Improving production build in Arizona

We’re looking at production house in Zone 2 (outside Phoenix), where most builders don’t even fully sheath exterior, instead using rigid foam before stucco. Duct work in attic with reflective barrier roof sheathing.
My thought was to negotiate with broker/builder to use taped Zip sheathing (walls and roof), and create conditioned attic with open cell foam. At that point, i’d pay for blower door test and Manual J to confirm heat pump sizing.
Any thoughts if this is practical/feasible? Is Zip Roof/conditioned attic overkill?
GBA Detail Library
A collection of one thousand construction details organized by climate and house part
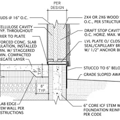
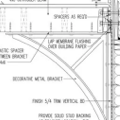
Replies
It doesn't have to be ZIP, but full sheathing detailed as an air barrier makes sense. ZIP tends to be less labor to make air tight, but that's only an issue in high cost labor markets. The southwestern US had tended to have much lower labor rates in construction than the rest of the US.
I understand that EPS sheathing with a skim-coat of stucco is even a security risk in your area, since access to the house is easily gained by people with strong legs and sturdy boots, or a framing hammer and some wire cutters if the skim coat is reinforced with wire.
A conditioned attic only makes sense if there is no other options for locating the ducts & air handler. Going with a plenum truss design and a vented attic full of fluff is probably a lot cheaper than R38 of open cell foam at the roof deck. The truss framing is a bit more expensive, but the insulation is a LOT cheaper.
https://www.greenbuildingadvisor.com/article/use-plenum-trusses-to-keep-ducts-out-of-your-attic
https://www.finehomebuilding.com/membership/pdf/72033/021233086.pdf
https://www.nrel.gov/docs/fy14osti/60056.pdf
With a radiant barrier roof sheathing and R38 of cellulose over a plenum truss it will outperform a code-min R38 fiberglass and RB decking by a measurable amount. Cellulose is opaque to infrared radiation, fiberglass is not, and it has some thermal mass to help level the load by lowering and time-shifting the peak load from the ceiling by several hours.
The vertical R38 coming up the sides of the plenum can be R23 + R15 rock wool batts constrained by chicken wire or rigid foam board to a height a foot above the top side of the plenum, to be filled with open blown cellulose. (R44-ish initial depth, R40-ish after a decade of settling.)
Mtn. Man,
It's hard to teach a builder who doesn't know much about energy-efficient building everything he or she needs to know. It's better to find an educated builder.
Airtightness matters, so your builder should have an airtightness goal -- maybe 1 ach 50, or maybe 1.5 ach 50 -- and should confirm success with a blower door.
Here are links to two articles about keeping ducts indoors:
"Keeping Ducts Indoors"
"Solutions to the Attic Duct Problem"
If you decide to use spray foam to create an unvented conditioned attic, be aware that open-cell spray foam is a riskier choice than closed-cell spray foam. For more information, see "High Humidity in Unvented Conditioned Attics."
Thanks Martin/Dana
I should have clarified we are committed to a home community with limited building sights/builders. Reason for the relocation is to be in same community as family currently is.
Lots of good ideas there to follow up on, especially tangible air tightness goal. My thought was Zip and Spray foam would be easiest to execute with minimal changes to their production process.
Regarding open cell, these all have clay/concrete tile roofs with air channel- is open cell still risky? Would 1-2" close cell and the balance open cell mitigate potential moisture issues? We plan to start in July/August which is monsoon season there- so even though its very dry most of the year, there is potential for wet sheathing (hence my thinking Zip for roof as well).
Don't get me started on Phoenix homes ;) GBA and Scott Gibson did a Q & A Spotlight article on my findings & complaints regarding on how new homes are built in the Phoenix and metropolitan areas:
https://www.greenbuildingadvisor.com/article/why-are-houses-built-this-way
I ended up building my own ICF home in Northern Arizona. Got sick of the extreme heat and the poorly built homes of Phoenix. They emphasize on size and interior upgrades more than they do with quality construction. Energy bills be dammed. $300 per month electric bills are the norm.
Burglars love that type of construction as they just kick or cut there way into the home from the outside with a portable rec saw-zaw. Much easier to break into a home in Phx through the walls than it is breaking down the door or a window. Bugs love the construction also. All the gaps and holes create a haven for insects like scorpions and roaches to enter the walls and home. $500k and $1mil dollar Phx homes have tons of interior scorpion and bug problems. Keeps the pest exterminating companies making $$ millions of dollars per year in Phx.
Peter, that article is what prompted my questions.
We were just out there last week and took a picture exactly like that one- I first assumed they just left for the day without finishing sheathing.
It looks to me like they frame, tar paper, R4 foam, chicken wire, stucco. That and mechanicals in unconditioned attic just seems crazy to me. But we love the area and walking distance to family....
> outside with a portable rec saw-zaw
Which also cuts plywood and OSB quite well. And windows are very easy to break. I wouldn't put much weight on this issue.
Taped foam is a good air barrier - so don't expect much difference with Zip here either.
Jon,
This is of course a "minor" issue compared to the poor construction quality. Although it is a valid concern as there are burglaries committed this way because without sheathing, one can cut through a wall easier than busting a window which creates more noise and risk.
Regarding taped foam as an adequate air barrier (without OSB). I will disagree with you here 100%. They run thousands of staples through the rigid foam to attach the metal lathe. This creates busted out foam everywhere and these thousands of penetrations equals thousands of air leaks.
I never lived in a house that racked as much as my former Phx home. The racking of the house during high winds was unnerving. My gable wall would literally flex in high winds. It sounded like an old wooden ship being battered at sea.
Without OSB sheathing the weep screed condition requires some better detail work. Otherwise you end up with this abomination for air and bugs to enter:
There is the so-called "air barrier" multiplied by 1,000 staples.
This is the end result of open framing without OSB sheating. Wall leaks during heavy rains. It may take 10 years for this to show up as the monsoon rains are sporadic and the water entry into the wall cavity might take a route through the wall cavity that doesn't result in it coming through the drywall. The reality is the walls leak CONSTANTLY in both air and water. 90% of homeowners will have no clue until a hard rain exposes wet drywall.
Sealing windows to open air. Truly unbelievable but it's true. Flashing flapping in the wind. What an abomination to the building trade and building science.
The other photo shows how pathetic the stucco coat is and the lack of OSB sheathing. When running a screw, the stucco collapsed and the screw went inside the wall cavity. They had to find a stud to attach the screw to.
Any updates?
You will have a VERY HARD TIME finding a building company that will allow you to add sheathing to the home or deviate from the house plans. They build these cookie cutter homes and they don't like changes that are not found in the house plans.