Insulating a walkout basment

I’m trying to insulate my walkout basement in Chicago so Zone 5. I read through bunch of the posts but just need some clarification if what I have gathered is correct. I’m attaching a diagram to show exactly what my plan is but just need to figure out if the section above foundation/ground will have any issues with this setup.
Thanks
GBA Detail Library
A collection of one thousand construction details organized by climate and house part
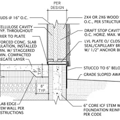
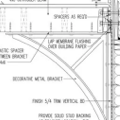
Replies
Tkaj,
The wall above the concrete wall does not need rigid foam in the middle of the wall. If you are using fiberglass batts, just insulate with batts. You don't want any air spaces.
The concrete wall is properly insulated.
As with any insulation job, pay attention to air sealing.
FYI - you should have a brickledge for your brick veneer on the outside of the concrete wall, otherwise, rainwater has a good chance of getting inside under the framed wall.
Tkaj and Armando,
I assumed that there is an air gap between the brick veneer and the housewrap, as well as the usual through-brick flashing and weep holes at the base of the brick veneer -- even though those details aren't shown.
If these details aren't there, Tkaj, then Armando is right -- this wall is in trouble.
An EPDM sill gasket to provide a capillary break between the concrete & wood is a worthwhile detail to add.
Using polyisocyanurate or EPS instead of XPS is substantally greener, due to the much lower impact blowing agents used. Over a few decades XPS performance drops from the labeled R5/inch toward the R4.2/inch that EPS of similar density as it's HFC blowing agents diffuse out. Like polyiso, EPS is blown with low-impact hydrocarbons (usually pentane), most of which leaves the foam at the factory where it is recaptured (to meet local air pollution standards) sometimes burned for process heat.
The slab isn't shown, but 2" of EPS under the slab, stubbed up around the perimeter to meet the wall foam is also "worth it" in a zone 5A location. With polyiso the cut edges without facers should not contact soil, or concrete that is directly contacting soil, but a concrete wall contacting the foil facer (rather than a cut edge) is not a problem.
Yes there is an air gap, flashing and weep holes.
Dana which big box store should you recommend for EPS?
Also it’s a 1967 Construction so there is probably nothing under the slab but I have about 2” of Head room and will be installing foam board on top of the slab and T&G plywood on top of that secured to the slab with laminate floor on top of that.
Basically I will need to fill about 9” to 10” of space with fiberglass bats that n the wall section above ground. Should I just use the R-30 bats for that or it’s better to compress and just stuff R-15s?
Depending how high your concrete wall is, you could stop the lower framed wall at the concrete wall height and create an artistic ledge. Its a good ledge to place pictures, household ornaments, drinks (if you have a game room), etc.
TKAJ: Both Home Depot & Lowes carry a selection of Type-I EPS with facers. Menards sells Type-I EPS with and without facers. Type-I is fine for the wall foam- it's easier to air-seal with tapes (and harder to break off the corrners in handling) using foam with foil or plastic facers. If you're through-screwing the subfloor to the slab it would be nicer if you can find something a bit denser, say some used Type-VIII or Type-II roofing foam. Type-I isn't as "walkable" prior to putting the subfloor down - it can dent easily under foot, and will compress a bit where it's screwed down, but if it's going to be clued down with foam board adhesive rather than screwed down it has sufficient compressive capacity for the room contents with the subfloor distributing the pressure.
Skipping the foam above the foundation and just going with R30 batts would require an interior side vapor retarder in a zone 5 climate. It's better to have the layer of foam in the middle. Type-I EPS without facers typically runs ~0.8--1.25 perms @ 4" which would be perfect. Unfaced Type-II EPS is more like 0.5-0.75 perms @ 4", which is also fine. Type-I EPS with facers is usually MUCH lower vapor permeance (at any thickness.) Fiber faced polyiso would run about 0.5 perms, give or take, foil-faced polyiso <0.05 perms. There needs to be a bit more 1/4 of the total center-cavity R on the exterior side of the interior face of the foam for dew point control (1/3+ would be even better), so analyze the stackup carefully.
These folks can probably take the sting out of the foam insulation costs for you better than a box store:
https://chicago.craigslist.org/sox/mad/d/used-poly-iso-insulation-sold/6439840358.html
Roofing polyiso is fine for the walls, but not the slab. Most foam reclaimers will have Type-VIII or Type-II (and almost never Type-I) EPS of some thickness in stock for super cheap (Typically less than half the cost of crummy Type-I at box store pricing.)
Run this search every week or so- there are others out there:
https://chicago.craigslist.org/search/sss?query=rigid+insulation
Thanks Dana. In regards to my R-30 comment I would only install that on the above ground section and leave the foam and R-15 fiberglass below.
On a different note Emmy whole house has faced fiberglass everywhere else above ground. Should I use faced fiberglass above ground in the walkout basement? Basically the last section of insulation above ground would have a faced bat against drywall and the lower level would be unfaced. It’s a little extra work I know that but just trying to understand since rest of the house has faced fiberglass.
I understood that you meant the R30 fiberglass to be on the above ground section, and with R30 in the walls the exterior sheathing would be too cold in winter to skip the interior vapor retarder, especially if there isn't a sufficiently vented air space between the sheathing and brick veneer. Since there is also a gap between the interior and exterior studs, R30 batts would leave voids.
At reclaimed foam pricing filling that space between the two studwalls will be cheaper than filling it with high density batts.
It's fine to use fiberglass with kraft facers, but not with foil-facers. Most R15s are unfaced anyway, which would be preferable (but not absolutely essential) for the below-grade section.
But if I stuff the 9” (top section) of space with any insulation wouldn’t that cause the same issue as having r30? Meaning exterior would be too cold?
The difference is that the few inches of foam in the middle is an adequate vapor retarder, whereas fiberglass batting is EXTREMELY vapor permeable, even air-permeable, which would allow moisture to migrate freely from the warm wallboard side to the cold sheathing side.
With the foam in the middle the exterior studwall will dry toward the exterior, the interior studwall will dry toward the interior, with essentially no moisture transfer from the humid indoor air to the cold sheathing.
Thanks Dana makes sense. Few more questions. Does it matter if I use 1.5” foam board vs 2” on the walls? Also since there are bedrooms above would there be any transfer of heat or moisture transfer since it’s insulated differently? I was planing on putting foam board in the area where the walkout basement stud wall meets the upstairs floor or would fiberglass bats work in that are as well.
I'd change the upper portion to match (thermally if not structurally) either a typical double stud wall or an external rigid foam wall. Lots has been written about making these safe (eg, cellulose and a smart retarder in the former, adequate foam on the latter).
I'm assuming i should not be using fiberglass bats agains the joist and plate so should i just use 2" of foam board or more 4"? glued and sealed with spray foam form can in the rim joist. and add fiberglass on top of that?
Tkaj,
Yes, you can do as you describe. More information here: Insulating rim joists.