Insulated light gauge steel and continuous insulation

I am working on a concept for thermally isolated steel framing (currently I am calling it thermastrut). Though I have done some prototyping and submitted a provisional it is no where near being a product.
My goal is to learn which configurations (if any) provide the most utility and perhaps to get some ideas about who to partner with to bring this forward as a product.
As I see it two primary use-cases exist. The first is a kind of Larsen truss where thermastrut is applied to the exterioir of a monopoly framed building. Some advantages include low cost and high durability, an ability to use deep layers of exterior isulation without needing long screws, ease of creating isolated window and door box-outs, ease of creating eaves that are fully isolated and the ease of adding components like decks or awnings that remain completely isolated from the inner structure.
The second use case is as wall and roof framing in and of itself. In this case balloon framing would likely work best, services would pass through the inner portion of the thermastrut and the sheer wall and air barrier are inboard of the framing.
I believe that high performance at a relatively low cost could be the outcome; but as I come from outside the industry I want to double check that thought before going too far.
My homemade tests so far indicate a thermal efficiency that is about 60% to 70% compared to EPS/XPS of the same profile depth, so about R2.5 to R3 per inch.
See attached drawings. Thank you in advance for any ideas, comments and critiques you may have.
GBA Detail Library
A collection of one thousand construction details organized by climate and house part
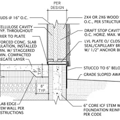
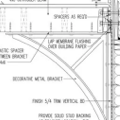
Replies
It looks like Thermal studs (formerly Tstuds) is already working on something similar?
It's called "Rhinostud"
https://www.thermalstuds.com/rhinostud
Thanks, yes I have seen their upcoming product. The primary difference with thermastrut is dis-continuity. The sheet steel of their product is one piece whereas my design has two steel members that overlap internally but are completely isolated from one another. Tensile forces aplied to the outer member, like a mechanical attachment of stairs or wind forces for instance, are translated into compressive forces which in turn act upon the internal steel member without contact. The benefit in terms of exterior insulation is that it elliminates the need for through connectection (12" screws for instance) to the inner structure.
Andrew,
Have you quantified the benefit the discontinuity gains you in r-value? My entirely intuitive reaction is I'm wary of relying entirely on foam as part of a load-bearing structure.
One other minor thing is the attachment flanges extending past or being being offset from the stud. That would seem to complicate conditions like window openings or corners.
Hi Malcolm. I had a test rig set up which is how I created the comparison but need to build a new one. At this stage it will not be as elaborate as the one that ORNL set up in the early 2000s to test the "snuggler" but it will be better than my first attempt. Temperature probes etc are currently on order. I am also in the midst of trying to find someone to set up some finite element analysis tests on the thermal transfer. I will post the results once I have better data etc
I am confident in the strength but will of course set up my own tests and have others do some testing, both real and simulated.
As far as flanges extending past the top or bottom it is also pretty straight forward. To feild cut the outer member you just hit it with an 1.5" or so hole saw and then nip it off with a zip disk or metal saw. This allows you to break away the exterior portion (or interior portion in the case of a roof member prodtruding as an eave support) of the thermastrut. Hopefully my hand drawing below gives some idea.
Thermal stud claims a 96% thermal break ...
What does that mean though? I see steel going all the way through. Steel has an r-value that is indistinguishable from zero to two decimal places. It's like the foam isn't even there.
Regarding the Rinostud, I am suspicious of the 96%. 'Compared to what' might be the question here.
Here's my take: The steel is an almost perfect thermal bridge. I see two pieces of steel separated by a piece of foam one third of the thickness of the assembly, that assembly is going to have an r-value equal to that one-third piece of foam. That's going to be roughly equal equal to a wood stud of the same dimensions.
You have to use something other than steel, something that has some r-value of its own. T-studs use wood, and then by reducing the amount of wood used and replacing it with insulation they're able to reduce the r-value of the assembly.
With all due respect I don't think the math works that way but new test data shall confirm or deny our assertions. I will post all data negative or positive when I get it.
OK, quick quiz. If you have a C-shaped piece of steel like in the attached picture, what is the r-value between points B and D?
Heat can travel from D to C to A to B. So no matter what lies between B and D, the r-value can't be any more than the r-value the piece would have if it was straightened out from B to D. To two decimal places the r-value of steel is zero, so if the piece is, say, a 2x6 shape, the r-value between B and D is going to be indistinguishable from zero. So regardless of what lies between B and D, the whole thing will act like a 2x6-shaped hole in your insulation.
