Insulated Basement Slab Vapor Barrier Retrofit

I have insulated my basement slab with 1″ expanded foam board with floating 3/4″ T&G OSB biscuit joined on the ends according to the Mixed Humid Builders Guide. The walls have 2″ expanded foam board. Expanded foam was chosen to allow drying to the interior. 6 months later the subfloor started cupping at the seams. Afterwards I figured out that a vapor barrier wasn’t installed under the slab when the house was built, which would explain my problems.
I have been thinking about my options and have come up with 2 that I think will work.
1. Seal the floor with epoxy as recommended in this article. Any recommendations on manufacturer’s?
2. Replace the slab with 2″ XPS insulation and a poly vapor barrier underneath. Possibly pouring the new slab flush with the footing for extra headroom which is currently 7′ 6″. Why they would do this in a 30 year old house I have no idea.
Any thoughts on my ideas? Thanks in advance.
GBA Detail Library
A collection of one thousand construction details organized by climate and house part
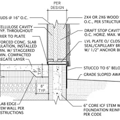
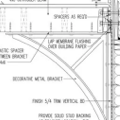
Replies
Andrew,
It's possible that all you need is a layer of polyethylene between the existing concrete slab and your rigid foam.
Concrete slabs and concrete basement walls do not need to dry to the interior. The idea that concrete should dry to the interior, long promoted by engineers from the Building Science Corporation, was a mistake. For more information on this topic, see Joe Lstiburek Discusses Basement Insulation and Vapor Retarders.
Martin,
Thanks for your reply. I wasn't aware that advice had changed. Would anything change if I added 2" XPS to the exterior of the basement walls?
If I used poly under the foam would I be limited by flooring choices? I would like hardwood or engineered hardwood if possible. Would the poly need to be sealed to the basement walls with some sort of sealant or adhesive?
Don't get TOO excited, and go off half-cocked. I suspect people have been misconstruing Joe-L on this one.
Basement walls don't need to dry to the interior IF...
...there is a good capillary break between the concrete and the sill plate (metal or EPDM is better than a foamy sill gasket, which is better than nothing...)...
...OR...
...you have a good 15-18" or more of exposed above grade foundation to dry toward the exterior, and 18-24" overhangs on the eaves/rake to limit drip edge splash-back wetting of the exposed concrete.
Screw the interior air moisture getting into the concrete in the winter- it's the CAPILLARY WICKING, of moisture up from the footing that really matters to the foundation sill(!). The concrete doesn't care if it's wet, but the foundation sill does, and without a capillary break the moisture content of the sill & band joist tracks the moisture content of the concrete. If you can jack up the house and slip some EPDM between the concrete & wood, GREAT! Otherwise, let the basement walls dry toward the interior. Even though that represents a latent-cooling load, it's a manageable load, and far cheaper in any time frame than replacing the foundation sill, and may even be cheaper than retrofitting a capillary break for the foundation sill in a 25 year time frame.
In new construction you can put capillary breaks between the footing and foundation wall, and even between the footing and the surrounding dirt, as well as a capillary break between the concrete & foundation sill, at which point the moisture content of the foundation wall becomes a "Who cares?" scenario. But in retrofits these details are largely absent, and it pays to be a bit careful to mitigate or retrofit those missing details.
It's too late to put a capillary break between the footing and foundation wall, which would also help, but if you break out the slab and dig up the footing, install a perimeter drain to a sump and at least 4" of clean 1/2-1" stone (no fines) underneath your foam layer. Keeping the footing dry lowers the moisture load of the wall & foundation sill/band-joist.
Instead of 2" of XPS, which comes with a high global warming hit due to it's blowing agents, and degrades in R value to EPS levels in about a century as it releases it's blowing agent. By contrast, you could use 2-3" of EPS (R8.4- R12.6) which has delivers than 1% of the global warming hit of R10 XPS. It'll all be R4.2/inch after 100 years, so from a sustainability point of view it's better to start off the R value where you finish, with a much reduced lifecycle damage. Even though XPS starts out life at R5/inch for a weighted average on a 25 year presumed lifecycle basis, it's true performance at age 50 is about R4.5/inch, but in that 50 year span it's whalloped the climate more than the energy use it has offset, in a sub-slab application. (How much varies by subsoil temp, basement temp, and heating energy source, of course.)
Andrew, pardon me if I insert my personal question into the conversation but Dana has brought up a topic that I have been concerned with regarding my own basement insulating plan - that is the moisture transfer to the sill plate.
Dana et. al, I want to install additional rigid insulation on the interior portion of my concrete basement walls. I have excavated around the foundation and installed waterproofing membrane, some exterior insulation, and a proper exterior draintile (same as you described above) in the heavy clay soils. Due to the age of my house (35 years) I am not confident a capillary break was installed on or under the footing prior to pouring the walls. There appears to be a capillary break installed between the concrete wall and the sill plate that looks like fiberglass insulation (was that once how it was done?).
Should I be concerned about moisture transfer to the sill plate if I install interior rigid insulation that fully encloses the exposed concrete walls? I do not have any exposed concrete wall to the exterior (its now covered by rigid insulation), but I do have 5' deep roof overhangs for what it's worth.
I also plan on caulking at the sill plate as the fiberglass insulation-like capillary break is a source of air infiltration, but that would also eliminate any possibility for moisture from the concrete to escape at that location.
