Insulating a low-slope roof

Hi Martin,
We are ready here to go ahead with the insulation of our low-slope roof, and decide to go with closed-cell sprayed foam as you recommended.
We had 3 quotes from local company, and 2 of them proposed to shoot 5-6 inches of foam underneath the 1st deck (in green in the following image), assuming we would remove the interior ceiling.
The third quotes also propose to shoot the same deck (in green), but from above this time, assuming we would redo the roof anyway. He said the roofer could provide them openings in the tar and gravel roof so he can shoot the foam down over the whole deck (in yellow in the image). Then the roofer would replace the tar and gravel roof with a membrane as planned.
I know you were referring to shooting the deck from underneath as a good method, and also to over the roof itself covered by a membrane, but is shooting the in between deck from above is also a good method?
Thank you!
GBA Detail Library
A collection of one thousand construction details organized by climate and house part
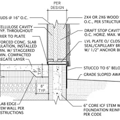
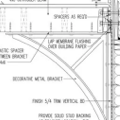
Replies
Francois,
Insulating this layer (the green layer, which is evidently some type of sheathing between the ceiling and the roof sheathing) from above is actually a little better than insulating it from below, because the insulation (if installed from above) will be continuous, without the thermal bridging through the ceiling joists (shown in red in your illustration).
Awesome!
For the same project, I was reading about adding exterior wall insulation from the interior (since our brick wall prevent us to do it form outside). From this article:
https://www.greenbuildingadvisor.com/articles/dept/musings/walls-interior-rigid-foam
Our current wall assembly is (from exterior to interior)
-Brick
-Tar paper
-2" x 12" horizontal planks (huge, old timber, not 2" x 12" from Home Depot)
-1" x 6" tongue and groove vertical planks
-3/4" furring, 16" spaced
-plaster and latte
So far, we removed the plaster & latte and the furring, and our idea was to go with this assembly:
-Brick (untouched)
-Tar paper (untouched)
-2" x 12" horizontal planks (untouched)
-3/4" x 6" tongue and groove vertical planks (untouched)
-7/16" OSB in 4' X 8', PL glued and fixed to T&G planks with screws long enough to reach the 2x12 (this to level the whole wall surface, give back a bit of square stiffness that might have been lost by removing the dense plaster & latte)
-1-7/8" EPS ISOLOFOAM HD 160 as one continuous layer (http://www.isolofoam.com/english/isolofoam-hd-160-0) <<< This isn't their Neoprene infused EPS since I need something thicker.
-2"x3" wall framing, 16" spaced, with 2-1/2 EPS ISOLOFOAM HD 160 in between stud, same thickness as the 2"x3" framing, so the whole thing is flushed
-vapor barrier / reflective barrier (http://www.resisto.ca/product/iflex-reflective-vapour-barrier/)
-1"x3" furring
-5/8" fireX gypsum.
Is that seem like a good plan in our limited option situation?
Thank you.
Francois,
If you can figure out a way to run your wiring between 1x4 strapping, I think that it makes more sense to install all of your rigid foam insulation as a continuous layer, without cutting any of the foam into narrow rectangles to fit between studs. Make the foam as thick as you want to meet your R-value goal, and then install horizontal or vertical 1x4 strapping over the foam (fastened with long screws through the foam to the OSB and lumber).
If you need deep studs for your electrical wiring, I would insulate between the studs with a conventional insulation like mineral wool, fiberglass, or cellulose -- not rigid foam.
It make sense.
Is strapping alone over 4" of rigid foam with 6 inch screws, fixed to the 2x12-1x6-OSB assembly, will be stable enough for the drywall not to crack? I never saw that thick without framing.
If I set the strapping vertically, they would at least rest on the bottom plate, limiting the vertical movement, but I'm wondering if I need any additionnal step to ensure the stability of the wall covering.
ISOLOFOAM HD 160 is their high density kind (110 kPa), so that should help.
I can live with the limited hanging capacity of the wall (for shelves and art, etc).
Francois,
Q. "Is strapping alone over 4 inches of rigid foam with 6 inch screws, fixed to the 2x12-1x6-OSB assembly, be stable enough for the drywall not to crack?"
A. Yes.
Martin,
I was reading this article
https://www.greenbuildingadvisor.com/blogs/dept/qa-spotlight/choosing-right-wall-assembly-2013
and while my wall assembly isn't double-stud flavor, I was wondering if the 7/16 layer of OSB is the best choice of material to sandwich the T&G planks with the 2x12 (see my wall assembly description above).
Should I be concern by the fact the OSB is more mould food than other sheating? Should I use plywood or something else (cement board?) instead?
