I’m converting a barn to a residence

The slab is not insulated, and there are no below-grade details beyond the posts that support the structure. My architect is resistant to insulating on top of the slab. He worries that if I don’t leech heat into the soil…
The slab is 64′ x 46′, and 4″ thick. The central section was tapered toward center drains, so we have some leveling to do. We are in zone 5, I believe, and temperatures have recently dropped to -18F, though that is unusually cold. My concerns are comfort as well as avoiding condensation that might degrade floor coverings and encourage mold growth.
GBA Detail Library
A collection of one thousand construction details organized by climate and house part
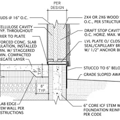
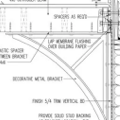
Replies
There is no risk to insulating on top of the slab, especially in a building that is now being heated.
The slab is at greatest risk of frost-heaving when the barn was not heated, and the direction of heat loss is from the ground upward, rather than from the building downward. Frost heaves propogate in the direction of heat loss. With a heated building above it, even that modest heat loss is going to
A: keep the soil directly under the slab above freezing, and
B: the direction of the heat loss is from the slab downward rather than conversely.
The story with foundation walls is similar.
You absolutely DO want to install insulation under your leveling over-slab, along with a ground vapor retarder. Without it the slab can run cooler than the outdoor dew point in summer, increasing the mold potential for any rugs or boxes resting on that cool slab. With insulation under it the slab tracks the temperature of the conditioned space within a few degrees.
In a zone 5 location R5 would be sufficient from just a mold-hazard point of view, but ~R8 would still be financially rational using modest assumptions about the cost of money and future energy costs. With 2" of Type-II EPS (R8.4) that would run you about 75-80 cents per square foot, which isn't much different in cost from a mere R5 using 1" XPS. (And over the next 50 years that R5 XPS performance will fall to about R4.2, whereas the long term performance of EPS is pretty stable.)
Dean,
There are several ways to look at this issue.
1. If the barn slab survived several decades without cracking or heaving, don't worry. After all, I assume that the barn wasn't heated when it was used as a barn. It seems to have survived cold weather.
2. In the old days, the barn contained equipment, hay, and maybe a few animals. When it was -18°F outdoors in the old days, the interior of the barn may have been 0°F or -10°F. So the soil under the slab was probably freezing. Now, however, your new home will be heated. There will be hot air above the slab instead of cold air above the slab, so the soil under the slab is less likely to freeze.
3. You should install vertical insulation at the perimeter of the slab. That will help keep the soil under your slab warmer than ever. If you want, you can also install horizontal "wing insulation" as an apron around the perimeter of your building -- perhaps 6 inches or 12 inches below grade, extending perhaps 4 feet from the building.
5. Imagine a sandwich consisting of a concrete slab with a horizontal layer of rigid foam below. Now compare that to a second sandwich consisting of a concrete slab with a horizontal layer of rigid foam above. To the soil under the slab, these two sandwiches perform the same. The R-value of the two sandwiches is the same, regardless of whether the foam is above or below the slab.
Excellent concepts which I will convey to my architect. Excellent because I'd thought of some of them already (pats self on back).
Martin, I cannot in good faith say that the slab has not cracked. The center "aisle" of the barn has several significant cracks, though I can't say I think any of them show signs of heaving... more like settling due to insufficient substrate support. The remainder of the building is carpeted at this point so I'm not able to comment on how the perimeter of the slab has fared. This building went frrom horse barn, to devided residence and business offices (what barn has 24 T1 data lines coming into it!?) I think we are in a good position to say the various sections have been both heated and cold.
Dana, you used the term "leveling over-slab" which is pretty much what I anticipated. However, only the center third (longitudinally) of the building requires leveling. Is there a viable alternative to a full depth slab-over? Perhaps level the center section then put a layer of insulation throughout, then sub-floor? I estimate a full over-slab would run me about $4000, which I'd gladly use elsewhere! I based my estimate on a 4" depth.
So I shared your thoughts with our architect, and this is his response. Do you share my concern with bridging through the furring strips? Would this assembly mitigate the condensation risk? See what you think:
"Given everything that we have found out about, I suggest a possible solution: 1) spray the concrete sealer that I mentioned above; 2) ramset flat treated 2x4 furring strips @ 16" or 24" oc with cedar shims in the present center corridor area to make it level; 3) add 1 1/2" XPS foam (about R7.5) between the furring strips; 4) install 5/8" or 3/4" plywood floor sheathing (about R0.77); 5) install what ever floor finish that you would want."
Dean,
1. Your concrete sealer may work; I haven't used such a sealer. But, sealer or no, you still need to install a layer of 6-mil polyethylene above your slab before insulating.
2. Your proposed method will work, but there will be thermal bridging through the furring strips. It would be better (although probably not cheaper) to level the slab with a leveling compound or a thin wet mix of concrete or grout with small-diameter aggregate. Once you have a level surface, you can install a continuous layer of rigid foam above the leveled slab without any furring strips.