Improving ACH

First and foremost,
Thanks to all those who contribute, I’ve learned a lot over the past while reading others’ opinions and posts.
I am in the early stages of planning an exterior renovation to improve the efficiency of our house and we’ll be doing a lot of the work ourselves as I am a carpenter.
We live in Edmonton, Alberta in a two-story built in 2000 with 2×6 walls an interior 6 mil vapor barrier, and fiberglass batt in the cavity.
The exterior sheeting is OSB with two layers of black felt which is not taped covered with vinyl siding.
We recently had an energy assessment completed with a 5.5 Ach at 50 pascals
Our advisor recommended new windows “triple pane”, as ours are original dual pane without Low-E, which have a U-factor ranging from 0.51-0.52 or r2, not the best insulating value granted but are in good condition which is why I am apprehensive about replacing them given their condition.
We priced out new windows on average we’re getting quotes between 17k-24k just for supplied only
Which is 2/3 of my budget.
The more research I do the more it appears I should focus on air sealing.
I wanted to know if would I be better off leaving my existing windows and installing removable storm windows on the inside with tinted plexiglass which will likely cost about $1500 materials only”.
I am thinking of focusing my attention on the exterior by completely removing the siding, felt paper and starting from scratch while leaving the windows for the time being.
Option 1
Tape OSB sheeting with 3m tape, seal the sill plate with a fluid applied that is compatible with Tyvek, and wet-set Tyvek commercial D, tape the joints covered with 2 layers of 2 1/4 inch Eps with offset joints taping the outer seams giving me an r20 with a 1/2 rain-screen with vinyl siding.
Option 2
Tape the OSB with 3m tape, seal the sill plate with fluid applied likely fast flash, wet-set Siga Majvest 200, tape the seams covered with 2 layers of 1.5 inches of rock wool giving me about an r12 with a 3/4 rain screen with vinyl siding
A few considerations with option 1
My initial thoughts would be to avoid installing 4″ of exterior foam as I have an interior vapor barrier which would limit drying potential to the interior but then I read “mind the gap” posted here.
It had a reference about being able to safely install exterior foam on top of a drainable WRB so long as there’s a gap between the two hence Tyvek commercial D “wrinkled WRB” to allow drainage even though I have an interior vapor barrier.
Just wanted to seek people’s input on such a wall assembly, it is a more economical solution roughly 35+/-%, easier to install with a better r value.
Any thought?
Option 2
After reading “calculating the minimum thickness of rigid foam sheeting”,
According to the article my climate zone 7 a would require R15 exterior insulation to keep my walls warm enough to avoid condensation,
Does this apply if you are installing exterior Rockwool insulation or would 3″ R12-R13 suffice?
Your input is appreciated.
GBA Detail Library
A collection of one thousand construction details organized by climate and house part
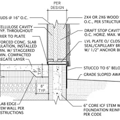
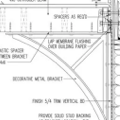
Replies
As someone who did a substantial addition and renovation on a 100 year old home that happened to also improve its energy efficiency (AKA a 'deep energy retrofit'), I would likely never advise on doing a renovation project purely focused on energy improvements such as you've described.
I would focus solely on air tightness via whatever reasonable means. If and when your siding needs to be replaced, then you can consider other things, but it likely doesn't make any sense to do so before then (unless you just want to burn money).
How many windows are we talking about that operate and how many are fixed? Sliders or casement?
With regard to condensation, the dew point doesn't care what kind of insulation you use, so yes, R15 would be the minimum exterior, and I'd do R20 given the climate extremes we are seeing. We are stuck in Canada with code requiring the interior poly, however the research pretty much shows that warm sheathing is generally dryer too. R20 of Roxsul is the "safer" bet, but as you have observed..not cheap to source/install.
Dennis,
"With regard to condensation, the dew point doesn't care what kind of insulation you use, so yes, R15 would be the minimum exterior"
The dew point doesn't care, but if the exterior insulation is permeable, and the wall can dry to the outside, where the dew point is doesn't matter much. That's why the code mandated levels and ratios of exterior insulation only apply to impermeable insulation like foam.
Malcolm, I understand the permeability/code issue but in Edmonton, it's not unusual to have temperature swings from +5 C to -20 C in just a day. So yes, the wall can dry outwards with Roxul, but I would want to avoid condensation in the walls if it was my build as the likelihood would be pretty high that it would occur in that climate, particularly north exposures. Thoughts?
