Insulating an uninsulated Cape-style home (cathedral/knee)

Hi all, new member here; new homeowner too.
I’m working plans to insulate my century old home that appears to be currently completely uninsulated. The home is in USA climate zone 5A, eastern NE. The main level ceiling/attic floor joists are 2×6, with all of the rest of the framing appearing to be 2×4, roof included. The bonus space in the 1/2 level attic area shares it’s framing with the roof. The interior is mostly plaster and lath, with some drywall in a few renovated spaces. There is also a single knob and tube circuit, with extensions and other “upgrades” that are not to code that need taken care of. The siding is aluminum lap (I haven’t looked under it yet), the 3-tab asphalt roof is recent and in good shape, and is on top of OSB sheathing (which is on top of planks nailed to the rafters). There are no ridge vents on the roof but a gable vent on either peak, and a few soffit vents around the soffit. There is also a single dormer in which a bathroom has been placed.
Right now, my plan is to basically renovate the attic, mainly to get more space between the ceiling and the roof sheathing: 2.5″ (roofing nails obstruct ~1″) is not enough space to properly insulate, let alone work. I’ll also need to deal with indoor air quality and ventilation, as the water heater, furnace, and stove are all gas powered with no intake (natural draft is the correct term?), and exhaust through the attic. Depending on how well I can seal the place, mechanical venting is in order: the only current active venting is the range hood: neither bathrooms have exhaust fans, only the full bath on the main level has a small open-able window inside the glass block.
I’ve consulted with some friends that do contracting work on the side, and they’re recommending I take the typical faced fiberglass batt on the knee wall and floor (some blown in too), and a couple of rafter baffles to “ensure” venting. They are opposed to some of the “non-conventional” ideas I’ve been reading about during my research (a simple example: “I’ve never heard of insulation on the exterior of the construction; it’s not common, at least not around here”), but I trust their advice. Thus, I’m kind of torn on which design approach to take. I believe I can trust all of my building science research, and I believe their advice is simply based upon what they know gets them work.
I’m open to all ideas, including the “hot roof” designs both with and without venting, and an unvented, rafter-insulated approach with blown in cellulose (likely dense-packed) is what I’m considering. I’m planning to include the side attics and the “top attic” (the ceiling doesn’t go all the way with the gable, it’s flattened) in the conditioned space. I’m also planning to seal up the existing walls on the main level as best I can and dense pack them with cellulose from the attic or holes in the plaster/lath.
I’m wondering: 1) should I trust my friends’ advice and stick with the “norm,” or should I trust my research and formulate a project-specific approach, 2) should I include ventilation in the design, and 3) where should I place the air barrier (in relation to the insulation) to ensure there are not condensation issues? By taking down the existing plaster and lath, I basically have a blank canvas to work with, and I can “fix” the knee wall by working around the poor framing style in my design. I suppose a 4th can’t hurt: where can I (easily; non-confusingly?) find information on local residential codes regarding insulation/roofing/siding (and electrical, though that’s where I’m most comfortable)?
I’m going to take the advice from this Q/A and formulate a design/plan for critical review. In the past few weeks I’ve learned more about building architecture, code requirements, and how to properly insulate than I imagined I would need to, but that’s okay because it’s been lots of fun. Thanks in advance for any advice!
GBA Detail Library
A collection of one thousand construction details organized by climate and house part
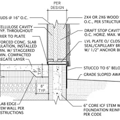
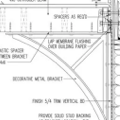
Replies
With 2x4 rafters in the cathedralized ceiling space the only way to get acceptable thermal performance is by putting rigid insulation above the roof deck, or take a serious hit in head room. This is best done while re-roofing. In zone 5 as long as 40% or more of the total R is on the exterior of a roof assembly, you can safely put insulation between the rafters snug up against the roof decking. Do do that you start with a air-tight membrane (peel 'n' stick versions OK) over the existing OSB, with rigid foam above that, held down with a half-inch OSB through-screwed to the rafters on which to apply the roofing felt & shingles.
