Insulated slab with compacted fill above rigid foam

I am intrigued by the insulated thickened edge slabs in articles written by Alan Gibson and Michael Maines. Rather than forming the rigid foam to the contour of the compacted fill, the rigid foam is placed flat with fill compacted on top. The foam perimeter is left exposed for the thickened edge. I love the simplicity of this approach, but I have questions!
– Does it work? Have others built slabs this way?
– Does the compacted fill add to the thermal mass?
– Does the additional thermal mass affect window sizing and heating?
The slab is detailed in a PDF attached to this article written by Michael:
https://www.finehomebuilding.com/2020/04/07/the-evolution-of-a-pretty-good-house
GBA Detail Library
A collection of one thousand construction details organized by climate and house part
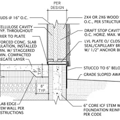
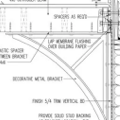
Replies
Alan, there are advantages and challenges to my detail. While I am adamant that trying to place rigid foam over contoured soil, the usual approach with thickened-edge slabs, is not easy to get right, it is possible and may be preferable for some builders. My go-to assembly is a raised slab detail, using a separate perimeter wall, but I showed a similar detail in my recent article on concrete-free slabs. The detail I showed in my new PGH article is one I designed last year for a builder doing a Pretty Good spec house and he said it worked well. I'll see if he can share any additional feedback. The main challenge I'm aware of is that dumping and moving fill over a vapor retarding membrane requires a lot of handwork or a very gentle touch with earth moving equipment.
The way G•O Logic does it, or at least the way I've seen Alan Gibson present about their system, is to use flowable fill--essentially a low-strength concrete mix, placed and moved like concrete. That approach costs more in material but depending on your labor source it may be worth considering.
Another option is what the fine folks at Warmform (https://warmform.com/) recommend: use thick layers of EPS foam to take up the "extra" space. Structurally I have no issue with that approach, though you might need to find a creative engineer to sign off on the detail. Placing rigid foam is easier (and safer on the vapor retarder) than moving gravel. The extra insulation further slows heat flow to the earth, of course. If you're building a Passive House you might need that extra insulation anyway. My main concern is that although EPS has lower up-front carbon emissions than most other foam, it is likely far higher than the carbon emissions of gravel fill--it would take a long, long time for the energy savings to recover the carbon emissions.
Whether you use gravel or flowable fill, it does add a bit to the thermal mass of the structure. If you live in a place with a lot of sun and wide temperature swings each day and night, you could take advantage of the thermal mass with careful window design. But in most places, for most homes with light-frame construction, good air sealing and insulation is usually much more important to consider than thermal mass.
Michael, my research into monolithic slabs a couple years ago brought me to Warmform and they were very friendly. I'm almost sorry I couldn't afford their product, I would have enjoyed working with them! The approach of using EPS foam for the "extra" space certainly caught my attention. My labor force is me (and whomever I can entice with free beer and sandwiches), so these methods appeal to me because not only does it appear simple and streamlined, but it just seems to make sense.
I'm wondering how you believe a concrete-free foundation would work in climate zone 7, with frost depths of 6' to 7'. I was reviewing your recent article you mentioned and also an article in FHB of a project by Randy Williams in Northern Minnesota.
I've even considered helical piers. If I'm not mistaken, it looked like Techno Metal Post in your recent FHB PGH article, so I spoke with Mike Brochu about my project. Unfortunately, my ground is riddled with rocks and ledge making helical piers unfeasible.
My project is my future home outside Presque Isle, Maine, a timberframe harvested from my land and milled on site. I'm not going to Passive House standards, but rather following PGH practices to some extent within a modest budget.
Alan, did you see the BS + Beer Show we did last week? It was all about reduced-concrete slabs: https://www.greenbuildingadvisor.com/article/the-bs-beer-show-concrete-free-slabs.
If I were you I would strongly consider a frost protected shallow foundation. They are time-tested and relatively easy to do. With or without concrete doesn't really matter--the idea is to keep the ground protected from cold air so it can't freeze. There are prescriptive rules here: https://codes.iccsafe.org/content/irc2015?site?type=public/chapter-4-foundations#IRC2015_Pt03_Ch04_SecR403.3, and more options available using ASCE 32-01 but you should engage a structural engineer in that case. (Usually money well spent, in my opinion.)
And yes, those were Techno Metal Posts, and Mike Brochu is my local dealer (he covers all of Maine and beyond). He has said that he can get through rocky soil, but there is a limit, of course.
Yes, yes, yes and "basically no".
When it comes to carbon reduction by reducing concrete use, always calculate the cost effectiveness of it. There may be better alternatives.
Jon, are you referring to a financial, or carbon, cost effectiveness?
The $/ton of carbon due to the reduced concrete design should be compared to the $/ton of alternatives.
Michael, I'll be sure to watch the BS+Beer show now that I know more about it! I've seen it on the website but hadn't made time to watch. Thanks for your input, it gives me more to consider.