In a flash & batt roof, should the foam encapsulate the rafters?

In a flash & batt approach to a flat roof deck or unventilated attic, should the closed cell foam encapsulate the rafters?
This is for an inhabited attic, with a sloped roof, in new construction but in working on the problem I realized it would also apply to a low-slope roof over living space. So I’m asking it for both.
My first thought is that I could simply detail the CCSPF (closed cell polyurethane foam) to be of the required minimum depth, between the rafters, and then make up the rest of the insulation with batts, also between the rafters. However, I’m questioning whether the rafters themselves, only providing a much reduced R value, will be inclined to act as condensing surfaces.
I could have the foam coat the sides of the rafters to their full depth, an inch or so thick. This would act as a vapor barrier, and then I could still use batts in between. The downside is that it will be much harder to install the batts because they will be too wide for the left-over space. And of course it would use more foam.
I work in several different climate zones so for purposes of discussion lets assume I’m in Zone 5 and I can work it out from there.
And also, yes, I know, there are other solutions that don’t involve spray foams. No need to bring that up. It won’t help me get an answer to my specific question. Thanks.
I’ve attached a photo that shows a flashed attic before the batt goes in.
GBA Detail Library
A collection of one thousand construction details organized by climate and house part
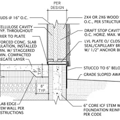
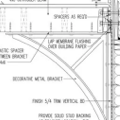
Replies
If you're adding batts, foaming over the rafters isn't necessary. Note that with flash-and-batt you have to add a relatively airtight material at the interior; indoor air can't circulate freely through the batts or else you will get condensation.
Michael,
This is basic and I should know it, but - could you elaborate?
If the CCSF is the minimum depth to create an air/vapor barrier, shouldn't the interior-side of the spray foam stay warm enough that if air moves through the batts and hits the CCSF, it won't be cold enough to be a condensing surface? Assuming that the CCSF is at least the minimum depth to be an air/vapor barrier, and assuming that there's the right ratio of air-impermeable to permeable insulation for a given climate zone.
Or, are you saying that the rafters could be condensing surfaces in a flash & batt install, if there's not a good interior air barrier?
In theory, a sufficiently thick layer of spray foam should be OK BUT in practice, there tend to be problems. It's safest to use some type of interior side air barrier, which is usually just a standard drywall ceiling (although I'd recommend taking care to install it as "air tight" drywall, which isn't hard to do). I find that putting batts in the rafter bays to limit air movement tends to help with moisture issues too, even if the spray foam is intended to be thick enough to provide ALL of the R value for the assembly (this is based on personal experience).
The interior side air barrier is there to prevent moist air from getting up into the assembly, circulating around, and finding devious ways to condense out and cause problems. The spray foam ends up being the primary air barrier for the building envelope in most cases. You should take care to seal off the ends of the rafter bays if they connect to other parts of the structure too.
Bill
Paul,
I asked the same question and Michael gave a detailed answer in this thread:
https://www.greenbuildingadvisor.com/question/michael-maines
Thank you Malcolm - I read that thread when it was posted, but clearly didn't retain much. Appreciate the re-link!
Paul,
I had it bookmarked because I have a mind like a sieve.
What I didn't mention in the thread that Malcolm linked to is why condensation happens if there isn't an interior air barrier. I covered it here: https://www.finehomebuilding.com/2011/01/20/why-flash-and-batt-makes-sense#:~:text=Fiberglass%20batts%2C%20on%20the%20other,cost%2Deffectiveness%20of%20fiberglass%20batts. I wrote it in 2011, before I understood the importance of reducing embodied carbon emissions, so add that to the financial cost of foam. I'll attach the key drawing from the article.
The gist is that the batts or fill layer keeps indoor heat from reaching the interior face of the foam, so in cold weather, the face of the foam will be significantly cooler than the interior temperature. If it's below the dewpoint temperature, condensation will occur.
That's when using something close to the minimum prescribed by the IRC, which is based on Joe Lstiburek's recommendations.
An older rule for using a mix of foam and fluffy insulation, in cold climates, is to keep roughly 2/3 of the R-value in the foam. In most cases that will keep the interior surface of the foam above the dewpoint temperature, but it depends how cold it is outside, for how long, and the interior humidity level. And it requires more foam than staying closer to the IRC requirements.
My thanks to all of you. That was an interesting, and for me surprising, discussion. Even with a good impermeable/permeable ratio there can still be problems. And thank you, Malcolm, for the link to the earlier thread. I read that as well.
Since there will be a drywall ceiling, I'm not too stressed about it then. It does raise the issue of what to do with a board ceiling. If the budget permits drywall under the boards that's an option. I gather another option would be to put up a variable perm sheet attached to the bottom face of the joists/rafters, and board over that.
Thanks again.
Before variable-permeance membranes were available, on a few projects with vaulted ceilings I did specify or use a layer of fire-taped and painted drywall under the wood boards. Since then I always recommend a variable permeance membrane. Long ago I also installed several board ceilings myself over kraft-faced fiberglass; I'm worried how those are fairing, but at least they were vented roofs.
It's become standard practice in my market & area to put up a layer of 5/8" gyp between framing and wood lids. The drywall is fire taped at minimum, and brought to a higher level if there's a possibility that the ceiling material might change during the build (which happens pretty frequently).
This is probably already on your radar, but if you go that route - and I think it's a good solution, budget permitting - you'll probably want to put up something between the gyp and wood boards so that you don't start seeing gaps open up with seasonal movement. We use a lot of reclaimed coral board, and it's typical to paint the gyp black (more labor and cost) or staple up black weed mat (fast & cheap). If (when) the ceiling boards open up a bit, you just see a thin black line and it goes away visually.
In that picture that you posted, there is a red arrow pointing to a gap between the collar tie & the roof rafter.
In my experience as a former spray foam estimator - this gap (if you can't "wrap the back" of the collar tie with foam) should be addressed with a "flash" of foam on three sides ....