With 2x4 rafters you can get up to about R15 (with rock wool batts or high density fiberglass works too, though there are other issues with f.g.). That means you would need at least R10 above the roof deck for dew point control at the roof deck. You can get there with 2.5" of EPS, or 1" of polyiso with 1" of EPS atop that. More foam-R is always better. With that stackup you'd be at R25 between the rafters, and about R14 at the rafters themselves, which performs comparably to R30 between rafters or joists. That's not current code, but it's easy to build. To hit R49 (the IRC 2012 code min for zone 5) would be more difficult & expensive.
If you did it that way, close off the gable vents, seal the attic spaces, and insulate the entire roof deck that way. It will be easier to make air tight, and perform better than a kneewall & attic floor treatment.
To air seal & insulate the kneewall and get it to perform like new code-min you can put R15 rock wool between the 2x4 studs and 1.5" of foil faced polyiso on the attic side of it, taping the seams of the iso with 2" FSK tape. The foam needs to extend to the attic side of the ceiling below, blocking any joists that would otherwise be a thermal bypass to for vented attic air to go under the conditioned space floor. Seal the edges of the rigid foam to the joists with can-foam. It's very hard to do a perfect job at this, but give it your best shot. You can then install chutes to guaranteed a minimum 1" clearance between insulation & roof deck and fill between the joists in the attic space with open blown cellulose, which is an easy DIY. You can hit R49 with an initial blow of ~15", which will sag to ~13" over a couple of decades. Without a floor to work from it could be awkward at that depth, but it's usually do-able.
If you go the kneewall route & no insulation above the roof deck, the best you can do with the 2x4 rafters on the cathedralized ceiling section is install ~3-3.5" of closed cell polyurethane (at about $3-3.50 per square foot), which will be a big improvement over zero insulation, but would be woefully below code-min. The center cavity R might hit R20-ish, but with~R4-R4.2 thermal bridging a the rafters thermal performance of the assembly would be no better than 3" of (much cheaper) EPS on the top side, with no cavity fill.
Unless there is venting in the kneewall mini-attics there can be moisture issues there with a kneewall & attic floor approach, since the roof deck & rafters in that section will now run much colder than previously. But as long as the air-sealing at the attic floor & kneewalls is near-perfect it'll probably be fine. The north side attic spaces will be the most-susceptible, since they get no solar warming to help cook the moisture out of the wood, so inspect it every year for signs of mold- your nose can tell a lot even with out a flashlight, but use your eyes too.
With any of these solutions, where a flue or chimney passes through an insulation layer that insulation cannot be combustible. Wrapping the chimney with R15 rock wool batting tied in place with steel wire would usually be sufficient to allow you to run the foam or cellulose up against the rock wool.
What are the specifics of the current heating system (fuel, type, & model # if available) , and does the chimney have flues serving anything other than the furnace/boiler?
Hi Dana. I wasn't clear in my post: I plan to tear down the plaster and lathe in the upstairs so that I can extend the rafters to have more space. I'm thinking about using some lumber (2x? probably) laid perpendicular to the rafters to help with thermal bridging/conduction. This will also give me more space, as I can make the ceiling a true cathedral to eliminate the headroom concern you noted: only the slopes will come in, and it will be at a diagonal, so only a portion of the extension. I'm not sure on depth yet, but I've got basically all the room I need this way.
I have taken and posted photos of the house, equipment and space for reference. Most of the photos have captions describing them, but you'll need to view them in the larger view (by clicking on them) to see. You can view them here (apologies if some are not up to snuff: holding a flashlight and getting things in focus is tough): https://plus.google.com/photos/104591573185116125039/albums/6084003000184236449?authkey=CIuVhvzIxMfoGQ
The roofing nails will make it difficult to get any sort of continuous/uniform contact to the rafters without spray foam, but perhaps blown in or f.g. batts won't be obstructed as much as I think. I can always make an air barrier between the cavity extension lumber and existing rafter, or on the interior (or on the rafter w/ e.g. spray foam, but that's $$$ I might not need to spend).
