Icynene Moisture Problem in Cathedral Ceiling

Dear experts I am lost, please help!
I had Icynene light density foam sprayed under a brand new metal roof and the walls of the upper floor. That was in October 2011.
4″ in walls and 6″ between rafters.
It was all fine until now. Now it’s summer we have 36C, 32% RH outdoors right now at noon (June 21 2012), Location: Climate Zone 4.
At the peak of the cathedral ceiling inside it’s so damp that my glasses turn foggy.
To exclude the possibility of indoor moisture going up there I did the following experiment this morning:
I took a transparent plastic sheet/foil and covered a 1 sq foot area of the foam at the peak area. I put a thermometer inside the foil and one outside next to it.
I taped the foil air tight with 6″ of tape in all directions. There is no way air can get inside or behind the foil.
I started the experiment at 9:50AM this morning. Both thermometers show: 24C, 57% RH. Outside we had: 33C, 46% RH.
At 10:58AM, 25C 87%RH behind the plastic, 26C 69% in open space right next to it.
At 12:39, just 2.5hours later: we have 26C 99%RH behind the plastic foil and 27C 86%RH next to it in the open area. Outdoors: 36C, 32% RH
The absolute moisture per m^3 behind the plastic went from 12.3 grams/m^3 to 23.9gram/m^3
What’s going on here? Why is there so much moisture coming through the foam?
The ceiling feels like sauna at the top 5 ft. Obviously the moisture is not coming from lower levels since it’s all A/Ced and the above experiment excludes this possibility.
One more thing: the moisture clears up over night. When I go up there in the morning it’s 50% RH no problems. By noon it’s a sauna. And this cycle has been repeating for at least a month now.
I have a feeling that open cell foam is no good for our climate, despite all the marketing materials claiming otherwise.
Thank you for your help!
GBA Detail Library
A collection of one thousand construction details organized by climate and house part
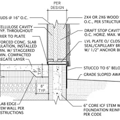
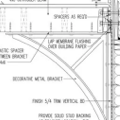
Replies
Oh Lord, where to start… 1. 5.5” of OC foam is R20, you need R38 in CZ4. 2. Have you done a blower door test to see where your air leaks come from? Do you have a tight building envelope? Sealed cathedral ceilings? Crawl space? 3. Is your HVAC system designed, installed and commissioned correctly? 4. Did you install mechanical ventilation? 5. Is your HVAC system capable of controlling humidity? 6. Where is the return air? I’m sure there are many more questions to follow before anyone can answer your question.
Hi Armando
thank you for your answer. Check out Icynene's website. They say r-factor doesn't matter and r20 is enough for our climate. Installers say same thing and I relied on it.
No blower test done at all.
3. probably not. but why does that matter. See I did the plastic foil test to exclude the possibility of indoor moisture source. Or is that wrong? How else can I test whether the moisture actually comes through the foam?
4. No
5. not enough probably.
6. i installed a 8" pipe to take air back down to basement and it worked fine but now I do experiments and hence switched it off.
See I have no doubt that I can install a huge AC to remove the humidity. But the point of spray foam insulation to me was to reduce my energy bill, not increase it.
I have strong evidence pointing towards moisture coming from outside through the foam, see my experiment above. I wonder if anyone else has seen this happening.
I have no doubt that some moisture comes into the house as well but I am not sure if that's the problem.
Ideally I would like to set up experiments and measurements to find out what's causing what.
Hi Don,
Something that may be contributing to your problem is "Sky Radiation"
at night ....Roof becomes much cooler than outdoor temperature
Roof sheathing, rafters and foam get cold and thirsty and absorb/adsorbs moisture from the house.....
next day....Sun comes out...heats roof assembly ...
metal roof is a vapor barrier...
moisture only has one place to go...
and is driven back into the house
course it may be something else...
I am just bringing up this possibility
Interesting point John.
I was checking out this forum entry and they are talking about radiant drive which brings vapor from outside through the ffoam into the building:
https://www.greenbuildingadvisor.com/community/forum/energy-efficiency-and-durability/15840/moisture-problem-between-roof-decking-and-ope
But you mean moisture from inside the building, right?
actually they messed up so it's 3 layers of high quality self adhesive membrane on wood planks (1920s home).
OK, BUT if moisture is stored and released, it would be released at night and sucked up during the day since temp increases dew points. Then, wouldn't the dampness occur at night instead of during the day?
Don, yes
I am saying the moisture MIGHT be coming from inside
and it may be stored and released
stored and released
Do you have Ice & Water shield ...and or is the metal vented ?
Don,
1. I don’t know what Icynene’s website says, however, the prescriptive code requires you to install R38 for CZ4, or less Rvalue on the performance code as long as you raise other energy requirements. That part has been used by the foam insulation companies to sell inferior installation to become price competitive. The fact is, just because the code allows it, it does not make it GOOD BUILDING SCIENCE.
2. If you had one done, you would know if your house was leaky and where the leaks are, and how big of holes you would need to deal with.
3. It’s got a lot to do with it. HVAC systems cool houses AND REMOVES HUMIDITY. If your HVAC system was is grossly oversized (99% of all are), it’ll short-cycle and it would not have a chance to remove humidity.
4. Providing mech. Ventilation will help you with humidity and indoor air quality.
5. Installing IAQ thermostats will control your mech. Ventilation.
6. Vaulted ceilings should have a return air at the highest point to remove hot, humid air.
My got feeling is that you have a leaky house, thru basement walls, rim joist, exterior walls, etc, PLUS your HVAC system is NOT working as it should, by design, installation or both.
There is a lot of information in this website for HVAC deisgn and moisture problems.. read on!!!
1. Icynene and their dealers sell something. I make recommendations that work to people that payment to test, not sell them something. I have no interest other than what works in this discussion.
2. Wrong Product! Open Cell on a Roof Deck - never! If the roof deck leaks, you have a sponge full of water. ANSWER! Remove and replace!
3. Buy a Bigger AC to remove Humidity! Wrong Answer! Your unit is probably too big at this time, and thus part of the problem. ANSWER: Fix other problems first. Then see about his one.
4. Ventilation Questions: I don't understand the big pipe you have disconnected! The question is, 'Do you have mechanical ventilation?" and it follows, 'Is it the right size?' Obviously you do not have this or you would have answered it. ANSWER: Get someone qualified, to figure the ventilation required by ASHRAE 62.2.2010 and get it installed.
5. You like to test. Great!!!! Keep testing or fix the problem according to the advice you have been given. All advice move is good. You don't need to test anymore.
Don - I can't tell from your description whether or not the foam is covered with drywall or some other wall/ceiling covering. There is obviously some issue with moisture penetration into your building, most likely from bulk water and/or air-driven moisture thru a leaky envelope. Since you like to test, a blower door analysis of your house seems in order.
Sounds like you live in a jungle and failed to mention an indoor pool. Your moisture is out of control high as you know. Plants, cooking, are you adding moisture? Giant fish tanks?
I take care of two homes with open cell spray foam, that need sump pumps and they are nice and dry.
Interested to here what you find out, sounds like humidity is just way too high. Also the 3 layers of high quality self adhesive membrane on wood planks (1920s home)" sounds odd.
Thank you guys for all the advice. Yes the 3 layers of underlayment were necessary because the crew first stapled the first one when everyone should know you can't. The second layer was nailed incorrectly so they put a third layer on and supposedly did that one right but I didn't inspect it at that stage anymore.
The basement and main floor have an old 2ton unit. Short cycling and oversizing I can tell you isn't an issue because the AC runs for hours now.
No moisture sources and not much cooking happening here so
I can't really tell where this much moisture is coming from.
The point is I am not sure why I put spray foam up ;-) I would have rather vented the roof but it has a complex cut and you can't vent it properly.
I would have liked using SIP but again in my area way high priced and can't afford it.
In the winter it was relatively cold up there so R20 isn't enough I agree absolutely.In the summer when its 35C on the metal roof it's 29C on the foam, so
in terms of insulation quality, it clearly sucks.
Now John you say 'wrong product', what would be the right product?
Can I take down the spray foam and put XPS between rafters, seal with spray foam from a can in-between?
Bruce, there is no drywall installed. Moisture penetration? I think so.
The plastic test shows clearly moisture coming into the house through the foam. Where that moisture comes from I don't know.
This morning the plastic is wet, the vapors condensed some time yesterday evening when it reached 99% RH....
My theory is the 10 perms are too much and the heated roof drives all the moisture through the foam into the house.
Why would the 1sq ft area encapsulated in plastic sweat within hours?
OK if moisture is coming from the house, why is there no problem at all until we reach about 25C outdoors?
How much does a blower door test cost and what answers can we expect from it?
Yes indeed I live in a jungle,..it's a big mess up there right now ;-)
Thank you for your advice everyone really appreciate it!
Don,
Your information doesn't add up: "3 layers of high quality self adhesive membrane" -- but later you say "the crew first stapled the first one when everyone should know you can't. The second layer was nailed incorrectly."
So are you talking about a self-adhesive membrane, asphalt felt, or synthetic roofing underlayment?
No matter what kind of underlayment you have, if you have roofing plus three layers of underlayment, you're not getting any exterior moisture entering your roofing assembly from above -- unless you have a roof leak and it's raining every night.
Hi Martin
it's a metal roof and the three layers of underlayment were necessary because the first two were not installed correctly. Instead of taking it off they put another one over and so on...
The roof leak is a thought that comes up all the time. It's a new roof however, standing seam.
How about this: I will take down all the foam in between two rafters and observe if there is water coming in.
Can I close it with a pink board later? Wouldn't want to hire a spray foam crew for a couple of sq ft!
Don,
I don't believe that sky radiation is contributing to the moisture in your enlcosure.
I think it may be contributing to the wild fluctuations that you are seeing in your experiment.
The crazy "cycle" that you noted.
Bill Rose Quote :"Cold materials tend to be wet and warm materials tend to be dry"
I think your roof assembly is consuming water at night(reducing RH in the air) and expelling water during the day(increasing RH in the air).
The source of the moisture is still unknown.... and could be from a variety of things.
and I agree w/ Martin....the moisture is not likely entering from above the roof
Don,
I don't think you have a roof leak. That's highly unlikely. No need to pull out any foam until you have a lot more information.
Sky radiation does cool things down, and on a clear night can cool them down below ambient. So it's definitely possible to collect water at the roof overnight and, with solar vapor drive, drive it inwards during the day. It's a mechanism that can explain most of what you have noticed, including the local absolute humidity in excess of indoor humidity. If your metal roof is shiny, this explanation doesn't hold.
One other possible effect hasn't been talked about much except over beers. A ridge is like an outside corner so it has all the peculiarities of corner geometry. Also, the ridge "sees" more of the sky than the rest of the roof does. So it would have greater heat loss to the sky than the flats of the roof. I bet you could rig up an experiment that would measure the temperature at the ridge, ideally at the underside of the deck, and compare that to a measurement under the deck at the flat and see if the ridge is colder and by how much. If the ridge is colder even by just a few degrees, then there would be a higher amount of water collection there than elsewhere.
Being pointy in nature means a higher amount of radiant exchange for the surface area. Lightning rods. Pine needles. Cacti like to chill the point and drink the dew.
Just an idea--I never measured it.
Hi Don!
At night the metal roof cools to the outside and the relative humidity and temperature remains higher within the interior space. The vapor drive is then from the inside to the outside. Moisture is diffused up from the interior space into the roofing system and spray foam insulation where it collects overnight. The moisture in the insulation and wood framing cannot dry to the outside due to the vapor retarding capabilities of the metal roof and roof underlayment system. Then when the sun shines on the roof the vapor drive is reversed and the moisture diffuses down from the insulation and wood framing into the interior space. The moisture is coming from the insulation and wood framing but it is interior moisture. This cycle will continue with high interior relative humidity in the building.
If you would like to discuss further, our Building Science team is more than happy to help you out anytime. Call 1-800-758-7325 and we can discuss one on one to help you out. Cheers.
Fantastic, I did indeed call Icynene several times as well as the insulation contractor and the roofer.
Guess what it's a blame game with me stuck in the middle.
OK so if the insulation turns into a vapor storage at night the problem would be resolved by simply running a dehumidifier at night and bring down the RH.
If the "Icynene Building Science" theory holds then during the day there should be no higher RH indoors since the dehumidifier has already sucked it all in at night. Granted some humidity generating activities indoors take place such as showers and cooking but that's it and we have AC running all day so that should take care of it.
So I'll run an expirement at night, dehumidifier maxed out, bring RH down to 40%. Next morning I'll repeat the experiment with the plastic foil at the same spot.
thank you for the suggestion, I don't want to point fingers either but the insulation sucking up so much moisture is a problem for me
Hello Icynene Building Science"
one more question. On your website it says <5% water absorption. Intersting I always heard "it won't absorb moisture" from "knowledgable" insulation people. They said it will float on water, etc.
Anyways. Check this out:
I have 170 sq meter area under the roof. Icynene LD is sprayed 6" deep, that's 15cm or 0.15 meters.
So 170 m^2 * 0.15m = 25 cubic meters of Icynene spray
Is that correct? Now 25 cubic meters * 0.05 max water absorption = 1.27 m^3 water = 1.27 tons of water.
Does this mean the Icynene in my roof can hold 1.27 metric TONS of water?
Bill Rose, thanks for your input. I have a thermal/laser thermometer with high accuracy. When I am bored I check the roof's temperature :) It's actually almost white with over 75% reflectivity I believe. It hardly gets much over ambient air temp. In the sun it may reach 47C when it's 35C outside. The neighbor's shingles are baking at 70C+ at that time. Inside the ridge is hot during the day, like 28 to 30C or so if you don't point a fan at it to bring AC air up there.
But you are right, it's worth the time to check it out at midnight and see how it cools off depending on location
Some thought about this distribing problem.
The topside of foam on the bottom of your roof deck spent the winter at outdoor temperatures, while being exposed to the mositure inside your home. There is a possibility that foam/wood deck loaded will condensation at the cold surface below the vapor barrier. Now the summer heat on the roof is driving the moisture to the cooler inside space. In other words, the wood deck/foam insulation is being dried out by the heat of the sun. Allow this happen. Next fall, you need a interior moisture barrier to prevent inside moisture from condensing on the vapor barrier on the top of the wood deck. Check with building science.com for more info.
Regards Ken
I like this last answer by Ken. Also, get the RH down in your home Don along with pointing a room fan at the wet foam. Where are you located? Wet climate? Has your spray company had problems at other homes? If not then between all of you on-site you should be able to figure this out.
Keep this thread going till all is solved. And for now as to removing foam. If never resolved maybe take out only the wet foam, let dry out and then replace with 1 or 2 pound foam.
