Insulating kneewall slopes from above

Unfortunately we are having to fix some poor quality work by insulation contractors.
How should we build baffles, or what kind of baffles/vents should we buy, to maintain >1” vent for 5’ sloped ceilings above a kneewall, which can only be accessed from the top attic?
At this point, the easiest fix for the slopes will be to build/buy a baffle and blow cellulose from the top attic. The house is mid century, and the rafter bays are uneven widths (often varying by 1”). Given that we wont be able to secure the baffles well and will have to insert these from above, easy and effective is the goal.
Thanks.
GBA Detail Library
A collection of one thousand construction details organized by climate and house part
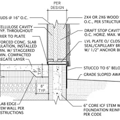
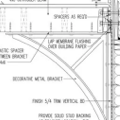
Replies
Emerson, the simplest solution would be a manufactured insulation baffle. Many insulation contractors like this one, which I spec regularly: https://www.brentwoodindustries.com/construction/accuvent/. They have both 1" and 1 1/2" versions. Some insulation contractors say they aren't rugged enough, in which case you can make your own (1/4" plywood or 1" rigid foam are the usual choices; just add 1" "legs" to make a flattened "U" in section). It's not important for 100% of the framing bay to be filled with the baffle. Ideally it would be airtight but with dense-packed cellulose, that's not critical either.
Emerson,
Whether or not you can accomplish what you hope from the attic above depends on the available space in the attic, the length of the insulated section of the sloped ceiling, and the skill of the installer.
I'd be interested in hearing from GBA readers who feel comfortable with this approach (that is, sliding baffles into the rafter bays from the attic above, without disturbing the drywall or plaster ceiling of the bays that need to be insulated). I'd like them to share their tips.
Martin
The space in top attic is moderate. Length of insulated section is about 4’. The skill of the installer remmains to be seen, haha.
While we stand by for others’ input, what would you do in this instance?
Thanks.
Emerson,
Q. "What would you do in this instance?"
A. I would post a question on GBA, asking readers who have done this successfully to give me advice.
If no one volunteered any tips, I would probably build some light-weight, sturdy baffles out of thin plywood with rigid foam legs, and make them a little long so they could be secured at the top. I would hope that the pressure of the dense-packed insulation would be enough to keep the bottom of the baffle in place.
“I would hope that the pressure of the dense-packed insulation would be enough to keep the bottom of the baffle in place.”
What do you mean by this? FYI, at the bottom of the bays, there is a 1.25” channel visible above 6” of rigid foam that was placed between rafters (we moved the thermal boundary in the kneewall space).
I agree, tips will w be very helpful!
Emerson,
If you have a method of supporting or securing the bottom of the ventilation baffles that you intend to slide down from the attic, then you're all set. I was assuming that the ventilation baffle would just flop around in the rafter bay until the dense-packing hose was inserted and the insulation was installed.
Martin,
It's more like a wall at the bottom of the bays (w/1" channel above it) than a support. That said, your point is well taken. We can easily (?) attach a 14"x5" piece of rigid foam to the bottom side of a 1" foam board (or thin plywood) baffle, to serve as a support. Is this what you are suggesting? Thanks.
Have others created baffles and installed into 4' sloped ceiling bays, from the top attic?
Michael Maines, Thanks for suggesting the Acuvents. Reading a bit more about out situation, do you still think them a viable solution to install from the top attic?
Emerson, I don't have firsthand experience installing them so I can't say for sure, but they seem like just the right balance of rigid and flexible. If you could upload a photo of what you have it would be easier to understand your limitations.
Thanks Michael, I can do upload photos. Will take me a day or two. The guys I hired did half the job very well and half the job very poorly. Real PITA, and wasted 3 months of my time with all their return trips to fix it, before I fired them. At least they used high quality products, which I am repurposing.
Emerson,
My company has done this many times, its no different than slipping proper vents in attics, just takes a little finesse. I use plastic chutes, like an Accuvent or Provent, not polystyrene because your enemy is roofing nails.
Usual tactic is to pull batts if the slope insulation is batts, or compress the loose fill enough to slide the chute in without snagging roof nails. Then you take a dense pack hose since a 2" doesnt usually slide in as nice and fill the cavity. The pressure from the fill raises the vent to the roof deck and wont go anywhere. I have not had any problems with crushing. They make extra long chutes, usually 4' isnt long enough to do slopes and stay above the upper attic R49 fill. They will distort some, but will maintain an air channel.
Ive attempted to use foamboard in the past in a few situations against a dense pack and snapped the foam board, it doesnt withstand the pressure when spanned at all.
T Carlson, Thank you, that is very helpful and just what we will do. I especially like the suggestion for extra long Accuvents; I had been concerned about this.
1. Currently at the bottom of the bays there is the end of 6" EPS that was cut and cobbled into the rafters along the roofline in the kneewall area (poorly done by the insulators, which is why we're redoing much of this work), leaving a 1.25" channel. Have you ever similarly tried to protect a lower air channel/do you have any suggestions how I can avoid filling that extant 1.25" channel when I blow cellulose into the sloped bay?
2. Do you know if I can I do any sort of "dense pack" with a DIY cellulose blower from HD?
1. Dont really follow. You can temporarily block openings with whatever while you are blowing, then remove.
2. Maybe. HD usually has little Krendl 475's or equiv which on paper can make dense pack pressure, but Im sure they arent maintained. I rented one of my local HD machines when I wanted to run an extra machine on a job and it was an incredible POS.