In addition to the furnace, the home has a heat pump. The setup is all Rheem, and the only stickers with model numbers show the following (also in the photos): on the unit above the furnace, sticker says: model RCBA-3765GG17XI (this looks to be the coil unit...) and the outdoor unit sticker says: model RPKB-030JAZ.
Nathan,
Here are links to two articles that should help you:
Two Ways to Insulate Attic Kneewalls
How to Build an Insulated Cathedral Ceiling
You can't put fiber insulation against the roof deck unless you put at least 40% of the total R above the roof deck. If you're not going to re-roof, install 2" of closed cell polyurethane foam (ccSPF) on the interior side, and fill out the rest with blown fiber (preferably cellulose, for the hygric buffering) and NOT batts, which would be much more prone to convection bypassing & condensation on the ccSPF. That would run about $2-2.50 per square foot- it's not cheap, but probably cheaper than re-roofing.
If the ~R12-R13 foam-R isn't at least 40% of the total R, install MemBrain or some other smart vapor retarder on the interior side. With 2" of ccSPF you can put up to 5-5.5" of cellulose on the interior side of it before MemBrain is really needed.
Blowing cellulose in mesh with a box-store rental blower is DIY-able if your contractor buddies can't come up with better equipment than that. If you don't have a ready suppier for blowing mesh, you can do just fine using landscaping fabric as the mesh (just staple the hell out of it, and roll the pillowed out mesh flush with your framing when you're done with a section of 3" PVC pipe to make hanging the interior gypsum easier & flatter.
In this type of stackup, the 2" ccSPF is a class-II vapor retarder to protect the roof deck from moisture accumulation, but is still vapor open enough to dry seasonally toward the interior. It also provides a moisture-tolerant first condensing surface for any moisture that gets in during the winter, but at a warmer temp than the roof-deck proper. As long as the average winter temp at that surface stays 40F or higher you don't need the MemBrain, but the more fiber insulation you have, the cooler that surface is. MemBrain would limit the rate of moisture accumulation in the fiber, but without limiting the drying rate, since it becomes fairly vapor open when the relative humidity in the fiber layer rises above 40-50% RH, which it will be in the spring/summer.
With cellulose as the fiber there would never be liquid moisture in the cavity, it would all be taken up as adsorb in the cellulose fibers. If fiberglass or rock wool there is some chance of liquids forming during extreme cold events, but as long as it's air-tight to the interior not enough to matter, and as long as the interior surface of the foam averages above 40F, or you have MemBrain or similar under the gypsum.
BTW: Even though you're probably not taking it to the nth-degree, most of the details in this guide are relevant, since it's also for a zone 5A climate:
http://www.buildingscience.com/documents/guides-and-manuals/gm-mass-save-der-builder-guide
Martin, thank you for the links. I've actually read through both of them multiple times already, as well as a few other articles on the subject; this site comes to mind: http://thehtrc.com/2014/getting-the-details-right-more-than-1-way-to-skin-a-cat
It sounds like I shouldn't be afraid to try a different approach than my friends were suggesting. I think I'm ready to start coming up with a plan for review. I'll start making some drawings and go from there.
I do have a few more questions, though.
Spray foam is quite expensive (I assume that's what the S in ccSPF is), especially if I'm going to be doing the whole ceiling: that's at least $1200 just for the ccSPF. Is it the roof sheathing, or the roof rafters, or both, that I should be most concerned with regard to moisture issues? Also, what portion does the "roof deck" actually refer to?
