Insulate addition walls, attic space, and partial cathedral ceiling
Hello,
I began planning to re-roof the first floor addition on my house. The addition consists of a 24’x16′ room with an attic space above and a 10×16′ room with a cathedral ceiling (monoslope/shed style roof with the high end intersecting wall of the 2nd story main house). The main house is stucco over brick, built in 1900. The addition is concrete block and was built in 1969. The age of the home means it is very poorly insulated. I am trying to use the re-roofing as an opportunity to add more insulation. I have also removed some nasty looking paneling from the 24×16″ room and will be adding insulation to the walls in this room.
I live in SE Pennsylvania (zone 4).
Plan:
24’x16′ room:
2 of the walls in this room had paneling installed which I have removed. Underneath is some drywall in poor condition. Between the drywall and the concrete block are .75″ furring strips and it looks like .75″ of Styrofoam. the 3rd wall (16′) has a brick veneer and a fireplace installed. the 4th wall (24′) buts up against the main house along 14′ and against the 10’x16′ room along 10′. My plan for this room is to remove the drywall and furring strips from the 2 exterior walls (other than the brick fireplace wall), air-seal where necessary and re frame the area with 2x4s and add R-15 fiberglass bats and put up new drywall. I will then blow cellulose insulation into the attic area to add to the existing fiberglass bats.
10’x16′ Room:
The smaller room in the addition has a cathedral ceiling with a mono-slope/shed roof with the high side connected to the outer wall of the 2 story main house. This area is currently un-vented and insulated with fiberglass bats, (7″ rafter bays). I have read venting a shed style roof is not a good idea (snow drifting) so will be keeping it un-vented. After doing some research and reading many articles/forum posts on this site I think I have 3 options:
1. Insulate above the current roofing sheathing. Add 3 layers of 2″ poly iso rigid insulation over the current sheathing. Where the cathedral ceiling meets the attic, I will add 2-3 layers of poly iso to isolate the attic from conditioned space. This is the part I have not found much information on. I think the best way to do this would be to cut through the current roof sheathing so that the vertical insulation meets up with the roof insulation and create a continuous envelope. Is this the correct procedure? Doing this would create a step on the roof with the section above this room 6.5” higher than the rest of the roof. I think the best solution would have been to install rigid foam over the entire roof, however there is a window ~6” from the roof deck over the 24’x16’ space and building up the roof height here is not possible. With the extra trim/flashing/sheathing and long screws this looks like the most time consuming and expensive option.
2. Spray closed cell spray foam against the underside of the sheathing using a DIY 2-part kit. This appears to be the easiest option.
3. Cut poly iso to fit between rafter bays and spray foam seams.
Any help/recommendations would be greatly appreciated!
Nick
GBA Detail Library
A collection of one thousand construction details organized by climate and house part
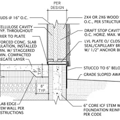
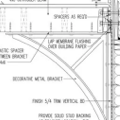
Replies
Nick,
Dana gave you a very comprehensive answer. The two red flags in your plan are the idea of installing fiberglass batts directly against CMUs (concrete blocks) -- that's generally not a good idea -- and the idea of using the cut-and-cobble approach for an unvented roof assembly (also not a good idea).
For more on why you don't want to use the cut-and-cobble approach, see "Cut-and-Cobble Insulation."
There is one option you didn't mention (unless I missed it): You can hire a spray foam contractor to install closed-cell spray foam against the underside of your roof sheathing.
For more information on combining rigid foam above the roof sheathing with fluffy insulation under the roof sheathing, see "Combining Exterior Rigid Foam With Fluffy Insulation."
Nick,
Q. "Where the cathedral ceiling meets the attic, I will add 2-3 layers of polyiso to isolate the attic from conditioned space. This is the part I have not found much information on."
A. You didn't fully describe it, but I think you are talking about vertical polyiso -- used to insulate a wall that separates conditioned space in your addition with unconditioned space (the attic of your old house).
You've got the right idea. The insulation has to form a continuous thermal envelope, without interruptions, so that your conditioned space is separated from adjacent unconditioned spaces. At intersections, make sure that the insulation is continuous (uninterrupted) and that the air barrier is also continuous.
You can't safely put fiber batt insulation directly in contact with a CMU wall. Fiber insulation wicks moisture. If you have 3/4" of polystyrene insulation (the "Styrofoam" mentioned) it provides at least SOME amount of capillary break, and at ~R3 would be sufficient for dew point control on a batt insulated 2x4 wall in your climate zone. But the whole assembly would be a bit shy of code-min, which calls for a continuous layer of R5 for an R13 2x4 wall. The thermal bridging of the studs cuts the performance of the cavity insulation down to about 2/3 of it's performance, so adding another R2 to the cavity insulation is NOT the same as adding R2 of continuous insulation.