So....am I making a problem, or am I making a big deal about nothing?
Thank you in advance.
Pete,
Dana will probably chime in with his opinion, but here is mine: I imagine that everything will be fine if you proceed as planned.
First of all, some sill-seal products consist of a fibrous insulation like fiberglass enclosed by two polyethylene facings. If that is the type of sill seal you have, it may include a capillary break.
Second, you can monitor the condition of your sill occasionally to see whether moisture accumulation is a problem. My prediction is that, considering all the factors you have listed, your house will be fine.
Any opinions on my additional questions?
Pete: See if you can dig out a section of the sill-seal material as a sanity check. Without facers fiberglass is a moisture wick, not a capillary break.
Five foot overhangs and good surface grading away from the house provide a HUGE benefit for managing the bulk water from rain, but does nothing for capillary wicking from the footing. If your footings are near the seasonal water table (like mine) it's a problem. But if the footings are 10'+ above the local water table, even with the capillary wicking of the clay, it's not a huge hazard.
With the membrane on the exterior there's no down-side to using a semi-permeable rigid foam (unfaced EPS) on the interior, since the primary moisture source would then be whatever is wicking up from the footing. Even at R12 (3" of Type-II EPS) you have over 1-perm of drying capacity toward the interior, which would be PLENTY for protecting the foundation sill, even if the footings are sitting in water. (If XPS, keep it to an inch or less, and if polyiso, use only fiberglass faced goods, not asphalt felt facers and certainly not foil facers.)
Can-foam or FrothPak sealing whatever that sill gasket is would always be the right thing to do. Either is still over 2 perms @ 1/2" thickness and the amount of air-drying you'd get through that thin crack is miniscule no matter what. The 1x sill itself runs about 1 perm at 15% moisture content, higher when wetter. Sealing and insulating the sill with as much as 2" of closed cell foam is usually OK, as long as the concrete's moisture content isn't too high.
Andrew: Adding 2" of XPS to the exterior above grade portion reduced the drying capacity toward the exterior to about 0.6-0.8 perms, heightening the importance of the capillary breaks (&/or drying toward the interior. That's reduced even further if you use an EIFS finish as opposed to a standard stucco or other cement-type finish.
If you use poly under the foam, it can trap water between the foam and poly which would take forever to dry, which can jeopardize the finish floor if it's sensitive to moisture. If you put the poly between the foam and the slab that can't happen- the concrete will wick any excess moisture from the pouring/curing and dry reasonably quickly toward the interior. You're always better off waiting some months before finishing a slab with moisture-sensitive materials, but if you have pockets of liquid water trapped between poly under the foam those months could easily become years.
Dana,
Thanks for your response. I am ok with exterior EPS in lieu of XPS. Actually I was wrong to start with, I was planning on using polyiso, not XPS. How does polyiso compare to EPS and XPS from a sustainability standpoint? Your advice about the poly was for under a new slab correct? What about on top of an existing slab?
Polyiso uses the same low GWP blowing agent as EPS, but the same basic chemical feedstocks as polyurethane. Polyurethane and polyiso are very similar in many respects, but very different in others, and quite different from polystyrene. It has comparable R/inch as closed cell polyurethane, doesn't melt (even when burning), and has a comparable kindling temperature as polyurethane that is considerably higher than that of polystyrene. From a global warming per unit-R perspective it's in the same league as EPS, maybe even slightly better.
But unlike polyurethane polyiso is somewhat hygroscopic and VERY vapor permeable. It can take on water, and loses it's insulated properties when water logged, so it's not to be used on the exteriors of foundations below grade or under slabs where it's guaranteed to saturate over time The facers on polyiso determine it's vapor permeance, and foil-faced goods are true vapor BARRIERS, unlike unfaced EPS or XPS, so stackup matters. Where you're looking for retaining some drying capacity through foam, EPS is your friend. If you're looking for a true vapor barrier to block moisture transfer, foil-faced polyiso (or foil-faced EPS) does it.
If you're leaving the old slab and laying down a layer of foam under a wooden sub-floor, it's usulally best to put the poly between the slab and the foam. If you're pouring a thin slab over the top of the foam, the poly goes between the foam and the new slab.
Thanks for the background info on the foam types. So I would want to use foil-faced polyiso on the above grade exterior walls and EPS on the below grade exterior walls. What does "stackup matters" mean? Stacking layers of foil-faced foam?
So basically the poly goes between the foam and slab whether above or below the slab. Are there major pro's or con's to using poly vs. epoxy on the existing slab? I really don't want to have to do this a third time.
"Stackup matters" means:
When you insert a vapor barrier or strong vapor retarder layer into a building assembly, it matters where it's located relative to the moisture and temperature profiles across the assembly. If you put foil faced polyiso in a wall, you want to be sure that it isn't creating a condensation issue where that condensation can become a problem, or blocking a drying path that causes a moisture problem at some other part of the assembly. eg: If you put a foil facer on the exterior above-grade portion of the foundation wall, (or the interior face of of the foundation wall) the moisture content of the concrete will be higher, which may have consequences for the foundation sill if there isn't an adequate capillary break between the susceptible wood and the concrete. If you're not sure about the robustness of the capillary break, use only materials in the wall stackup that allow some drying capacity, to either to the above-grade portion of the exterior, or to the interior.
Oh ok. I understand what your talking about.