Insulating 1990s slab family room (NE Ohio, 5A)

We have a 2 story addition that a previous owner put on in the early 90’s which sits on a slab. The family room is always colder by a good 5 degrees. We had the wood fireplace converted to a direct vent gas insert and that’s much better air sealed now.
We’re starting to plan on redoing the room and I’d like to do what I can to better insulate it. Using a simple temperature gun and just feeling, by far the coldest area is the bay window. I’m not sure there’s any insulation in the seat part of it, it’s open outside. I’m thinking a few layers of rigid foam board and then encased in plywood and painted? The windows in the bay window are triple pane. I don’t see removing the whole window as an option so I have to make the best of it.
The slab is right under the carpet but it’s not that cold. I’m thinking of something along the lines that’s discussed in this thread, if it will make a difference that’s worth the expense. How would I decide? I have no idea if there’s insulation under the slab. https://www.greenbuildingadvisor.com/question/insulated-floor-on-top-of-concrete-slab
I have no idea if there’s insulation under the raised part with the dining room table. I’m thinking of cutting a hole behind the couch and seeing. It’s not that cold though. If not I can add insulation to the underside of that area, probably along the lines of this article: https://www.finehomebuilding.com/2012/03/08/how-to-insulate-a-cold-floor
The ducts don’t blow very warm air. I’m sure it’s because they go across the room in the concrete. I’ve done a little insulating of ducts in the basement, I could try to add insulation to those lines before they enter the slab. I believe there’s a duct that dead ends under the bathtub on the other side of the family room wall. When we redo the bathroom I’m trying to decide if I relocate the duct through the wall into the family room to blow nice hot air in or just eliminate it altogether. I can’t leave it in the bathroom, with two ducts ending in there it gets super hot with the door closed.
Thank you!
GBA Detail Library
A collection of one thousand construction details organized by climate and house part
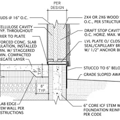
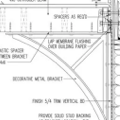
Replies
Drill a hole from the exterior on the underside of the bay window to find out if there is any insulation under the seat- it might be full of spray foam, fiberglass batting, or empty cavities. If empty it's worth squirting some cellulose in there prior to installing 3" of polyiso on the exterior. (IRC code min for exposed floors is R30 if between joists, R19 minimum if there isn't sufficient depth.) Empty air in the assembly would be a potential thermal bypass of the rigid foam.
With 3" of rigid foam you can usually cover it cleanly with 3" - 4" drip edge.
What does the top of the bay window look like? It may need insulation too.
The carpet can take the bare-foot comfort up by quite a bit, but it's at best R2, and a considerable heat loss. Inspect the exterior to see if there is any slab edge insulation. Current IRC code-minimum slab edge insulation for zone 5 is R10 continuous insulation to a depth of 2 feet below grade. Three inches of EPS (not XPS, not polyiso) protected with a purpose made cementicious coating such as Quikrete Foam Coating, or roughing up the surface with at least 1/4" of standard stucco scratch coating works. Used or surplus roofing EPS is fairly available on the cheap in NE OH, and far better material than box store Type-I EPS. Use 4" masonry cap-screws (or wide washers with standard masonry screws) to fix it to the stemwall, screwed tight enough that the caps/washers compress sufficiently into the foam that they are flush with the exterior plane of the foam. Before applying the protective coating, install Z-flashing to direct any bulk water coming down the drain plane toward the exterior rather than between the foam & concrete.
These folks advertise reclaimed and factory seconds foam of all types regularly, but there are others:
https://cleveland.craigslist.org/mad/d/akron-insulation-king-rigid-foam/6795398969.html
Running this search on your most-local craigslist will likely find other sources, perhaps nearer you:
https://akroncanton.craigslist.org/search/sss?query=rigid+insulation
For slab edge insulation used or factory seconds XPS is fine, but not polyiso, which is easily waterlogged when in ground contact. Derate the XPS to R4.5/inch (the maximum warranteed performance), though inch for inch it will eventually hit the same performance of EPS of similar density. Most roofing EPS is 1.25lbs density (Type VIII), though sometimes 1.5 lbs density (Type-II) is available. As long as there is reasonable surface grading and drainage it will perform fine at 2.5" thickness or greater.
Hi Jeremy -
The picture of your bay window does not show enough depth below the glazing for there to be much if any insulation. Rigid is the way to go, making sure that you airseal as you insulate.
Heat loss from the slab is going to be of course greatest at the slab edge. I remember some work that Building Science Corp did--but a very long time ago--suggesting that even in a milder climate such as Atlanta (CZ3), conductive losses at the slab edge of a home such as yours could account for as much as 10% of total heat loss. Definitely worth insulating from an energy AND a comfort perspective.
As far as ducts in your slab: We lived in a home very much like this in MD and the air quality of those ducts was always an issue. We sold the home before ductless mini-splits were commercially available but that would have made the move to simply "kill" those ducts with a ductless mini-split approach to space conditioning.
Peter
Thank you both. I've been trying to figure out the EPS vs other options part right now. I don't believe any water or moisture comes up through the concrete, the carpet and pad don't show any water damage. Do I still want EPS for it's higher perm rate for sure? If XPS is going to degrate to the same R-Value as EPS do I want XPS as it should be stiffer under the finished floor? Sorry for all the questions, I'm trying to learn so I get this right:)
Dana recommended Quikrete Foam Coating, why is that superior to putting down plywood?
Thank you!
For protecting slab-edge foam, plywood in contact with the ground (even pressure treated plywood) wicks moisture, and is more vapor retardent than cementicious materials, and is more prone to insect damage/infestation.
For protecting any foam on the underside of the bay window overhang MDF or asphalted fiberboard is fairly vapor open and would have about twice the R-value of plywood, but plywood or OSB is still fine there in your climate zone.
Thank you Dana. I'm reading as much as I can find on this site that's relevant.
I don't know if there's polyethylene or insulation under the slab but wall to wall carpet that's been there nearly 30 years has no water damage or mold that I can see. It sounds like adding polyethylene is a no lose so I should add it anyway.
For making the foam air tight every article says "to use high-quality European tape, with caulk, or with canned spray foam" What's an example or two of the European tape?
Won't the tap-con screws from the plywood into the concrete break the air tight bond?
Thank you!
>"Won't the tap-con screws from the plywood into the concrete break the air tight bond?"
Concrete is pretty air tight all by itself. The annular rings around the tap-cons don't add up to more than a square inch of leak area for the whole floor.
It's probably cheaper to do R10 slab-edge insulation down to 2' below grade than it is to put an inch of foam + subfloor over the entire floor .
"t's probably cheaper to do R10 slab-edge insulation down to 2' below grade than it is to put an inch of foam + subfloor over the entire floor ."
It's a finished room built on a slab. Are you suggesting digging down on the outside?