If you strip the furring only leaving the 3/4" foam, then fill in the gaps with new 3/4" foam then glue a continuous layer of 1/2" foil faced polyisocyanurate there would be an even better capillary break (the foil facers), and it would raise the foam-R to R6-ish, with no question about meeting the letter of code. Alternatively, using a continuous layer of 3/8" XPS fan-fold siding underlayment (about R1.9) would also get you there, but the half-inch foil faced polyiso solution is both greener, and arguably easier to air seal using foil tape, and easier to install using just foam board construction adhesive (which uses solvents compatible with foam board, unlike standard construction adhesives), no fasteners.
With either solution the 2x4 studwall & wallboard is substantially isolated from the high moisture drives of the CMU wall, and there is ample dew point margin for being able to use just standard interior latex paint as the interior side vapor retarder.
On the roof insulation front:
1: With as little as R15, (3" of polyiso ~R17, using standard 2lb density goods, R19 for 1lb foil faced) above the roof deck you can safely install up to R35 of air & vapor permeable on the underside of the roof deck. A standard 2x8 rafter bay is 7.25" deep, so R30 rock wool would be the right solution. For the IRC prescriptive for exterior-R minimums (at code-minimum total R, in your case R49) see:
https://up.codes/viewer/utah/irc-2015/chapter/8/roof-ceiling-construction#R806.5
With 2lb roofing foam that would "only" be R47, not the code-min R49, but since the 3" of exterior foam is a thermal break over the rafters it beats the performance of R49 between joists, and would meet code min on a U-factor basis with no problem. If using reclaimed roofing iso the cost of the foam is about 1/4 to 1/3 that of virgin stock goods. Factory seconds cosmetic blem foil faced polyisio is typically half the cost of showroom-perfect goods. These folks might be a good source (or not- shop around):
https://chambersburg.craigslist.org/mat/d/factory-seconds-of-foilback/6632725632.html
The thinner foam + fluff approach means standard latex ceiling paint is a sufficient vapor retarder, yet allows ample drying capacity for the roof deck. Interior latex is more than an order of magnitude more vapor open than R49 of closed cell foam (which would be a "dries never" assembly from a practical point of view.)
2: The DIY closed cell kits are expensive and not very green, due to the HFC245fa blowing agent- not recommended. It has to be applied in lifts no greater than 2" at a time to avoid being a fire hazard as it cures, and putting R6/inch foam between framing is a waste of good foam, since the thermal bridging of the framing severely undercuts it's performance.
See:
https://www.finehomebuilding.com/membership/pdf/184243/021269086NRGnerd.pdf
3: Cut'n' cobbled rigid foam board between the rafter suffers the same performance issues as sprayed closed cell foam, but also introduces the risk of convective moisture transfer to the roof deck, since it can't be made reliably air tight for the long haul. (Yes, field failures of this approach are not rare in unvented roofs.)
Thank you all for the input and detailed answers. Dana do you suggest adding foam to the entire roof or just over the cathedral ceiling portion? Adding 3" foam + .5 sheathing will only leave about 2" from the top of the window sill and the counterflashing would end up over the top of the sill. I think this could work but I would be worried about the sill rotting/possibly having water enter the window.
Is using spray foam insulation (contractor) a viable approach or will I end up seeing the same thermal bridging through the rafters? This option would be most expensive for just the insulation, but I would save on an extra layer of roof sheathing long screws and some trim/flashing.
Fot the interior walls I will put up foam board before the 2x4 framing. Is any other vapor barier required or will the foam accomplish this if taped and sealed on the edges? Most of the old drywall is still up but from what I see the old polystyrene looks like it was cut pretty rough with alot of gaps between the furing strips so it may not be worth trying to reuse on these walls but I may be able to find a better use somewhere else.
Nick,
What you end up deciding depends in part on your goals and your budget. If you can afford to install rigid foam over your entire roof, the results may end up looking better and being more satisfactory in the long run. But that option costs more, and requires you to rethink the insulation plan in your vented unconditioned attic.
Similarly, if you are worried about the fact that an existing window will end up with a sill that is close to the height of the roofing, you can always reframe the opening and install a smaller window (as long as the new window meets any egress requirements, if applicable). Again, a decision like this depends on your goals and your budget.
You're right that installing closed-cell spray foam on the underside of the roof sheathing doesn't address the thermal bridging through the rafters. That isn't necessarily a deal-killer, though. Every job involves trade-offs.
On your walls, if you install a layer of rigid foam against the concrete blocks before you frame your 2x4 wall, you don't need an interior vapor retarder. (In fact, there is no code requirement for an interior vapor retarder in Climate Zone 4). As with all energy retrofit work, attention to airtightness is always essential.
Martin,
My main goal is to create a structurally sound roof system. I do not have the budget to make the entire home as energy efficient as possible but if I can cost effectively add some insulation while making other necessary repairs/updates then I will, as in this case with tearing out the paneling/old drywall in the 24’x16’ room. The current unconditioned attic does not appear to have any moisture/structural issues. The window is a 3'x7' original window which matches the other 6 on the main house. I would prefer not to replace it. I think a better bang for my buck would be to air seal (current ceiling in this room is foam tiles and I will be replacing with drywall) and add blown cellulose. I also plan to add blown cellulose to the 2nd floor attic at this time as well. The one possible structural issue with the unconditioned attic space is ventilation. The current space has a ridge vent and a ~9x9 gable vent. There are no soffit vents but there are airgaps around the soffit and facia which is allowing some airflow. Before adding the cellulose insulation, my plan was to add soffit vents and ventilation channels.
