Beefing Up Insufficient Flash-and-Batt Insulation

House is 15 years old in zone 6 (northern NY state). Builder used flash and batt in the walls. Noticed some water stains on an unfinished (osb) floor in a loft area. Opened wall and found only 1/2 inch of flash on exterior wall sheeting with unfaced R19 batts with poly stapled up but slit open behind sheet rock. Can I replace poly with certainteeds membrain and have a workable system that will prevent condensation on the flash in the wall cavity? Or is the only option to apply a couple inches of spray foam? Then install less batt fiberglass?
GBA Detail Library
A collection of one thousand construction details organized by climate and house part
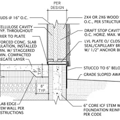
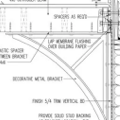
Replies
Generally the thin layer of SPF works with a solid warm side air and vapor barrier, the slitting the initial builder did is probably what created some of the problems.
Going with a smart vapor retarder that is well detailed should work great. Make sure you seal the vapor barrier around the perimeter, tape any seams and replace any regular device boxes with vapor tight ones. Getting everything air tight is the most important part.
To double check... it is okay in this case to have a thin layer of SPF on the exterior wall sheeting, then working inwards... unfaced fiberglass batt, well detailed smart vapor retarder (Certainteed Membrain), then sheetrock painted with a quality latex paint? Just goes against conventional wisdom (my lay person understanding) to have two vapor barriers but I'm assuming you suggest this okay because the smart aspects of the Membrain (i.e., will prevent moisture transmission in winter and allow drying of the wall cavity in the summer)? I talked to a Certainteed "Customer Experience Team" member and they just referenced not having two vapor barriers. Unfortunately it was clear they were reading off scripts after doing word searches based on our discussion and had no real understanding of the application of their product in this case. Your recommendation seems to make sense to me which is why I contacted Certainteed in the first place, unfortunately they didn't seem to have the training or experience to really answer my questions with any reassurance they knew what they were talking about, not knocking the individual, they did their job and were polite but the whole wait one... [typing]... response read off of computer wasn't reassuring.
I agree with what Akos is recommending here. In regards to your customer experience team experience, the issue is that they are thinking the Membrain is a vapor barrier when in fact it is a vapor retarder. The SPF is the vapor control layer (the least permeable part of the assembly as it is essentially vapor impermeable). The Membrane is a vapor control layer also, but it is permeable- and at different rates depending on the levels of RH it is experiencing at any given point in time. These 'vapor barrier' and 'vapor retarder' terms often get confused by people. Too bad the folks at the customer service center don't have this basic understanding of the terminology sorted out...
Use Table 2 below for a good wall. You don't have enough spray foam for 2B, which leaves 2A. 1/2" of spray foam will be about 2.5 perms, which isn't vapor impermeable or a vapor barrier. But it does prevent flow through at 5 perms, meaning you need a Class I on the interior.
+1 on a lack of an interior side air barrier (ie, holes in the poly) being a problem. It needs to be well air sealed.
https://www.appliedbuildingtech.com/system/files/200311_abtg_rr_1701-01_moisture_control_guidelines_figure_update_final.pdf
This will lead you to the same Class I conclusion.
Best solution: add a little more spray foam - which will then allow a Class II smart-retarder on the interior side.