If the foam won't dry out this summer with proper RH reduction and good air circulation to aid drying then it may be time to get the Big guys at Building Science to visit. It would make a fantastic paper to report on for all us that use spray foams and are concerned when we read about someone having a major problem like this wet foam issue.
Attaching F-C scale to aid in reading this thread...
Hey AJ thanks a lot. I already contacted the "Big Building Science" however the entry point investigation start at $2,500 so yes thinking about it but at this point I am even thinking about cutting losses and tearing everything down incl. the new metal roof.
Not because I am crazy because I am getting there ;-)
it's because nothing appears to be done right and it's frustrating.
Where are all the good builders, bring them please I am starting a new project:)
I don't like to accuse anyone but each contractor will point at some one else and it is confusing.
Like Icynene will never consider there could be something wrong with the foam, and if yes, they say if there's something wrong it's the installers fault.
I understand the concerns of installers, too.
I did the math with the perms and vapor drive entering the house. I can explain in theory and with experiments that vapor is coming from outside.
But I am not a university with a research lab to prove it and I may be wrong. I am still stuck with the problem, however.
OK so there is more info: The foam isn't wet anymore. It dried within two days. I had it covered up with XPS, pretty much sealed up well,
so well that the water only found 2-3 spots to come down initially. So in the winter we had a very good vapor barrier that's why I don't quite comprehend it's
winter moisture coming down in summer. When I took the XPS down a month ago it was a disaster. By the way, the idea with the XPS was double checked with the installer
before hand and also with BuildingScience.com
They even have an example chart with open cell foam and xps over it.
Icynene says it's wrong because there is another vapor barrier above (the roof).
But hey, then all closed cell unvented roofs would be bad too, right?
I have a feeling that a lot of the "facts" out there aren't facts at all. I.e. the guys from building science.com may be too much more like SellFoamScience.com but
again no proof don't want to argue with anyone anyways.
Then of course, everyone blames the roofer. That's why I would love to take down some foam and watch the water drip in,
at least then we know what's going on.
At this point only one thing is for certain: The foam creates such a MESS that nobody wants to deal with.
It's better you have water dripping in, trash the fiberglas or whatever and move on with your life.
Cut your losses, fix the obvious damage, etc. But what we have now is ridiculous. I can imagine that every single installation of foam under roofs will end
in the same scenario of confusion. At some point the roof leaks (or not) and homeowners don't know what's going on.
They are sold a new AC or a new roof, or whatever but nothing fixes the issue.
I thought I would get the best premium insulation and roof to avoid all this and I was wrong.
Sorry to vent but I blame the foam for at least confusing a
dozen professionals already and of course my entire family. I can't use the upper floor for 2 years now, the old roof was leaky but at least more predictable
AJ, as a builder, wouldn't such a mess sort of kill the business? Off topic but what the hell!?
Don, 23 posts and only now do I read pertanant facts. I call what you built overkill that also led to the construction of a water trap. Like a "lobster trap" little holes let in things like water or lobsters that then have a hard time getting out. As time went by you caught enough water that when you opened your homemade trap, you released your catch of water.
The sheet foam has to go.
The 3 layers ice and watershield is wrong, is overkill, massive overkill. Asking a contractor to do way too much is as bad as too little sometimes. Ie, overtighten a nut and the threads strip or the bolt snaps. I have helped many aircrafts be built and just right is right, too much is as bad as too little.
That said, I don't think the roof leaks. So leave the overbuilt roof alone. I think the humidity in your home went in past the rigid foam and couldn't get back out. It is very very hard to seal rigid foam in a build like yours, impossible really. The beauty of spray foam is that spraying it glues it tight and stops air moving water born air behind it to get trapped and cause issues not desired.
Hi Don,
your situation is difficult to "picture"
could you please post a picture of your vaulted ceiling and your experiment.
AJ and everyone else here I very much appreciate your expertise and time!
Now while I take full responsibility for the crap I built, it's my house anyways so who else to blame? :)
I think AJ's theory has some validity, naturally Icynene pointed this out to me as well.
Here's how things had progressed:
1. Spray was installed in fall, I had spent months cleaning the place it was a major renovation job
2. Around Dec I noticed R20 is crap not enough. Plus the foam smell wouldn't go away.
3. So I asked the installer how about installing XPS, he says doesn't matter what I put over it.
4. I checked BuildingScience.com and they recommend a vapor barrier XPS (!) over OCSPF in the climate zone right above us which is really only 50 miles away from here
So I thought great lets put it up, make the place warmer and get rid off the smell too
And it worked until in May the water started dripping down the ceiling after a strong thunderstorm.
NAturally everyone first pointed to the roof, which is still not clear if there's a roof leak.
The 3 underlayments happend because the roofer apparently subcontracted to someone who hires people off the street. They could have removed every layer they screwed up but it was certainly not planned that way to have 3 underlayments.
But even 1 layer is fairly heavy.
Now to cut the story short: If AJ is right, then the KEY to understanding the cause of the problem is that the foam is to blame because it absorbed so much vapor. Had we used closed cell foam this would not have occurred.
Yet another thing complicating things is that the water only came down from the top 2 or 4 ft. And two random spots at eye level where the knee walls used to be. I thought if condensation issues are to blame it should affect the bottom layers of XPS more since temp is lowest at floor level.
Another theory is vapor diffusion of vapor coming from outside. I did the math and it matches roughly the experimental measurements. However I am not a physicist so I may have screwed up. I figured that each m^2 of 6in Icynene at 10 perms can EASILY and realistically under normal conditions that we had let in 50 grams of water vapor per 24h. If you multiply the entire roof area you get about a gallon per day and more. And if you check how the RH increases inthe room during the day, it matches perfectly. AJs trap idea would make sense here too because XPS lets in 20x less per day, so only 3-5grams per m^2 per 24h. Hence we would have a problem if the vapor entering from outside is indeed the issue.
BUT I may be wrong and this is yet another waste of time calculation.....
Don. Open cell foam is open and holds water when dunked in water. XPS does not. Open cell does not smell. If it does something went wrong in installation. I have homes here sprayed with the same R value, and the homes do NOT need added insulation. Water in your home after a rainstorm. Bad roof. Sounds like you, your roofer, your insulation installer need outside expert help.
You never said location, rainforest?
You either have roof water leaks that are not from external water vapor penetration or your internal RH is high and needs mitigation.
Don - two things:
1- why is the foam not covered with drywall or other material. For one, this a code violation. For two, you still need a good air barrier to stop air driven moisture from penetrating the insulation. This is an important part of the the system.
2- You should probably remove a small are are near where the moisture is occurring. A small leak is always possible, though, as stated above, doesn't seem likely....but can't hurt to check.
-Bruce
Thank you guys for all the info. Location: MD
Interior RH is always around 50 on the main floor and basement so that shouldn't be an issue.
The drywall wasn't put up yet, no time, money and wasn't certain the job was done right. Turns out I saved myself over $5k since all the drywall would need to come down after all this water came in...
I was told I can leave it as-is with the foam in the open.
The open cell foam does smell but for that subject we need to open a new forum entry.
yes help we need indeed, soon I'll need mental help too ;-)
Bruce the idea to take down a piece makes sense. I was planning to take down all the foam between two rafters exactly where the plastic sheet test went 99% RH. It's still stuck on 99% RH several days later by the way!
the roof leak discussion is another thread on its own. The metal cap has no z closure but the roof is fairly steep. I was told it wasnt needed but the roofer will come to caulk the gaps some time dunno when...still waiting. there is a chance the 3 underlayments are all 3 screwed like swiss cheese.
i think we need to shred the foam and return it to Icynene and scrap the metal and send it back to the roofer.
"i want my money back"...put me in a time machine damn it ;-)
OK another question: if the underlayment has holes but the roof is OK, would dew or moisture come in?
The thing with smell is many people have a higher tolerance level, aka burned nose vs. dog nose.
However levels here are so high several people have gotten headaches and nausea, hence all the effort to seal it up with xps in addition to r-value.
the r20 is simply not enough here. sure you can turn up the heat to compensate for it, just like we could install a stronger hvac to suck up the moisture but honestly that goes against the entire idea of installing expensive spray foam, doesn't it? I wanted a comfortable, smell free, cold spot free home which is also efficient.....and I think more than just one thing went wrong.
If you say your foam doesn't smell, the insulation is enough, the roof shouldnt be leaking...I think I have to start from scratch again
If you accidently drop a tree on it....
Don, R 20 spray foam done well is fabulous.
Pics, post lots of pics soon.
Any good beaches nearby and I might come by to see with my own eyes what you have.
Don,
Q. "If the underlayment has holes but the roof is OK, would dew or moisture come in?"
A. No, not if you have a standing seam roof and three layers of self-adhering membrane.
Thanks Martin, the three layers have been penetrated by probably a hundred nails when a blue tarp was nailed over, before the metal was done. a tropical storm came before the metal was installed so they nailed up a tarp...I am certainthey didn't patch the holes afterwards.
So yes the other discussion is whether the lack of a z-closure under the metal cap is the problem or some caulk failure.
AJ, the R20 doing a fabulous and smell free job was what I was promised and I paid for. To give you an idea how it progressed. When the spray was done we left the house and I came in later when it was done to check. We left all windows open and left the building for a couple of days. Came back still stank, put up vents for over 30 days all open upstairs. Then it got too cold to continue venting but the smell slowed down with temp. However the smell is apparently heavy and it comes down to main floor.
In spring with hot temps the smell came back full force and worse.
One month after the spray job my retired parents came for a visit. No place to put them I cleaned out upstairs, the foam did look beatiful, granted, put mattresses in and all that.
I didn't say anything about the smell to test them! The first night they came down saying they couldn't breathe! Headaches, almost like confusion state. Naturally we cleared another bedroom downstairs and they didn't go up there until another time 2 months later.
OK, MAYBE we are a chemically sensitive bunch...or the job wasn't done right, or perhaps people who install or work with it get used to it and don't smell it anymore.
Beaches: Ocean City, MD beautifully clean and warm water, however not quite the carribean or Mediterranean experience.
Pics will follow soon
R-20 Spray Foam between the Rafters "done well"
in Climate Zone 4 is NOT-So-Fabulous
Don,
I live in a "spray foam" house myself
If I had a do-over ... I would build myself a one story house
with a vented attic
with an airtight ceiling
with Cellulose Galore on the attic floor
Don, Brooks is a hater of foam and is very good at opposing my thoughts. (Feel the love). I also am not for bad spray foam work but that said, millions of homes have been done like yours and mine successfully, no smell at all, no water problems, and performance much better than standard builder fiberglass batts.
I know R 20 works and here Brooks, actual use in zone 6. And what is your actual use in zone 4-6 are you referencimg, any?
I also have moved towards higher R values as I am a fan of passive house, PGH, cellulose, rock wool, and natural building. Robert Riversong did post here and taught all of us much about natural materials. Gone for now as he got too edgy with some of us and owners of the site. If he was back someday we all could gain from his wealth of knowledge to do with using the least amount of unnatural materials.
No one should be getting headaches from the foam. Something is up. The foam is exposed and wet.
You now add to your story about taping, nails, open ridge cover, what next?
Martin, GBA trip time, investigating this would make a good blog here and would help out Don I'm sure. Don, ask GBA down. We all would learn.
Brooks, all my love my man.
OK foam guy came today we started cutting some foam!
He liked the plastic over thermometer idea too.
To me it seems more likely than ever that the moisture is coming from outside, from the air through the foam into the house.
I used a moisture meter to check the wood planks behind the foam: 8-10% just like the ones inside the house. No difference.
The theory right now is, AJ and all others who see no issues, if you cover with drywall the drywall will simply suck it up pass it on and then the AC will be busy busy drying up the air.
If you switch off the AC then you start seeing it but in your case you would need to check behind the drywall.
I hate drywall, it's a disgusting material. When I gutted the house I can tell you there's nothing good about it other than it's cheap. Anyways it wouldn't surprise me if some materials fail in the longer term if the house isn't permanently dried mechanically. But even so the permanent moisture transfer must be putting some stress on the materials.
The conclusion for me at this point is the foam is no good for my climate/situation. The recommendations from BuildingScienceCorp don't apply. The XPS idea was from their publication and it doesn't work, worse, it creates problems.
A roof leak may still be the source and now that I have cut up a few areas I can check after a strong thunderstorm, too.
The theory that the roofing material sucks up moisture at night and releases during the day...doesn't seem to apply. The moisture meter shows no difference. The wood planks I checked were same moisture level as inside. Hence, the moisture is coming from outside.
I did the perm calculations, I figured out the water contents and RH rise, it all makes sense to me now and I am going to take down this foam most likely....
nevertheless I will do what "the foamer" suggested. isolate an area with plastic sheet and monitor RH just in case the moisture comes from somewhere downstairs.
However, my plastic test over the foam pretty much excludes this possibility. I will try his suggestion anyways and see what happens.
I think at this stage I need to collect some creative ideas of how to vent this tricky old roof...remove the foam and vent the roof properly...somehow!
John I am all for it. the next house, no stick frame but solid cement brick walls, no basement, no sump pumps, solid cement ceiling, xps over it, foil faced to reflect upwards and the attic not just vented but the wind blowing right through it. XPS exterior, stucco, paint.
Then put some nice ceramic tile on the roof and voila it's done, you got a proper house. air tight, chemical free, cheap, solid, period.
The materials are not at fault Don. They have worked great for me in a colder climate. I think the use of the materials has lead you to where you are and how you feel about them. But, you can have bad experiences with cellulose, concrete and many other materials if not used properly.
I still think you need some help, expert others to look into your situation at the site.
If you don't like drywall, don't use it. Building inspectors here want complete plans before construction starts. And then they inspect. And they want vapor barriers over spray foam. And there has to be something approved for fire stop.
Approved plans by experienced contractors are worth the cost beyond DIY contracting, of course not always. The best case is to have work done by highly repetitively experienced crews, not newbies.
And lastly, living in a concrete vault, well that's not my kind of house here though we are a heating dominated climate. Warm climates certainly can use the mass to their advantage. I hope some nice stucco finishes are to be included with all the concrete surfaces along with great tile work and more.
AJ I truly respect your opinion and expertise and appreciate how you give all of us insight into the business.
I agree and disagree, however. I agree that each material requires a unique set of skills. And each material brings its own challenges. What the average homeowner like me doesn't comprehend is the extent of all these challenges and how they work together. You can create a big mess even as a builder with good skill and intentions.
And that's where I disagree. Sure enough if you are the builder and you know compentent people you can get a house built out of any material. But then you sell it, the problems come later in every house regardless of material, and then it gets really complex especially when too many things are unknown. What's behind the wall? Noone knows until it's opened... That's what I am talking about.
