Insulating and ventilating a vaulted ceiling with polyiso foam

The family room in our home has vaulted ceilings and gets very hot on a warm day – to the point the air conditioner can’t keep the room cool. The current construction of the roof & insulation ceiling is:
The roof is dark composition shingle over ½” CDX plywood. The framing is 2×10 rafters 24” on center. And the room is finished in sheetrock. Each rafter bay is stuffed with fiberglass insulation. 3 small ventilation holes are drilled at the end of each rafter bay. The rafter bay cavity is 9″ high. Ventilation is minimal.
While we have R-30 insulation – the room still gets unbearably hot. Our guess is the lack of ventilation allows heat to build up and ultimately overwhelms the insulation.
We are looking at re-insulating with polyiso boards and increasing ventilation. We have 3 different options and trying to find the best approach for minimizing thermal gain in our home. We live in central East SF Bay Area. Summers are dry and can get very warm – 100+ degree days not uncommon.
In each option we increase ventilation in each rafter bay.
Option 1
Use 2 sheets of 3” polyiso, providing R-36. Create a 3” venting space between the insulation and the top of the cavity (9″ Cavity – 6″ Insulation).
Option 2
In this option we increase the insulation by 1.5” getting to 7.5″ total insulation – increasing the R-Value to about R-45 – Create a 1.5” venting space between the insulation and the top of the cavity
Option 3
In this option use two 3″ polyiso sheets – but we Increase ventilation flow around insulation boards by putting 1” furring strips between each 3” sheet of polyiso. Our goal is to increase airflow between polyiso sheets to reduce the overall temperature in rafter cavity. Net result is 1″ of airflow between boards, 2″ between insulation and top of the cavity.
We would appreciate your opinion on the best approach.
Thanks in advance for your help – Frank Galdes
GBA Detail Library
A collection of one thousand construction details organized by climate and house part
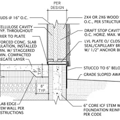
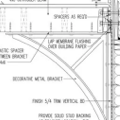
Replies
Frank,
Several observations:
1. Option 3 should be imediatiately eliminated. If you ventilate between layers of insulation, you are undermining the insulation's R-value. So take that option off the table.
2. I suspect that your house lacks a ceiling air barrier. If that's true, performing air sealing work at the ceiling level is essential. I tend to be a skeptic concerning the value of ventilation -- it rarely helps improve the performance of cathedral ceiling insulation. If your roof is impossible to air condition, increasing ventilation through your rafter bays clearly won't help.
3. None of your options address thermal bridging through the rafters. The best places to install your polyisocyanurate panels is not between the rafters; it is either on top of your roof sheathing (an option which would require you to re-roof your house), or between the bottom of your rafters and the ceiling drywall.
Frank,
I agree with Martin about eliminating option 3, and I also agree about using one layer of foil-faced polyiso as a thermal break/air barrier underneath the rafters, with all seams taped and all perimeter edges foamed for air-sealing.
But I disagree with Martin about the benefits of roof ventilation. While the color of the roofing is far more significant in terms of summer heat gain, with a dark roof adequate ventilation not only reduces ceiling temperature but also roofing peak temperature which will prolong the life of the shingles, and it will allow the roof sheathing to dry if there is every a leak. If you can afford to re-roof with a light-colored roofing, you'll reflect much of the solar energy back to the sky.
However, "3 small ventilation holes" in each rafter bay (I assume you mean in the soffits) is no adequate and completely inadequate if there is no continuous ridge vent to serve as the exhaust. You should install continuous soffit and ridge vents (preferably ridge vents with external wind baffles to prevent infiltration of rain).
You could keep the fiberglass in place and add a layer of polyiso under the rafters, or you could eliminate the poorly-performing fiberglass and install additional polyiso between the rafters. But this is how I would recommend it:
Leave a 2" ventilation space under the roof sheathing, install the first layer of 2" foil-faced polyiso, leave a 1" air gap and install the second layer of foil-faced polyiso. Leave the remaining 2" gap and install the final layer of foil-faced polyiso under the rafters and thoroughly air-seal.
Those 1" and 2" air spaces will provide a radiant barrier to summertime solar gain and offer a "free" additional R-3.5 for each space (@ 45° pitch with two facing foil faces = emissivity of 0.03). That will give you an R-41 roof assembly with good ventilation and good radiant barrier. You will notice a dramatic improvement in indoor comfort and cooling costs. If you add a white roof, the improvement will be even greater.
Robert's layering method is absolutely the best way of insulating. Furring strips are usually the way to achieve the R-3.5 gaps. This is one of the rare cases where you can get something for nothing.
The white roof suggestion just might get you the most bang for the buck. The Henry's elastomeric white roof coating at Home Depot is only about $0.12/sq.ft. Caveat - - I'm not sure if Henry's considers the stuff compatible with asphalt shingles. In practice, I've seen it last 12+years on a well-sloped roof. The #105 primer is also cheap and helps it stick. Coating a steep roof is dangerous unless you can do it from the ground with a long-pole roller. Up to 4/12 pitch is dead easy, sweep the roof, pour it on, roll it out.
"Shasta White" shingles are an improvement, but absorb 2-3 times more sun than a white coating. Silver coatings don't perform as well as white.
A crazy idea but with easy installation is an exterior polyurethane sprayed on roof layer. Don't even have to strip the shingles. Coating maintenance is not expensive, but is MANDATORY.
None of these coating ideas will add resale value to the house, but neither will the R41assembly.
If you decide to ventilate behind the roof plane (which your building inspector might REQUIRE) I would consider powered ventilators that can work in the early evening when you need it the most. (that would eliminate the solar powered ones). Natural convection is 5x slower than forced convection when moving heat with air.
Even more important is exterior shading of east or west facing windows. If you have the overheating in October, you also need shades for the south windows. http://greenbuildingindenver.blogspot.com/2009/09/sun-control-one-of-solutions-to.html
In a Florida Solar Energy Center study of roofing, attic temperatures and heat flux to the interior, a vented white metal roof performed better than any except a white tile roof, whose mass delayed peak temperatures until late afternoon. They also found that doubling the ventilation ratio (from 1:300 to 1:150) improved the performance of a dark shingled roof with radiant barrier.
I agree with the poster that ventilation is important. You are in a somewhat damp environment, and your insulation may have absorbed significant moisture over time, degrading its R value and causing it to absorb thermal energy. Fibrous insulation can still be used, but you should have ridge vents, soffit vents, and an air gap running between the two so that the insulation can be ventilated by leaving a gap between insulation and sheathing. Avoid use of Rafter mate type structures if you can, since this will cut the insulation off from being ventilated, but if you have to use something to do the spacing, buy some GAF ridge vent mesh material and staple it to your sheathing. That will keep an air conduit open and prevent moisture buildup within fibrous insulation, .
I'm not clear about how the layered method differs from the initially proposed option 3. In the layered method while the gap isn't intended for ventilation purposes I could see a poor execution of both option 3 and the layered method giving similar results.
I would reiterate further examination of the state of the ceiling's air barrier. You could do a blower door test with infrared thermography or create a new air barrier with taped polyiso boards on the interior of the rafters as has been suggested.
Sometimes (if not often) a good idea doesn't get executed so well in the field. Retrofitting polyiso boards between rafters can be done well or poorly. As much effort should go into finding the right person to do the job as is needed to figure out what is the right thing to do.
Frank, in what direction(s) is the room oriented, and how much glass is there?