Improving the building envelope for existing bump-outs

We are in the process of addressing repairing some structural framing issues (dry rot caused by bulk water intrusion due to missing flashing) in our 110-year old home, a two-story balloon-framed foursquare in Manhattan, KS (climate zone 4).
Since we have to remove the siding to repair the framing, we’re taking the opportunity to tighten the envelope and add insulation. The new wall structure will be (from interior out): original lathe-and plaster, 2×4 framing on 18” centers with cellulose-filled cavities, existing board sheathing, taped zip-system panels, two staggered layers of taped 1” polyiso, a ¾” rain screen gap created with 1×4 furring strips secured to the framing, and finally LP SmartSide lap siding (using the original siding’s reveals of 4” and 2.5”).
We’ve already converted the primary roof to an unvented assembly by spraying 6” of closed-cell foam under the roof deck. However, there are a couple of bump-outs that I am uncertain of how best to handle the details on. One is relatively small – a 10’ wide section cantilevered a couple of feet out of our kitchen. It is a major source of drafts in the winter. Would wrapping the roof and base of this bump out in the same layers as the walls of the house be sufficient, or is there a better strategy?
The other area is a 6’ x 20’ one-story room on the north side of the house built on top of a crawlspace. I’m planning on encapsulating and insulating the crawlspace (as its dirt floor is a major source of moisture in the adjoining basement), but I’m not sure how to best handle its roof. The roof is hipped, and a relatively gentle slope (about 5/12). Currently it has about 3.5” inches of blown cellulose on the ceiling, plus R-19 fiberglass batts laid on top of that. It shares a water wall with the house that contains the main sewer stack and pipes serving the upstairs bathroom. This space has also been used to route HVAC flex-duct to several upstairs rooms (though I am in the process of replacing those inadequate ducts with new runs in the conditioned space). Before the attic was spray-foamed, the water pipes would occasionally freeze in the winter. I am also dropping the ceiling in this room by eighteen inches to conceal the new HVAC supply ducts and an ERV, both of which are routed on the south side of the space. The ERV ducts will angle over the HVAC supply to reach the joist spaces of the upstairs.
What would be the best strategy for insulating and air-sealing this space? I can’t add any height to the existing roof deck – it is too close to one of the second story windows.
GBA Detail Library
A collection of one thousand construction details organized by climate and house part
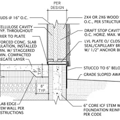
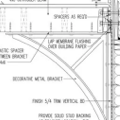
Replies
User-6885249,
First of all, care to tell us your name?
Second, did you know that LP wants you to use 2x4 furring strips over your rigid foam, not 1x4 furring strips, when you install SmartSide lap siding? For more on this issue, see Installing Lap Siding Over Foam.
Nathan,
The basic principle of air sealing work is making sure that your air barrier is continuous, and that transitions between roofs and walls, as well as between walls and foundations or floors, are properly addressed.
It seems that your go-to air barrier for the roof assembly is closed-cell spray foam. It would have been logical to include the underside of the roof sheathing of this bump-out when the rest of your attic was insulated. Why was it skipped?
Martin,
It's Nathan. I was aware of the 2x4 furring strips, but then I saw (in the revisions to the article you mention) that LP issued a technical note allowing for 1x4 furring for certain species of wood. I still might do 2x4 - but I'd also like to maintain as much of my roof overhang as I can (our zoning district wants 12" minimum overhangs).
The attic was insulated after we tore out the existing finished walls to locate an electrical short - turns out it was the only Romex / Knob and tube splice in the house that was actually in an electrical box, but the box was buried in the wall. Once we had the walls down, it seemed a good time to replace the inadequate and poorly installed 2" mineral wool batts.
The laundry room (the room in question) still has its finish ceiling in place. When installing the HVAC duct I found a layer of some kind of fluffy particle board that I was worried might contain asbestos, so I'm reluctant to tear it out.
Nathan,
So, if I understand correctly -- you told the spray foam contractor to skip this section of your attic -- you should invite the spray foam contractor back to install spray foam on the underside of the roof sheathing above this room.
Before the spray foam contractor shows up, however, you should test the existing insulation for asbestos (or get an experienced inspector to tell you whether it looks like vermiculite). You don't want to endanger your contractor's health. If it's vermiculite, you should pay to have a certified asbestos abatement contractor to remove the vermiculite safely. For more information on this issue, see Fixing Attics With Vermiculite Insulation.