Insulating new construction home with no exterior rigid foam

Okay smarties, here is my scenario:
-I am Building a new home that is currently in the framing stage. 2×6 studs with Forcefield Sheathing (essentially same as ZIP).
-I am in in Climate 5 (iowa)
-My home is a California style architecture, 1.5 story, pitched roofs (now I realize why this is better suited for CA-vented roofs better option in Midwest!)
-My initial goal and how I came across these articles was to prevent mold (still is)
-Second goal was to have healthy IAQ (as much as possible) I have spent a considerable amount of time researching paints, caulks, indoor furniture, etc but now realize how important ventilation and building envelope is
Anyway-I UNDERSTAND the best option for a building envelope in Climate zone 5 is to do Exterior Rigid Foam (EPS preferably) equal or greater than an R value of 7.5 with seams staggered. BUT I cannot afford it! AND no one even understands what I am talking about! No experienced installer means more money and it may not be done right!!! Also, concerned about ants with rigid foam…would actually prefer Mineral Wool on exterior in a perfect world.
Also, should note that I also understand closed cell foam would also be a good application when no exterior insulation HOWEVER I am absolutely opposed to spray foam.
SOOOOO, thinking my option is to make sure I have a rain screen with 1×4 furring strips on exterior of sheathing and then doing
A) wetblown cellulose between 2×6 studs, Membrain or another smart vapor retarder over that then my drywall with eggshell paint…..
B) same scenario as above but with JM Spider insulation….
I understand I will still get moisture on interior side sheathing but gap should help it to dry out???
I have more questions on roof insulation too but thinking I will save for another post!
THANK YOU for any help or insight! Cost is a factor but I also want a building envelope that will last, be healthy-ish and prevent future issues.
GBA Detail Library
A collection of one thousand construction details organized by climate and house part
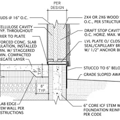
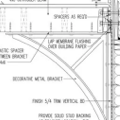
Replies
Dear User 6809983,
The building code requires walls in Zone 5 to have a minimum R-value of R-20. (That's for insulation between the studs; actual whole-wall R-value will be less than R-20, but the building code in this case determines R-value by the R-value of the insulation, without counting the studs.)
You can get there, barely, with well-installed cellulose or blown-in fiberglass. So your plan will work. As long as you have a vented rainscreen on the exterior, your sheathing can dry out to the exterior, so you don't have to worry about moisture accumulation in the sheathing causing any problems.
The key to making this wall work is to to pay attention to airtightness at every stage of construction, and to verify that air leaks have been minimized by performing a blower door test before the drywall is installed.
-- Martin Holladay
Closed cell foam between the thermally bridging studs also buys you very little, one of the lousiest bang/$ propositions in the insulation. (In continuous layer applications without the thermal bridging it at least buys you something!)
There are several square miles of 2" roofing foam in salvage yards and foam reclaimers warehouses, typically at less than 1/3 the price of virgin stock foam, and one of the BEST bang/$ propositions in insulation. At 2" any type of foam has sufficient R for dew point control for a 2x6/R20 wall in zone 5, and sufficient R to beat code minimums for a 2x4/R13 wall, and has HUGE dew point margin. This reclaimed 1.5" polyiso in Washington, IA also has sufficient R for dew point control on a 2x6 wall:
https://desmoines.craigslist.org/mat/6076481095.html
A 2x4 wall with 2" foam is the same thickness as a 2x6 wall, and at 2" or less it's not very difficult to assemble. Mounting the windows "outie", putting housewrap on the exterior of the foam and lapping the window flashing accordingly might be easier for untrained crews to get right, and is easier to inspect.
Even without the foam, an OSB sheathed wall with back ventilated siding (vinyl siding, or any siding with a rainscreen gap) doesn't need an interior side vapor retarder (other than latex paint) in a zone 5 climate.
Looking at the rough elevations, implifying the footprint and roof lines a bit will be easier to air seal. There are a lot of corners and overlapping roof planes, and several features such as valleys that will become snow-traps (don't skimp on the height & quality of the kick-out flashing there!) The greater the numbers of corners, the more exterior surface there is per square foot of conditioned space, and the higher the thermally bridging framing fraction. It doesn't have to be a shoe-box with a gable to be an efficient shape, but creating bump-outs for architectural drama isn't a great idea. Changes in cladding , changes in roof overhang depths etc can deliver similarly compelling aesthetics without compromising the thermal performance. Keeping the number of roof planes down makes it less leak prone too.
Thanks Guys! You were both who I was hoping to provide some input!
I have asked my builder for a rainscreen (1x4 furring strips) to go under our LP smart siding and he said he would just rec'd a stucco tyvek wrap instead. He said that would be sufficient with the crinkles to allow drainage? To me this seems counterintuitive since a furring strip is solid AND 1" away from sheathing. Are there alternatives to fur strips (less expensive) or would this be a good way (stucco tyvek) to kill 2 birds with 1 stone?
User 6809983,
Crinkly housewrap is better than nothing, but it isn't the same as a ventilated rainscreen gap. For more information on this issue, see All About Rainscreens.
-- Martin Holladay
For way less money, you could, as Dana suggests, lose the multiple roofs and bumpouts and insulate with recycled foam on the exterior. Air sealing and insulating the existing design will be a nightmare. Just framing it will be difficult and expensive. Since you asked for advice, mine is to hire an architect.
I'm with Stephen and Dana - simplify the design a bit. The money you save by doing that can be used to purchase reclaimed rigid foam and pay to have it installed along with a proper 3/4" rainscreen gap behind your SmartSide. If your contractor pays attention to interior air sealing, as Martin suggested, you'll have a very durable, efficient structure.