I'm wondering what other options I have beside the costly spray foam. What about sealed rigid foam between the rafters? It might be difficult to get continuous/uniform contact with the roof sheathing with this approach, as the OSB is on top of planking, and the roofing nails are everywhere. Though, perhaps the nails will penetrate the rigid foam fine (so I can just press the foam into the nails), and I can fill between the planking with can spray foam to ensure good contact and seal. This would leave the rafters exposed (which I believe are vapor permeable, though the lumber is old lumber, which I read is denser and contains more sap (I did notice some sap spots)). I'm also toying with the idea of clipping off all of the nails flush with the deck with a large pair of diagonal pliers or such, though maybe this is a bad idea (not because it's laborious, but because it might affect the roofing structurally)?
Does the (tar?) paper and asphalt on the roof sheathing act as a vapor barrier, disallowing drying to the exterior? And with your suggestion of MemBrain, I would apply this on the interior of the cellulose, not between the ccSPF and the cellulose? Placing it in the middle of the insulation would still mitigate concerns for the wood rot, but placing it behind all of the insulation protects all of the insulation as well, correct?
I'm going to review all of the resources linked here, especially that 200+ page guide Dana shared (thank you!), and start creating some drawings of different approaches. I'll have some hard numbers this way so that things can actually be evaluated.
Beyond the physics of things, the next concern is making sure I'm conforming to local code requirements. I'm having trouble determining what my local codes are (I'm pretty sure they just reference the common standards, IRC, NFPA 70/70A, NEC 2011 (or is it 2012?)), as well as just traversing the giant documents and finding the pertinent information. Confirmation that I'm looking in the right places would be nice, but if I need to consult with a local expert, I'm willing to do that assuming it actually saves me time. I'm mostly concerned with code affecting how I insulate the main level walls (dense pack cellulose) with regard to plumpbing, ducting, and electrical. I should keep spray foam away from the boxes and opt for caulk instead due to flammability concerns?
Nathan,
It sounds like you are thinking of trying the cut-and-cobble approach. I'm not a fan of using cut-and-cobble for unvented cathedral ceilings, because of several reports of failures. To learn more, read Cut-and-Cobble Insulation.
Q. "Does the tar paper and asphalt on the roof sheathing act as a vapor barrier, disallowing drying to the exterior?"
A. Yes. If you want drying to the exterior, you need to add a ventilation channel directly under the existing roof sheathing, or directly over the existing roof sheathing. You can accomplish the second goal by installing 2x4s on the flat above the existing roof sheathing, one 2x4 above each rafter, from soffit to ridge. Of course, this means that you'll also need a second layer of roof sheathing and new roofing -- and if you are going to that much trouble, you might as well install a thick layer of rigid foam above the roof sheathing instead of the ventilation channels.
Detail question for Dana, Martin and others, related to exterior roof foam: : what do you see as the pluses/minuses with installing 2x4s above exterior roof foam, and venting that channel? Since the foam will stop air movement, we aren't venting hot attic air, but would be venting the OSB/Ply/Advantech deck. Dana is advocating non-vented sheathing here; I've heard different thoughts on this method, both pro and con:
(This was Dana's comment I'm asking about:)
"start with a air-tight membrane (peel 'n' stick versions OK) over the existing OSB, with rigid foam above that, held down with a half-inch OSB through-screwed to the rafters"
Martin, thank you for that read. The article ends with the note about thermal bridging: if I lay 2x perpindicular to the existing 2x4 (which will contain the rigid foam, perhaps even with a 1" or more vent channel next to the sheathing, due to the nails), that would help quite a bit with the thermal bridging issue, if I understand correctly. I could even consider a thin layer of foam, if it would make sense (thinking fan, or thin XPS/ployiso) between the framing (the existing and the extension). Remember, all of the cavity would be blown (dense packed if possible) cellulose, except directly against the sheathing (in the scenario where there is ventilation).
Do you think such a setup would work? I would have to be certain the thin foam layer (if any) allowed the cellulose behind it to dry, but that's about it I think (no condensation/liquid issues). Doing it this way affords me 2.5+ inches of insulation (and room space), and is still likely cheaper than any spray foam option.