That's what I thought too until I tested it. It seems that it doesn't work that way.
Therm is pretty clunky but works great for these types of 2d heat flows. If you watch the tutorials, it might take you an evening to set up and run your assembly.
https://windows.lbl.gov/therm-software-downloads
I would run two setups, one just of the stud profile another for the complete wall assembly. Post the results once you run it.
Gut feel, I'm with DC, you are looking at an R4-R5 or so assembly, so about as good as a wood stud. This is actually great as regular steel studs are terrible thermal bridge especially once you go above 3.5" depth.
Akos. Thanks for the software link. I will try to get someone more capable at that than myself to set up a model and try it. In the meantime I will set up another more thorough, small scale, comparison based (to pure 6" depth EPS) heat leak-down test and see if the results differ significantly, which I admit could easily be the case. I will update this thread when I get any more somewhat useable data. Regards.
If the wall is 6" EPS it would have an R-value of R-24. Let's say the studs are 1-1/2" wide, 16" on center, and have an R-value of R-8 (As I proposed in post #6) . The R-value of the assembly would be:
1/(1.5/16*1/8 + 14.5/16*1/24)
Which I get as R-20.21. I suspect you're going to have to have a rather sensitive test procedure to measure a difference between R24 and R20.2 experimentally. It's a difference of about 15%, so it should be measurable, but you'd need pretty good methodology and instruments.
Turning the question around, if you are able to measure heat loss through the assembly, you should then be able to derive what the R-value of the stud alone is. Which is really the whole question.
Deleted
Per the quiz: The only thing that matters is the steel gauge, because that's the cross section that is the thermal path through the surrounding insulation. The 2 inch dimension doesn't matter. You could make it an 8 x 6 and it's the same. Changing the steel gauge would matter, because now you're changing the cross sectional area of steel through the insulation.
Just because all the points are on the same path, does not imply that you can change the shape of the path and then shortcut from end-t0-end instead of along the path.
Here's my answer:
I'll preface it by saying there is no such thing as R-zero, whenever there is an assembly there is a layer of air along it that has some r-value. Normally it's so small you can safely ignore it, but when you start talking about steel framing members it dominates the discussion. What the value actually comes to is a topic of hot debate, and the assumption greatly influences the outcome. I'm going to assume that it's R-0.5 for the purpose of this discussion.
First, imagine a wall with a straight piece of steel going through it. Let's say it's a piece of 25-gauge steel, which is what's commonly used in residential construction, so it's 0.025 inches thick. Let's say the wall is 6" thick, and it's 20F outside and 70F inside. Steel has an r-value of about 0.001 per inch, so that piece has an r-value of r-0.006. But due to the air cushion the assembly has an r-value of 1.006. There will be a temperature gradient across the piece proportional to the r-value, so the inner face will be at 45.15F and the outer face will be at 44.85F. It's important to realize that this piece is not at ambient temperature of either side, due to the insulation of the air layer.
So what happens when you attach a flange to each side? It's going to be connected to the part that is above or below ambient, but it is also going to be insulated by the air layer. On the warm side the end of the flange will be warmer than the through piece, and on the cold side the end of the flange will be colder. There will be three heat flows in this assembly. There will be a heat flow from A to C (from the figure I posted above), determined by the R-value and thickness of the steel and the temperature at A and C. There will be a heat flow from B to A and from C to D, determined by the temperature difference between B and A and C and D. And there will be heat flow from the environment to surface AB and CD, determined by the R-value of the air layer, the size of the surface and the average temperature of the surface.
All of those flows have to be equal. Solving for that (I can show the math), I get that on the cold side the inside corner is at 35.7F and the outer edge is at 38.8F. On the warm side the inside corner is at 51.2F and the outer edge is at 54.3F. The heat flow through the assembly is 4.3 BTU/hr. This equals an assembly r-value of r-1.45. R-1 of that comes from the air layer on each side, so the steel has an effective r-value of 0.45 or 0.075 per inch. While this is still very small, this is about 75 times larger than a solid piece of steel in the same dimensions.
The above assumes a perfect insulator in the space between the flanges. I haven't done the math but I don't think a piece of foam changes the behavior materially. In no case could it increase the r-value.
Deleted
Thanks DCcontrarian, yes, I think my methodology needs to be tightened up. I re-ran my simple heat leak-down test (20 minute time intervals and an electronic heat probe) and it came pretty close to replicating my initial findings. We (my son and I) have some more thermal probes and relays, Arduino etc on order, all of which should arrive in the next three days or so.
