I would like to ask some questions about attic insulation in a place with very mild weather

Our house was built in 1907 in the South Park neighborhood in San Diego. It is a two story Foursquare Craftsman with 3200 square feet of living space. The home is located right under the landing path of airplanes going to the San Diego Airport which as the crow flies is 3 miles from our home. We have two major problems, no insulation and too much noise.
Our house is located in IECC 2009 Climate Zone 3 a place with very mild weather.
San Diego weather between 2010 and 2016 had:
zero days below 32 degrees Fahrenheit
number of days when temperatures reached at least 70 degrees F:
130 days in 2010
242 days in 2016
Number of days when temperature reached at least 90 degrees F:
3 days in 2010
14 days in 2014
6 days in 2016
Rain fall is low to dire:
16.3 inches in 2010,
5.6 inches in 2013
10.2 inches in 2016
Our average humidity is 70 to 80% in AM (at the high end in the summer, low end in the winter), and 50 to 67% in the afternoon.
The attic:
The house has vented attic (40 feet x 40 feet floor space with 9 feet height at the highest point ) which contains an 8-year old Trane gas furnace and all the conduits that provide heating and AC to the upstairs and also a major conduit that travels through the space of an old cooking chimney and connects to the conduits in the crawl space.
The 2-year old roof has light color asphalt shingles with perimeter plastic vents tucked under the shingles and a ridge vent . The soffit panels are old and leaky. The roof has no insulation
We have 12 inches of blown in fiberglass insulation on the attic floor which has done nothing to prevent the attic from heating up the upstairs rooms
In April on sunny days the attic was about 40 degrees Fahrenheit hotter than the outside temperature (outside temps in the 70s, attic up to 113). Under heavy clouds the attic temperature differential was only 10 to 15 degrees (outside temp in the mid-60s, attic temp 76)
The IECC recommendations for our area is
Ceiling R-value = 30
My questions:
I know from your articles that making attics containing ducts part of the conditioned envelop by air sealing and insulation the attic is beneficial. Applying closed cell foam to the attic ceiling would accomplish both, however, in California, the installation of ignition barriers to cover the foam is required. Our gas furnace can be converted from open system to closed system.
In a location with such mild weather, would the expense of this approach be justified?
What if we were to insulate the ceiling with Roxul R15 Comfortbatt (we have 2 x 4 rafters spaced about 20 to 23 inches apart) leaving the periphery vents and the ridge vents unobstructed. Then insulate the floor of the attic with Roxul R15 Comforbatt to add up to R30. Would this work?
GBA Detail Library
A collection of one thousand construction details organized by climate and house part
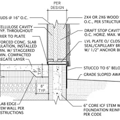
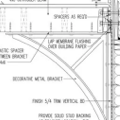
Replies
Leda,
There are a lot of variables here, some of which are impossible to pin down, and some of which can be pinned down with a site visit. But if you decide to install spray polyurethane foam on the underside of your roof sheathing, you probably won't save enough energy to justify the high cost of the work.
That said, your house will be more comfortable.
One other option to consider: You could install a radiant barrier on the underside of your rafters. Depending on the cost to install this measure, it's more likely to be cost-effective than a full insulation job.
Martin: Thanks for your prompt answer. About a radiant barrier: Would a painted on radiant barrier like LoMitII water base product work? What if I placed a radiant barrier on the underside of the rafters and then used Roxul Comfortbatt R15 next to it, would this work? The Roxul would help with airplane noise as well as insulate.
Combining a low-E silvery paint like LoMitII on the underside of the roof deck, combined with a perforated aluminized fabric type radiant barrier will indeed do a better job at limiting the heat transfer than either one alone.
Blowing 3-4" of cellulose over the top of the fiberglass (and over the ducts, etc) can lower the noise transmission issue, and increase the insulation effectiveness. Cellulose is more air retardent than blown fiberglass, and is opaque to infra-red radiation. Fiberglass is somewhat translucent to the IR radiation, and under the radiation of a hot roof deck the fiber glass is often hotter 1-2" into the insulation than the attic air temp. That phenomenon goes away if a radiant barrier is installed, but the sound transmission/air-retardency issue is still real. Sound abatement is primarily about impeding air paths, and while rock wool batts are of sufficient density, installing them with NO gaps is often impossible. But 3-4" of blown cellulose gives continuous seam-free coverage.
Air sealing the ducts, and the attic floor/upper-floor ceiling is important for sound abatement too, but if the walls have no insulation and aren't well sealed a large fraction of the noise will be coming through the walls. Blowing cellulose of any density into the walls makes it much quieter. Insulating the walls doesn't change the peak cooling load as much as the peak heating load, but afternoon sun beating on an UN-insulated western wall late in the day can deliver a large fraction of the peak cooling load, as do west facing windows.