That said, I may as well consider the option of starting at the interior of the current rafters, it may be cheaper yet. I don't think the 2.5 inches will be that much: the rooms are big enough they don't feel crampy. I'll mock it up in some 3D sketch to get a feeling before I pull the trigger anyway.
I'm really not considering any options on the exterior of the roof, so I haven't been giving much attention to the ideas there. Feel free to discuss though, that's obviously why we're here. I'm not sure that's a good idea in the middle of winter anyway, but I don't know.
After reading about those failures, I'm liking more and more the idea of a foam air barrier all across the rafters. However, it sounds like Angela's case failed specifically because she left venting in the design, and it was improper (not ridge vents). I wonder if that's the case and the condensation was from the outside air. If it was raining from the ceiling, then there was obviously also not a very good air seal, as you note. Do you think the combination of dense packed cellulose, careful installation (of a single layer, where I can go overboard from the inside without space constraints to ensure proper seal) of cut-n-cobble rigid foam, and perhaps another air barrier in the mix (between rafter/extension or on interior) would still be concerning?
It seems like the main thing we're trying to avoid is placing air-permeable insulation against the cold roof sheathing/deck. This is the case regardless of a quality air barrier, but for some reason if the barrier is against the sheathing, then things are fine. It seems contradictory that a quality air barrier on the inside of the air-permeable insulation is irrelevant if the insulation touches the roof deck. This page seems to share that belief: https://www.greenbuildingadvisor.com/blogs/dept/musings/how-install-cellulose-insulation
The page notes that while it may work, ultimately it's the inspector that needs convincing that the setup works (to prevent moisture-laden air from reaching the cold sheathing). I haven't considered what I'll need as far as inspection goes. Forgive my naivete, but what is typically required for such a project?
Barring exterior modification, spray foam against the sheathing, and dense-packing against the sheathing, my only real option is to go with a vented roof design. That's becomes costly in terms of reduction of living space. I'm really wanting to try a cut-n-cobble approach or a dense-packed approach, and focus my efforts on achieving a quality air seal. There will be plenty of places to place air barriers and reduce convection as I'll be extending the framing, so I don't think assuming a quality air seal is too outlandish.
Martin, are you against such an approach? (Dense packed cellulose in contact with the roof sheathing combined with multiple layers of air barriers on the interior with no vapor-barrier (inside drying design), and a meticulous air seal around electrical work (wiring for a single light in each room) and combustion/ventilation air exhaust/intake?
Nathan,
You can't install cellulose insulation (or any other air-permeable insulation like fiberglass or mineral wool) between your rafters unless you either (a) install a thick layer of rigid foam above the roof sheathing, or (b) install a ventilation channel between the top of the cellulose insulation and the underside of the roof sheathing.
On this point, the code is clear. I agree with the code.
This must be very reminiscent for you all: https://www.greenbuildingadvisor.com/blogs/dept/qa-spotlight/rescuing-problem-cathedral-ceiling
I couldn't help but chuckle when reading that article.
Martin, Dana, everyone: thank you for your patience and answering my questions.
I've found a local source on some used 1.5” polyisocyanurate sheet that can't be beat, so I suppose that's what I'll be going with. I'm considering a vented roof with an airtight baffle between the rafters (thinking cardboard with a center foam spacing runner, perhaps with a layer of housewrap facing the vented space) so that I can dense pack in the existing rafter space followed by a combination of the taped polyiso sheets and more cellulose, depending on the price points. This let's me save 2.5” of room space and cut down on cost per R.
One parting thought: dies it make sense to insulate the attic/roof to code if the walls of the rest if the house aren't up to snuff? 3.5 inches of dense packed cellulose won't get me there in the walls.
Again, thanks for taking the time to help me, I truly appreciate it.