The roof lines really are a problem for locations that get substantial snow, and are potentially problematic for places that get much rain. It probably works fine as-configured in the desert SW or soCal, but Iowa gets enough snow to collect large depths in the inherent snow traps, and enough rain that the kick out flashing has to be ample & perfect, (and stay perfect forever.)
Crinkled house wrap is no substitute for a rain screen. In IA a 1/4" mesh material (such as 6mm Obdyke Slicker Classic plus a flat houserwrap or 1/4" Slicker HP, that is laminated to a housewrap) would work OK under Smartside, but a furring estabilished rainscreen would be better. Some of the differences are explained in this bit o' marketing fluff video:
http://www.benjaminobdyke.com/jobsite-gallery/differences-between-slicker-rainscreen-hydrogap-and-flatwrap
For the record, I've never used these products, but they should work OK, and make for thinner wall than 1x furring.
Thank you for your help. Unfortunately the house is already framed! Of course I realize all the woulda, coulda, shoulda's now! Yes, the roof lines are giving me grief. The builder wants to do the roof vented but I am just not confident it will be done right. My true desire would be exterior foam on the roof but once again, same problem as above, no one understands how to do it. Now I am a tiny 5' girl but dang if I don't want to figure out a way to do it myself!
I am looking into doing an unvented roof now with closed cell spray foam but I really did not want to go that route.
Also, we are now working with time constraints since the house is framed. They have already installed the Forcefield incorrectly so we already have to push for a Tyvek housewrap. Yes, hindsight is 20/20. Should have had an architect and spent more time at the beginning researching the mechanicals and insulation....
Most of the roof lines are simple planes, and easy to vent the roof deck from the lower eaves to the top. The upper gable roof is also just a pair of planes that can be vented soffit-to-ridge.
But the lower gable interrupted by the upper floor wall for most of it's length might be better off unvented.
How deep are the rafters?
Dana- The rafters vary but generally 12".
User-6816910,
Please don't take this as piling-on about your roofs, but for the benefit of other's contemplating similar designs:
Roofs that meet other roofs with only the height of a fascia between them are almost impossible to install. Imagine trying to get a hammer or screw gun into that space. I've managed a couple with palm-nailers and bloodied knuckles. It's not a good detail.
I'm afraid there are more lessons here for GBA readers who are still at the design stage than there are useful suggestions for User 6809983.
As I've written before, you want to finalize your insulation details before the excavator digs your foundation hole. Once your house has been framed, it's kind of too late.
More here: Plan Ahead For Insulation.
-- Martin Holladay
If the rafters are 2x12s (which are actually 11.25" deep) there is no way to hit code performance with a code-max U-0.026 for the roof assemblies, without a continuous insulation layer over or under the rafters & rafter-fill. It will take at least some amount of closed cell foam to make code compliance with an R49 rafter-fill only, with or without venting the roof deck at the code minimum 1".
With a 1" vent space you have 10.25" in which to hit R49. That would be an average of R49/10.25"= R4.8 per inch. If you install 4" of an ~R6.8/inch HFO blown foam such as Lapollla Foam-Lok 4000-2G (https://www.lapolla.com/wp-content/uploads/2016/10/FL-2000-4G-TDS-08112016.pdf) or Demilec Heatlok XT ( http://www.demilec.com/documents/Tech-Library/Heatlok/Heatlok-XT-(High-Lift)-TDS.pdf ) it will cover the first R27, leaving 6.25" for the remaining R22 to hit R49. That can be done with cheap damp-sprayed cellulose, or compressed R25s designed for 2x8 framing. For an unvented solution with 4" of HFO blown foam on the roof deck it would leave 7.25", which is the depth R25 batts are designed for, and it would still have more than adequated dew point margin.
From a performance point of view the 4" ccSPF + R22-R25 fluff would come in slightly worse than U0.026, but would still meet code on an R-value basis.
I've yet to see real quotes the HFO blown foam, but for 4" it will probably come in around $4.50-5.00 per square foot. Unlike HFC blown closed cell foam 4" can be safely installed in a single pass, and the global warming potential of the blowing agent is negligible.
Installing 4-5" of polyiso over the roof deck and stuffing the cavities with 11.25" of cellulose (or low density R38s, which actually perform at R37 when compressed to 11.25") would be both cheaper and higher performance, but there may issues preventing that due to the chopped up and stepped roof lines. If only 4" of polyiso is used it would be worth installing a smart vapor retarder such as Intello Plus or Certainteed MemBrain behind the ceiling gypsum, since it will be marginal for dew point on R37-R40 cavity fill when the foam derated for the average wintertime performance, even though it makes the IRC chapter 7 prescriptives in on a labeled-R basis.
Reply to Malcolm: I noticed that too and wonder what the point is? More expensive to frame,sheath, roof, vent, etc. for minimal change in exterior appearance. I don't want to pile on either, but for everyone planning a new house, at least consult with an architect who should help you avoid expensive design quirks.
Dana-Thank you! Thank you! Very informative and helps greatly. Like I said, if I had know what I know now, I would have definitely changed everything. Too late now though. I have learned a ton through this experience. Should I ever move again and build I will pick a simple home and focus my money and attention on all these details first and foremost. Education can be expensive....GBA has been very helpful and I have taken many notes. Now I just wish I knew one handy person that could help me do this myself!
Stephen,
In the interests of full disclosure: Straight out of school with no building experience, I designed several roofs with that awkward condition. Perhaps my bloody knuckles went some way to repay the poor roofers on those jobs.
Malcolm: If we knew then what we know now.....