Dennis,
That's probably good advice. Why impose a burden on the sheathing it doesn't need to have? But I'm left wondering how a wall with any amount of exterior mineral wool is riskier than the standard 2"x4" or 2"x6" ones with none, that are most commonly built and seem to function well?
PJ has poly at the interior wall face, so currently that is all that is preventing water vapour reaching the outside sheathing and condensing at low outside temps. Right now, the wall can dry to the outside.
But tape OSB seams, add wrap and the sheathing drying ability to the outside will drop. 1.5” of Roxul will not bring the dew point outside the sheathing so any air leaks into the wall cavity will still condense on the inside of the exterior sheathing. Increase outside insulation to R15 or better, and there is reduced risk of condensation inside the (now sealed up) sheathing as the dew point of the wall system will now be outside the sheathing.
So with a 2x6 wall that already has a poly air/vapour barrier (in Edmonton), I would be a lot happier going with R20 for the CE insulation, (regardless of permeability), particularly if the exterior sheathing is going to be air sealed.
This is a good read on the subject: https://continuingeducation.bnpmedia.com/courses/huber-engineered-woods/continuous-insulation-in-framed-exterior-walls/3/
Dennis,
Sorry, I'm still not following the logic.
- The dew point in the existing wall is inside the sheathing - and the wall is fine.
- The first change proposed is to tape the sheathing and replace the building paper with house-wrap - and we know walls build that way have a good ability to dry to the exterior.
- The second is to add exterior rock-wool, which also doesn't significantly reduce drying, and while not sufficiently thick to move the dew point outside the sheathing, will keep the sheathing warmer, and thus safer - or at worse as safe.
I just don't see where the increased risk comes from. I understand the concerns with impermeable foam (which is what the Huber article you linked to is about) but not rock-wool.
Here is Martin's take on it:
"Mineral wool insulation can be substituted for rigid foam insulation on the exterior side of wall sheathing. One advantage of mineral wool over rigid foam: because mineral wool is vapor-permeable, it doesn’t inhibit wall sheathing from drying to the exterior. That means that builders can install mineral wool of any thickness on the exterior side of their walls. You don’t have to worry whether exterior mineral wool meets any minimum R-value requirement. (Of course, thicker insulation always does a better job of resisting heat flow than thinner insulation.)"
You may find this article helpful. The author chose to use Rockwool on the exterior because there was poly in the walls.
https://www.greenbuildingadvisor.com/article/wrapping-an-older-house-with-rock-wool-insulation
Unlike foam, there is no minimum thickness for exterior Rockwool because it’s vapor permeable. I am unsure what you mean about sealing the sill plate because the sill plate is normally accessed from the basement. Do you mean to seal the bottom of the sheathing to the foundation? I agree with Patrick that this will be a huge undertaking. I would suggest taping the sheathing and adding exterior insulation at a future date when you replace the windows and siding at the same time. Other than replacing the windows, were there any other recommendations from the energy audit? Did the person who did the assessment locate any specific air leaks? Due to the stack affect, most leakage will be at the top of the house and the bottom of the house. This would be the ceiling plane on the second floor and the sill plate/rim joist area in the basement, so you you may want to start with those two areas. There is a video series on GBA showing how to air seal the ceiling plane in an unconditioned attic.
And here is an article explaining how to air seal the attic.
https://www.greenbuildingadvisor.com/article/air-sealing-an-attic
If you want to improve air sealing, focus on the holes in your walls, not the walls. So, traditional air sealing, not siding and windows. You’ll find a lot of articles on the topic here at GBA and at BSC. Almost all of them will tell you to seal the attic floor first, and then possibly blow in cellulose insulation to cover up all the old insulation that you just displaced and compressed while searching for air leaks around wires and any other penetrations in the ceiling/attic floor.
After the attic, look at the rim joist in the basement to air seal it and then insulate it with rigid insulation.
At that point you’ll probably be see measurable improvements in ACH, and if you were in the USA you’d be past the point of needing mechanical ventilation, which is where you should spend your extra money instead of on windows. Being in Canada, you may already have mechanical ventilation, I know my friends in Ontario have had ventilation requirements for a while now.
There are other approaches to air sealing, this is just a summary of the most common suggestions here. The work on the exterior walls is a separate project, IMO.
From a return on investment the things on your list are very unlikely to save enough fuel to recover what they cost.
Replacing windows will never recover the high cost. Only consider this if the old windows at made of aluminum or are literally falling off the house. If you want to replace for comfort that OK but it is quite a luxury.