If you use thermally insulating brick and stucco on both sides as my friend did in AZ, the wall is tight. You get your 10 perms natural vapor flow, not too much not too little. No potential for condensation. The XPS board goes outside with nice stucco over it. No chemicals in the house and spray foam necessary. You can't hear the other person talking upstairs or in the next room. Sure you could do that with stick frame but then you gotta bring chemicals and other nasty stuff to the interior. Then you create mold & fire potential. One thing leads to another.
You see the material dictates how things need to be done and it brings its own challenges. The stick frame construction promises low initial cost and brings a high maintenance cost. When you insulate inside you create problems, rather than solving them. Then again climate zone is also very important too and again to me that's another reason to build tight with tight and lasting materials.
The builders who built my home in 1928 knew their craft: I gutted the entire home and the only thing that survived was the original material from 1928. All 'renovations' thereafter had to be trashed. Mold everywhere and all mostly built according to building standards back in the day.
The electric wiring from 1928 is still good whereas newer cabling burned and got damaged. Wrong installations? Perhaps. Bad material: 100% I know I gutted it. Perhaps the cheap choice... In my house you can see how the last 100 years of building science progressed and how materials age
I have very high respect now for stick frame built in the 1920s! It's a master piece and will last easily another 100 years.
While I agree a good job is most likely done by a good installer, the materials play a significant role.
I am not going to buy a new stick frame house anymore. In 1928 that was good work but today it isn't. And, today we don't use the thick hard wood we used in 1920s so there is no way the new stick frame will survive as the old ones did.
Another example: if you build with wood you need to worry about rot and termites. If you build with concrete you need to worry about weathering and issues with stucco, thermal expasions, etc.
The foam guy yesterday told me he and another home owner spent 6 months investigating a similar issue like mine with moisture. They finally figured the moisture came from a cylinder block basement wall. They had sprayed over it and created the problem. Then they filled the wall with cement to avoid repeated wetting.
There you go again: hollow walls, air and water penetration.... But I blame the materials are not a good choice if experts need to spend 6 months to find the problem. That's a lot of money wasted
Don, control Rh inside your home and things should start to look up for you.
Up my way there are long time exterior rigid foam using contractors. So no foam inside. Here's one, Bruce Brownell, great guy
http://www.aaepassivesolar.com/
And Don, stick or concrete homes or many others can be built and last for decades and longer. Better days are ahead my man.
Just thought of this. Did you heat with construction heaters and or add lots of new materials during this renovation? If so there could be some of the source of added moisture. Cellar, Maryland humidity, new construction, construction heaters, humidifiers, plants, showers, Italian chefs, etc...
Keep thinking RH control not the roof or foam. Add vapor barrier paint sprayed on the dry foam.
I read Robert Riversong's entries in a couple of forums and I wish he would come back, too.
AJ thanks for the hint,about the contractor
I actually talked to a foam guy some time ago and he told me they foam roofs from the outside.
At that point I already had the new roof though..
Now, back to my experiment no 56 :)
approx 1 sq ft covered with thick plastic transparent and put a thermometer behind it.
Remember it only took 3 hours to shoot up to 99% RH at roughly 28C.
Now, this time we cut up the foam behind it and removed.
According to foam guy, foam is in perfect condition and did stick well too.
The moisture meter shows the wood is sort of wet = 15% moisture but it's dry to the touch.
This is facing north.
Then we went a couple rafters to the right, still north facing, cut out a piece that had an air bubble behind it. Deflection observable about 1/2 inch in the middle.
Obviously didn't stick well at that point. I am sure I checked the foam everywhere after installation so this wasn't there before.
I took the foam out
and put another thermometer BEHIND the foam and closed it up again.
Check out the results after a couple hours:
outdoor temp: 29C 31%RH -> 8.8gr /m^3
behind foam: 32C 62%->20gr / m^3
interior, next to it:24C 62%
-> 13.gr water per m^3
you see there's a lot of moisture BEHIND the foam (under roof).
We may argue which direction but to me it's clear: moisture goes right through the foam, too fast, too much.
today in the morning:
8:40AM
behind foam: 19C 79% RH
interior: 23C 57%
outdoors: 18C 54%
1030AM:
behind foam: 24C 72%RH
interior: 24C 52%
outdoors: 22C 41%
The pattern is under roof (behind foam) we always have more moisture than outside AND interior.
Based on the measurements the moisture is coming from behind the foam into the building.
You know, before putting this damn plastic foam up, I thought of Airkrete which I liked very much.
Especially the part that it doesn't stink or burn.
But the 10 perms appeared to be too much back then, so I went for Icynene...could have went for Airkrete, same perms same R value
no stench no burn risk and no need to cover with flame block material. But of course we don't know the details of that material either until we install it, right!?
Sure the question is still does the moisture go up there from the house and soak the wood 'wet'
or is there a minor roof leak coming from the cap down and finding its way in through the dozens of nail holes (when the blue storm tarp was installed and taken down again)
I think these numbers are hard evidence that moisture and too much of it goes right through the foam.
I wonder if there's any benefit compared to dense packed fiberglass!
And sure we'll all blame the installer. No, I am still certain on blaming the material but that's just my opinion.
Don,
It sure would be helpful if you posted some photos
It is possible that some of the moisture is "stored & released" AND that
some is coming from the "oustide".
without photos it is hard to tell...but
there may be a 3-D Network of Voids between the plank sheathing that connects to the "outdoors"
Something else that could be "contributing" ....
By doing significant air sealing at the roof and at the 2nd floor walls...
and not doing any significant air sealing in the lower half of the house...
the Neutral Pressure Plane (NPP) has moved "down" considerably
The further down the NPP moves ... the greater the pressures near the ridge and perhaps even near the 2nd floor soffitt area.
John is right.
And as to the roof, the roof membranes should have gone over the ridge. Your indoor RH is high. The moisture to me is NOT coming through 3 layers of membrane and a metal roof!! If the roof is bad, then get the roofers to replace it. But your inspections that are telling you "roof leak" are telling me "inside vapor pressure is high" either now or back when you were working on it
along with the XPS leaking warm humid air in that is now getting out.
Fans, and dehumidify and as John says hopefully you also tightened up the rest of your home completely to cellar floor level. And your cellar is dry as a bone.
Fans and dehumidify. Stop moisture entering walls, floor sills, cellar...
Old "air leaky" homes naturally vent and reduce moisture issues. Take the same home and do less than a complete well planned insulation renovation including proper ventilation and use of ERV or HRV and well it is easy to have moisture and air quality issues. This site and the internet are full of stories. And yes even the experts run into head scratchers like you may have.
Post pics. Are you working with engineered plans Don? Oh, and eventually if this all resolves, you owe a round of Sierra Nevada's.
granted, any beer you want :)
It's funny roofer called they come to caulk tomorrow morning!
Pics are on the way for sure.
John brilliant thought, haven't thought of it.
AJ , I will run again the dehu and bake the entire upper floor again. If the caulking stops moisture from coming in then we know it was a nasty 'drip under metal effect.'
Now if air infiltration is the case, wouldn't the moisture be the same as outdoors? How could it be more than outside consistently, especially when in the morning it's drier outdoors?
Don, Warm air holds more moisture. Your RH to me says you have moisture in your home coming from air leaking in from outside but not air leaking through the roof. You still haven't told us about the rest of the build and building air leaks. And now you say you aren't running the dehumidifier. I think you need dehumifying and a fan on the foam for your entire warm humid season. Yaa gotta dry out that home and seal up walls or floors or windows that are sourcing moist air.
Did they lap membranes over ridge? If they did, your caulk idea is nuts. Factory metal ridges are NOT caulked. Never. The factory ridge may have a factory seal that was forgotton. Caulk doesn't last. Seals on anything are marginal. Remember the first Space Shuttle to blow up? Seals. Ever see caulk last around a bathtub, no? Me either. Lapped over the ridge membrane will not leak.
Quality top contractors. Pictures for us.
IPA time. Good luck with the caulked roof. Keep that Idea to yourself though.
I was thinking about the gaps between planks...
that may not have been filled with foam
gaps that leave a passage to edge of the roof
Don,
In all data you've posted the interior vapor pressures are greater than the exterior vapor pressures. This seems to indicate that you are generating water somewhere in your house. Also, your RH measurement for "Behind the foam" seem suspect. Can you explain how you are measuring at that location?
The vapor pressure differential favors a migration of moisure from inside to outside in all cases but 6 inches of foam and three layers of low perm roofing paper should be significantly retarding that diffusion (even if there are nail holes through the paper).
But, there's a lot of posts here and I might have missed something..
Foster, there are a few dozen posts that say the interior moisture is too high.
John & AJ thank you so much for keeping the ball rolling.
I don't understand 2 things, please clarify:
1. how can infiltration of air from outside gather at the top of my celing at 99% RH? I think of it this way: I open the window: boom there's the infiltration, and leave it open say on first floor. Then moisture will eventually go up. But it can't reach, in my opinion, a 90+% RH and an absolute moisture content that's higher than outside for prolonged periods can it?
2. how was the vapor pressure greater indoors when the readings "behind the foam" (Thermometer stuck behind the foam where we found a small void) have higher absolute moisture levels than interior and outdoor measurements
Agree caulk is crap most of the time. A roof should rely on sealants at all. Yes they did wrap the underlayment over the ridge but remember the blue storm tarp was nailed all over the place, especially at the top. The tarp was torn by the end of the storm, water had gathered I am telling you like half a swimming pool where the tarp fold hanging down on side of building. Had to cut into it to let the water out, felt like being in FL that day ;)
John the planks being space so far apart is apoint of concern for me, too. I don't buy the idea that the underlayments and roof form an air tight seal onthe house because they don't. You could smell fresh air up there for a while (and of course the rubbery smell of the underlayment). Wasn't 'windy' up there but for sure good air circulation before foam went up.
Anyways today I'll be posting pics and I'll send you beers let me know your address!
Don,
Since you like experiments
You will probably like this Bill Rose book (if you don't own it already)
http://www.amazon.com/Water-Buildings-Architects-Guide-Moisture/dp/0471468509#reader_0471468509
there is an interesting discussion and "experiment" on page 85 concerning the storage of heat & moisture
I will try to describe the experiment later
I question your comment about infiltration.
I believe.....
If you open a window on the first floor of an airconditioned home...
and it is hot outside....
There is a good chance that air will not "infiltrate" thru the low window.
I think it is more likely that the house air will Spill Out of the lower level window...
and that Air will infiltrate thru "openings" above the Neutral Pressure Plane (NPP)
the further the "openings" are above the NPP...
the greater the pressure
John now that's a valuable reference indeed! What's on pg. 85?
If the planks end open at the Gables, they need to be sealed shut for sure!!
And keep the dehumidifier running at least a few hours daily all summer.
John, take over!!
Don, I may have missed it, but did you ever clarify what type of membrane is on the roof? Is it self-adhering membrane, or tar paper, or a synthetic (non-sticky) underlayment such as Rooftopguard or Titanium? Does the underlayment wrap over the ridge?
You have interior moisture issues, not enough insulation, and the wrong type of insulation, but I have a feeling your ridge is leaking.
Michael, it's a self-adhering high temp underlayment made for metal roof, Sentrigard ht-sa with a cool roman head logo in blue and a white background.
AJ./John how to seal the gable end planks? I don't think this was ever done for sure since I gutted the entire floor. The spray guys closed the gable vent with foam board and then sprayed over it, in case you mean the vents.
The planks reach out probably 16 in or more past the wall and there's aluminum flashing & siding so I can't tell
Now check this out.. The roofer guy came and said there was only one time his company sent him to seal the metal cap with caulk from underneath near a coastal area. They, too, had wind driven rain coming in under the cap. Now that's the clue I was looking for since a lot of people kept telling me it's 'very unlikely' to happen....
Michael I do agree wrong and not enough insulation and likely water penetrated from outside, hence the higher moisture readings behind the spray foam.
Don, does the Sentriguard wrap over the ridge? We build and renovate a lot of coastal homes, and wind-blown rain is a huge problem.
I think what AJ meant by "gable-end planks" is the end grain of the roof sheathing boards. Are they exposed? What is on the underside of the rake overhangs?
Don said they wrapped the membranes and said they put on the membranes 3 times due to errors and tarps.
Don, tarps?? Why tarp a roof covered in membrane??? Time for some good contractors to move your way. Are you using lowest cost contractors?
How are the walls and floor and cellar sealed and insulated?
As to John' s board gap, have the insulators seal that gap at the gable wall either inside or outside for access. Should be an easy job.
Don, before you caulk, take off a section and see if the membrane is perfectly applied over the ridge. If it is, good, then do whatever coastal caulking is working and approved, etc. And as to coastal, Michael Maines is your expert.
My "gap in the plank" concept is a stretch
I was just trying to noodle how air "might" get past 3 layers of peel & stick
I will describe "Page 85 experiment" after Don Posts photos
OK guys I know no one likes suspesion I am in the process of getting the pics sorted out.
In the meantime I did another experiment, bored as I am:
I took a half-fist size Icynene light density piece, less than 3 inches long less than 2 inch high, weight came up 0g so I assume it's less than 1g. Put it on water, it floats, back on the scale (but I waited for the water to stop dripping): scale shows now 2g!
So then I went ahead and immersed it in water for a couple of seconds. Took it out and waited for water to stop dripping. Back to the scale: 16 grams!
And its surface started to feel like the wet areas I had at the top of my cathedral ceiling.
I find it amazing how Icynene says on their website "water absorption less than 5%" when it's clearly a lot more like 1/3rd. Even by volume rather than weight it's way more.
I found an older test result here http://www.tailoredfoaminc.com/technical-data/data-files/icynene-ld-c-50/icynene-ld-c-50-test-results.pdf
and they said in 1988 the water absorption is 34%, closer to my experimental values.
Well, wet fiberglass isn't nice to have either but I had different expectations when I read >5% water absorption on the website.
Especially if it were really true it's only 5%, the water would have come down dripping. Instead the foam absorbed it very much like a kitchen sponge.
Actually you can squeeze the water out of the foam, just like a sponge. So if anyone had to know whether Icynene open cell absorbs water, the answer is clear: like a sponge and it keeps it in like a sponge, too. In contact with roofing materials this means prolonged high moisture contact....as the case with my ceiling. The ridge was fully saturated with water, when lightly pushed water started running down my finger
I do have a milligram scale as well, If anyone needs precise numbers I can repeat the experiment with a nicely measured and cut cube and milligram precision.
Gee
it sounds like Riversong knew what he was talking about
There you go, told ya. Riversong needs to come back! The guy is right and the foam is crap, and I'll prove it.
I plan a new experiment by the way.
I got these souvenir German beer mugs 1 liter, perfect. I'll put a thermometer in it and place it upside down on top of 6" Icynene which sits in warm 40C (underside of my roof avg.) water.
I bet the vapor will move right through it and shoot the RH to 90+% within hours.
