the simplest way to isolate the interior. Is that footing just cooling the concrete all the way up that foundation wall?
Thank you for you time.
Richard.
GBA Detail Library
A collection of one thousand construction details organized by climate and house part
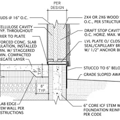
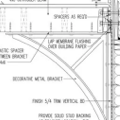
Replies
Richard,
To learn more about this issue, I suggest that you read Foam Under Footings.
Richard,
You mention isolating the interior. Without exact construction details it is impossible to say. With typical details, you will have a sill plate sitting on your ICF, upon which you place joists, trusses, etc.
Yes, the footing will bypass the exterior portion of the ICF insulation. Concrete is a great conductor of heat.
If your sub slab insulation is continuous with your interior ICF insulation, that will create your thermal break between the soil and your crawl space.
However, heat can still move unimpeded from the top of your ICF wall (through your mudsill, etc), down through the footing. That is unless you have thermally broken that area in some way. Is this amount of heat transfer, between the interior and subsoil temperatures at your footing level of consequence? Only you can decide.
As I am sure you know, to complete the thermal break, you must place insulation under the footing, or between the top of the ICF and the rest of the assembly.
If I have misinterpreted your assembly details, please clarify.
cheers.
Thank you for the replies, the Foam Under Footings is a great article, thank you Martin. Her is a quick sketchup of what I'm purposing. Any suggestions/comments/critics are welcomed. Having never worked on anything other then typical code built houses, this project is a departure from my comfort zone. But what an interesting direction to go! I appreciate any ones thoughts.
Thank you.
Richard.
Richard,
Your assembly appears to include two layers of foam under the footing? If that is the case, then the only thermal bridging I see is:
a) The base plate that rests under your truss and structural walls.
b) Whatever mechanical fasteners you intend to use to connect the ledger board with to the foundation.
I am wondering how successful you will be compacting 3" of gravel on top of EPS foam, however. I am skeptical you will get compaction and will likely damage the foam in the process. What is the purpose of the fill?
Last thing, I do not see any vapour barrier below the slab?
cheers.
Good point on the compacting ontop of the foam. Does not make sense to even try that. I updated the picture to show the EPS wrap down under the footing then back up to directly under the vapour barrier, then slab. As for the mechanical fasteners for the ledger, aren't those not a concern because the entire outside of the footing/foundation is wrapped in EPS?
Richard.
Richard,
Yes, in your updated design with a sealed/insulated crawl space, the fasteners should be a non issue.
Cantilevering your exterior wall over foam might need to be engineered. While it's true you can get foam with high PSI to withstand the load, your inspector might want "proof", as in a stamped drawing - if you don't already plan to.
In the same vein, the larsen truss may need to detail how wind loads shall be transferred from the exterior wall to the interior (structural) wall. While it's true that dense packed cellulose is dense, a solid mass, I am not sure it alone would qualify.
Lastly, while it is likely omitted from your drawing for clarity, most building codes call for an anchoring system to hold down your structural wall baseplate (in your case the 2" x 6" baseplate).
cheers.
Jason, thank you for the reply. Good points on the weight of the Larsen truss, and the windloading. Both those points are beyond, my know how, I'll have to run it by our engineer. Also the plan has changed just a bit. Anchors for mudsill are still not included. I would appreciate any comments on the new detail.
Question, should I be working about non overlapped joints in areas like where the subslab eps meets the footing eps?
Thanks again.
Richard,
It looks like the start of a good detail, provided you have no issues with the (increased) cantilever onto the foam, either with your inspector or just making it buildable.
If you have not already, you may want to start considering a way to protect the foundation insulation below grade, from deformation during backfill and more importantly - insects if they are a local issue. Any above grade foam will also need similar protection from UV damage and to be finished in some way.
I am not sure what you mean by the foam not overlapping. Are you worried about the vertical piece that separates the slab from the footing?
cheers.