Insulating a pier foundation floor in a marine climate

What’s the best practice floor insulation assembly for a structure built on a very low pier foundation in a cold and wet marine climate?
I’m rebuilding a very small, very poorly-built, addition in south coastal BC (Canada). The addition rotted out, in part due to poorly managed roof runoff.
The climate here is damp year-round, with 50%-100% humidity. Temperatures go much above 60 F for eight months of the year. Winter means nine feet of rain with temperatures in the 40s (F) while summer means a few weeks of temperatures in the upper 70s (F).
The floor joists are 6″-18″ above soil that’s pretty close to waterlogged in the rainy season.
I’m planning to install tiles over Ditra, which is impermeable.
I’m leery of installing fiberglass so close to waterlogged soil without a vapor barrier, but a vapor barrier on the underside of the joists will be wrong-side and will make a moisture trap between it and the Ditra.
Is XPS or closed cell foam the only way to insulate this floor or is there a more cost-effective technique?
GBA Detail Library
A collection of one thousand construction details organized by climate and house part
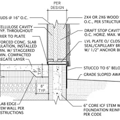
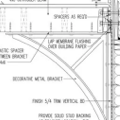
Replies
Joe,
You really don't want to install floor joists that are only 6 inches above damp soil. What you want is a slab on grade.
Retrofitting a slab on grade can work, but it's probably an awkward & expensive approach.
In that climate installing a ground vapor retarder along with minimally vented skirting around the perimeter can work. pretty well.
Since it's probably less insulation to build an insulated-air-tight skirting than it is to insulate the floor, you might as well do something decent for skirting, maybe even pouring a light-duty footing and installing a CMU quasi-foundation to make it an unvented conditioned crawlspace.
Thanks for the feedback.
I don't have the experience to do a slab-on-grade conversion and don't have the budget to hire someone who can.
If a conditioned space is the way to go, then could I do this PWF skirting detail with the addition of 4" of XPS and a ground-level vapor retarder?
Joe,
I'm going to disagree with Dana on this one. I really don't recommend that you install joists that are only 6 inches above the soil -- especially if your soil is "pretty close to waterlogged," as you describe it.
First, you need to lower the grade.
Second, you need to adjust the grade so that it slopes away from the house in all directions.
If these steps aren't possible, you need to pour a slab.
Here are the questions you need to answer if you don't follow my advice:
1. How will you gain access to the crawl space to inspect the area or correct problems?
2. Will you use pressure-treated joists?
3. How will you insulate the floor assembly and make sure that it is airtight? Will you install rigid foam and pressure-treated plywood on the underside of the joists? If so, how do you intend to install them? Is this assembly even buildable? (The answer is yes, it is buildable -- but it isn't easy, and you have to plan ahead.)
Martin wrote: "How will you gain access to the crawl space to inspect the area or correct problems?"
A good point - and one that didn't escape the code writers in BC who precluded building that close to grade.
I winterized a camp with tight space underneath and wet ground. It does not perform great but it works. 20 years ago I put boat cover poly on the wet ground.. skirted it and we put in a low speed vent fan that pumps boiler room warm air down into the crawl. Crawl goes from 2' to 6" in height. I was in this crawl just lost week and there are no moisture problems in the structure even though the are wet ground spots due to nearby lake water level (5' away.)
If we did it again we would have lifted the camp and installed a good concrete crawlspace done to modern specs .
Every project has compromises.... If left open the space should survive, closed you may need to do like I did, but due cover the ground.