Then we'll figure out how many perms it really has based on the RH rise and time interval. Nice physics experiment for me who never had a clue about freaking physics. But now it's about cash so now I am interested!
Bets, anyone ;-) welcome to Spray-foam-vegas! (^_^)
Hey I figured if I trash $5k worth of insulation, might as well have some fun with a couple of learning exercises right!? Perhaps I can change someone else's mind about the foam to get the facts straight before hiring someone. Too bad I can't take a pic of the smell it has to prove it to you guys, trust me you would not let your children go up there with the XPS removed, it's that bad.
And, at least now the roof has been sealed up nicely by the roofer, I am a chicken scared of heights otherwise would have done it myself long time ago... Hence now we can exclude future roof leaks from the equation
Just came across this discussion – sounds like it belongs in one of Aesop’s fables under the title of “house as system” with some cheesy moral at the end… Pardon the analogy, but like the blind men in the fable about the elephant, each of us has been grabbing a different part of this beast and come to some conclusions about what’s going on here. Don, having dealt with spray foam issues in an old house myself, I can relate to your frustration.
I’d tend agree with John, AJ and others who suspect the low-density spray foam has been soaking up moisture primarily from interior vapor movement, and it sounds like several different unrelated conditions may be at work here and bringing moisture from multiple sources, maybe over several months? But before you go and trash $5K of insulation, maybe there are other options.
Key observations and comments so far:
- It’s a 1920 wood framed house, so board sheathing and old age start you off with a pretty open, drafty envelope that has been drying out fine on its own but at the expense of your heating bill;
- Even with the dehumidifying effect of air conditioning, you could still have internal moisture building up from cooking, gas appliances, people, wet dogs, showers, laundry, dryer vents, etc. especially in the winter and spring;
- From the storm and hasty tarp incident during roof install, you might have gotten some water entering through nail holes;
- Since you’ve raised some questions about whether you had a top-notch roof installation, there’s the possibility of other leaks at the ridge or other connections with valleys, dormers, chimneys, plumbing vents, etc. where additional moisture could enter;
- John’s hypothesis of any roof sheathing boards wicking in moisture from any ends exposed to the outside air is worth exploring;
- It sounds like the exterior walls aren’t well insulated or air sealed; a blower door test would help evaluate that and locate where air is entering or moving, and possibly transporting moisture;
- Similar to how water moves through a sponge, I imagine moisture could move over time within the insulation if it has gotten wet, so it might not end up where it started;
- Seasonal changes, temperature gradients, hot moist air rising, an impervious roof, all might contribute to the moisture migrating up toward the roof ridge;
- The sun on the roof may then be accelerating the moisture movement, but maybe it just needs a way to dry out. If you can get it dry, then you can take the steps to keep it dry….
(There are some discussions in other GBA posts about the odor from your spray foam installation – one theory is that if the mix of A and B parts is off you can get a “sweet ammonia smell” from too much catalyst in the mix that didn’t react during the install. That smell can linger for a long time (some cases more than a year in a stuffy, unventilated attic) and may eventually get to a low level that you notice less or not at all. Maybe it's better to expose the foam to air it out?)
In principle, I think it’s less a question of which is the right or wrong building material to use, but more a question of how they all interact and respond to changes, flaws, errors, etc. and whether the people working on each part of the system fully understand how their part interacts with all the others. Easier said than done, I know.
To help figure out a course of action here we might look for ways to assess where the water/moisture is, perhaps with a moisture meter inserted into the foam across a grid of chalk lines and at different depths? Then we could examine all the possible places it might have come from, whether by drip, vapor drive, vent, heat, wind, rain, evaporation, condensation, etc. over the course of the last year… hard to do without some boots on the ground. That might uncover some other mystery problem to fix, or narrow down the possible sources.
As for possible solutions, do you think it’s possible to airing out the insulation Is there a way to make a temporary “ceiling” of plastic or OSB and then open up the ends of this “attic” and cross ventilate with fans or window air conditioners? OK, I’ve rambled on too long already.
Don, clearly the Icynene is NOT the problem. The construction plan IS the problem!! Proper use and application of Icynene is the missing link. You still keep looking for a fall guy, but no pics and no details of the rest of your air sealing and insulation. And your install is not legal or to code. Vapor barrier and fire stop are required. And what about ventilation, ASHRAE 62.2? Hire a GC. DIY is a fail.
Not sure I can add much to long discussion but a couple of thoughts...
1. You have to determine the source of moisture before anything else. All else is moot until that is determned.
I tend to agree with the thoughts that it is interior loads and not a leaky roof.
2. Icynene is not the problem. However, if it is still as smelly as you say. Then there could be a chance that it is a bad insulation job, as has been noted.
We have used open cell in walls, ceilings and roofs for years in all types of houses (old, new, complex, simple) with lots of success. We have used closed cell foam in walls, roofs and ceilings for years in all types of houses with lots of success. We have used cellulose in walls, ceilings and roofs for years with success.
My own house is 2x8 rafters w/ dense packed cellulose and 2" of unfaced xps on the interior side (not allowed by code now). The xps was painted w/ intumescent paint and all seams sealed with tape. It is a pretty simple roof, so it was easy to get a good air barrier on the underside of the rafters. While the xps isn't great from a drying potential standpoint, there is enough that we get some drying to the interior in the summer. It has performed fine in a house that hovers around 50% RH.
I do think your situation seemed to scream for closed cell foam (limited rafter depth, unvented assembly, no drying potential to the exterior). Not sure why it wasn't offered as an option from the insulation contractor.
Find the source of the moisture first...all else will fall into place.
Don,
I just came across this thread and have read everything with great interest.
We are spray foam installers in zone 5 and as such compete with Icynene on a regular basis. I believe that it is a fine product and when installed correctly, it has very little smell. The odor you describe points to an off-ratio application. Unfortunately, Icynene are long term proponents of the 'R-20 is all you need' argument which damages the credibility of our industry. That said, I agree completely with A.J. that it can work very well.
As you describe your roof assembly, it is pretty clear that you have a complete and total exterior vapor barrier. Given your high indoor humidity, open cell foam was the wrong choice for you. A semi-closed cell or closed cell foam would have provided the vapor control that you need but if you can get your humidity level under control, you may find that your issues will go away.
The Icynene was installed my qualified, licensed, and trained installers according to manufacturer specifications. The barrels had Icynene stickers on them, so they appeared definitely to be authentic.
Why would I blame the installer? I have no reason to blame the installation because there is no proof they messed up. I blame the material because the installer did apparently follow the instructions. And btw this is not about Icynene. I had another crew do another closed cell foam (BASF) elsewhere. It stank too, that's why I initially tended to blame the installation. But now after two different installers and two different foams I conclude it's likely not the installer's fault but rather the material. AJ perhaps in your climate it's not as hot and it won't smell much
Don,
The Pics your sorting out don't need to be magazine quality.
Snapshots would be fine.
It is very simple to post photos here at GBA
When Icynene was brought to market, I wondered what it was for?
Why would anyone market an open cell (insulation?)
What would it be used for?
Well not in a situation where the water vapor cannot pass through?
Water vapor has very tiny molecule, far small than air, it can pass through many things used in building, but not steel sheet.
Water vapor always moves towards cold.
Water vapor in cold climates, is always created by people, cooking, washing, breathing, sweating.
In warm or hot climates, where air conditioning is used, it often arrives from outside, but not always.
You have a situation where during the day the roof and the roof insulation is very hot and the water vapor is forced out.
At night the roof is cold in comparison to the room below and the water vapor moves in.
Had you used a closed cell insulation, Styrofoam perhaps, you would have avoided this problem.
Do keep in mind that some 12.5% plus, of your home is in direct contact with the cold air inside and the hot air outside, conduction being an important fact in heat gain, you really need to insulate the frame as well.
Hi Roger,
Water Molecules are indeed very,very,very small.
But so are the other molecules that make up "Air"
Quoting good ole Riversong:
"You might think that anything that would stop an O2 or N molecule would surely stop an H2O molecule, but it's not simply the size of the particles.
The primary difference is in the driving force. Air moves by pressure differentials. A blower door tests a house for leaks at 75 pascals of pressure difference, which is the equivalent of a 30 mph wind on all house surfaces simultaneously. In normal winter operation, a house might experience a 5 pascal pressure due to the stack effect, which is just 1/10 pound per square foot pressure.
On the other hand, water vapor diffuses by vapor pressure differential. With the indoor air at 68° and 40% relative humidity, and the outside air at 30° and 90% relative humidity, the vapor pressure differential is 425 pascals, more than 85 times as much driving force as experienced by the air. If the indoor humidity rises to 50% at the same outside conditions, the vapor pressure increases by 55% to 660 pascals.
So, a material like conventional drywall can easily stop air flow, even with a 30 mph wind, while being unable to resist water vapor flow very well at nearly 6 times the pressure. That's also how a Goretex jacket can keep the wind and rain out while letting your insensible perspiration (water vapor) diffuse to the outside.
In addition, water moves by capillary suction due to its extraordinarily high surface tension (with pressures 1,000 times as much as diffusion pressures), and by osmotic pressure (with pressures 10,000 times as much as diffusion pressures)."
taken from this thread
https://www.greenbuildingadvisor.com/community/forum/energy-efficiency-and-durability/15776/vapor-flow-light-frame-construction?page=1
John Riversong is a guru.
Probably the spray foam mafia killed him that's why he won't be coming back :)
Roger, vapor moves from high to low pressure and that even works from cold to hot. Actually vapor temperature is irrelevant, it's the pressure differential that counts.
Here are two awesome resources I use all the time:
http://www.conservationphysics.org/atmcalc/atmocalc.php
http://www.numericana.com/answer/gas.htm#perm
Btw, that's why I now bite my tongue when a HVAC guy or a roofer tells me "condensation occurs when hot meets cold"....no man it's not so easy....actually it's freaking complex :)
Don, you bought the foam, but you didn't have a plan, and didn't complete the job. Pictures and all the rest of your homes insulation and air sealing details or admit this is all caused by your lack of plan and lack of completion.
Icynene works for thousands of installs. At my places you can bury your nose in the foam and there is no smell, no moisture.
The mistakes are particular to your project.
Dehumidify and properly complete to code your home. Hire an expert for a rebuild plan or drop a tree on it.
Don,
You wrote "Actually vapor temperature is irrelevant" and also "actually it's freaking complex". The second quote is true. The first, not so much.
Diffusion is "caused" by a force known as chemical potential. Chemical potential is a function of pressure, temperature, molar concentration and other things. Temperature may be less significant but it is not irrelevant. There are any number of industrial chemical separation processes that take advantage of this phenomenon called thermophoresis (aka, the Ludwig-Soret effect).
FYI, I have the word "caused" in quotes because it is not strictly accurate. The reality is that diffusion happens, in the same way that cannon balls fall when dropped off the Leaning Tower of Pisa, and "chemical potential" is our best explaination for it, just as gravity is our best explaination for the falling cannon ball.
AJ is giving you good advice.
AJ you can bury your nose in my foam as well and you won't smell it. You need an outdoor temp above 80F and switch off ventilation inside the room. Wait an hour or two and then it's potent enough for almost everyone to smell it. The odor travels down first so at the stairs before you go up it's strongest at first then it covers the entire upper floor.
Now back to the relevance of temperature. According to this guy here http://www.numericana.com/answer/gas.htm#perm
"The value of a perm in SI units does not depend on temperature ! Please ignore all those well-meaning Internet sources...."
And he explains that vapor pressure differentials cause the vapor to move through materials. I found the table most useful, because it shows the actual water content in gram for an example vapor pressure differential of 2300 Pa.
AJ, no blame games here. I am well aware it's my house but I don't see why the homeowner is liable for some contractors who apparently did it all wrong here. If all your installs are fine then we must be having a major screw up here. I hope someone can spot the actual problem beyond speculation-level based on the pics which are about to follow in an hour
THANK YOU for being patient!
Pictures attached as PDF! Thank you for your time and advice!
Back to this logic I keep hearing a lot. "Icynene works for thousands of homes"
You know there are a lot of people taking medication X and no other medications and
no other conditions.
Then they suddenly die from a stroke. Does it mean the medication is at fault?
Does it mean the patient would have died anyways?
Could it be the medication made it more likely to have a stroke?
Is every stroke reported to the pharmaceutical company and the FDA so that someone can investigate
for a possible connection between the two?
Sure the doctor will tell you, "this pill works for thousands of patients".
Does that mean it will work for you without side effects?
Icynene may not stink in your home because perhaps:
* you can't smell it anyways
* you can't smell it until it reaches a much higher level than other people
* the installers didn't mix it well
* the company shipped defect material
* the environment wasn't right, RH whatever
* the house has some weird reaction against the foam
* whatever you can imagine.
Whenever a product has no many potential points of failure I see the risk is high and hence
the product is crap. If it takes 10 people with PHDs to install insulation properly, we got a problem! I wouldn't take medication with so many potential problems either.
Again, the installers were licensed and properly trained. They certainly worked professionally and knew what they were doing from what I could tell at least.
Perhaps in the homes you build it smells, too, but you can't smell it and the people
who live in it don't tell you?
Perhaps they get now more migranes than before and other allergies. Did you ever ask them?
Perhaps their doc has no idea about chemicals in the house and prescribes them some medication
when it's actually their home/foam environment making them sick.
Perhaps! Perhaps!
I know that MY installation is definitely problematic. I don't know why and I was hoping someone could help. I do get headaches from it, too.
There are no trees to drop on the house unfortunately so I gotta fix it!
Thank you!
Thank you for helping me and I sincerely hope this info will help others avoid or solve their problems, too.
one more thing, in the pdf you'll see the chart from the "Building Science Gods" clearly RECOMMENDING XPS over open cell foam, that's what I did. This was DIY, granted, but I researched it very well before I even put the roof up. yet, evidently, I must have missed something
1" XPS is supposed to allow some drying to the interior, but in reality it does not allow much drying.
I'm not a foam expert but to me the lack of adhesion and the smell indicate improperly mixed product. Trained professional installers screw up sometimes. Or the product itself is bad.
In addition to excessive indoor humidity, I still think you might have some sort of roof leak. We recently had a comparable situation which turned out to be leaking windows.
ok here some unscientific kitchen results.
Weigh foam at start: 18 grams.
Hold over boiling water vapor for a few minutes;
Weigh again: 22 grams
Sure, it's biased unscientific etc. But shows that foam does indeed absorb and hold vapor moisture. There was no direct water contact.the foam did start feeling moist like upstairs
Don, thanks for posting the PDF
here is a brief description of (Water in Buildings) "Page 85 Experiment" you asked about
"Empty jar and jar with {small chunk of} wood are brought to equilibrium.
Lids are tightly closed.......