Francois,
OSB will last a very long time as long as it stays dry. If I were you, I wouldn't worry.
That said, you asked a very specific question: "Is the 7/16 layer of OSB the best choice of material to sandwich the T&G planks with the 2x12?"
A. No, the best choice would probably be plywood. But most builders stop well short of choosing the best possible materials, out of cost concerns. Usually, builders choose "good enough" materials.
Back to the ceiling / roof, for several reasons, we decide to insulate from below. We have 11 inches to work with. Our idea is to spray foam for a certain thickness, and do the rest with either mineral wool (Roxul) or cellulose. My questions:
-Is there a minimum thickness I should spray polyurethane foam, considering I'd fill the rest with Roxul / cellulose? Foam is of course more expensive, but also highly flammable and not as green as we would like, but we want to do it right. So how thick I should go (I live in Zone 5B)?
-Is there a preference between cellulose and mineral wood for the filling? I think mineral offer a better fire protection and sound damping, and it is easier to install, while being more expensive. Anything else to consider in that particular case?
Thxs
Francois,
The rule is that in Climate Zone 5, at least 41% of the total R-value of the roof assembly should come from the spray foam layer.
If you use open-cell spray foam, you'll need at least 5 inches of spray foam. The total R-value of your assembly will be only R-40 -- in other words, less than minimum code requirements (R-49).
If you use closed-cell spray foam, you'll need at least 3.5 inches of spray foam. The total R-value of your assembly will be R-50.
I agree that mineral wool insulation will be easier to install in this case than cellulose insulation.
All right almost ready to submit our plan to city hall, but one question:
Do we need to leave a gap between the mineral wool batt and the foam above? Right now our wall assembly specify that the mineral wool is pushed up as far as it can go without compressing it, so it is a snug fit, touching the foam above.
Is that fine?
Francois,
Yes, that's fine. You want to do everything within your power to avoid having an air gap between the two types of insulation.
Awesome, that gives us more space under to work with.
Back in the day when our ceiling assembly didn't had any foam, we included a radiant barrier behind the gypse that was also acting as a vapour barrier. Now that we spray foam under the deck, should we remove it?
I understand that the mineral wool would lay in between 2 vapour barrier if I keep it (the closed-cell foam above and the radiant barrier under), which is usually not good, but what if I want the benefit of that radiant barrier?
Francois,
If you are combining spray foam (on the exterior side of the insulation sandwich) with mineral wool (on the interior side of the insulation sandwich), then you don't want a vapor barrier on the interior side of the mineral wool. You just want an air barrier (usually, that would be the gypsum drywall).
So don't install an interior radiant barrier.
So major development. We called back our chosen contractor for the foam spray to discuss the details of the operation. At some point, the discussion went to how thick, and time it would take, and we noticed he was calculating for 5 inch of foam sprayed in two passes, so 2 1/2 inch per passe.
Now most of the documentation I read on SPF specified 2inch max per passes with enough time in between for the previous passes to cool down, and sure enough, the documentation on the specific product this contractor use suggest the same, but he just said everyone is doing it that way and it is fine.
Most of bad SPF jobs seem to come from either bad mix condition (AB ratio or temperature) or spray too thick / fast to properly cure, At the end, the product seem safe enough when properly installed, but the variable of the on-site conditions makes this "properly installed" kind of shaky concept. And this contractor disregard for his own product specs shattered the slim confidence I managed to built to finally decide on the SPF solution.
So I guess I'm back at square one: finding a suitable insulation solution for my flat-roof that doesn't involded on-site chemistry, at least not indoor.
Francois,
You didn't ask a question, so perhaps you aren't asking for advice.
If you are willing to install spray foam, you can either seek out a different contractor -- one who gives you more confidence -- or you can call the manufacturer of the spray foam that your contractor wants to use. Sometimes a manufacturer's rep can clarify requirements or visit a job site to mediate issues like the one you raise.
Indeed, so let's do a quick recap of my options:
1- Closed-cell spray foam under the deck = best solution on paper, but risk associated to bad installation and difficult removing process in case of failure makes it uncomfortable for me to choose this way.
2- Mineral wool + vapor retardant indoor side and better venting of the roof assembly (doghouses) = Possible and cheap, but the upper deck has only 4 inches in the lower part (center) and might prove difficult to vent properly, since there is no side openings (soffit). Contractor said it would be insuficient. He said either go with #1 or #3 instead.
3- Rigid foam on top of roof deck - Seems to solve most of the issues, but it is very expensive, and we throw away a roof that still has perfectly good years of service left.
