Insulated slab detail “problem”

We are to build a Passive House in PA, and have “borrowed” a technique from another PH in Virginia, where part of a typical EPS under slab was substituted with a layer of perlite bags placed over just 4” of EPS. I believe it also allowed us to reduce the slab thickness to 4” (in the center).
I just noticed that in our detail, the 10 mil poly vb goes over the perlite bags. Don’t know how it was done in VA. Will there be a problem with air gaps in between the perlite bags (under the poly) and the surface being so uneven? Should we possibly flip the location of the poly vb to be over the EPS and under the perlite bags? (Unevenness obviously does not go away…). In the posts, I also saw the matter of quantifying amount of concrete to order, which will also be impacted by this. We are to have the welded wire fabric in the slab. Online, in other PH posts I find people stressing the need to be very flat when installing under slab insulation and even adding fine particle gravel on top of other gravel to achieve it, etc. Is it for the purpose of creating flat surface under insulation itself (no gaps between EPS) or is it related to the concrete surface also?
GBA Detail Library
A collection of one thousand construction details organized by climate and house part
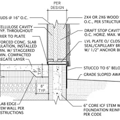
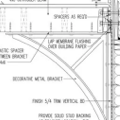
Replies
Lucyna,
I have never seen or read about the use of bagged Perlite under a concrete slab. Do you have a link to a website or document that describes the practice?
I think it was this one:
http://www.jetsongreen.com/2013/09/virginia-homeowners-build-a-passivhaus-on-a-budget.html
and maybe there were some other details elsewhere...
Lucyna,
I don't see any reference to perlite in the article you linked to.
Lucyna,
OK, my brain is waking up. Here are some links to relative web pages on the GBA site:
https://www.greenbuildingadvisor.com/community/forum/energy-efficiency-and-durability/27805/perlite-compressive-strength
https://www.greenbuildingadvisor.com/blogs/dept/green-building-news/trekhaus-passivhaus-duplex-oregon
https://www.greenbuildingadvisor.com/community/forum/energy-efficiency-and-durability/27075/can-insulating-concrete-be-used-footings
Any honest concrete contractor will tell you that welded wire is a joke and to use real rebar.
As far perlite bags go. If it is so rare that nobody knows about it in the Building Science community, why do you want to be the guinea pig in this experiment? Rigid EPS is inexpensive so why try and fix something that isn't broken? Use rigid EPS as it has been tried and true. In the end you will be holding the bag when things go south on a build-up that hasn't been widely used.
Peter, welded wire is the norm in residential. Millions of slabs. Rebar is the norm for commercial. Millions of commercial slabs. Rebar unless specified via engineering in residential is overkill. Post tension is another option and is also an engineered solution and is not generally in use for residential basement or slab on grade projects unless conditions immediate to the site call for it via a soil engineering solution.
Rebar in a 4" slab is not doing much either because the slab is not thick enough and more importantly the slab is not engineered.
I could be wrong but in my area wire is the norm residentially and slabs poured right are fine.
Luc.... Concrete slabs that are formed with the thickness kept as close to right on hold up better and have less cracking issues also will use less concrete which is important when building Home Depot's.
You could use non compacting sand to level your bags, then poly, then concrete.
AJ you are right about using welded wire in residential slabs on the east coast. Post tension is the norm on the west coast.
10 mil poly under a slab seams a bit thin now that 20 mil is available for this use. Placing the 20+ mil membrane down over a properly graded base and then insulating sounds more appropriate to me to prevent termite infestation of the slab foam stock. Usually the thicker material is used in soil mitigation areas but is very strong and blocks soil gas from entering the living space.It can also waterproof the slab when installed properly. A very strong flexible slab should include glass fiber added to the pour. This eliminates the need for any welded wire or rebar since fiberglass is far stronger than steel and far less costly. Just my opinion.
I guess the engineers out there deal with slabs differently but my PE called for rebar and dismissed welded wire in a floor slab for any long term significant crack prevention. He stated the wire will not hold any loads and if the concrete exerts a load on welded wire, it will snap like a twig.
I was also told that most installers don't install welded wire mesh correctly and it's placed on the bottom of the cross section where it becomes useless. It must be installed within the middle of the slab, which most of the time, it is not.
The slab subsurface must be 100% unyielding and never settle, move, heave, shift, etc. once the concrete is cured. If it does yield and puts tension on the slab, the slab will crack and only the rebar will keep the crack from becoming a structural problem.
Concrete is great in compression but bad in tension.
Peter,
As you say engineers seem to have several preferences for this situation. Neither mesh or rebar in the centre of slabs are there to resist loading, just crack control, as it is placed in the neutral axis of the slab. If you go to an engineers discussion board you can see them having the same fight over which of the two performs this function best, usually with fibre additives championed just as frequently. A forth strategy of using frequent saw cuts works well too. Probably the most important thing is to make sure whatever strategy chosen is executed properly.
.
Here is the link to the perlite institute's recommendation. http://www.perlite.org/library-perlite-info/insulation-perlite/Perlite-underslab-insulation.pdf
As you can see they recommend topping the bags with compacted sand! giving a flat bottom for the slab. My version uses loose perlite to fill the gaps between bags, then sand then compact
I'd put the poly right next to the concrete for better curing of the concrete.
FWIW loose perlite mixed with Lye, either NAOH or KoH +water and sometimes waterglass as well ( the ratios are very important) will create a " geopolymer" that is solid and sets up in several hours at room temperature. This is one way rigid perlite board and pipe insulation products are created.
As for the mesh /re-bar discussion better than either, and more economical is use "Helix" @ about 9#/yd.
Hello, I thought I'd share the improved under slab perlite insulation solution we developed based on both the comments above and also the continued desire to reduce the use of foams (perlite is a naturally occurring volcanic material). The location of 4'' EPS layer was swapped to be above the perlite, rather than under the perlite and the sand is now specified to fill in the gaps. 120 degree edge forms for EPS is an additional work, but hopefully not too much. We plan on it being cut on site from 4'' boards.
Tried attaching the png file to the above post, but it does not show... but here is the link where it can be seen:
https://www.greenbuildingadvisor.com/sites/default/files/Perlite-detail_1.png