Upon heating, the relative humidity in the empty jar is lowered.,
while the relative humidity in the jar with wood is slightly raised."
the illustration shows both jars starting at 50% RH
after heating .....
the "empty" jar shows 20% RH (as might be expected)
the jar with wood shows 51%RH (not-so-intuitive)
To me this experiment shows that the Absolute Humidity is rising in the jar (with wood) as the wood is heated.
To me it would follow that if the wood were cooled ...it would adsorb/absorb water from the air and the Absolute Humidity in the jar would go down.
I think this may explain "part" of the wild fluctuations you observed
John that's interesting. OK do you think the foam would absorb by the same principle when cooled rather than when heated?
Check out Riversong's second or third comment here on solar vapor drive:
https://www.greenbuildingadvisor.com/community/forum/general-questions/17488/high-humidity-issues-spray-foam-attic
In your photos I "see" 3-D networks of voids on both sides of the sprayfoam
not the "compact assembly" as illustrated by BSC
it reminds me of "AutoCad 2x4's"
the kind that look perfect in the drawings...but
in reality ... they are not-so-perfect
@ post 87
Yes
I think the fluctuations could be a combination of foam & wood
sorbing and desorbing
you have a lot of wood that is connected to the 3-D networks of voids
lots of thermal bridges and "Cold Edge Effect"
and perhaps even "Corner Effects" that Bill Rose mentioned earlier
BTW you should buy Bill's Book just to read about "Cold Edge Effect"
OK, I am not a roofer
but looking at 3 layers of Peel & stick
hard to imagine large quantities of "Rain" getting in
Don, you seem to associate the big water event with the springtime storm
I have noticed after springtime storms ...Absolute humidity goes way up and...
It is not really hot enough for AC to run much if any
my not-so-leaky house becomes very humid ... and I have to run a dehumidifier
Don, starting fresh now with your pictures, thank you for posting!
1-the roof is bullet proof.
2-the moisture is coming from nature, the outside but NOT via the roof.
3-the spray foam install; factory materials are not at issue. And mix looks good. My aha moment, the TSP and mold, and moisture levels. Something there messed with foam gluing to frame.
4-BSC doc; just like John said, perfect in CAD, horrendous lobster and water vapor trapping device in reality!! Why? Just look at all the infusion points where you end your foam overlay Don. Would be no problem in Phoenix, but humid Md a disaster not waiting, to happen.
5-uncontrolled humidity; old leaky home with leak proof (on two sides) sponge for a roof. Your walls and foundation and open porch floor and windows and doors are bringing in moisture. That moisture got trapped. Taking down the XPS has greatly opened the trap.
So what to do Don. Next post.
Lessons;
1-Mold cleaning prior to spray foam. Use the dry ice blasting method. No water and no TSP residue.
2-Never build lobster traps except for catching lobsters. Open cell foam needs to be able to dry well in all directions is best. Closed cell does not.
3-Foam, the most forgiving foam is rigid foam exterior with a great rainscreen. Open cell foam applied to all six sides of a new construction project done by very experienced crews during FAVORABLE weather does a good job, better than basic batts, but batts are now able to perform well in six side sealed stud walls
4-Permeability; is hugely key to any design or renovation today. Huge! The simple answer is to Not experiment! Build exactly what works where you live with the best.
Thank you very much, finally some direct answers!
Great so we all agree OCSPF is a "sponge" and the BSC recommendation also crap as proven 'by learning by doing', what's next?
I was thinking to take down the spray and cut XPS to size, squeeze between rafters, spray around perimeter with can, use 2 layers =R20. That way we won't have a sponge since XPS doesn't absorb much and the smell will hopefully be gone. I'll end up again with huge bags of trash but at least this time they aren't soaked and moldy! If I can save the XPS it would help, too.
The XPS between rafters was actually my initial idea before the spray foam idea came up but I was concerned about the air gap between xps and roof deck and the 0.5 perms being too low. But if I spray it well enough, should be fine right?
Would that work based on your experience, AJ, John, and everyone?
New plan, version 1.0 (update as we all ponder this)
1- First and foremost, finish reducing permeance of your home. Also bite the bullet and set up dehumidifier on auto with permanent drain, etc.
2-Don't put XPS in rafters. Your roof is too low perm for such. You would be creating lobster traps again but more! Use it outside your frame somewhere or sell it.
3-Existing foam; decide about smell, is covering it going to be OK or are you now sensitized to it? I would remove foam from cathedral section, dry ice clean, and spray closed cell just there then put up drywall and latex paint the drywall, no recessed lights, etc. And then leave the rest, spray it with vapor barrier paint. And put up the rest of the rooms drywall, painted, sealed electric boxes. This all should with other steps solve all. The closed cell has to be sprayed in lifts to cure without overheating. Experts only! It will give you twice the R.
Option 2, remove roof, add proper exterior rigid foam roof. Remove all interior foam and clean all. Massive expense.
Option 3, plant a Weeping Willow, water well, in five years cut tree down in favorable wind.
Best option, IMO, option one and if foam has sensitized you, sell, as it may just be you at that point. Any of us can acquire such a sensitivity with over exposure to for example epoxy. Happens. Forward motion=sell the problem.
And Don, as to "finally", if pics and details were all in your first post, this might of wrapped up in 10 instead of 90 posts. ;)
I have time this fall if you need an IPA enthusiast to drop by and observe all the redo fun. I'll even bring my own Adirondack lawn chair.
Not sure you have any answers
just speculation
I would not take it all down so fast
I am not sure that your XPS between rafters solution would have been much better
maybe you should Hire Bill Rose
ok the tree idea sounds reasonable:) thank you for your patience!
I took down a couple more spots and I think the foam didn't stick anywhere properly, not even to itself. The new spots I checked where sprayed in two layers and you can easily separate the two.
The 'hair' on the exterior end of the foam clearly shows that the some foam did stick on the rather dirty roof deck but the mass separated and moved with gravity before it fully cured. I have seen this 'hair' effect with spray from the can, too.
0. Who's Bill Rose?
1. now, why would xps create a problem but closed cell spray wouldn't?
2. is there any way to leave the roof as-is and insulate *without * a spray? There has to be something else we could do!
Let's both sit out there by the pool with the lawn chair and watch them do this :)
http://www.youtube.com/watch?v=nPxg9IlYnWg
Hello Don,
You have a few installation problems that could be easily remedied, but no material defects. Blaming materials is like blaming the other contractors on a job; unprofessional.
1. The gable ends are not sealed. This becomes a problem with a boxed soffitt, because the air can travel up the soffit and then enter in the gaps between boards. That is why it manifests at the top, because the warmest most moisture laden air is rising up the soffit and then entering near the ridge.
2. Everything on a metal roof is screwed down through the membrane. This is generally not a problem, but if there is a leak it can be. Your leak is probably at the ridge, because you do need either a z-closure or the roofer could choose to turn up the top of the panel instead. This is especially important when the ridge terminates into another roof plane as yours does. I have seen plenty of roofs leak here when there is no z-closure and the roofer didn't overlap the valleys.
3. You must get an infiltration test. I do these for $100. Don't ask for an energy audit, just test for air leakage and scan with IR.
I am sorry to be so terse, but I gotta get back to work.
Bill Rose is William Rose
http://www.amazon.com/Water-Buildings-Architects-Guide-Moisture/dp/0471468509#reader_0471468509
I believe that XPS between rafters might still leave you with a 3D network of voids
the Open Cell is not the only sponge.....you also have a lot of wood up there
Bill Bradbury thanks for the input. I had exactly the same thought this morning, air must be moving up from the soffit! Because at the top it's not only hot but now that there's a hole in the foam, there appears to be air coming out of the hole.
John, the XPS would leave an entire 1"+ gap behind it but if air can escape sideways wouldn't that be enough? If we install closed cell we basically put plastic over the wood 'sponge'....wouldn't that create the same issues as we have now? The fallacy was 'open cell' would help us in case of a roof leak, I guess it doesn't because it buffers too much water.
The theory I had this morning was: warm outdoor air enters at the soffit and moves up and gets stuck. Then at night the roof temp drops sharply below dew temp and open cell (+ wood) suck up the condensation. This cycle repeats day after day until the open cell is saturated.
This theory would explain why we saw the plastic condense when I taped it against the foam.
If we replace the open cell with XPS, the water would run down to the soffit where the air entered initially. There are of course a couple of rafters that don't end down at the soffit but at the valleys instead, not sure what to do about those....
OK one more theory:
how about we create a new envelope out of XPS. I trash all the foam and open the soffits. Because there is no ridge vent I create a box at the top and open a vent at the wall instead. We basically build a pseudo-vented roof. Take the air from soffits all the way up into an insulated cavity leading to the exterior wall. Better than nothing and cheaper than tearing up the roof.
The problem with the home's cut is you can't easily vent the roof, I had more than a dozen roofers look at the roof before re-roofing and no one could come up with a ventilation plan.
Hence the idea new interior envelope that's at least most of it vented
...
Hey "Finally some direct answers" was ment to be a joke, sorry if it was offensive!
Michael the roof is unvented there is no ridge vent. I was planning to do the XPS to avoid spray and it's potential smell. I am well aware it's going to be a nightmare effort hence I want to be certain it will work summer & winter without causing more problems.
Because it's an unvented roof, I am surprised you recommend fiberglass. Can we use fiberglass in my situation?
The separation of the Foam from the roof deck is pretty shocking
There probably are tens of thousands of roofs with no problems.....
and probably lots of roofs with unseen problems that have not revealed themselves
YET
I sure think the Humble Vented Attic looks better every day
Don, I am adding your thread to my
Bulletin Board of Enclosure Failures
http://pinterest.com/johnkbrooks/enclosure-failures/
exactly, you can't tell it's off the deck until you randomly cut out a box and it slides right out.Blame the clean up,the material, blame whatever you want, but for sure I need to take it down .
Great my house is now listed in building failure databases, well it's fun at least.
So, if people tell me they don't have problems with their spray foam, I should say...."wait and see".....but you may be lucky and it's fine :) Hey AJ is right, sell the problem
Open cell doesn't stick well to itself, just kind of is there, doesn't concern me. Always try to spray it in single lifts.
If much of your foam is not stuck to roof that is no good. You and spray contractor have to figure something like I mentioned before contributed to that.
Anyway, solutions. XPS is down, humidifier on, foam dry? Then to me you could call it and be done. Make sure to seal the board gaps at the gables. And spray proper perm paint on foam. Check for more loose foam, remove and reapply properly. Call for that $100 inspection. Plant the tree, won't be ready to drop ever if you don't plant it.
Don, lots to learn on the other thread John dug up...
60. Helpful?
1
+Vote up!-Vote down!Robert Hronek:
I think RH over 50% could lead to mold problems in the long run.
Indoor humidity levels during the heating season greater than 40% can cause sufficient vapor diffusion and air-borne moisture transport to create a potential for condensation within the thermal/structural envelope and consequent mold or rot.
But it requires a constant 80% RH to create surface mold conditions, and 90%-95% RH to sustain conditions conducive to decay organism growth.
Answered by Riversong
Posted Wed, 08/25/2010 - 19:51
--------------------------------------------------------------------------------
59. Helpful?
1
+Vote up!-Vote down!John,
Since most bulk water from a rain event rolls off a roof (that's what it's designed for, after all), I would think that a morning dew would wet a shingled roof just as much as a rainstorm. In fact, the saturated morning air would penetrate the layered shingles more than a surface rain.
Answered by Riversong
Posted Wed, 08/25/2010 - 19:45
--------------------------------------------------------------------------------
58. Helpful?
1
+Vote up!-Vote down!Oh, yeah...
I visualize a litre to be about the size of a litre of Dr Pepper
A liter is actually about the size of a liter of Coke or Pepsi or Sprite, not Dr. Pepper, Sarsparilla or Moxie.
Answered by Riversong
Posted Wed, 08/25/2010 - 19:43
--------------------------------------------------------------------------------
57. Helpful?
1
+Vote up!-Vote down!Robert,
When I read about solar vapor drive with Brick veneer.. the examples are always after a rain event.
How about Solar Vapor Drive thru roofs?
Is the extra moisture from "morning roof" alone enough to contribute to Significant Vapor Drive?
Or does it take a rain event for significant vapor drive?
Answered by John Brooks
Posted Wed, 08/25/2010 - 19:13
--------------------------------------------------------------------------------
56. Helpful?
1
+Vote up!-Vote down!ROBERT HRONEK,
I've never seen any code or engineering standard for "maximum insulation". It's more a cost-benefit issue. The ideal insulation would be of infinite R-value.
Sandwiching any wooden or cellulosic material between to layers of relatively impermeable insulation or other materials (like a roof-top vapor barrier) is asking for trouble, not preventing it.
And we've had "rainscreen" roofs for decades - they're called vented roofs. Most roofing materials, except wood shakes or thatch (or any other natural material) do not need an air gap under them - they are designed to be water-proof or water-resistant. A vented roof, however, allows drying of moisture penetrating from either above or below and is the most reliable method of creating a durable roof assembly.
Answered by Riversong
Posted Wed, 08/25/2010 - 18:48
--------------------------------------------------------------------------------
55. Helpful?
1
+Vote up!-Vote down!John,
Was that you narrating the cat herding video?
You must have a different Joe-Math down there - not the same as Joe (Pi) Bartok, who can heard cats with the best of them:
http://geocities.ws/web_sketches/
And, I didn't think you had square meters in Texas. I thought it's all big pointy feet and tall hats.
Vapor diffusion is slow in Vermont, but real fast under the Texas sun. Actually, it's slow when driven by vapor pressure, but pretty speedy when solar powered since it's an energy-dependent process. And you're right that anything hygroscopic will suck up moisture and then release it to the air when heated.
Answered by Riversong
Posted Wed, 08/25/2010 - 18:41
--------------------------------------------------------------------------------
54. Helpful?
0
+Vote up!-Vote down!I finished reading page 2 of the responses. I think RH over 50% could lead to mold problems in the long run. You have some choice on contrilling the humidty. Get better air circulation be attic and living areas or run a humidifier.
I would say that your attic is under insualted. Because of that you fear providing more air flow between the living space and the attic.
I have heard the argument that open cell will show the roof leaks. I take the view that most roofs are going to leak and that many of the leaks start out very small. To me the insulation may slow drying and lead to greater damage. Damaged roof decking is going to be more diffiult to replace as the insualtion will be attached.
It is my personal opinion but I do not like the idea of insulating the inside of the roof deck unless the outside is also insulated and a more weather resistent roof is installed. There is movement to going to rain screen walls as this will allow drying of clading and draininage of bulk water that gets behind it. I think a similar approach should be taken with a roof. The building science guys have shown in thier paper "mind the gap" that small gaps can accomlish a lot. Double layer of house wraps, light scoring of the back of rigid foam etc can provide both vapor release and small amount of bulk water.