Removing good siding to air seal and insulate is a non-starter financially. And from a green point of view sends to much useful materials to the landfill needlessly. Sounds like the current wall is R20 or so the amount of energy to be saved is pretty small beyond R20.
I think you should find someone to do blower door directed air sealing and try to getting the ACH-50 number well under 3 should be achievable If you can get 1.2 or so would be great. As a DIY project duct taping a box fan into a window and using the smoke from incense sticks to locate the leaks and caulking to plug them can find and fix them just as well.
When it is cold have the house inspected with inferred camera locate any missing insulation.
Walta
Upgrading windows soley for energy efficiency probably won't pay back, unless perhaps you were starting with aluminum framed single pane windows. I would look at the storm window option though, which "fakes a third pane". I don't see why you would go with tinted plexiglas though -- why the tint? You're pretty far North, so solar gain in the winter is a GOOD thing, and not as much of a bad thing in the summer since you probably don't have much of a cooling season. I would skip the tint. I would also consider polycarbonate instead of plexiglas (which is acrylic), since polycarbonate is far more durable. Note that both materials are subject to scratching though.
Regarding posts #6 through #9:
ANY amount of exterior insulation of ANY type shifts the dew point further outwards in the wall assembly, because the exterior insulation makes everything inside the wall WARMER, so DRYER. If the sheathing were the outermost surface in the assembly, it would be the coldest -- close to outdoor ambient temperature -- and any moisture in the wall would condense there as long as the outdoor ambient was at or below the dew point of the interior air (assuming most of the moisture is leaking into the wall from INSIDE the home). If you add even R3 of exterior insulation -- regardless of the ratio of interior to exterior insulation -- you have increase the average temperature of the sheathing above the outdoor ambient in ALL cases, meaning you have REDUCED the condensation risk. That means you're better off, but how much better off depends on the ratio of interior to exterior insulation, as well as the vapor permeability of the exterior insulation in this case.
Exterior mineral wool is very vapor open, and as such it does not reduce the drying ability of the wall assembly at all. This is why the ratio of interior to exterior doesn't really matter here -- the exterior mineral wool ALWAYS increases the average temperature of the sheathing, and doesn't reduce the drying ability, so it only helps you. This means you REDUCE the amount of condensation that will occur inside the wall, which is better/safer, and you don't inhibit the ability of the wall to dry to the exterior, so there is no downside to the exterior mineral wool insulation here.
If you go with vapor impermeable exterior insulation, then the ratio of interior to exterior R value matters, because you HAVE reduced the drying ability of the wall to the exterior, so you have to keep condensation from occuring in the first place. Now the ratio comes into play, to ensure the average temperature of the sheathing remains above the dew point nearly all of the time, so that the wall doesn't need to dry -- there is no moisture condensing out to begin with. In this case, the ratio of interior to exterior insulation determines what the temperature of the sheathing will be since the temperature of the sheathing is proportional to the ratio of the R values and the thermal delta through the wall. In the simplest example, if it's 0F outside and 70F inside, the sheathing will be 35F if there is R15 in the studbays and R15 of exterior insulation too.
For the OP: I would price out EPS (the cheapest rigid foam) and compare it to rigid mineral wool. You may find you can hit at least code minimum R values with EPS for similar cost to a lower R value worth of mineral wool, in which case the EPS option is the way to go: it's safe from a moisture standpoint, and more R is better for energy efficiency. I would tape the seams of the sheathing for air sealing, and I'd pay particular attention to the perimeter of the framed walls (sill plate, corners, etc.), since you probably don't have a bead of sealant in between the framing and the sheathing in those locations. A fluid applied WRB is probably a good way to air seal those areas, since it would be able to flow into all the little gaps and cracks that would be difficult to seal by other means.
Bill
Bill, Martin, I do agree completely with what you're saying. However, the reality of older construction is that there are likely more air leaks carrying vapour to the inside sheathing surface, which is where condensation will occur. My point, is that if you raise the sheathing temperature beyond any dew point considerations, then the wall assembly becomes much "safer", and then you can focus on exterior air sealing (retrofit) at the sheathing layer where it would be a lot easier to address on existing construction where interior finishes are not being disturbed. Chances are there is a poly layer (with a lot of leaks!) in place. Again, my comments are very much oriented to cold climate as that is where my experience sits. At -30 C, air leaks and water vapour really expose building issues...and it's often not until spring here that warmer temperatures expose them.