Nathan,
You found (and linked to) and old Q&A Spotlight article that address a dilemma similar to yours. But if you wanted to search old Q&A threads, you will find many more threads in which the same questions are asked. I think that no other question comes up as often as: "How do I retrofit insulation in my existing cathedral ceilings?" Here at GBA, we answer these questions again, and again, and again.
Q. "Does it make sense to insulate the attic/roof to code if the walls of the rest if the house aren't up to snuff?"
A. Yes. Code-level insulation (or better) = good, even if the rest of the house isn't there yet.
When your siding starts to rot, you can address your walls.
I worked up drawings for two different designs: one with ventilation and one without. I give R-value totals for the insulation, but I realize that the actual ceiling will be less efficient due to framing and inaccuracies. Locally we're still using the 2006 IRC, which mandates a ceiling R-value of 38 (2012 mandates R-value of 49). I believe these are for the whole wall, not just the insulation installed, correct? It's interesting then that the materials packaging, which accounts for framing in its design, claims it will bring the assembly (wall, ceiling, floor) to the labeled R-value... I assume that is inaccurate and an R-13 batt will actually yield less even if done perfectly?
---- Ventilated Design
https://docs.google.com/file/d/0B9CipiZ5FsCLME1nOTlzakFTdFk/edit
The ventilated design incorporates cross ventilation between the soffit and ridge spaces, using rigid foam and blown in insulation for a conservative cumulative R-value of 45 (4 inches polyiso @ 5.6 R per inch, 6 inches dense packed cellulose at 3.7 R per inch). The ventilation channel is 1 inch, created by affixing tight fitting 2 inch polyiso between the rafter space offset from the interior rafter faces 0.5 inches. Follow that with dense packed cellulose inside a 2x6 "mooney wall" faced with 2 inch air sealed (taped) polyiso sheet (I drew it at 24" centers, but I'm uncertain on the spacing requirements). Finally, drywall hung off of the 2x6 with long screws through the rigid foam with staggered seams.
---- Unventilated Design
https://docs.google.com/file/d/0B9CipiZ5FsCLQTVIckxlVGpVc1k/edit
The unventilated design eliminates all ventilation and is simply four layers of 2 inch polyiso sheet, with the first two layers cut to fit between the rafters and pressed tightly against the roof sheathing, producing a cumulative R-value of 45 (4 x 2 inches polyiso @ 5.6 R per inch). Canned spray foam used liberally (but properly) against the roof deck to fill any irregularities in boundary contact. The outer layer will be air sealed (taped) and followed with drywall attached to the 2x4 rafters with very long screws (4.5 inches of foam). If the very long screws don't work or aren't suitable, I think I can use 1x4 furring attached to the 2x4 rafters with very long screws, with the drywall attached directly to the furring and the gaps between the furring filled with rigid foam.
----
Some quick calculating says that, in the ventilated design, the cellulose alone will add over ~700 lbs of weight to each half of the roof. Woah, that sounds like a lot! Is that a real concern, given that it is spread over a 28 x 15 foot area (very rough estimate 0.012 psi)? With this approach, I don't think I need to be concerned with moisture/condensation and the cellulose sandwich, as I have a ventilation channel (tightly fit, not a perfect air seal) above the cellulose, as well as no vapor barrier (but an as close to perfect air seal as possible) on the interior. Is that correct?
I don't think there are any concerns with the unventilated design, except to ensure proper contact with the roof sheathing, and the ever-necessary air-seal.
----
The drawings don't show it, but there is horizontal framing about 7 to 7.5 feet up from the floor between the rafters, making a flat ceiling. I plan to eliminate the flat ceiling and have a true cathedral ceiling, but I'm not sure if I can remove this framing without concern. I'll have to open the top attic space to get a better look, but I believe there is nothing special, just this horizontal framing. As well, the drawing doesn't show it, but I plan to place a layer (or two) of polyiso between the gable/peak walls where possible, creating a tight air seal. The main floor walls will be dense packed with cellulose, and adjoining an air barrier (perhaps e.g. Tyvek sheets cut to drape down interior of cavities before packing) with the level above.
