Insufficiently thick exterior foam: Remove, increase, ignore?

Hi there,
I’ve been reading the articles on GBA about exterior foam and I think mine is too thin to keep the sheathing above the dew point. I’m wondering your opinions as to the best remedy. I’m assuming that removing or increasing the thickness will both be expensive. I believe my wall assembly is risky, but have no evidence it is actually a problem. Given that I’m wondering if the best course of action is to live with it. Here are the details:
– 2 x 4 walls
– .75″ polyiso
– Plywood sheathing
– No rain screen
– Stud cavities filled with fiberglass batts
– No interior vapor barrier
– Climate zone 6 (Cabot, VT)
Greatly appreciate your thoughts.
GBA Detail Library
A collection of one thousand construction details organized by climate and house part
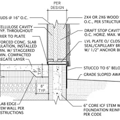
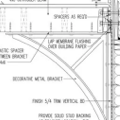
Replies
Maybe Kohta will chime in hear, but he and John Straube gave a presentation at NESEA this month talking about moisture of course. I believe they were looking at CZ 6 with 50% indoor humidity and the worst scenario was a wall assembly that had rigid foam on the outside, but nowhere near enough. It allowed condensation to develop, but it hindered drying to the outside.
Jeremiah,
Tough call -- but if it were my house, I'd probably do nothing. Just engage in "watchful waiting."
The lower your interior relative humidity during the winter, the lower your risk. So you might want to buy a few hygrometers. Operate your ventilation system to keep your winter interior RH at 30% or below.
When it's time for remodeling, inspect what's going on. Good luck.
-- Martin Holladay
- 2 x 4 walls
- .75" polyiso
- Plywood sheathing
- No rain screen
- Stud cavities filled with fiberglass batts
- No interior vapor barrier
- Climate zone 6 (Cabot, VT)
If the sheeting is on outside of the foam you should be OK. Your assembly looks a lot like the ZipR walls.
I looked at the ZipR wall and I do not recall seeing any climate zone rules.
If you want to be certain use an Inferred camera to find your coldest spot open up the wall and see if you find any mold.
Walta
Walter,
The rules for the minimum R-value of exterior rigid foam apply to Zip-R sheathing as well as to the walls built by Jeremiah Breer in Cabot, Vermont. For more information on these rules, see Calculating the Minimum Thickness of Rigid Foam Sheathing.
If your Zip-R sheathing has too low an R-value, or if Jeremiah's layer of rigid foam has too low an R-value, the interior face of the rigid foam won't stay warm enough during the winter to avoid condensation. You'll end up with beads of water or frost on the interior face of the rigid foam. This moisture can drip down and form puddles on the bottom plate. Eventually, you can get mold or rot on your bottom plate.
-- Martin Holladay
The most important first step is to verify that the wallboard is air-tight, since air convection from the interior into the cavities moves a LOT more moisture in than vapor diffusion through standard interior latex paint. Chasing the leaks down with a blower door (or a large window fan, room by room) can start at any time. Use a decent long lasting flexible caulk (polyurethane caulks are good). You may have to pull some floor/window/ceiling trim to really nail it all in an aesthetic fashion.
The most susceptible walls will be those that get no or minimal sun, such as north facing walls or shaded walls. If possible, paint those walls with half-perm "vapor barrier latex primer", but wait at least until July/August to allow plenty of warm weather drying time for the sheathing. Half perm paint goes a long way toward limiting peak moisture, but it slows drying.
+1 on air sealing and low humidity. Also note that if you keep the interior at a lower air pressure than the exterior, air won't leak outward - even with never-perfect air sealing.