4- Replacing the closed-cell foam from #1 with Cut-and-Cobble rigid foam technique = risky and not recommended, but I'm getting to the point where I might have an easier time living with those risks than those associated with bad foam job.
After reading carefully your C&C article, I understand failures seem mostly associated with the inability to prevent the air and the moisture it carries to the upper level, where it condensate on the cold surface. Those leaks happens either because of poor workmanship on the sealing around the rigid foam, or cracks from the structure movement or the foam that doesn't stick well.
To prevent this situation, I was thinking that a flashing membrane could help to seal the whole assembly. This is the kind of product I'm refering to:
http://www.resisto.ca/product/redzone-25/
Among the properties of this really sticky membrane, those are the most interesting:
*Provides a continuous air/vapor barrier
*Eliminates drafts and water leaks
*Self-sealing around nails and screws
*Can be sprayed with polyurethane foam
*Remains flexible at low temperatures
The install process would go like this:
- Cut 2 inch thick XPS slightly undersize on width, and push it right underneath the roof deck.
- Seal the gap on each side with Windows and Door spray foam (it stays a bit more flexible). Tape the seam with the next xps sheet with tuck tape.
- Tape over the foamed seam with the membrane in L shape, which would stick over the edge of xps for at least 2 inch and to the side of the joist for another 2 inch (so I would probably use 6 inches width membrane).
- Repeat the process twice with another layer of xps / foam / membrane, staggering the taped joints from the previous layers.
This would add up to 6 inches of XPS, divided into 3 independant sealed layers.
Another idea was to finish this whole assembly with a foil radiant barrier, which is also air / vapor barrier. It would be taped on both side of the joists in an inverted U shape, and maintained in place with a 1x4 over the tape.
So now the question: Does that looks like a not too bad approach to a somewhat bad solution, and how would you improve on it?
I know where you stand on C&C, and I understand this is totally on me, but at the end if I can't live with #1, can't make work #2 and can't afford #3, then might as well look at the very best practices to make #4 works. I'm not looking for your blessing, just advices and guidelines.
(as your suggest, I called for another contractor on the foam spray, and will meet him tomorrow.)
Thxs for your time Martin.
Francois,
You've analyzed the situation well. You can't afford the best solution, and you don't want to adopt the second best solution. Therefore you have decided to adopt the not-so-good solution.
Your analysis is correct: "I know where you stand on cut-and-cobble, and I understand this is totally on me."
Good luck.
ahaha all right fair enough. I have a question not C&C related though.
Let's say I'd postpone the operation until I get the funds for the best solution (#3), but need a temporary setup for the winter, especially now that the latte&plaster ceiling is down, I assume that a continuous EPS or XPS foam under the exposed joist would work fine right? As long as I follow the minimum thickness of 4inch, that should work fine as an assembly AND would provide me a more than welcome insulation layer?
I can live with the lower ceiling for the winter.
Francois,
Q. "I assume that a continuous EPS or XPS foam under the exposed joist would work fine, right?"
A. Yes.
Q. "As long as I follow the minimum thickness of 4 inches, that should work fine as an assembly AND would provide me a more than welcome insulation layer?"
A. There really is no minimum thickness, especially if this is a temporary layer, except whatever is stipulated in your local building code. In most jurisdictions, remodeling work doesn't have to comply with the code.
If the minimum code requirement is R-49, you would need about 12 inches of EPS, or about 10 inches of XPS, to meet code requirements. Four inches would have an R-value of R-16 to R-20.
Remember that you need to install a layer of 1/2-inch drywall on the interior side of the rigid foam for fire safety.
Ohhh I though I had to follow the Climate Zone 5 — R-20 from this article:
https://www.greenbuildingadvisor.com/blogs/dept/musings/calculating-minimum-thickness-rigid-foam-sheathing
Also, is it a problem if I install mineral wool batts over the continuous EPS / XPS, in between joist if I follow the 41% ratio foam to fluffy ratio? Again this would be temporary, but I already have the mineral batts and it would give us a boost for the winter.
Francois,
The foam-to-fluffy ratio rules apply when you are installing rigid foam on the exterior side of the roof sheathing, along with fluffy insulation on the interior side of the roof sheathing.
The foam-to-fluffy ratio rules do not apply when you are installing rigid foam on the interior side of fluffy attic insulation.
I see.
So if I have a continuous layer of foam under the joist, let's say 2 inch, I'm good to fill the cavity between the joist, over the foam, with fluffy insulation? Correct?
Francois,
If you want to "fill the cavity between the joists" with fluffy insulation, you need a vented attic above. As I tried to explain in one of my earlier responses, for a low-slope roof, this approach requires an attic that has, at a minimum, 6 inches of air above the top of the fluffy insulation, as well as air inlets at the perimeter of the attic, and a doghouse cupola in the center of the roof.