----
I've found a source of 2" polyiso that is $11 per sheet, yielding 3.069 cents per R per square foot. Dense packing cellulose available at the local big box store comes out to 3.097 cents per R per square foot (when packed at a density of 3.7 lb / cubic foot). High density fiberglass batts (R21 in 2x6) come in around 3.82 cents, with regular fiberglass ranging from 1.3 to 4 cents. New rigid foam is much much more expensive, obviously.
Nathan,
You wrote, "I don't think there are any concerns with the unventilated design, except to ensure proper contact with the roof sheathing, and the ever-necessary air-seal."
In fact, there are concerns. You have chosen the cut-and-cobble method. You should consider the fact that there have been several reports of failures when the cut-and-cobble method is used for unvented cathedral ceilings. I don't recommend this approach.
For more information, see Cut-and-Cobble Insulation.
Nathan,
The code appears to allow the cut-and-cobble method, as you point out, although it would be better if the code were written more clearly.
Whether or not a code official would accept the cut-and-cobble method, a builder still has to decide whether the method is worth the risk. I agree with you that, if your installation method is meticulous, the method should work. However, I feel duty bound to inform you that there have been several reported failures of the cut-and-cobble method when used for an unvented cathedral ceiling.
Only you can decide whether this method is worth the risk.
Martin, I thought that it was acceptable to place rigid foam sheathing in direct contact with the roof sheathing, so long as there were fully butted sheets of taped rigid foam on the underside of the rafters. That is what I'm proposing with the 4 layers of polyiso design. I may have to fur out the 2x4 rafters to create a flush face for the first un-cut layer, but there will be two full layers of polyiso sheet between the rafters and drywall (or furring for drywall, then drywall, if necessary). This should create an excellent air barrier and provide excellent thermal bridging mitigation (4" of polyiso insulation between roof/ceiling rafters). It should provide an excellent vapor barrier as well, basically just like ccSPF. The spaces around the roof/wall (and wall/ceiling more so, as this is a sort of "raised heel" design) will be properly sealed and insulated as well, and the soffit vent spaces and gable vents closed/sealed.
This seems to be complete acceptance with Section 11 of the 2012 IRC (though I'll technically need to make any new wood framing to code if I remove / raise the ceiling flat). 100% air-impermeable insulation in complete contact with the roof sheathing, with all seams taped (two layers, or three layers even). I think if I couple this with some air-impermeable membrane draped down the insides of the exterior wall cavities before dense packing, the setup will create an excellent air barrier and help ensure moisture laden air (due to poor air seals on main level, though I'm obviously going to try my best here with proper spray foam and caulk) doesn't creep up the walls and into contact with the edges of the insulation where it might be more difficult to properly seal.
Bob Irving and others, Nathan.
Where I build many homes have been built with rigid foam above T&G. The ones who add a vented roof above the rigid are doing well. The cold roofs when they go bad are disasters that cost tearing off the entire roof system and starting over. I was asked to do one of those jobs... I would have done it if it was time and materials only. There is no way to know how much damage is hidden.
Rigid foam will leak at the seams. It will. Now if a leak proof item like Grace ice and water is applied then the leak doesn't cause problems of warm interior air moving through the rigid. So a cold roof should have the Grace and can work. A vented over rigid works.
As to cut pieces of foam. I do not like the idea for walls or floors and despise the idea for cathedrals. Cathedrals are just waiting to cause problems compared to lower down.
Cut foam has much more edge per square foot of rigid application. It only makes sense that the risk of a leak past the edge is much more apt to happen. I'm not a gambler when the odds are against me and or unknown. I loop planes that are not aerobatic rated, but I have trained to do so at the proper low g forces that make these loops 100% safe to do in a plane that should not do so. The risk is eliminated. So for cold roofs, you need Grace. For unvented cut and cobble, you need a special connection to another universe where our rules here on earth do not apply.
