Insulating Basement in Flood Plain

Hello, my wife and I purchased a flood damaged house in our home town last year. The flood was three years ago and resulted in four feet of water in the first floor. It was considered a 500 year flood, before this the house had never seen water in the first floor in it’s 60 years, though the basement has flooded multiple times. We’ve restored the first floor to that of a normal house and I’m now looking at two areas to work on: my desire to have a basement hangout and weather proofing. I figure the best place to start is where the two meet. I’d like to finish half of my basement and insulate the rest. I’ve inserted foam board into the rim joists I could access and used can foam to seal the edges and sill.
I know the basement will flood again and am willing to accept a certain cost of having to restore my basement if need be, but I want to be as smart as possible about it. My best thought so far is to use tongue and groove XPS foam board floor to ceiling glued to the wall and then covering it with some sort of sealer. The two forms I’ve found are the Quikcrete substance they use to cover outside foam applications and Styrospray, a substance used mostly for foam props. I’ve read the XPS doesn’t allow mold but I’m not sure if sealing one side of the board would trap moisture in and ruin that property. I’ve thought about just using 4″ think boards and simply painting them, but I would really like them to be tougher than normal especially on the short side since the top of the wall is about 1/4 inch inside the bottom.
I know the smartest way to finish a basement in a flood zone is probably to not do it, but if anyone can give me insight on a way to minimize my risk/cost I would really appreciate it. I don’t need it to look like regular living space but I would like to be able to have a durable, paintable surface that can also help insulate. Thank you.
GBA Detail Library
A collection of one thousand construction details organized by climate and house part
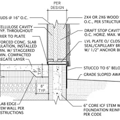
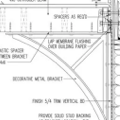
Replies
Sorry, forgot to mention I'm in Zone 6A
Joseph,
My suggestion: install EPS on the interior of your walls, and cover the rigid foam with cement backerboard.
(Building codes require rigid foam to be protected as a matter of fire safety.)
You're right that you will still probably have a mess on your hands after the next flood. Make sure that you don't have any HVAC equipment or a water heater in your basement. And I would install all electrical wiring in the ceiling -- with none on the walls.
Joseph, Martin has hit on what may be the largest impediment to your plans: A conflict between practical safety and the electrical code. The code specifies the location and required number of outlets and switches for finished areas. These locations are almost inevitably going to be under water when your basement next floods.
Thank you Martin. Your answer leads me to a couple more questions, some for curiousity sake and some practical. Can you explain to me why EPS over XPS? Also, were going to get a quote for having foam sprayed in to at least the bottom 5 feet or so of the first floor (our big summer project will be replacing the siding so while it's off we figured it'd be a good time to look into that), if they also sprayed the interior of the basement would that withstand a good soaking? And could they form it straight enough without a frame? And lastly, could I install the backer board with fasteners into the foam instead of glue so that I could take off the backer board to let the foam dry out?
Thank you for your help. I've learned a lot in this process but I have a long long way to go and this site has been great reading the last few days since I discovered it.
A flood-prone basement can be insulated without it qualifying as finished space. Only if it's turned into full-on living space would the electrical codes for outlet spacing become relevant. If the plan was to slather on some QuikCrete Foam Coat, it doesn't sound like the interior finish for the new bedroom or game-room.
EPS has a somewhat higher fraction of truly closed cell structures than XPS, and even though it takes on moisture into it's interstitial spaces between it's macroscopic bead structures when submerged, it dries very quickly compared to saturated XPS. The resistance of EPS to long term immersion is quite favorable, which is why EPS (and not XPS) is used for everything from crab pot buoys to dock floats.
Another reason to use EPS and not XPS is that XPS is blown primarily with HFC134a, which gives it a higher initial R/inch than EPS of equal density, but it packs a greenhouse gas punch about 1400x CO2. EPS is blown with penane, at about 7x CO2. And after a handful of decades of use as the HFC blowing agent leaks out it's R-value eventually falls to that of EPS of equal density & thickness.
Adhesives alone would not work from a fire-code point of view for hanging the foam & thermal barrier (be it tile backer or something else), since the test conditions for thermal barriers are at temperatures well above the service temperature of the adhesives. Mechanically through-screwing the thermal barrier to the FOUNDATION (not just the foam) is required, or some other mechanically secure structure such as a non-structural studwall (probably not what you want to do in a flood prone basement). In some areas intumescent paint applied directly onto the foam is considered acceptable fire protection for unfinished insulated basements.
Thanks Dana, for the good explanation of why EPS.
I wonder if you would want to try to do it in a way that facilitates disassembly for cleaning and drying after a flood. Foam+cement board panels attached to the wall with machine screw threads so the panels could be taken off quickly and easily if needed. Seal the edges with weatherstripping instead of caulk.
If somebody makes you put in electrical outlets below flood line, you could put all those on a separate circuit with a lockable disconnection. After inspection, turn off the disconnect, lock it, and never turn it on again.