If you've forgotten these details, you might want to re-read this article: Insulating Low-Slope Residential Roofs.
Ok things are moving fast, and in the right direction I think.
We looked at all aspect with another contractor, and decided to redo the roof this year with an elastomere membrane, and add 2 X 3 inches (so 6 inches total) of polyisocyanurate insulation board. According to the contractor, this should give us around R34, a bit less when temperature gets very cold.
He will also open the roof sheating to have access to the perimeter of the upper deck so he can insulate the exterior walls with mineral wool. I will do the lower deck perimeter from inside.
My question is: while having access to the upper deck from above, can we add some fluffy insulation in the upper deck section (cellulose)? The top roof sheating is pooling toward the center, so I might have 12-14 inches on the perimeter, but only 4-6 inches toward the center, but still, the more the better.
Reading the article Insulating Low-Slope Residential Roofs, I'm not sure which apply to my situation:
You can install a more moderate layer of rigid foam insulation (2 to 4 inches) above the roof sheathing, supplemented by a layer of air-permeable insulation below (and in direct contact with) the roof sheathing.
You can install a layer of closed-cell spray polyurethane foam roofing on top of the roof sheathing, supplemented by layer of air-permeable insulation under the roof sheathing. (For more information on spray-foam roofing, see Spraying Polyurethane Foam Over an Existing Roof and Roofing With Foam.)
In the first case, I install more than 2-4 inches of rigid foam (polyisocyanurate in my case), and the cellulose wouldn't be in direct contact with the roof sheating after setting in. In the 2nd case, it refers to closed-cell spray polyurethane, not polyisocyanurate panels, so I'm not sure it qualify.
Can you clarify this for me? Please note this only apply to upper deck, not lower deck.
Thxs
Francois,
I'm not sure what you mean when you write that "The top roof sheating is pooling toward the center." It certainly sounds like you are discussing a flat roof with ponding issues. If so, I hope that your roofer corrects the problem before installing new roofing.
If you are combining rigid foam above the roof sheathing with fluffy insulation below the roof sheathing, the best approach is to have the fluffy insulation in direct contact with the roof sheathing. This is to minimize the chance that you will get air flow or convective looping in the air space between the two layers of insulation. (Air flow would diminish the effectiveness of the insulation.)
If you can't figure out how to get the cellulose in direct contact with the roof sheathing, you can break the rule. But it's better to follow the rule if you can.
In your case, you can hire a cellulose contractor to dense-pack the space where the cellulose is being installed. Dense-packed cellulose won't settle -- it will stay in contact with the sheathing. For more information on dense-packed cellulose, see this article: How to Install Cellulose Insulation.
Martin,
I actually meant that the slope is toward the center of the roof, where a drain collect the water and send it to city sewer. The slope itself is good (well, for a low-slope roof) and drain fine.
I'll see with the contractor what he can do in that regard, and if he have the equipment to dense pack cellulose.
Otherwise, is insulating the 14 inches or so perimeter wall of the upper deck with mineral wool is good practice? Should he use any foam sheating in the assembly? Any specifics I should be aware of for that part?
Francois,
If you are creating an unvented conditioned attic, even one that is only 14 inches high, you need to insulate the walls of the attic. Mineral wool is one option.
On the other hand, if you fill the 14-inch-high space with dense-packed cellulose, you certainly don't have to insulate the attic walls separately -- because you will be filling the whole attic with cellulose.
Note that in Climate Zone 5, you still have to follow the foam-to-fluffy ratio rules with this type of roof assembly. One disadvantage of installing 14 inches of cellulose (that is, about R-50 of cellulose) under your roof sheathing is that you need at lot of rigid foam to balance the cellulose layer.
In Zone 5, at least 41% of the total R-value of your roof assembly has to come from the rigid foam layer in this type of assembly. Here is a link to the article which explains the rules: Combining Exterior Rigid Foam With Fluffy Insulation.
My guess is that you don't want to install 14 inches of cellulose in light of the foam-to-fluffy ratio problem. [Later edit: As Francois pointed out, if the roof is insulated with R-34 of rigid foam and R-50 of cellulose, the ratio is fine.]
Isn't R-50 of cellulose right on spot with a 41/59 % rigid/fluffy ratio if I have 6 inches of polyisocyanurate board (which gives R34 according to the contractor)?