For the other room:
I tore off the fascia on the current cathedral section. The fascia had some dry rot and several of the rafter tails are also dry rotted. From what I can see the roof sheathing is good condition with no dry rot, however where the unconditioned/cathedral sections meet the sheathing on the cathedral side has pulled away from the rafter and warped upwards ~ 1/2-3/4". I believe this was caused by water damage to the facia, when I moved into the house the gutter in this section had pulled away from the facia and water was going behind the gutter and down the facia. Is there any way the lack of proper insulation (fiberglass batts) contributed to this?
If I was to spray foam the inside of the cathedral section, will the thermal bridging possibly cause condensation issues? How much foam is needed to prevent issues? This is what I am most concerned about in this section of the house. This area has windows all along the outer walls and a skylight so it making it energy efficient will be a hard battle. The home does not have central air so I only use window units in the bedrooms and one living area which is separated from this room by the kitchen. During the winter I tend to keep the heat fairly low so even with the current leaky house my energy usage is not very high.
Again thank you very much for all of your help,
Nick
Nick,
Q. "From what I can see the roof sheathing is good condition with no dry rot, however where the unconditioned/cathedral sections meet the sheathing on the cathedral side [something] has pulled away from the rafter and warped upwards ~ 1/2-3/4". I believe this was caused by water damage to the facia, when I moved into the house the gutter in this section had pulled away from the facia and water was going behind the gutter and down the fascia."
A. I have inserted the word "[something]" in your question -- I'm not sure what you are talking about here, but I'm guessing that the "something" that pulled away from the rafter is the roof sheathing.
Q. "Is there any way the lack of proper insulation (fiberglass batts) contributed to this?"
A. No, but it's possible that the lack of a proper ventilation channel contributed to this. Without a ventilation channel between the top of the insulation and the roof sheathing, moisture can accumulate in the roof sheathing.
Nick,
Q. "If I was to spray foam the inside of the cathedral section, will the thermal bridging possibly cause condensation issues?"
A. No.
Q. "How much foam is needed to prevent issues?"
A. In Zone 4, the building code requires spray foam installed in this location to have a minimum R-value of R-15. This requirement is based on the assumption that the builder will also be installing additional fluffy insulation on the interior side of the spray foam, to reach the total code minimum roof/ceiling R-value of R-49.
But even if you skip the fluffy insulation, R-15 of spray foam won't result in moisture problems -- just higher-than-usual energy bills. For more information, see this article: "Combining Exterior Rigid Foam With Fluffy Insulation.".
Thank you Martin, I signed up for a premium membership but haven't been able to access the premium articles yet. I will read when I am able, I have read many of the other articles you have written and they have been very helpful.
You are correct in my meaning in the first question you answered. I should have had a comma after meet or worded the description more clearly in the sentence "where the unconditioned/cathedral sections meet, the sheathing on the cathedral side has pulled away". In this location the sheathing on the cathedral side has warped and pulled up from the rafter.
A. In Zone 4, the building code requires spray foam installed in this location to have a minimum R-value of R-15.
I was not sure if the insulation would behave in the same way on the interior of the roof rather than the exterior. I am still weighing my options but since I am tearing off the roof anyway in this location it probably makes the most sense to put rigid foam on the outside. The downside is some extra flashing work. The area is on the back of the house so will not be very visible and I don't think it will look bad even if it is.
Out of curiosity, how do the new IECC regulations work (2018 has been released). Is it up for the locality to adopt the new code? From what I see Pennsylvania's current code is IECC 2009 which says only R38 is required in ceilings. I may be wrong on this but I could not find anything in my local or PA code referring to newer insulation codes.
Link: https://energycode.pnl.gov/EnergyCodeReqs/?state=Pennsylvania.
My town, West Chester still uses IBC 2003. I downloaded a copy of this standard. Section 1301.1 says: Buildings shall be designed in accordance with the IECC, but no version is given.
If I go with 3" foam on the roof deck + rock wool in the stud bays I get over R-38 but may be slightly under R-49.
Nick,
Q. "I was not sure if the insulation would behave in the same way on the interior of the roof rather than the exterior."
A. If you install R-15 closed-cell spray foam on the interior side of the sheathing, it will have the same resistance to condensation as R-15 rigid foam installed on the exterior side of the sheathing. The building codes treat these two types of insulation as equivalent (when it comes to the ratio rules for foam-to-fluffy).
That said, they don't "behave the same way" -- because the exterior rigid foam reduces thermal bridging through the rafters, while the interior spray foam has no effect on thermal bridging through the rafters.