If you havent done it before and you dont know what dense packing feels like at the end of the hose you will struggle. My advice would be to build a test box so you can practice dense pack beforehand if you insist on doing it yourself.
Martin - I also think that sliding baffles into rafter bays is do-able. Four or five feet is probably the maximum that one can do. Foamboard and mineral wool worked for me. I used thin strips of foam to create the vent space, glued those spacer strips to the rafters / roof deck, then slide the foam board in with some glue on it, then pushed the mineral wool in underneath (which compresses just enough to fit snugly and keep the baffle in place). I doubt any contractor would do this, though. It's time-consuming work. With 24in O.C. rafters, I had to add a middle spacer strip to keep the thin foam board from bowing in the center of the cavity. Picture here (hopefully):
https://www.greenbuildingadvisor.com/sites/default/files/sloped%20ceiling.jpg
Emerson - I think that T Carlson's suggestion will be easier, but depends on circumstances. Can you ensure that the cellulose won't fly out the far end of the bay? Is it sealed up? DIY dense-pack is possible but read up a bit before doing it. The stronger the blower the better. Menards has more powerful machines than HD in my area. Here's some info:
https://www.greenbuildingadvisor.com/community/forum/energy-efficiency-and-durability/101926/dense-packing-cellulose-krendl-425
T Carlson, Thank you.
Joe Duchek,
The photo is impressive, nice work. I'd actually prefer to outsource this, but as you said, it's PITA work. The insulator I hired screwed me on this, and I don't think I can get anyone to come do it for a reasonable fee. FWIW, I've been using the expression "dense pack" loosely; I really just want the space filled.
In terms of the far end of the bay, there is currently 6" of EPS and 1.25" vent above. I want to maintain that air channel, of course, so would have to be very careful that cellulose doesn't leak in there. Was that a factor why you used mineral wool? We have about 25 or 30 bays, and I'll have a helper.
Thoughts appreciated.
Emerson, out of curiousity what is a reasonable fee?
If access from above was average I would charge you around $900 for 25 vents, that's $36 per vent installed and filled and most homeowners would pass and do it themselves. What is your knee jerk reaction to that cost?
There are other companies in my area that I know need to get more than that. It wouldnt be worth my time to do it for anything less. An average house with knee walls is easily well over $5,000 air sealed, vented and insulated properly and Im not sure those people will get their money back in a reasonable time frame, which is why its such a subsidized industry.
That is one reason why home performance contracting is basically dead in anything but large metro areas with guys that will travel.
T Carlson, That's a good question. When I fired the bum insulators (whom I selected because I thought were the best - certainly not the cheapest!), I got stuck having to finalize the slopes myself. I also have 350sqft of floorboards, mostly lifted, where I need to fill 7.25" cavity beneath the boards w/cellulose, replace the boards, and then blow above boards to total R60. I have created plywood barriers and am ready to do all of that work myself for about $650 material cost, including a helper. I can also do the slopes myself, but they would be a PITA. I suppose if I could get all the work done (350sqft +slopes) for $1500, I'd do it. But I don't think I can get it done for that amount. Maybe I'd pay a bit more - BUT after hiring a well-regarded insulation company who proceeded to fill the top half of the bays w/4" polyiso and crookedly left the bottom half of the bays UNINSULATED, thinking I would never notice, I'm inclined to think I can do a better job, with less hassle, than hiring it out. That's "where I'm at." What would you charge for that work?
Hmm, so you're putting floorboards back in then blowing over the top?
Baring it all, I would have ripped the floorboards out permanently, blew in your R60 for 350SF for $590 incl floor disposal, vents at $900 and an air seal in each exposed floor joist, Im guessing an equal 25 cavities for $295 for total of $1785 if I liked you, could stretch that to 22-2400 if I got the PITA vibe, which no offense but by your posts I would have done if you werent a referral. Work impeccible of course, we practice leave no trace, warrantied unofficially until you died, maybe throw in a unadvertised before and after blower door if the air sealing was a large bypass opportunity since it would be a short day anyway. If your house is all jacked up price goes up but based on the pics youve been posting its not too bad.
You just got to find the right guys.
BTW, you probably wont find long chutes unless you order from a specialty dealer, so you use 2 chutes per bay, remember to lap the 2 chutes shingles style in case of a water leak. Your tip of the day.
T Carlson, Are you local? I wish I found you to begin with. Ha!
Yes, even though the floorboards will be covered, they were there originally and quite nice, so why not keep them? That's my thinking anyway.
You in the dairy state?
You know you could repurpose your floor boards to one of those wood walls behind the 1/2 bath toilet that everybody wants now, if thats your thing. When people want to keep the wood we drill 3" holes usually and dense pack through that against an onion bag. Otherwise what happens is the cellulose settles under the boards and you get an air channel underneath the floor.
Good luck with it.
T, You know, that's an interesting point. We'd been planning to "pack" under the floorboards to avoid settling, but not with an onion bag. Most of these floor boards are already up anyway. Is there another material that you would use? I mean, we could lay batts beneath and above the floorboards.
T Carlson,
Based on your helpful suggestion, we've decided to remove the tongue/groove floors excepting in two small spaces for storage, where we will do our best "dense pack" beneath the floorboards (and settling will cause no harm anyway). We also have a plan B to gain access to most ofthe slopes from below. I can see the light at the end of the tunnel. Thanks!