Insulated slab – shallow or not? Maybe PWF?

Getting ready to build a smallish (1000 sq. ft.) home for myself in climate zone 6B and am trying to walk the line between green, cost, and ease of build. I’ve decided to build on a slab and am trying to come up with the best way to insulate it.
Building a FPSF uses quite a bit of foam running at least 2 vertical feet outside the slab and 2 horizontal feet away from it (over $400 worth of 2″ XPS). Then I also have to detail that 2″ of exterior foam to the exterior wall.
Trying to think of ways to use less foam and less money I had the thought of building a PWF stem wall 4′ deep to get below the frost line and then only using enough foam to create a thermal break between the stem wall and slab, as well as full sub slab insulation. This would save me $400 in foam and maybe $500 in concrete. I figure the PWF stem wall would cost me about $750 to build.
So cost savings aren’t huge but I’m more comfortable working with wood than concrete so there would be a labor advantage. Excavation cost would be higher having to dig the full 4′ footings but I’m really not sure how much more it would be.
I’ll be building with a double stud wall so that will cover up the foam thermal break between the stem wall and slab. If I used exterior foam on the slab I feel like I’d probably need to construct the outer wall from 2×6 so I could hang it over the foundation enough so that it would end up flush with the foam. With no exterior foam I’d feel good building it with 2×4, which I have a lot of after tearing down my old house.
Any thoughts? Is this a mistake? Should I just quit being a weeny and pour concrete and foam the outside? Should I still use exterior foam even with a full stem wall?
I’ve done a lot of research on PWF and am pretty comfortable with them. They’re somewhat common in my area and I’ve talked to a couple people that have had them installed for 35+ years with no issues. I’m also blessed in this regard to be building on very well drained soil with a low water table.
Any thoughts appreciated,
Alan
GBA Detail Library
A collection of one thousand construction details organized by climate and house part
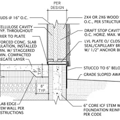
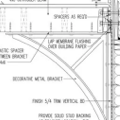
Replies
Put your load bearing wall to the interior, and hang out over the foam with a Larsen Truss. Detail the exterior truss wall to hang in line with whatever foam you have, and finish it as normal.
Slab on grade gets you a lot of nice thermal mass as well assuming you're insulating under the entire slab.
That would be an option. I've read about them a bit but haven't researched the truss design much yet. I'll have to do some more looking. In my case (2" exterior foam) the outside wall wouldn't bear entirely on the foam but with 4" it would. Is this still acceptable? It seems like it wouldn't take much shifting or settling before your doors or windows got a little wonky. Do you need to do something to ensure the foam stays firmly attached to the concrete?
I'm still a bit up in the air on the best way to insulate a FPSF. Assuming it's a mono pour with thickened edge should I run the horizontal insulation under the footing, similar to the recommended procedure for a non heated structure? This would give me maybe 8-10 inches of fill between the foam and the slab. That seems easier (and more energy efficient) than trying to follow the contour of the thickened edge or just omitting insulation there as well as under the footing.
If the extra cement wasn't so much cost and work a full non-insulated stem wall with only a thermal break between the wall and slab, as well as under slab insulation, seems like the least foam intensive and maybe most energy efficient. That's why I was thinking of a PWF stem wall. But maybe I'm wrong there.
I'm starting to suffer from too much research and not enough practical experience. It will be nice to finally start building.
Alan
Alan: I'm not a pro, but I'd suggest you dig into your ROI on that foam. $400 isn't stink, in the long haul. Build a quick spread sheet and play with it. Unless you have free access to fancy software, you'll have to take your best shot at assumptions for actual soil temps under the slab, future fuel costs, etc; the edge, where it is critical, is determined. Ask your city/county building department if they have any soil temp profiles, and go from there. Just bear in mind that the delta T under your slab is there for 365 days (pretty much). 6A sounds cool, and I would bet you'll find that 4" of foam under your whole slab, and 4-6" at the edge, are well worth the investment. In your climate, you can use John Siegenthaler's formulas (get a copy of his Modern Hydronic Heating book) to calculate your slab losses. It would be well worth taking the time to do; you may be surprised. $400? How about $19K? (And it will pay for itself.) If you are going to bear weight on foam, make sure you get "the rest of the story". The advertised psi rating is at either 5% or 10% compression. Your 1% compression rating is about 1/3 of the advertised number. You'll have to decide what % compression you can live with, but with EPS, once you go beyond about 5% your start getting into permanent deformation (as opposed to elastic), which you'll get at 10%. More research for ya! DOW has this info on their web site, as does insulfoam.com.