So other than the mineral wool or cellulose, I don't need to have any rigid insulation or vapor barrier on the interior side of that 14 inches perimeter wall of the upper deck? I can just seal any seam and crack with canned foam, and install the fluffy against the wall and it will do just fine? My understanding was that the condensation is prevented on the roof sheating by the fact that the surface is kept hot enough by the rigid polyisocyanurate above the sheating, but if the perimeter wall doesn't have this rigid board (it is brick on the exterior side).
Wouldn't the hot humid air from inside the house would get through the fluffy and condense on the perimeter wall?
Francois,
Sorry -- You're right. I haven't had enough coffee this morning. R-50 cellulose plus R-34 of rigid foam will work fine.
Q. "So other than the mineral wool or cellulose, I don't need to have any rigid insulation or vapor barrier on the interior side of that 14 inches perimeter wall of the upper deck?"
A. No.
Q. "I can just seal any seam and crack with canned foam, and install the fluffy against the wall and it will do just fine?"
A. Yes.
Q . "My understanding was that the condensation is prevented on the roof sheathing by the fact that the surface is kept hot enough by the rigid polyisocyanurate above the sheating, but if the perimeter wall doesn't have this rigid board (it is brick on the exterior side). Wouldn't the hot humid air from inside the house would get through the fluffy and condense on the perimeter wall?"
A. Hopefully, you have an interior-side air barrier -- something like taped drywall -- to prevent hot humid air from migrating out of your house. There will be some vapor diffusion, of course, but not enough to be worrisome. The cellulose is hygroscopic, so it will act as a hygric buffer, taking on a little moisture in winter, and drying out slowly during the spring and summer. In any case, your brick wall can dry toward the exterior.
Martin,
MH. Hopefully, you have an interior-side air barrier -- something like taped drywall -- to prevent hot humid air from migrating out of your house. There will be some vapor diffusion, of course, but not enough to be worrisome. The cellulose is hygroscopic, so it will act as a hygric buffer, taking on a little moisture in winter, and drying out slowly during the spring and summer. In any case, your brick wall can dry toward the exterior.
Actually I might not have any air barrier in a 450sq ft area of the house. When we took down the ceiling, we thought the raw joists and wood planks were beautiful, and we had this idea of not covering it with drywall if we were going to insulate from over the roof sheating.
Here's pretty much how it looks like right now (a bit cleaner though, with no nail holes):
http://www.gettyimages.ca/detail/photo/exposed-ceiling-joist-and-flooring-in-an-old-house-royalty-free-image/641482984?esource=SEO_GIS_CDN_Redirect
Is it possible to keep this that way?
Francois,
If you plan to install cellulose above this ceiling, you should really install an air barrier first. Is there any way that you can install OSB or plywood with taped seams on the exterior side of your ceiling?
That would requires to strip the whole roof sheating. I will ask to the contractor about it. If we strip the whole roof, I feel this would not be such huge extra, especially if we end up finding the that deck needs repair anyway (this house is 1924 after all).
Alternatively, would an air barrier installed in between the joist on the interior side of the ceiling, covering the planks but leaving the joist, would be sufficient, or is this would most likely cause the same potential problems as the cut&cobble thing?
Third scenario, is the air barrier only required if we add cellulose? What if we keep only the R34 polyisocyanurate board with no fluffy. Do we still need the air barrier at all?
We talked with the contractor about removing the roof deck to install an air barrier (taped seam plywood), and while possible, he said it would be quite expensive.
I'd still prefer to add one though, but I'm not sure if there is any alternative to do it from the interior side.
I assume the planks are a valid air barrier, and the problem lies in the crack in between. Is caulking would be doable?
What about gypsum cut tight in between the joists with finished seams, and then another layer of planks just for the look, or is it the same situation / risks as the cut&cobble scenario?
Any other trick upon your sleeve that would allow me to keep my ceiling unfinished?
Also, just to make sure, is the air barrier only necessary if I plan to add cellulose in the upper deck? What if we keep only the R34 polyisocyanurate board with no fluffy?
Thxs!
Francois,
I think it's time for you to start making your own decisions. You have the information you need.
You like the aesthetics of your existing leaky ceiling. If you are willing to accept a little air leakage in exchange for the beauty of your ceiling, that's your decision.
Any efforts you make related to sealing the air leaks, even imperfectly, will help. It's hard to say whether the expense and hassle of an unusual measure like caulking the seams between the boards would be worth it. I'm inclined to say it wouldn't be.
Even if you leave your leaky ceiling as it is, you probably won't have a catastrophic failure. After all, you'll have an air barrier at the level of the roofing. Questions remain, however, about the airtightness of your attic walls. (I know it's not really an attic, but it still has walls.)
Aesthetics or performance? Your decision.