Insulating an attic framed with steel beams and precast decking

I am an architect, working on a renovation of a building constructed in 1957 in Nashville, TN. The building is uninsulated and has an attic structure unlike any I have seen. There are steel I-beam “rafters” with precast concrete planks spanning between them as roof decking. On top of that is some kind of weather barrier (I have not seen it, but probably some sort of board and some tar) and then a slate roof. A photo is attached.
We have been considering various options for insulating this building, including insulation at the ceiling level (keeping the attic uninsulated) and another option of applying closed-cell spray foam to the beams and roof deck and making the attic a conditioned space with HVAC supply and return. There are a lot of complexities in the ceiling-insulation option — perhaps too many to get into right now. So mostly I am interested in opinions on the spray foam roof deck option.
Most likely we would apply foam to the deck and to the beams in a thickness to get R-30. This won’t be cheap — contractor has estimated $60K or more for it. My concern is that it is an unfamiliar application. I do both commercial and residential design work and have used closed cell spray foam on residential attic roof decks just like this — except they are wood and have wood rafters.
My concerns are: (1) will there be moisture accumulating on the steel beams, either from condensation, leaks, or what might naturally be trapped in the assembly and (2) will that cause corrosion on the steel that can’t be detected because it is all covered up. Also a third concern is that this seems like a major change to the building that cannot easily be reversed if something does go wrong.
Any thoughts or observations on these concerns would be welcome, as would (especially) any experience with a similar type of construction and a similar (or better) solution. A lack of “comparables” that can be evaluated for long-term durability is the source of a lot of my uncertainty about this.
Many thanks.
GBA Detail Library
A collection of one thousand construction details organized by climate and house part
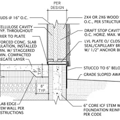
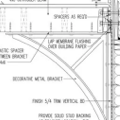
Replies
That looks like commercial-style construction. I've seen this before. Note that those precast panels are often pre-stressed with rerod so be very careful if you drill any holes. I've been warned by structural engineers that coring through rerod in precast assemblies can be a BIG deal.
Your steel all appears to have been painted an is in good shape. If the paint includes one of the proper steel primers, you should have pretty good corrosion protection for the steel. I wouldn't worry about encapsulating the steel with spray foam since that's not going to be much different than the common fire retardant insulation that is spray applied all the time without problems. The steel won't sweat once it's encapsulated since there will be no way for moisture to get to the steel.
My only concern with moisture would be water migrating through the concrete and contacting the steel in the area where the concrete is in contact with the steel, but even that is probably not much of a problem.
Another possibility for you may be to install rigid foam sheets on the underside of the steel beams. You could glue the foam up, and you'd have a ventilation channel between the foam and the concrete to allow for any drying concerns. Usually commercial roof insulation is on top of the deck though, so this would be a bit of an unusual installation but I can't see any reasons why it couldn't be made to work.
-Bill
I get nervous when any0ne combines these three: "lot of complexities;" "unfamiliar application;" and "closed-cell spray foam."
If you airseal/insulate at the interior of the roof assembly, you are making everything to the exterior of that layer much colder and therefore less likely to dry should it get wet.
So:
1. you MUST be sure that bulk water management in the roof cladding and underlayment (particularly connections of flashing to underlayment at any penetrations) is perfect.
2. you MUST be sure that your insulation and air sealing spray foam is perfect.
My comments do not mean that you can't do this approach successfully; just means you really good quality program.
Also, please consider this article I wrote on getting foamed-in-place insulation right: https://www.buildinggreen.com/blog/foam-place-insulation-7-tips-getting-injection-and-spray-foam-right.
Peter
Thanks to both commenters here -- good information.
I saw a link in that article to a spray foam consultant (H. C. Fennell) and I will give him a call -- the owner may be interested in have a consultant and commissioning done on this project since this is such a critical area.
I think safest play is to insulate on the outside and add a new water proof façade.
Walta