Insulating San Jose basement

I’m following the advice that’s been posted here in terms of turning a basement into living space – 1″ faced EPS with taped seams on the floor followed by floating T&G OSB and 2″ faced EPS on the walls. My house was built in ~1900 but fairly certain that the basement walls and floor were poured sometime later but they still have no protection against moisture or insulation. The basement stays mostly dry except occasionally there might be a few spots with dampness.
I’ve got a few questions:
1) the taped floor seams feel significantly colder than the EPS should I be worried about condensation collecting on the tape?
2) I have a large beam running through the middle supported by 4×8’s however half of them are resting directly on the floor and one of them is about a quarter inch off the basement wall. My plan was to just leave a few inches open around the bottom of these for inspection/drying. There is a few small amount of water staining I can see on one, but the drywall that was there before I started looked like it had never gotten wet (I’ve owned the house almost 6 years and it was vacant a few years before that). Is this a sensible approach? Should I try to get foam in that 1/4″ of space between post and wall?
3) If my concrete walls are a very old pour of concrete, is there any damage that can be done by sealing them up like this so they are more likely to be constantly moist?
4) related to 3, is there any concern about driving more moisture up into my redwood sill plate?
5) to keep costs down I wanted to use the OSB as the finish floor by painting on some kind of water based poly, are there any issues with this?
Thank you for the help!
GBA Detail Library
A collection of one thousand construction details organized by climate and house part
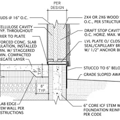
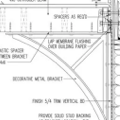
Replies
Hi user-7657115 (it would be great to get your real name).
From your post, it sounds like you may have some water or significant moisture issues to look into before insulating and finishing your basement. Concrete does not need to dry, but if it is too wet, your risk of mold growing on the materials that you add to your basement is high. On the other hand, if the basement is getting wet from indoor air condensing on the concrete slab and walls, the insulation (and some humidity control) might be helpful.
Also, as you noted, wood should not be allowed to stay wet, so it is important to make sure that those wood posts and your mudsill are not wicking moisture from the concrete and can dry if they do get wet.
I suggest that you start with the article below which offers some information on how to determine how your basement is getting wet. Proceed from there. It just isn't worth doing any of this work until you know you basement is dry enough that you won't be tearing it all out in a couple of years.
Fixing a Wet Basement
Thanks Brian, I've done a good amount of work over the years with exterior grading and fixing my gutters and downspouts which has made the basement much drier compared to when I first moved in, which is why I'm ready to undertake this project now.
I’d be concerned about those 4x8s resting on the floor. End grain is most susceptible to sucking up water. I’d check on the feasibility of putting something under those posts. I’d probably use some EPDM with a precast paver or partial solid concrete block on top, then another layer of EPDM between the top of the block and the bottom of the post. The lower layer of EPDM keeps the block from wicking any water up from the slab, and the top layer is a capillary break for the wood post. The block gets the bottom of the wood post up above your subfloor where it should always be dry.
I’d look into putting in a capillary break for your rim joist. I like HDPE sheet for this since it’s stiff and slippery which makes it easy to slide into place.
I’d use some CDX plywood sheathing for the floor instead of OSB. The plywood won’t be much more than the OSB, and it will give you a nicer floor surface to paint and will also be less prone to coming apart if it does get wet. I’d also apply primer to all perimeter edges of each plywood sheet AFTER cutting and before laying it on the floor so that the edges are sealed for better moisture resistance.
Bill
That's a great idea to prime the ends I hadn't thought of, thanks Bill! It may seem silly but the OSB with a clear finish is nostalgic for us so that's what we went with, especially since it is cheaper than plywood.
I'm worried that it will be quite a bit of work to get anything under the 4x8s. One post is two sistered 4x8s and the other is just one 4x8 but it's up against the wall. Also in this case ignorance is bliss, I'm not sure I want to cut into the slab and find out these posts are only bearing on the slab...
If money was no object is love to excavate the exterior, underpin the foundation to get more basement headroom and then waterproof everything. As it is I'm trying to make the room usable and safe for the kids without taking up a huge budget yet still do it right. Thanks for the help in getting me there.
OSB usually has the edges sealed at the plant to make it less likely to swell in the presence of moisture. It’s really best to seal any cut edges prior to installation to maintain that protection. If you like the look of OSB there is no reason not to use it, just be sure to seal the edges.
My concern with those posts is that if you insulate and seal the floor, any moisture might get trapped and wet the ends of those posts leading to rot. You might be able to use some jack posts (which are surprisingly inexpensive and can even be rented) to lift the beams a bit so that you can at least slip a capillary break under the posts. How far you want to go is up to you, but I’d really try to at least slip a capillary break underneath at a minimum.
Bill