Contended Insulated Foundation Detail

I’m at the end of my rope here… I’ve been trying to get through the building plan review process for over a year. I had designed what I thought wouldn’t be a strange stem wall and slab foundation (I think a monolithic slab is out because of a 3 foot grade difference?) based on GBA articles on smartly insulated foundations, and really specifically this article from buildingscience.com: https://www.buildingscience.com/documents/insights/bsi-059-slab-happy.
I’m in zone 4, building a small ~850 square foot single story home.
My plan reviewer (who I’ve heard is notoriously… wrong… but what can I do) said that if I plan on a poured foundation, versus block, it must be engineered. So I sent my structural engineer my foundation plan and asked him to do a design for the stem / foundation wall.
He, in his typical fashion, marveled at why his services were needed, “this is all normal stuff”, and then sent back the black and white drawing attached.
Naturally it completely ignores what I sent him and makes no allowances for the slab insulation etc. When asked about whether cutting the “shelf” into the foundation wall for the slab and insulation would work he said “Yeah that’s fine”. But when asked to amend the plan he, very confusingly for me, said “Sorry I have no way to modify a standard detail taken directly from the Code Book.”
Isn’t this what an engineer… does?
During a brief rare phone call in which we got disconnected it sounded like he was saying, and sticking to, “The minimum thickness of a foundation wall is 6 inches”. If that’s the case, how did this buildingscience detail ever come into existence… It seemed like the right way to go as it keeps me from having a large section of fragile exposed foam on the outside of the foundation.
I am trying to do this _right_ but feel like I’m doing it so wrong.
Is this foundation detail problematic elsewhere? Has anyone actually built with it?
I’m considering moving the insulation to the exterior of the slab but am concerned about the appearance and durability of a 3 foot tall section of exposed foam. https://www.greenbuildingadvisor.com/article/getting-slab-edge-insulation-right
The “simpler alternative” cantilevered wall there seems like it would set off more alarm bells with the planner also…
Is the only code-approved way to do this just to stick the fragile foam insulation to the outside of your stem wall?
GBA Detail Library
A collection of one thousand construction details organized by climate and house part
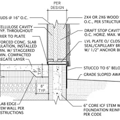
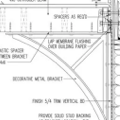
Replies
Tyler,
I don't know what's going on with your engineer, but he doesn't have to follow the prescriptive paths in the building code - that's the whole point of employing him. This is a fairly standard detail I and many other builders use routinely, however if you are going to get a lot of pushback, maybe it's easier to use an alternative. Apart from moving the insulation to the exterior there are a few others:
- Pour the foundation 8" wide and cover the exposed exterior portion with a cap flashing.
- Reduce the foundation to 6" and taper the top of the insulation between the slab and stem-wall so that it isn't exposed.
- Cant the outside of the 8" stem wall at 45 degrees so it is reduced to 5" at the top.
Your engineer might mean that he can't change the actual drawing taken from the code book, but he can provide a detail that meets code requirements even if it means creating a new drawing. Assuming you're on the IRC, this section relates to minimum thickness: https://codes.iccsafe.org/content/IRC2018/chapter-4-foundations#IRC2018_Pt03_Ch04_SecR404.1.5.2. It says that the concrete needs to be at least as thick as the framed wall above. On new construction I usually have 10-12" thick double-stud walls and a similar foundation to what you propose; code officials and professional engineers I have worked with all interpret the IRC requirement to mean that the concrete needs to be at least 5 1/2" thick, to match a 2x6 stud, or sometimes engineers will let me go down to 5" for the raised portion. You may need to start over with a different engineer.
It might also be worth pointing out that the "shelf" in the stem wall in this case is not to support the slab, but simply to make the stem wall thickness match the wall framing thickness so that there is no exposed stemwall inside the house to create a thermal short. The slab is fully bearing on the compacted fill, not the stemwall. We like to see stemwalls 8" thick or more for strength and stiffness over their entire height, but a thinner section at the wall bearing doesn't change the strength much if at all.
Tyler,
I have gotten some pushback in the past with this detail, but only in highly engineered homes in seismic zones built on old landslide debris (...I know. I know). The structural & geotechnical engineering explanation for why it wouldn't work was that the slab (along with additional interior strip footings under the slab that tied together footings on opposite sides of the house) was an integral part of the bracing / lateral resistance of the stem walls - essentially the idea was that is there was a seismic shift, the foundation and house would move as one piece. Sort of like a raft slab.
So, it's not unheard of for the detail not to fly... but I figure it's probably safe to assume that these conditions don't apply to your home?
What we've done in the past is pretty much what Malcom suggested above: move the insulation to the exterior of the stem walls (typical for us here in Montana). We will sometimes also taper the top of the insulation so it is covered by the slab (although, in the above seismic situation, we couldn't do this).
I'm sorry if this was mentioned above, I didn't see it: Are you planning on having the slab be your finished floor? If not, you can just use whatever thickness stem wall your engineer / plan reviewer wants, put in the border strip of insulation for a thermal break, pour the slab up to it, and run your floor over the foam - that way you're not tied to the thickness of your exterior wall framing + finish + baseboard to cover the foam. One way would be to run two layers of Advantech and put your finish floor on top of that (basically, a floating floor).
You can acccomplish this with block, and it will be just as strong, durable, and constructable as a poured wall.
Use 8" block, and transition to 6" block for the last row. It is 5+5/8, but with a 3/8" parge coat it easily meets requirements, gives you the shelf you need for the insulation, and it's all standard detail that requires no further involvement from engineers.