Using this philosophy I think the top of the roof deck gets 2 layers of a suitable vapor barrier. Then rigid insulation and a roof that has at least a 50 year life that is back vented and drained.
For this homeowner they would not have the vapor drive if there was 2 layers of rigid insulation on the outside. His R value would be in the R30 to R 60 range for his area. Currently he has an R19.25 (3.5 x 5.5inches) This is well under the R30 minimum and only 1/3 of the R60 maximim.
Adding 4 inches of rigid at 6 per inch would add an R24 plus the R19 for a total of an R36. Hardly an extreme level of insulation. What it would do is cut down on vapor drive and thermal bridging. The multiple layers woud allow the deck to dry in both direction and it would give a path for bulk water drainage.
Answered by Robert Hronek
Posted Wed, 08/25/2010 - 18:11
Don, I erased post 104 because in the time it took me to write it more information was presented, and it no longer made sense. Bill Rose was mentioned in several posts and posted once himself. Unlike most here I think fiberglass can work well in a flash-and-batt arrangement (google it or search this site) but your situation is complicated and I would not recommend anything but tearing everything you have down and starting over.
Final answer; BSC may have given bad advice. Joe is amazing. But we that build, just sayin Joe....
Don, implement one of my plans.
Life is good and when you hit bottom up is all that's left.
There is nothing wrong with the detail from BSC.
It is clear, for whatever reason, the OC foam installation has failed. If there is gap between he sheathing and the insulation, as you show in your photo, you will have condensation issues. The insulation should be removed and replaced.
Given the moisture issue in your house, whether climate related or due to some issue with your house, a closed cell foam might be a better option. And then cover the foam with drywall, caulked and taped as required to provide an airtight seal.
Get a blower door test as suggested above.
Make sure the rest of the house is properly air sealed and insulated.
Provide for ventilation per ASHRAE 62.2
And plant the tree...it will provide shading to lower your cooling costs.
Regards....Bruce
I, like many/most who have commented on this thread, am NOT an expert.
That's why I stopped commenting for a while.
I AM just very,very, damn curious about this "Stuff"
I applaud Don for posting here
and for all of his effort to try and do it right
and his effort to document...and warn others
There is a lot of stuff going on here
If a House is a System...this House may only be a Half-A-System...
because Only the Top Half has been partially "upgraded"...
ventilation has not been mentioned
and it is still unclear where the excess moisture is coming from.
could be coming from outside at soffit
from gaps in planks
from a not so perfect air barrier above the porch
from a variety of leaks in the lower half
from inside activities
from the basement/crawlspace
yada...yada
The BSC detail looks good "on paper"
But who would of ever thought that "Foam Shrinks" and "Shit Happens"
I think the BSC detail is Not-So-Forgiving
Don was lucky ..in a way..because his problem(s) were revealed
BEFORE he completely finished "upgrading" the entire house.
How many other houses are out there with Not-So-Perfect Foam Jobs and Pressure Boundaries(peel&stick) on the wrong side of the assembly?
Festering....with no way to relieve the pressure
100% agree with your last post John.
I've only done a few myself, but guys who do a lot of infrared inspections of spray foam jobs--before and after the drywall is up--report finding a LOT of problems out there with the foam separating from the framing, and/or voids within the foam itself. Sometimes IR inspections are done shortly after the foam is installed, to "validate" the installation, and sometimes they're done later, with drywall in place or even having been removed because problems were suspected. Seems likely to me that a lot of jobs out there have yet-unknown/unseen problems, and many are going to result in situations where interior air can find a way through the foam to the cold sheathing, condense, and.......
OK looks like Bill Bradbury was on the right track.
There's a reason I like experiments: they are the only true data you can get when everyone else either doesn't know and relies on other's data.
Open cell foam is a sponge. It sucks up water AND vapor. That's not a good thing at all if you ask me. You might as well use fiberglass. I don't know what Icynene means when they write on their website >5% water absorption. My experiments clearly show it's more than 30%. The weight of my sample went from 1 gram to about 20 grams after immersion.
Some people may argue it's false advertisement.
Anyways, the foam guy came with a IR camera and it looked "OK". I saw it myself. Naturally I didn't believe it. It's another deception device even if it's not intentionally used as such.
This is how what we dealing with: spray foam conceals everything and we trust those fancy machines and believe it's alright.
Even the experienced installer didn't notice a thing. If you believe in your "God" of BS (building science:) Joe, do so but don't spread the gospel as 'fact'. Some things in those publications are simply stated as facts when they are mere theories.
I took my knife and went for it and it was FUN. Randomly I cut into the foam and guess what. The foam DID stick to the boards but then before it cured it detached itself from the wood planks and sagged about 1-2 inches. John's 3D voids theory was also correct. The foam didn't cure fast enough apparently, hence the "hair" towards the exterior side of the foam.
I cut and cut and the way down to the soffit and guess what: air flow! Hence the air went up the soffit, under the foam, through the voids all the way up and got stuck
Then, it must have been condensating at night, saturated the spongy foam which sucked it all up and hence the RH shoots up the next day!
I cut it all out and you won't believe: the RH went down! Today it's hot and same as always, I turned off all vents but have AC on as usual. The RH is in the 50s when right now it would be around 90% already.
So then I thought, since I am trashing it all (I will send it to Canada to Icynene's offices I am telling you :) I might as well cut some more. I went up to the highest points of the cathedral ceiling and cut more. Bingo! Over 2 inches thick voids, continuous in all directions.
Let me summarize
* No expert saw anything unsual
* IR camera: nothing
* No deflection at those points
* Foam did stick a to rafters
* Foam did stick to wood planks but detached itself LATER but BEFORE fully cured, hence, sag & voids, hair-like appearance on foam's exterior side
* Foam sucks up water like a kitchen sponge
* Foam stinks, the odors get really bad as temp goes up
* Foam sucks up vapors as well
* voids in the foam are perfectly concealed by the foam itself and it even fools the trained eyes of experienced installers
* Foam doens't stick to itself well, which is bizarre because it did stick well to wood
* Foam leaves gaps when layered, fist size and bigger
* This subject pissed me off for weeks now and I am losing even more hair. :)
Hence my conclusions
* Foam is crap, spray foam is a hoax. That's my opinion and I respect yours if it's different. You think you have a good installation, you get it inspected, and you still don't know what you have. In case YOU think your installation was good, grab a kitchen knife and cut, see for yourself!
* The vapor absorption qualities are a disaster
* Spray from a can sticks better, way better
* Upside down spray is risky because it won't cure fast enough: Try the 'great stuff' cans upside down, it's the exact same situation/problem
* too much can go wrong with spray foam. In the case of closed cell you'll need to tear down half the house. And who's gonna pay for that, just in case?
* chemicals and more chemicals...airborne etc
* fire risk smoke risk
* if the installation isn't turning out good, you're stuck with a big mess and lot's of fingerpointing and excuses and B.S. even from the manufacturer
* Who needs this kind of trouble for some questionable future promised energy savings?
Why on earth would I want spray foam in my house?
Naturally the installer will have to come and scrape it out and give me a full refund. I will never consider spray foam again, that's for sure.
And neither will I read anymore of Joe's publications either, he may have a wealth of theoretical knowledge but I rather resort to experiments to establish facts, it's cheaper and more accurate. I now understand why a lot of roofing examples were 'computer simulated' rather than measured on actual roofs.
Thank you all for helping me out and pointing me to the right direction. I will take some pics to illustrate the foam failure in detail. I am sure it will help to see it and perhaps these issues can be avoided in the future
Before you discount IR inspection of spray foam, I'd like to know the inspector's credentials (is he at least a Level 1 trained thermographer?), what instrument was used, and the conditions leading up to and at the time of inspection, specifically the interior and exterior temperatures. I have seen many IR images taken with drywall in place that show problems such as you are describing, and many more of the foam itself (which as you know appears monolithic from the interior).
Had you called a good thermographer you might have discovered these problems very early in the game and without all this fuss.
I wouldn't discount Joe, either, but that's a different issue.
Hi Don,
Are you saying that the sprayfoam company showed you thermal images...and assured you that there were no voids?
I know GBA does not require you to post your last name...and your City
But I think it would be "Helpful"
It was the installer's equipment and I looked at it myself. You could see the rafters it turned red when pointed to an area with no foam. But the voids were not visible
Now check out what I found here: http://www.inspectorsjournal.com/forum/topic.asp?TOPIC_ID=6049
Chad Fabry writes in a different forum:
"I believe the only effective way to insulate the structure is to apply foam directly to the bottom of the roof deck.
Normally, I'm a proponent of icynene, but for metal roofs closed cell urethanes are the clear choice.
I've seen several failures with each style of foam...roofs rusting through from the inside out. The failures with the icynene appeared to me to be the result of the product allowing some conditioned, moisture laden air through causing rust around every area where the protective coatings on the metal had been violated..screw holes, scratches and chaffs where the material met metal purlins etc.
The urethane failures looked to all be installation error. Pockets of uninsulated roof connected to conditioned space by crevice, nook and cranny.
A modest applied cost for urethanes in this area is 1.50 a board foot installed and about .90 a board foot if you rent the equipment and install the product yourself.
"
Now that sounds like a JACKPOT reference to me
John there were no assurances, just saying 'looks OK' and it did look OK on screen. It was a formal inspection by a third party and honestly I won't pay for anything at this stage anymore
David, I don't discount anything/anyone. I am just saying I am not buying their opinions as 'facts'. Especially BSC, installers, or Icynene's. Sure the installer wasn't a themographer and perhaps a super expert themographer would have spotted it. I looked at the screen, it was all green nothing to see.
I don't mean this as an offense but let's be reasonable. I am not buying a space shuttle, I am buying insultation. The last thing that I expected is to hire an army of experts to look at my insulation job and pay more for inspections than for the foam itself.
With all this money I could insulate to R 200 with fiberglass.
Had I known this before, I wouldn't want spray foam even if it was free!
Check this out: Now that I cut the foam open, the absolute moisture in the air is about the same as outdoors, a tiny amount more. The temp is of course lower, about 16F less.
I guess now that the air blows straight into the room there is no problem anymore, isn't that bizarre?
Read back all my posts Don. When I saw you post detached foam, and you posted cleaning with water and TSP, I started to feel somehow at installation, the structure was not in a state that foam should be sprayed to.
Wet, cold, too hot, TSP residue, all kinds of issues when you sprayed. I was not there. Something caused your foam not to stick.
Why did you buy foam to start with if you think it is a gimmick?
Don, people make mistakes. Icynene the manufacturer did not make the mistake. The install failed most likely due to conditions when sprayed.
Back to solutions. The gap is definitely a problem.
So now Don. How are you going to insulate and finish your home? And have you sealed up the rest of the home and insulated it?
As to busting on Joe L, you should call them and deal with them. Thousands if not millions of us treasure his research. Modern tighter homes are problematic. We need Joe and his research. Your home Don, needs to be checked for sure. Call Icynene too and have them come see the detachment. They both should on at their cost go look at your home. Maybe the TSP, cold or wet was the problem, or not.
But, in the end, ALL of us that build need to know why the foam did not stick. It is stuck at the two homes I take care of and the homes are super.
Get Icynene and BSC involved Don.
Don, least expensive solution. Easy, you can do it today. Cut the peak and make it a venting ridge. Done, the gap under the foam will vent. End of added heat, and moisture.
Then get the companies to explain why all failed, mostly Icynene as to the lack of adhesion. I think since the foam did not stick Joe did not cause anything more than exacerbating the "no adhesion" problem.
AJ , you are always talking about all of these fabulous R-20 foam roof houses that you have built...
What is the name of your Construction Company?
and how many homes Have you built?
True in this case it wasn't Joe's fault, granted. But check out what the inspector said about icynene under the metal roofs..... OK he also blames IN PART bad foam jobs but how would you know you have a good foam job when the IR shows it's good and the installer says it's fine, but then it isn't!?
Icynene tells me all kinds of stories and I am sick of it. I will be talking to the installer to get it removed and yes I hope all your projects are indeed fine.
TSP I don't think is to blame, I rinsed it and the foam did stick to rafters, where I also applied TSP. Spray from a can sticks very well on all the areas I applied TSP. The spray can has much more adhesive than Icynene that's for sure I have used various spray cans before for years they all adhere perfectly. The surface was relatively clean and the Icynene did initially stick. It sort of 'broke off' in the middle. Exactly like a hole in a bread when it rises too fast, you know what i mean? You do eat homemade bread right ;-)?
I would love to provide samples to anyone who wants them but honestly this cryptic material isn't for me and I want it out of my house asap.
Check the internet how many spray foam homeowners complain about chemical odors and moisture in the house....I found hundreds!
It can't be that they all need dehumidifiers and ventilators. There's more to the story and I think Icynene definitely doesn't want to hear it.
But they've got plenty of installers to hide behind. Here's a "six-digit idea" as Joe likes to say: sell inferior products and hide behind installers
The inspector I quoted says clearly "
The failures with the icynene appeared to me to be the result of the product allowing some conditioned, moisture laden air through causing rust around every area where the protective coatings on the metal had been violated..screw holes, scratches and chaffs where the material met metal purlins etc"
There is your answer, if an inspector has seen it, I report a similar thing, there is something to it...I presume even without the presence of voids in the material. I think the key failure of OCSPF is its high permeability which isn't good for this application. Yet they advertise the use in cathedral ceilings on their websites. I suspect a systematic product error because there are simply too many installers out there and they can't be all careless/newbies/beginners/etc if they are all trained by Icynene and at the same time you see so many people out there holding red flags.
Again you may be lucky and your installation is fine
John, LMAO ;-) fantastic interjection.
I will post pics so you can all see the facts
Don said:
"Check the internet how many spray foam homeowners complain about chemical odors and moisture in the house....I found hundreds!"
Don, I have seen many of these complaints on the Internet myself...
...but only a handful have posted their names.
my challenge to AJ ... was also a challenge to you ;---)
John I understand your concerns. Put yourself in my shoes would you put your name and address down? Think about all the possible repercussions of doing so.
As a home owner you encounter a lot of denial from installers and manufacturers because they don't want to be held liable. You can chose to deny the validity of my posts.
However, I am not the one here trying to sell something. The other forum players who are installers, builders and manufacturers, do and hence should appear with their full business name.
I read all those forums before I installed spray foam. I believed BSC's docs and I honestly thought spray foam is my only option. Even though I was careful I got screwed.
That's why I am posting here for people to read my story. Feel free to ignore and deny the authenticity of my story. I posted it here to get some assistance so I can get to the bottom of it and to help those who plan to install spray foam. My message is don't believe anyone and there appears to be a lot about this material that we are not being told by those who make it and work with it on a daily basis.
