Insulating a house built over water

Hello All,
I have recently purchased a vacation home on the Intercoastal Waterway in NJ.
The structure was built half over solid ground, and extends out over the water, supported by pilings.
the section on land is an enclosed “garage” with a dirt / sand floor, the part over the bay is two boat slips. When hurricane Sandy came thru a few years ago, the fiberglass insulation that was installed got soaked , and the vinyl siding which covered it was damaged. All of it had to be removed, leaving the entire underside of the house completely un-insulated and exposed. In the winter, we rent the house out , so it remains occupied . This past winter was extremely cold at times, and my tenant had very high utility bills . The enclosed section does have a hot water radiant blower heater(REZNOR), which ran almost constantly. I need to insulate this place!! I do not want to do fiberglass batts, because that could be ruined in the next storm. i need some input from those in the know. Would rigid foam be best? Spray foam? Will the foam deteriorate faster in the wet climate? Any input would be greatly appreciated..
Thanks
Jason
GBA Detail Library
A collection of one thousand construction details organized by climate and house part
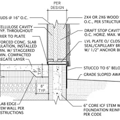
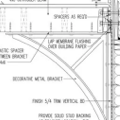
Replies
Jason,
Half the house is a dirt-floored garage, and half the house consists of "two boat slips." So where's the house? Is there a living room, kitchen, bathroom, and bedroom? Maybe those are on the second floor?
Anyway... The answer to your question depends on how often the waves rise to hit the underside of your house. If the water gets the underside of the floor wet, you need to use boat-building techniques, not housebuilding techniques.
If the underside of the floor assembly has some kind of durable sheathing -- maybe cementitious backerboard -- you could try to find a roofing contractor to spray closed-cell roofing foam (the super dense stuff) on the underside of the cementitious backerboard. Then you could spray an elastomeric coating (again, a roofing product) on the cured foam.
Martin,
Yes . The living space is on the second floor. Hurricane Sandy was the exception, not the rule. It does not get hit with waves often., but it's obviously a humid environment. Any idea what a ballpark square foot price on your suggestions would be? Would your suggestions be a more commercial / industrial oriented product? Thanks for your input.
Jason,
The last time I checked -- admittedly a few years ago -- one-inch-thick spray polyurethane foam roofing cost between $2.50 and $3.50 a square foot. You'll want more than 1 inch, of course, so you can expect the cost to be proportionally higher.
I think Fiberglass or rockwool may be the cheapest/best option. Ideally you would want something that could withstand another storm surge, however that requires some local knowledge that may be lacking in your area. The alternative to that is something that is normal weather durable yet easily repairable after extreme events. Fiberglass and rockwool meet that definition, though you do have to be very careful with the install of fiberglass. You would still have to install some underside sheathing preferably plywood, with the face edges primed and taped. That should allow some moisture to diffuse out through the plywood. With it being on the underside of the house bulk water and UV shouldn't be a problem so paint would not be needed, though if you do paint you would need to use and acrylic latex top coat over a premium latex primer (http://www.buildingscience.com/documents/reports/rr-0409-painting). To fasten the sheathing I would use stainless steel fasteners, likely screws or lag bolts.
My concern with foam is that it can hold water (even closed cell), and that the storm surge may very likely damage it. That said even though it can hold water and still be easily damaged it's repair cost may very well be below that of fiberglass. However that will likely require at least one specialty contractor taking it out of the DIY category. Anytime you are dealing with a storm surge (ie fast moving bulk water with stuff in it) damage is likely to occur. In your area I would like to be able to do the repair myself without relying on a contractor, because after an even like that the contractors are going to be very busy and that type of repair would put me at the back of the line. That means using mass manufactured materials that are easy to work with, and aquire. That basically means fiberglass or rockwool batts.
To meet IRC 2012 code in US climate zone 4A (all of coastal NJ) the floor insulation has to be R19, which would take ~3" of 2lb density closed cell polyurethane applied the the subfloor (not the higher density 3lb roof foam) which costs about $3-3.50 per square foot (a buck a board-foot, maybe a buck-ten) in my neighborhood.
The performance of 3" of thermally bridged foam is pretty lousy compared to 5.5" of lower R/inch material though, since the path through the more conductive wood is only 3", not 5.5". To hit the same performance point you'd have to encapsulate the joists in a flash half-inch shot of 1/2" of closed cell foam, but that's not a bad idea- it would protect the joists from a soaking in a storm surge.
To meet fire code in my neighborhood painting the foam with intumescent paint is sufficient, but that may not be the case in your area, otherwise it would require something like half-inch gypsum or OSB over the whole thing as a thermal barrier/ignition barrier.
I'm not a big fan of closed cell spray polyurethane due to it's environmental impacts, but if ever there was an application where it made sense, this would be one of them.
If it gets dinged up by flotsam in the next storm surge, you can patch it with 1.5lb polyurethane FrothPak air sealing kits available at box stores ($40-50 for a 12 board-foot kit). It it takes more damage than that, there are bigger 2-part foam kits available from internet sources.
The stuff is pretty water proof, - it'll block water from getting into the subfloor from the bottom, but if the first floor floods it won't dry quickly through the foam- it has to dry toward the interior. Anything you do in a hurricane flood-zone is a bit of a crap shoot. At 3" the 2lb foam is structural as well- it glues the joists to the subfloor, making it stiffer and less likely to break up from minor wave pounding. With bigger waves it might lift the whole thing off the pilings, but if it's that bad you probably weren't going to save it anyway.