Installing Polyiso Foam Over Concrete Slab

I purchased a large quantity of recycled fiber faced polyiso for my exterior insulation retrofit. I have quite a bit left over and thought I could use it to insulate my concrete floors. The house is built slab on grade.
I was a little concerned about the way any potential moisture might affect the fiber facing. I dont currently have a moisture issue and the slab is more than 60 yrs old…but I thought I’d err on the side of caution. My plan was to cover the slab in 6mil plastic and then lay the polyiso on top…followed by 3/4 t&g mechanically attached to the slab with Tapcons.
Any issues with this plan?
GBA Detail Library
A collection of one thousand construction details organized by climate and house part
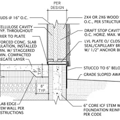
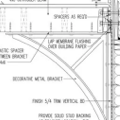
Replies
Hi Shane,
Martin Holladay has written an article about this idea. It includes the basic steps for installing rigid foam above an existing slab and how to control moisture: Installing Rigid Foam Above a Concrete Slab.
Thank you. I’ve read this article along with several others. Ive also considered floating two layers of plywood with overlapping seams...glued and screwed like Martin mentions. My real concern is the fiber facing on the polyiso. Martin suggests EPS and my type of Insulation (with fiber facing) isn’t really mentioned. I’m wondering if I need to worry about mold growth because I assume it contains organic matter. I figure the 6 mil poly between the concrete and polyiso should help with this. And I’ll certainly due my best to make it air tight...but am I taking a chance of future mold problems with this plan?
Tapcons are about the most labor intensive method for doing this. OF course in the event of an unexpected gravity shift, they would hold the floor down well.
I would think you could let it float pretty easily.
Or a moisture barrier trowel on adhesive. I used this to hold down plywood on my concrete floor to attach hardwood to, and it has lasted 10 years so far. I used an air powered 't' nailer to hold the plywood down while the adhesive dried, much faster than tapcons. I think you could use concrete blocks if time was not an issue
I, too, would be nervous about the fiber-faced portion of the insulation down there. I’d also be surprised if there wasn’t moisture present from soil wicking, even in a 60 year old slab. You could always tape a 3x3 piece of barrier to the floor and let it sit for a while to see what you’re dealing with. In any case it seems like there are a couple of options...
One would be a well detailed vapor barrier. It sounds like you’re thinking in those terms already with the 6-mil plastic. However, I might consider bumping that thickness up a bit. Others can correct me here, but I remember reading somewhere that 6-mil plastic is considered a retarder, not a true barrier.
The other option would be to buy thin EPS and detail it with a high-quality tape, letting it serve as the vapor barrier and the placing the poly iso over the top. 1/2” foil faced eps is around $8 per 4x8 in my area.
You don’t mention square footage, so the latter may be too expensive to be worthwhile.
Either way, I’d consider a double layer of plywood for the floating floor as noted in the article Kiley referenced and suggested by Keith above. 60 year old concrete is pretty darn tough to drill into.
I would also 2nd Brian's suggestion of a layer of EPS underneath. You can also go with one of the drainage tiles typically used for finishing basements to space the polyiso off the concrete.
Fiber face polyiso tends to taco when it gets wet, a floor will inevitably see some spills/leaks. This is fine if restrained with screws, don't know if it would cause issues with a floating floor. Even if you do go floating, I would still screw it down a bit.