Don, I post here out of interest of all, even Brooks, Riversong, and more. And like you I prefer not to get personal which is what John wants. No thank you my Texas friend. This is a fantastic thread. We all have learned about a fail with the build that Don has. I have stated before that foam failures, rigid, closed, open, all concern me especially for my customer's sake. And liability wise feel comfortable not posting under any other name. John, you know I have just two spray foam units built by me. Both are doing well, and yes via calculations by spray company were issued proper permits. We also sprayed vapor barrier paint as per the code request and the roof spray foam was continuous since it was truss and the spray covered the truss members.
John, if you want to chase me off this site, you are well on your way though I think It's GBA's site not yours.I enjoy friendly banter but not stalking and haters. Am always willing to be at peace with you, Riversong and the entire world of lovers but not haters and stalkers.
Lastly, let's stay on topic. Our personal can go offline. Ajbuilderny for gmail.
Love,
Aj
ps- john you can be a lover, I know ya can our big Texan buddy. Clip art's just not showin the love....
John you wrote: "I have seen many of these complaints on the Internet myself...
...but only a handful have posted their names"
If you honestly believe these people aren't saying the truth and it's some gimmick to hurt the spray foam industry, then please send me a message, we organize a time for you to come to my house and we make a video proof of you judging the odors on camera.
How about the youtube video I posted above. These guys wouldn't be taking down their house for fun.
Besides posting names doesn't prove anything either. I still don't know if John Brooks is real or not, and even if real, you could make things up, too.
The stories must be true in my opinion because I can relate to them. I see it happening in front of me. It's not made up.
I can imagine people don't want to put down their names because they may be afraid they could mysteriously disappear one day....
Finally I took my pics and here they are, proof, truth and nothing but the truth:
Don, I think it is highly likely that you are being honest.
that's my opinion
and I apologize for the "anonymous distraction"
I was having an aspergers moment
thanks for posting
Thank you John I really appreciate your participation here and the hints and advice you gave. I think you Riversong, AJ, and many others have contributed a lot to this thread and I value your time and expertise. I am sure all other homeowners reading this find it educational to some degree as well. I had never seen foam or any talk about foam issues before buying it. I think the photo material presented here would have helped me plan my roof & insulation projects better.
What do you think of the latest pics?
Do you think these installation errors (or whatever caused it) warrant a full refund?
Let's see if Icynene joins us again inthe forum. They were quick to blame influences external to their product but how about the foam itself? It should be a piece of cake for them to analyze the situation based on the pics provided. They should know their product in and out. I would add more pics if they wanted a specific sample or procedure performed.
I am open to cooperate and get to the bottom of this, I hope some installers or other foam experts and especially Icynene would join at this point as well.
I think the foam companies have application guidelines for temperature range....
I wonder if they consider the moisture content of the surfaces?
Torsten?...or other foam experts? any insight?
Don, the weather history that you posted ... looks like absolute humidity was extra high for an extra long period ...just before the application
I wonder if the exothermic reaction...combined with solar loading ...and extra wet wood..
could have "blown" the foam away from the surface?
just thinking out loud
Like I said before the conditions that the foam was sprayed to were way worse than my builds. My sheathing had shingles above over 30# felt, the sheathing was new, and dry as could be, no mold or TSP. Foam is stuck tenaciously.
Note to all, I like building slower like many of us custom builders up here. My frame is given time to dry and normalize. My drywall since we started working hard at great finishes is screw pop free.
And one more issue. Full membrane on roofs does under the right conditions end up being destructive. Every material we use has eco's that work, semi work, and fail. Wood sealed up on one side has to pump out moisture fully to the more permeable side and or take it in.
Again; stated back some years. I now much prefer natural materials(thank you Riversong). Am ok with spray foam that my one company (Northeast Sprayfoam) provides for me but do not feel anyone should use it if there is even a bit of hesitancy especially any health issues.
Don, glad John is back to Mr. Nice Guy. Your pictures and research are fantastic. Send all of this to BSC and Icynene.
Existing situation solution; add ridge vent put back foam and XPS. Less smell and pretty good insulation. If out of $$$ it would be a good bandaid fix. Much better to remove foam and blast wood fully clean. Then if a settlement check comes along, take off the metal and membranes, build a proper externally insulated and vented roof.
You could also vent inside with glass batts, rigid foam drywall.
Don, as I said before and see in the pics, the boards look terrible in places where the foam did not adhere leaving residue.
@ post 136
"Foam is stuck tenaciously."
considering Don's Experience ... How do you "Know"?
AJ knows, period ;-)
Hope you guys had a good holiday!
I spent some time taking down the Icynene between three rafters and installed XPS between the rafters as I originally intended to do. It's actually simple; however, removing the open cell foam is not.
Yes I know I may be building "lobster traps", I am trying not to but at this stage I don't care anymore.
A new round of spray is not an option.
The bulk comes off quickly but leaves a 'dust' like film over the wood, which appears to be fine foam particles. Obviously no new foam will adhere to it and I'll need to use sand paper to remove it at least from the rafters. Removing the foam is quite labor intensive, and you are left with a mountain of foam bits.
Can we trash it or is it hazardous waste?
! RUST !
What really puzzled me was a new discovery. I spotted about 6 screws coming through the planks and they are all corroded! It's a brand new roof and I am certain these are rust resistant screws they used. All the screws were encapsulated by Icynene foam and the rust left a mark on the foam too.
I am not an expert but I interpret this has happened because interior vapor reached the frozen roof deck in the winter? We obviously didn't have a roof leak there. I guess this is strong proof this ain't the right material for under a roof!
Check reference in post 119: The rust on the screws matches what the inspector observed in other roofs: "I've seen several failures with each style of foam...roofs rusting through from the inside out. The failures with the icynene appeared to me to be the result of the product allowing some conditioned, moisture laden air through"
Tenaciously stuck. Happy July fourth GBAers.
Don, open cell is "blown" into foam by water turning to steam as it exotherms upon mixing and exiting the gun nozzles.
Are you finding foam stuck to the better looking boards? What temperature was the roof when sprayed? What was the date? I think you posted that data... Point me.
Tenaciously yours,
Aj
Don, sprayer fault, they fix. Are you assuming fault?
AJ, after looking at those pics and the experiences you had with your own installers, would you say it's "obvious" my installer screwed up? I have a feeling they might come back with more B.S. and patience is running low ;-)
Don, Something made the foam detach. The sprayers have a major interest in doing all good work including identifying conditions that are not conducive to spray foam application. Not matter if it is temperature, moisture, a board roof with spaces, TSP, or mold.
Please answer my questions. What are you finding at the wood surface where you have good verses poor foam adhesion?
You really should get Icynene, the sprayers, and BSC fully notified of this thread, all your pictures and request all come look in person, and you'll provide bottled water refreshments gladly.
Hi all
well Icynene has already participated here so I guess they are already aware of the material we gathered. Haven't heard anything from them yet. But I think their explanation addresses only some of the phenomena we have discovered.
"What are you finding at the wood surface where you have good verses poor foam adhesion?"
I found this extremely helpful doc online: http://www.jlconline.com/cgi-local/viewnew.pdf/52bd293d12f10b17a17ea34bf56ce8e7/7f9d7781ac1a3a7d056da9c720894a44/www.jlconline.com/cgi-bin/jlconline.storefront/4ca4bc7808478e5127180a32100a063c
or google for "troubleshooting spray foam"
It says you shouldn't spray foam when within 5 deg of dew point and not on a cold or moist surface.
I am now almost 100% certain the foam was applied when RH was too high for too long and the temp too low.
The document also has sample pics that look a lot like mine. For example: the 'rising dough' phenomenon is shown there, too, and it's caused by spraying to a cold surface.
Now, in my case adhesion to rafters is good whereas around 90% of the time the foam shows the 'dough' phenomenon against roof deck. Since it's an unvented metal roof and they sprayed early in the morning, it's almost certain to me the roof deck was at dew point for sure AND cold ,hence the foam broke away from it because it affects it's curing process. It did stick but it sagged down before fully cured.
TSP isn't an issue, nor is mold. First I cleaned and rinsed relatively well and I treated the rafters even more than the roof deck. Rafter adhesion was no problem.
Rafters are also better insulated. It's 6" deep and I can tell you right now in the summer an exposed rafter will be 12 def F colder than the exposed roof deck, the R value is definitely playing a role here.
In addition, some planks were replaced and the adhesion problem exists there as well, those planks I didn't treat at all.
As I said the foam did initially stick everywhere and then separated away by breaking off. It's not the same as spraying on a dirty surface. Because the dirt would show on the foam. Here we have a layer of foam on the wood everywhere, about 2mm and then 'hair' onthe exterior side of the foam that sagged down.
What concerns me is that apparently the winter moisture went right through the foam and rusted the brand new screws. 6" of Icynene did not create a sufficient vapor barrier, the roof deck froze and vapors apparently have condensated there.
I'll be talking to the sprayers and see what we can come up with, will keep you posted
As always, thanks a lot for your help!
Don, your last post says it all. I am glad we all stuck with this and that you worked so hard to investigate you wetting issue. GBA should write up the short story version. The JLC article is priceless.
Don, you should print this thread out along with the JLC article to go over with your spray contractor.
My contractor was heating and recirculating his hoses, checking temps, keeping his barrels heated day and night, etc. Owned the best Graco made, tested foam during spray, and more.
Northeast Sprayfoam is my contractor. I use no other.
I called and they said the installer will come next week with an Icynene rep
I hope they won't come to try to make me believe I screwed something up....or worse that the foam is OK, which it clearly isn't.
Well the foam will be removed either way and I'll make them pay for it. Whether it's going to be a couple students and sandpaper or something more 'professional' I don't know but it needs to be done
I just don't want to wait too long as it may be too cold to get this done. As we have seen in my case, mid-Oct is already too late for mid-Atlantic regions. I will be documenting the progress and I am planning to add a couple of temp&RH sensors into the assembly so we know 100% what's happening behind the new insulation
So Icynene came and the guy says "he sees no problem with the foam"....looking at the areas I took pics of, see previous PDF post.But he wanted to check back with his buddies.
Installer says could have been done better, didn't stick as it should have. Refund plus cleanup costs are on the way and I'll be taking this stuff down as quickly as possible before more damage occurs to the roof.
I can be such a pain in the ass, huh!
However, I maintain the position that the stick or not stick isn't quite the main problem.
The main problem is open cell is no good and especially no good for ceilings due to the high perm rating and water absorption characteristics. The already rusted brand-new screws I found are proof the roof deck receives a good portion of interior moisture in the winter... even behind 6 inches of "good" foam.
I'll summarize my findings later on but in the meantime check this out "Repairing a Rotting Roof",
a fully documented story of how someone else like me got screwed with Icynene. OK let's be fair
how someone else got screwed with Open Cell Foam since all of them are the same.
Anyone still considering spraying open cell under the roof after reading this?
http://www.jlconline.com/cgi-local/viewnew.pdf/52bd293d12f10b17a17ea34bf56ce8e7/36d788c301e849ce97885b518ca065ce/www.jlconline.com/cgi-bin/jlconline.storefront/4c969cd90919808a27190a32100a0671
Sure, blame the installation. These guys had even 9 inches, whereas I had only 6 installed. Of course, blame the house and the HVAC. Fact is they were sold the same material with the same results. Different house, different installer, similar story. Some voids, ok, how do you your installation doesn't have them?
The "gimmick" of this product appears to be based on fingerpointing, not solid performance proven in various settings. Then, when all fails, Icynene or whoever makes the material, blames the installer and the house and they are back clean. If the product was so great they would install it themselves....but then they would have to pay huge reimbursements to their employee installers down the line since most of them will probably end up with lung cancers. It's a well thought out business, I agree.
My opinion remains the same, spray foam is an expensive joke and quite a risk to our health, but please find out for yourself... Whether it worked for you, you'll see when the roof needs to be replaced...or perhaps you may get some health problems inhaling it, God forbid, knock on the wood, I hope I am wrong on this one.
AJ make sure you're far away when the roofs start failing and the home owners start calling.... or are your roofs vented? :)
First of all Big Thank You to John Brooks, Bill Rose, an every one else who participated.
There are no rants in this last entry so read on :)
**** Summary of Analysis *****
1. Open cell foam is not suited as roof insulation because of its high vapor permeability.
After the first winter I opened several rafter spaces and removed the 6 inch foam layer. Every single fastener showed clear signs of corrosion! See example picture below.
This is enough proof to me that in the winter time enough vapor went through the foam and condensed on the underside of the roof deck.
This alone is reason enough to remove all the foam. I don’t want a $20,000 roof to rust prematurely.
2. Open cell foam is not a good insulator in general for humid climates because of its hygroscopic characteristics.
Open cell foam retains far too much moisture. Browse the web and search for moisture issues and spray foam. All the reports and customer complaints I could find refer to open cell foam.
Why, it’s very simple. Open cell is huge sponge, a mega moisture buffer. Why would you want to have this in your house?
The response to this thread made by Icynene on page one was hence partially correct. The foam, not the wood structure, is to blame for this enormous moisture increase in the upper floor I have been measuring. Remember the relative humidity in my upper floor goes up from around 45% in the morning to over 80% during the hottest hours of the day, similar to all other consumer complaints I found on the web.
No, it’s not that we have too much moisture in the house. There is also no fault with the AC. This has been checked by professionals. The problem is simple, it’s the foam causing all the issues and below is the experimental evidence.
Based on ‘the experiment’ quoted by John Brooks earlier that appeared in Bill Rose’s book I made a couple more experiments. In Bill Roses book two sealed containers were heated. One with just air, the other one had a piece of wood in it. The air container’s RH dropped, while the one with the wood remained high even though the temperature was also increased-> overall moisture in air had risen.
Remember the foam I covered with plastic and stuck a thermometer behind? The RH inside the foil shot up to 99% within hours but never returned back to normal. Actually it remained constant at 99% for DAYS.
I removed the foam and let everything dry. I checked the roof deck with a moisture meter: normal 5-7% moisture content. Actually I can check anywhere behind the foam, the wood is always at 5-7%.
Then I took a new foil and taped it directly on the roof deck with a thermometer stuck inside. The RH started at 50% at regular room temp in the morning. It then increased during the day to only 60%. The next morning it was 35%! Hence, the wood does indeed exhale moisture when it gets hot and sucks up moisture as it cools off.
Thank you Bill Rose! Your experiment was replicated successfully and it explains a couple of important principles.
Now this morning, I took a square foot sized Icynene foam, 6 inch, and put it in a bag along with a thermometer. I wanted to repeat a similar experiment as before but this time with the foam alone, based on the principle that moisture exists the material when the material is heated.
The initial thermometer reading was 24C and 54% RH. I took the bag and placed it outside, see pics below. The next reading was: 38C and 41%RH. Doesn’t sound like a lot, but look at the details!