To Andrew's comment, I'd agree that for 7A, the 2" of closed cell in the attic followed by blow in is hard to beat for effectiveness. It's exactly what I've done with my own 1905 vintage balloon frame home which had massive air leaks into the attic.
On the windows, we used triple glaze casements combined with interior acrylic panels (magnetic) in our last commercial project to great effect. That building (along with furred air space interior retrofit) cost all of $192 to heat in a month averaging -20C. It's a 9000 square foot building.
I also had the same manufacturer manufacturer interior acrylic panels to apply to the double hung sliders (vinyl, double pane) in our home and saw a considerable drop in heating costs due mostly I suspect to the reduced air leakage. These panels also drop sound transmission about 50%. I've taken quite a few FLIR images, in one case at -20 C outside temps, and the interior surface is at least 7 to 9 C warmer on treated windows vs identical (as in beside each other) untreated glazing. They are pretty much invisible when installed.
I would say based again on FLIR images that our newer full lite triple glazed door, performs about the same as a double hung slider double pane with the acrylic panel in place. The panels are not cheap, but they work very, very well. In practice, most of them stay in place all year with just a few removed from upstairs bedroom windows.
I can dig up and post the FLIR images if there is interest.
Since your in Edmonton look at the work of Peter Amerongen (https://www.linkedin.com/in/peter-amerongen-155a7540/) and the site https://www.retrofitcanada.com/ which has a number of deep energy retrofit case studies.
There is also some hands on training coming to NAIT in Feb that will teach you all about the issues your are discussing.
https://www.passivehousecanada.com/events/ab-hybrid-150p-nait-feb-2023/
For purely air sealing you can look at areobarrier.
https://www.ecosynergy.ca/
Speaking again to the permeable vs non-permeable CE insulation I found this which is exactly what I'm talking about with respect to permeable vs non-permeable exterior insulation and condensation risk from interior air leaks:
Reference:
https://www.buildingscience.com/documents/digests/bsd-controlling-cold-weather-condensation-using-insulation
"The same solutions that avoid air-leakage condensation will also completely solve cold-weather condensation due to vapor diffusion even if the exterior sheathing is a perfect vapor barrier (e.g., foil-faced or plastic faced insulation boards). If the selected sheathing layers (including structural sheathing, water control, and insulation) are somewhat vapor permeable (such as expanded polystyrene over building paper and plywood), less R-value can be used and diffusion condensation will still be controlled (because much of the vapor that diffuses or leaks with air into the stud bay will pass harmlessly through to the outside by diffusion). If the sheathing layers are very vapor permeable (e.g., rockwool over fiberboard or gypsum sheathing, and housewrap) then very little insulation value is required outboard of the stud bay. However, while these permeable layers can essentially eliminate vapor diffusion condensation risks with lower exterior sheathing R-values, the risk of air leakage condensation does not drop as much: air leakage may still deliver more water vapor to the back of the sheathing than can be removed by diffusion through the sheathing, and hence condensation could still occur and accumulate."
So to the OP, I'd still be looking at R15-20 with Roxul if you're able, or use the 2 layers of EPS for R20. At some point (if you are keeping it for awhile) you will likely not be using natural gas for heat, and the extra expense now on the envelope will make more sense then.
DennisWood,
We may just be going around in circles here, but let me take one last stab at it:
Understanding that the permeable exterior insulation may not be adequate to deal with the problem of moisture accumulation due to of air-leakage, why in this case where the existing walls don't exhibit any moisture damage from air-leaks would they become risky when they are air-sealed - regardless of how much mineral wool was added?
Malcolm, PJ won't know if there are any existing issues, until he pulls the siding off. PJ is looking to reduce permeability of the outer sheathing/OSB by taping seams and adding wrap..if there are interior leaks , then the risk of condensation vs the ability to dry outwards changes.
All I'm saying really is that if the inner surface of the sheathing remains above the dew point always, at any temp in Edmonton, then the risk of a drying issue goes away, as there will be no condensation there needing a drying path. R20 on the outside would achieve that goal. That's pretty much what John Straube says in BSD-163 that I quoted. Permeability of the the CE insulation is irrelevant in that respect.
I'd agree 100% that if you're going to use CE insulation that is permeable, and you decide to use less than the R20, there is no scenario where you'd be increasing risk over what is already present. However, why do that if you can go to R20 and reduce the potential of condensation on the inner sheathing surface to zero, regardless of drying potential?