Air leaky roofs don't always show up for a few years too. Some I have dealt with went 10-20 years and or to the first shingle redo... Rip off the shingles... and guys almost falling through into the home through the rot.
Cut and cobble at your own risk. I will not.
The net risk increase of a cut'n'cobble on an unvented assembly isn't worth the additional ~R1-R2 of "whole assembly R" performance you get out of the higher R/inch material. For that cut'n'cobble to work all the wood has to be dry when installed (and it can't even leak even a tiny bit from above), and the air sealing has to be perfect on day-1 and for the next 25 years. Any thing that requires perfection to work is a bad design, not very resilient.
Dense packing cellulose will be more protective & resilient, since it buffers & redistributes moisture without loss of function or damage (within limits) sharing the moisture burden with the roof decking. Using a smart vapor retarder on the interior side of the cellulose as the air barrier also adds resilenence.
You can then put rigid foam to the interior side of the rafters, but NOT foil faced polyiso, since that creates a severe moisture trap with the low-permeance roofing materials above the roof deck, which is the opposite of resilient. The best approach would be to use unfaced Type-II EPS (about 2.5-3 perms @ 1", 0.8-1 perm @ 3" ), and put a smart vapor retarder between the foam & fiber. Seal the seams of the EPS with tape + duct, mastic.
All rigid foam will expand & contract seasonally with temperature at a different rate than the structural wood, which creates a mechanical strain, and most rigid foam will shrink slightly over time. Taping & sealing the seams is good, but relying on taped seam of rigid foam as the PRIMARY air barrier is a dubious practice at best. Using a variable permeance membrane such as Intello Plus or Certainteed MemBrain is cheap insurance. Putting it between the foam & fiber reduces the likely hood of damage over the long term.
Nathan,
While Dana feels confident that his proposed assembly is low-risk, you should be aware that it violates the building code.
Most building science experts feel that installing cellulose in contact with roof sheathing is risky, unless:
(a) you have a significant amount of rigid foam on the exterior side of the roof sheathing, or
(b) unless you have a low-permeance membrane and a ventilated air gap above the roof sheathing.
If all else fails, I can add an inch or two of ventilation between the roof sheathing and the rigid foam. Simple solution, at the expense of longer drywall screws (4.5 inches just became 5.5 or 6) or more layers of furring between the rigid.
For Dana: the choice for rigid polyiso foam sheet is because it is actually the cheapest insulation material I have available. The extra R-per-inch was the initial appeal, and it just happened to be cheaper. I understand your thoughts here comparing it with your cellulose option, however. Wouldn't placing 3.5 inches of polyiso between the rafters (WAG 90% area), as well as breaking the conductive bridging with 4.5 inches of polyiso beyond the rafters actually perform very well? 3.5 inches * 1.25 + 4.5 inches * 5.6 (R-values: wood: 1.25, polyiso: 5.6) yields an R-value of ~30, versus the non-stud cavities of 45, together yielding an R-value of ~43 (~10% studded+polyiso area). Do you agree?
Another idea: what if, between the layers of cut rigid foam between the rafters and/or the full polyiso sheets on the underside of the rafters, I placed a complete/taped layer of Tyvek/air-barrier? That should eliminate concerns related to the air-barrier quality of the layers of taped polyiso sheet (maybe eliminating the need for tape, if you're daring), which is the primary concern for moisture condensation inside the unvented space.
It looks like if I want to use a ventilated design, I will need to re-do the soffit vents. It looks like the rafter tails are boxed in on the underside with plank sheathing, separating them from the soffit space, which doesn't have enough ventilation on the siding/facing anyway. This will add more to costs if I can't find an acceptable solution to the air barrier concern of multiple layers of taped rigid (polyiso) foam.