Insulating a pole barn style garage Eastern Washington

I know this has been beat to death but even after researching this issue I’m still not coming up with a direct answer to *MY* specific issue. I’m hoping to try here but with a bit more background detail on what I have going on.
I have essentially a two story garage that is built over TJI joists and a 3″ slab of concrete over tar paper and sheathing on a slope. The walls are just simple 2×6 wood stud construction with horizontal metal sheeting. There is no OSB or house wrap on the outside under the metal. The metal is direct to stud. The metal roof however does have “blanket” insulation so minimal R value but there is some vapor barrier there. There will be gable end vents and the roof ridge will be vented. I will be heating the shop in the winter (Ea Wa Zone 5) to around 60deg while the outside temp will average in the teens and 20’s F. There is very little to almost no humidity here in the summer and I will not be cooling the shop, just using fans.
I have already hung 5/8″ drywall on the ceiling and I’m going to install R38 attic insulation rolls over that. The attic space will remain cold,vented and unused (no storage). On the walls I have installed 1.5″ R-Tech rigid foam insulation with a poly facer on each side in between each stud. I’ve also purchased R-13 fiberglass batts to fill up the rest of the space in the 2×6 studs bringing me flush to stud. Over that I was going to install OSB and then eventually drywall. (See below for vapor barrier info).
My biggest question is now I’ve purchased and started installing this stuff and not feeling comfortable with the topic of vapor barrier. It’s my understanding that since I have a poly faced rigid foam board in between the studs ( I wanted to avoid direct contact of the fiberglass insulation touching the raw metal sheeting) that adding an additional poly vapor barrier over the studs and under the OSB would be a bad idea. Essentially creating a vapor pocket that can’t dry out. I went this route due to cost. I can’t afford to have the walls spray foamed. It’s just not economically feasible for our investment here at this property. I’m really hoping to find a reasonable solution short of taking off the siding off which really isn’t an option at this point. I’m currently OK with staying the track I’m on and just not putting up more plastic on the warm/inside so I don’d end up with a double VB. The OSB will be installed shiny side in and taped with Tuck tape. Then drywalled. Hoping the OSB below will offer some support for the drywall to keep it from cracking and some shear support to the walls.
The long and short of it is I’m hoping to do a decent job insulating this shop without creating a huge problem in the process. Any feedback is appreciated. Thanks!! -Shawn, Cle Elum,WA.
GBA Detail Library
A collection of one thousand construction details organized by climate and house part
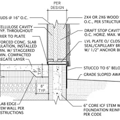
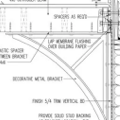
Replies
Hi Shawn.
I have a few questions. What's the R-value of the rigid foam? Why are you installing OSB before drywall? And why radiant barrier OSB?
Hi Brian. The Foam is 1.5" thick, so just shy of 6. It was recommended that I install OSB before the drywall since this building doesn't have any on the exterior beneath the siding. The concern was about lack of shear in our high wind area here and this building does seem to flex and moan a lot. It was recommended that I install it on the inside. Plan was that it would offer some support for the drywall and help against cracks etc.
Got it.
I don't think you have anything to be concerned about with your plan. However, you'll be wasting your money on the radiant barrier sheathing, because the foil needs to face an airspace to be effective. Unless you plan to add an airspace, you can save some money and use regular OSB. Also, I'd consider using sealant around the perimeter of the OSB and taping the seams to air seal the walls. That will go along wall in terms of keeping the walls healthy and efficient. And, do everything you can to air seal the ceiling before insulating.