I am building a box that is covered on all six sides with 6" depth of polystyrene (overlapping 2" layers). I will leave an 18" X 18" hole in the top surface. That hole will be tested with 1) no insulation but for the 1/2" plywood 2) 6" of polystyrene and 3) in-filled with 9 x 2" wide X 18" long thermastut test pieces. Note: this reperesents about 50% of the top surface of the test rig.
The test rig will be placed in a temperature controlled garage (about 45 degrees) about 3 feet off the floor. An internal heat mat will bring the rig up to 110 degrees and an automated data logger will kick in and plot the temperature readings in tight intervals upon cool down (after crossing back through the 110 degrees). This will provide a heat loss comparison between the above 3 experimental conditions.
Later, a whole second set of tests will use a watt meter to record the steady-state enegy requirement to maintain each test protocol at 110 degrees over a period of X hours.
I will publish all the primary data along with graphs and some photos (later next week assuming all the necessary equipment arrives on time.) In the meantime my son will take a look at the software that Akos recommened above and hopefully get it to work. Cheers.
R-value testing is federally required to be at 75°F mean temperature, ±25°F. Anything else will not be a fair comparison to other insulating materials or assemblies, as almost all of them perform better at lower mean temperatures. ASTM C-518 describes the testing procedures and it's pretty affordable if you're serious about testing.
Hi Mike. Thanks for the information. We are still waiting for a some components to arrive but otherwise we are ready to do some testing (which may take a few days in order to ensure long enough heat-soaking and test-cycle times).
At first glance it looks like our test rig approximates the above requirement enough to get a first approximation. If the thermastrut design performs moderately, versus terribly, we will continue on to repeat the process according to the ASTM standard in the near future. Best.
Here's what I would expect.
Let's say the box is a cube 2' on a side. It has an outside area of 24 square feet. Let's say the foam is R24. The plywood and the air layer probably gives another R1 so R25 total. The formula for heat loss through an assembly is area*temperature difference/r-value. So with a 45F outside temp, 110F inside temp, difference of 65F, we get:
65* 24/25= 61.4 BTU/hr, or 18 W.
If the insulated stud has the same R-value as the foam, that would be unchanged with the test piece. If, say, the test piece was really R-8, and it's two square feet, you'd have 22 square feet of R25 at:
65*22/25= 57.2 BTU/hr
and 2 square feet at R9 at:
65*2/9= 14.4 BTU/hr
Total 71.6 BTU/hr or 21 W
Now, 18W and 21W are different from each other. What I don't know is how many measurements you'd have to make to establish the difference, it depends on the variance you see. IE, if you do the first test and the measurements average 21 but range between say 15 and 30 you're going to need to do a lot of them to have confidence in the methodology. On the other hand if they range between 20.9 and 21.1 you could have more confidence.
I'd much prefer trying to maintain a steady state, trying to model a cooldown is impossible without knowing the heat capacity of the interior of the box and that's going to be difficult to measure with any precision.
I'm not sure what the purpose of the plywood alone test, but I'd expect:
22 square feet of R25 at:
65*22/25= 57.2 BTU/hr
and 2 square feet at R1 at:
65*2/1= 130 BTU/hr
Total 187.2 BTU/hr or 55W
That's a huge difference and should be easily viewable.
The plywood alone is more of a control test. Assuming the 1/2 " plywood is about R0.5 to R0.6 it sets up a comparitive range between the 6 " of foam at about what R24 to R27 to see where in that range the Thermastrut lands.
I agree the steady-state, engergy input is probably better. We will do both. This is basically an evolutionary test procedure from an initial assumption that it would not be better than solid wood to 'oh, maybe it is better for some unknown reason'.
If all the next week or two of testing, at this small scale, is somewhat positive then we will consider building a much larger rig of some description and again test the steady-state energy input versus X surface area exposed, but that would cost more money and time so for my budget that will have to wait.
i don't understand the structural performance of the CFMF stud without being restrained both on the inner flange and the outer flange top and bottom. seems weak to fasten only on the front flange and on the bottom.
In what force vector are you refering to?
Note: these need be viewed as an assembly of two or more struts and they theoretically can be anywhere from 26 gauge (with a double hem on the front flange) through to something like 12 gauge if used in light gauge steel framed construction, versus being surface mounted (like a Larsen-truss) to a "monopoly framed" structure.