Air in bag: approx. 1 cubic foot -> 0.0283168 cubic meters (m^3)
Start temp and RH:
24C, 53 % RH => 0.01146 kg/m^3. Actual moisture in bag = 0.0283168 m^3 * 0.01146 kg/m^3 = 0.000324510528 kg = 0.324510528 grams
At noon:
38C, 41% RH -> 0.01875 kg/m^3. Actual moisture in bag = 0.0283168 m^3 * 0.01875 kg/m^3 = 0.00051219 kg => 0.51219 grams
Difference: 0.00729 kg/m^3 = 63% rise in moisture in bag! In grams: 0.51-0.32 = 0.18768 grams rise
The moisture in the air in the bag increased from 0.3 grams to 0.5 grams!
And this was just one sq foot of foam. I’ve got 1,800 sq feet of foam installed.
Let’s do the math:
If 1800 sq ft Icynene exhale 0.2 grams/sq ft. of water vapor when the temperature rises from 24C to 38C, which is actually a very realistic assumption, the underside of the roof deck goes up to 51C on very hot days, then we have a total water vapor of 1800 * 0.2 grams = 360 grams.
This means that in a short period of time, a couple of hours, at least 360 grams of water are released into the room, which has a total air volume of approx. 140 m^3. That’s an extra 2.57 grams for each cubic meter of air that the air is loaded with.
Based on this useful tool http://www.conservationphysics.org/atmcalc/atmocalc.php you can figure out that an extra 2.57 grams of water per m^3 at room temp (23C) causes a 13% RH rise, for example from 50% to 63%
But then we need to also consider (all other things being equal) that dry air is heavier than moist air; hence, vapor moves up. That’s why we see clouds in the sky. As time passes vapor gathers at the top and begins saturating the air.
Over time the 13% RH rise will turn into a much higher rise at the highest point of the ceiling.
If all the vapor accumulates in the upper quarter (140 m^3 /4 => 35m^3), then the rise is 360 grams / 35 m^3 = 10.28 grams / m^3 rise
And that would easily increase the RH from 50% to 98% RH! I have measured over 90% RH on certain days, normal range is 70-80% RH. The floor of the room, on the other hand, is usually in the low 50% RH.
Hence, we always get the Icynene recommendation “ventilate and use AC”. Now you know why, because if you ventilate you spread the 360 grams across the entire room (the rise from 50% RH to 63% RH) and it will feel muggy but there will be no condensation. If you don’t ventilate you’ll see condensation at the peak of your ceiling, likely causing long-term damage since the vapors have nowhere to go, around 90+% RH.
The problem is the walls and ceiling store and exhale moisture and this moisture cannot be easily removed by an air conditioner. If your roof is vented, the moisture is likely to come from the outside as well since the foam would be open to the outside humid air in the summer.
Since most likely you’ll install drywall over the foam, the drywall will actually work as an additional moisture buffer and keep air flow away from the foam. Since there is no air movement between drywall and foam, it’s a typical setting for mold growth because the RH in that cavity will easily top 90+%, even if you ventilate the room well.
It is likely I would not have had this moisture problem with closed cell insulation materials or other non-hygroscopic insulation materials. Moisture can easily be removed by an air conditioner, as long as it stays in the air. Once materials absorb it you need strong dehumidification to pull the moisture out of the material, ie. you need high RH difference. Also, ACs are made to drop temperature 20 degrees F (air intake vs. out) but this may not cross under the dew point temperature sufficiently in order to dry the air. The result is the AC reduces temperature but not so much moisture unless the dew point is near room temp.
I also think that a lot of that moisture comes from outside and not from indoors because the foam does come into contact with outdoor air, for example at the soffits. Also stick frame construction is very leaky, so unless you spray all your walls or build using brick and mortar there is enough infiltration from doors, windows, and walls to bring in moisture. That moisture gets absorbed by the foam during cooler days and then gets dumped when temperature rises.
After removing half of the foam in the room above porch, the RH problem has disappeared; hence, there must be some validity to this perspective.
Conclusion:
1. Rust on fasteners is clear proof that open cell foam is not suited for ceiling applications, when installed under roof deck. Even at 6 inch there is still too much vapor making its way through the foam and it condensates under the roof. I have quoted other customers earlier in this thread who found the roof was rotting and a building inspector who has seen metal roofs like mine rust “from inside out” when open cell was installed. Do not use open cell under roofs, period.
2. The 900 cubic feet of Icynene I had installed in the upper floor are in fact a huge moisture buffer. The proof is the experiment below (open cell foam enclosed in plastic bag). A lot of moisture is held by the foam and it is difficult to remove that moisture because the foam is installed between outdoor and indoor air. It’s a physical fact that vapors want to balance so you will always have the problem of vapor traveling through the foam due to vapor pressure. The high vapor permeability of open cell is a problem because it lets vapors pass and the foam being a moisture buffer is also big issue because you need to deal with the moisture inside your house. Wouldn’t you prefer to keep moisture out in the first place?
3. The condensation upstairs in my home occurs because the foam dumps large quantities of water vapor back into the room. Unvented roofs don’t offer any other escape path for the vapors; hence the room’s RH shoots up and vapors gather at the top because moist air is lighter than dry air (another physics fact I had to learn). A vented roof, on the other hand, would allow vapors to be driven towards the interior, through the foam, on humid days.
4. Additional proof apart from my experiments: I removed half of the foam in the room above the porch and replaced it with XPS. The relative humidity now hardly ever reaches 60%, while the other section of the house still rises above 75% RH on hot days, with the spray foam intact.
Our friend Riversong would agree I bet he would respond:
1. Don’t build unvented roofs, it’s stupid!
2. Don’t use open cell foam at all.
I want to also add that if you do ventilate mechanically and get a bigger AC to dry the air and a dehumidifier to remove all the moisture dumped by the foam, you quickly end up with an electricity bill higher than you can imagine. You may never see any of the promised energy savings, I certainly haven’t.
Don, I can only agree that your home was insulated in a failed manner.
There are thousands if not millions of homes that are insulated with open cell successfully.
Your home had way too many things done wrong.
The application did not stick to the roof.
The application (taking into account the rest of the project details) should not have been attempted.
To me the blame lies directly with the GC (you) and the sub (the spray company).
Any material can fail, XPS can fail, cellulose beloved by Riversong is a no go in a cellar because there is a huge moisture source in a cellar. The much loved cotton batts are a horrible choice where moisture load is going to get to them. IE, my laundry when left in my very dry cellar for a few days too long gets so moist that it feels wet. Cellars are no place for hydrophilic's.
You are half right Don, but not fully right.
For your home that you are slooowly building in a humid climate and not adding any moisture control that is needed, yes you need to not use unstuck open cell that is being bathed in outside air via the unstuck and unvented chutes your installer improperly made and that you improperly designed and improperly built too slow and with out taking into account the entire envelope design that you even admit to.
I agree to disagree Don. ;)
AJ I agree with you. This should not have been built that way using open cell foam.
I should have never sprayed foam anywhere.
I tried to make the point, that given the average leaky window, door, etc, in a stick frame construction, you'll have air infiltration and hence moisture infiltration. Iam talking about the homes out there AJ, not new ones made by an insulation expert.
The rusty fasteners behind intact and correctly installed foam (no voids) show that open cell is clearly not the right material. You cannot build a house with OC under an unvented roof and not have rust on the fasteners. Unless you kept perhaps RH under 10%?
Like you said, all materials may fail and can be used in a 'wrong' setting. The point I am making
is you can't use open cell under a roof in an average existing home.
You would have to run dehumidiers and AC like crazy to compensate for the vapor buffer effect of the foam. If you use a different material, such as closed cell then:
1. there wouldn't be any rust on fasteners since moisture can't get to the roof deck
2. the moisture would remain in the home where AC can pick it up easily
3. the R value would have been better, too.
R20 is not enough in MD, in case anyone wonders. If you want to keep your heater and AC running more that's up to you but it's not comfortable as R30 are.
All of the above has nothing to do with how the installer screwed up. It's the choice of material that was the issue. I based my material choice on Joe and Icynene's website docs, along with other materials online. This was clearly a bad and dumb idea. These are all people trying to sell foam.
I posted the above info to help people know more essential facts and make a better decision.
In the meantime I am removing the Icynene and I'll keep an eye on the how the new insulation performs.
And once again, I agree with you AJ, the guy who hires these people and uses these materials is to blame. But I disagree also because I have been given false and inaccurate information; hence, I put this online for others to read. Installers move across the country telling their tales of energy savings and they install foam where it shouldn't be installed.
*Those* are the people I want to help avoid mistakes. Don't buy open cell. If you AJ are able to design a moisture controlled superior construction using open cell, that's great.
However, the homes out there are average leaky homes like mine and they are being sprayed with open cell when they shouldn't be. And you know, leaky is good to some degree as clean air can enter the house without the need to run electric fans to do the same thing.
Then, Icynene and installers come and blame the house: this is indeed the problem!
The blame is relying on false info, on the web and all over.
AJ, you hit the nail on the head!
Update: the foam in the bag outside is now 44C hot, the RH inside the bag: 36%.
The new numbers are: 0.63 grams of water vapor in bag, hence, 0.32 grams more than when I packed it, for my entire upper floor 1800 sq ft of Icynene * 0.32 grams water vapor rise per sq ft = 576 grams. There is now 60% more water vapor in the bag than in my calculations above at 38C.
When you do all the other math it turns out the RH rise of the entire floor is +20% at room temp, for example from 50% RH to 70RH!
Moisture issues with open cell foam are now demystified!
And last update. The bag was in the sun and reached a stunning 65C, 20% RH. The amount of water vapor in the bag is now 3x as high as it was at noon.
I that's 1039 grams of water for the entire upper floor more than this morning, a 7.4 grams per m^3 rise, which is equivant to a humidity rise from 23C 50% RH to 90%RH !!
I think we have enough proof now to finalize the subject. If anyone has evidence that 'so many houses are OK with open cell foam' please present proof because I simply don't believe it.
At least I can back my claims with solid numbers, but I haven't come across a source to back the claim that open cell under a roof "is ok", and this includes AJ's claims
Don, your science experiment with foam in a bag is nonsense. Bad experiments resulting in bad results are meaningless. Icynene would be out of business years ago if all their thousands of homes ended up being sprayed wrong like yours was.
Your sprayer sprayed foam that detached and created the moisture trap with your help in adding the XPS water trap. That gap above the foam was a huge part of what allowed humid air to rise to your peak and wet your foam. Icynene would not ever detail such. This site is filled with disasters where unvented channels end unvented. Beside the moisture if you left all, you would have had a rotted out roof, not just rusty nails.
And as to your rusty nails, give it a break man. The part of the nail rusting in the foam is not holding the roof on. The part embedded in the wood is holding the roof on. I just measured a 25 year old roof. You should see the goof ups. I think most roofs up this way have goofs. 25 years ago ridge caps were all aluminum this way. Roofers would just use cheap gun nails that barely have coatings. Dissimilar metals together are batteries, one metal becomes the cathode and the other the anode. This makes the nails eat away faster than a roof goes bad and then the ridge flops off someday.
I know you feel like dissing Icynene for the rest of your life but your home had too many things going against success. Many companies and specifically my company definitely can install spray foam and leave their customer happy and well insulated. I am posting from a perfectly sprayed customers home sprayed to R-20 that barely uses energy. I know, I see the bills. And yes, the entire home was detailed to save energy including proper siting for solar gain and shade.
Don, in the end, someday down the road your XPS cut and popped into the rafter spaces, will be much more water resistant. What that means is any wet air the will get to the roof deck will for sure rot out your roof not just rust the nail tips. So your next disaster may be in say 5-15 years. Good luck with that one and who to blame.
DIY homebuilding is a grand experiment Don. Enjoy. It is tough enough as a contractor trying to build modern homes tighter without making any fatal mistakes.
Spray foam was your nightmare Don. But it has not been for me. My warning on this thread is to not repeat your mistakes. And we all make em, especially me. :)
Just looking at the Icynene site. They say to contact their staff for building details. They also say to use a vented roof when the roof is low perm such as this roof being discussed. I still say the spray men and the person in charge of details, plans and material selection made the mistakes not Icynene.
The lesson for all of us is to contact manufacturers, use their sites, and repeat builds that knowingly work in your build environment.
As has happened before, the use of full roof ice and water shield at times has led to major failures for lack of permeability.
The shingle companies of late only warranty their products when their permeable underlayments choices are used. They also will develop exact materials list for when needed.
The manufacturers want us and themselves to succeed and the internet should via manufacturer sites be a positive.
.......
HI Don,
How about an update?
Did the Foam company refund and/or settle with you ?
Were you satisfied with the settlement ?
Hi John
your hint about Bill's experiment was extremely helpful. The experiments we did with the foam were hard evidence to get the company to settle. Actually they settled very quickly, so quick that it appeared to me they do this rather often and know that the materials are problematic. Naturally they won't admit nothing but they immediately agreed to an additional sum for cleanup that I proposed. It was rather low but I wanted this off the table without legal action, which in itself would be expensive and stressful.
I got my own crew together on weekends and we scraped about half the foam off. The humidity problem disappeared almost completely for now. The smell got better, too, but we are not done yet removing all of it. We pack the foam pieces in trash bags and I keep them in the garage for now. Guess what, the garage smells like Icynene now, just like the installer's office by the way, which is very well air conditioned.
These people got so used to the formaldehyde smell they don't notice anything anymore.
Anyways, I'll keep you posted. The XPS performs very well so far, I will be embedding RH sensors under the roof deck to monitor moisture all year long. At least if I screw up again, I want to know precisely what needs to be improved. It's also intersting that using the pink stuff at 4" and paying for the labor to cut and seal is still cheaper than hiring a spray foam company. As I mentioned earlier, the main reason we're doing this is not the cash but the odor problem that comes with spray foams.
Fasteners under the foam: all rusted by the way with new mold formation on new wood planks. Open cell under unvented roofs is a dumb thing to do and I now got the proof for it. The stories you read online are all pointing to the same direction: it's the material not the installation causing the problems. I might take some more pics for you later this week.
Hi guys
just wanted to let you know, I got my hygrometers from China which are unbelievably cheap and accurate. I plan to embed these right under the roof deck before installing XPS over it:
http://www.tvc-mall.com/details/Multi-function-Digital-LCD-Hygrometer-Thermometer-HHC-2254/
This should give us a very accurate idea of what's happening inside the assembly during winter and summer extremes. I got 10 of these for under $30, and the first one I tried appears to be quite accurate. They are supposed to work from 10%RH to 99%, and -58F to 158F. I never measured over 130F under my roof deck, even when it was well over 105F outside. That's most likely due to the light colored metal we have on the roof. So I think these ten probes should give us a lot of info to work with.
Is XPS between rafters under an unvented metal roof a good or bad idea? The probes will tell us in a couple of months. I'll be taking pics shortly, half the roof is done already