In trying to insulate a cold, north-facing parlor of my 1890 house, rigid foam board was recommended

In trying to insulate a cold, north-facing parlor of my 1890 house, rigid foam board was recommended in this forum. Further driving revealed that only one of 7 walls (there’s a bay window) had enough space for that, and for 6 of the 7 walls, there’s only…
Also, there’s aluminum siding over the walls with the bay window. Otherwise, the exterior is brick.
GBA Detail Library
A collection of one thousand construction details organized by climate and house part
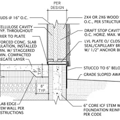
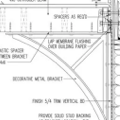
Replies
Susan,
You didn't say whether you intend to install the rigid foam on the interior or the exterior. Because you mentioned that the exterior is brick, I'm guessing that you're talking about installing rigid foam on the interior. But I may be wrong.
We need more information.
1. Are you planning to install rigid foam on the interior of your wall, or on the exterior?
2. What is your climate zone or geographical location?
3. What exactly do you mean when you tell us that "only one of 7 walls had enough space for that"?
4. What is your question?
Have you removed the plaster so the walls open on the interior?
Is there any knob and tube wiring present in the walls?
You do understand that insulation is useless unless you have an effective air barrier to stop the wind from blowing thru your walls.
Are you willing to make the walls thicker and give up interior space?
You may find this blog interesting. http://www.frugalhappy.org/blog/2018/1/15/insulation-walls
Walt
Martin, My question was truncated somehow.
I'll use bullet points rather than my usual narrative style.
- When I asked about insulation last year, I thought each wall surface had the same amount of space between the plaster and lathe and the brick.
- However, when a contractor came in and drilled into each wall surface, we discovered that for most of the room, there was only about an inch and a half.
- One contractor recommended cellulose.
- Another contractor said cellulose settles, and recommended "slow-rise two part foam".
Question: Do you agree with either of them?
P.S. I just got your book "Musings of an energy nerd" and will read the chapter on insulation.
Walter,
I have not removed the walls, but there are four or five holes, each about 2 inches in diameter, in the walls (due to the desire to dehumidify after a water accident.)
- I don't believe there is any knob and tube wiring in those walls, but it's possible.
- I thought that the insulation created a barrier, and neither contractor discussed an air barrier.
- Another contractor recommended building the walls out with studs and then insulating with fiberglass, but I have 5 large windows with old molding in that room and would rather not do so.
I will look at that blog - thanks, Susan
- Another contractor recommended
Martin, To answer your questions:
1. I assume that with only an inch and a half of space between the exterior brick and interior plaster and lathe, there's not enough room for rigid foam.
2. I live an hour west of Philadelphia.
3. For some reason, the wall to the right of the bay windows has about 5 inches of space between the plaster and lathe and the brick, whereas the wall perpendicular to the right and the wall perpendicular to the left only have about an inch and a half, as does the wall to the left of the bay windows.
4. My question is how to insulate a room in a Victorian with little space to insulate. Thanks again.
Susan,
The types of insulation materials used for walls have a maximum R-value per inch of about R-6.5 per inch. That's physics. You are in Climate Zone 5. In your climate zone, the prescriptive requirements in the building code generally require a minimum of R-20 insulation, which requires a little more than 3 inches of room to install. Again, that's physics.
You can certainly install insulation with a lower R-value than R-20 in a retrofit situation if you want -- and some people would even argue that your brick walls qualify as "mass walls" under the code, and therefore could be insulated to only R-13 or R-17 -- but thinner insulation will never perform as well as R-20.
You can insulate a brick wall on the exterior if you want, but then the appearance of your house will change, and it will become a stucco house.
You can insulate a brick wall on the interior if you want, but then your room will become smaller, because the 3 inches of insulation takes up room.
Finally, you should know that an old brick house shouldn't be insulated with fiberglass batts on the interior. Read this article to learn more: "Insulating Old Brick Buildings."
I did not see an answer to my question about knob and tube wiring. Please understand it is a big fire risk to add insulation to a wall with K & T wiring and it is not uncommon for sellers to hide K & T wiring with short sections of modern wiring in the outlet boxes.
I think you need to be very careful with your insulation plan this house, has survived 125 years because the wall can dry to the inside with lots of heat in the wall to dry things out.
With any insulation plan I would want to see an air gap between the siding/brick so it can continue to dry.
It is completely understandable if you are unwilling to give up the space on the inside and or the original trim to make room for insulation. The most important thing is to do no harm to the house.
If opening up the walls is out of the question, I think adding insulation is too dangerous.
My guess is you can improve the comfort in the room if you do a good job of sealing up the air leakage. Most contractors will not spend the time necessary to do a good job at this type of work.
Set a fan up to blow air out of the house and use the smoke from an incense stick to locate the leaks and calk them shut.
Walt
Just back from vacation - thank you to both of you. I'm thinking I should finally accept defeat on insulating this room, at least for now. However, I will seal up air leakage.
Best Wishes, Susan
Not exactly factual: "Please understand it is a big fire risk to add insulation to a wall with K & T wiring..."
...writes Walter Ahlgrim.
The risk is primarily theoretical, not based on a history of high numbers of actual fires. The theory is that poorly implemented twisted splice connections could heat up sufficiently to ignite cellulose insulation or wood that is indirect contact with the splice if insulated. That's demonstrable in a lab but field data doesn't support a high risk. (More fires are caused by deteriorating metal-clad BX wiring than K & T, according to an aquaintance of mine working for the fire department in a city with large numbers of houses wired with either BX or K & T.)
In several states (California, Nebraska, Oregon & Washington) it's now legal to insulate over knob & tube in wall cavities provided it has been inspected for corroded or poorly implemented splices, and in some of those states it can even buried in attic insulation provided it has been inspected, with locations marked, with signs posted to alert anyone in the attic of it's presence. (Sometimes the insulation itself has to be non-combustible too- as in "not foam, not cellulose".) eg:
https://www.menlopark.org/DocumentCenter/View/80/Knob-and-Tube-Wiring-Safety-Requirements-for-Attics
https://www.sanjoseca.gov/DocumentCenter/View/1753
https://www.mytpu.org/file_viewer.aspx?id=42840
More: https://www.pct.edu/files/imported/business/nssc/docs/articles/KnobTube_Report_WTC.pdf
Of course decommissioning / replacing knob & tube wiring removes all question, but the "...big fire risk..." aspects are completely overblown. It's not inherently unsafe to insulate over it, especially if using non-combustible insulation such as rock wool or fiberglass.