The likely single pane double-hung windows can be tightened up with weather stripping, but don't forget to install pulley seals too. Tight low-E storm windows over the antiques can also make a large difference in noise transmission, as well as improving the overall comfort levels. Low-E storm windows make the windows net heat gainers in the winter (more heat comes in during the day than is lost overnight, even on north facing windows), but they also lower the solar gain, cutting into the peak cooling load in spite of their heat-trapping characteristics. This is in contrast to clear glass storm windows, which lower the heat loss (but still lose more than they gain), but barely move the needle on peak cooling load- much higher gain than low-E storm windows. The better grades of Larson storm windows sold at most box stores are tight enough to cut sound transmission, and come with a low-E glazing option. The "payback" on lowered energy use is faster with low-E storm windows than for clear-glass storms, despite the up-charge for the low-E glazing.
Dana thanks for your answer. I am planning to work on the uninsulated walls and old windows next. The walls have lath and plaster on the insider and lath and stucco on the outside. The windows are single pane double hung, 110 year old windows. I was planning to do the following starting with the South and West walls;
Remove the stucco and the exterior window frames.
Preserve the interior window frames
Insulate the cavity with Roxul Comfortbatt as thick a layer as the cavity allows
Install plywood sheathing, 1/2" thick
Water and Air proof the sheathing with a liquid applied WRB: StoGuard
If feasible a one inch layer of Roxul ComfortBoard 110
Install 1 x 4 pressure treated lath rainscreen to hold the Comford Board to the Sheathing and to allow for water drainage.
Install Hardie Lap siding and Hardie window trim
Remove the old windows
Install the Alpen windows
This should make the house quieter and tighter.
Batt widths& thickneses are designed for standard milled lumber dimensions with studs on standard spacings. As such they are usually a lousy choice for retrofitting early 20th century houses, which are usually built with rough full-dimension 2x4s and aren't always 16" on center. Even if the stud spacing is perfect, it means the batts are 1/2" too wide and prone to buckling, and are 1/2 too thin, making full cavity fill nearly impossible unless compressing an even thicker batt. It ends up being a lot of work, and usually a second rate (third rate?) fit.
Damp sprayed cellulose scrubbed flush to the stud edges, or any fiber insulation blown in mesh are a far better way to go.
If there is no sheathing between the stucco and cavities, with the stucco applied to lath nailed directly onto the studs, assuming it's all still in good shape, you may be better off leaving the stucco in place, blowing cellulose into the cavities (no mesh, drilling the installation holes from the exterior) then spraying the stucco with the StoGuard, or applying your layer of plywood (through-nailed or screwed to the studs) over the stucco. A layer of 1" ZIP-R could be used instead of the Comfortboard, in which case the StoGuard isn't needed (the ZIP is the WRB, if properly installed.) That seems like a lower risk, lower cost way of hitting the same performance point. If there's a plank sheathing layer, stripping the stucco but leaving the plank in place is probably best, especially if the plank sheathing turns out to be structural (though there may be let-in bracing to keep the walls from racking.) It's still perfectly easy to blow insulation (even dense-pack for better air tightness) behind plank sheathing.
If using 1x4 furring to establish a rainscreen gap they need not be pressure treated- the cavity provides excellent drying capacity for the lath, as well as for the sheathing & siding.
When you pull the antique windows you'll have a chance to install proper window flashing, which is pretty important even in drought prone SoCal.
Thanks for you answer Dana. When the interior was renovated two years ago, we removed the interior wall in the kitchen and I could see the lath and stucco from inside. The stucco fingers that were supposed to be through the lath had mostly broken off so the stucco is standing in parallel with the lath work but not really adherent to it. I think the stucco needs to go. During the interior remodel, I had not yet found this website, so I missed a great insulation opportunity. Some fiberglass batts were added to the cavity but the kitchen is not well insulated.
Leda,
Have checked to see if your home is eligible for San Diego's Quieter Home Program?
Try BeOpt simulation, it's a free download.
If you want to get somewhere the first step is to make a list of your goals and prioritize them.
If your main goal is make your home sound proof so the airplanes do not disturb you, then comfort followed by energy efficiency.
For sound proofing, air sealing is the best bang for your buck.
For comfort, spend money on your duct work get it inside the building or sealed and insulated in place.
Given your mild climate and current R-26 insulation, you will never see a return on any money invested in insulation or Aspen windows. Put this money into solar panels and air sealing where you will get a good return.
Walta
Steve: we are eligible for the San Diego Quieter Home's program. We signed up years ago, and they inspected our home and did a noise test and told us we qualified. Then we waited as we saw the work being done closer and closer to our home. One day about one year ago, they replaced windows across the street. Then everything stopped due to financial problems with the program. Although they replaced wood window with wood windows before now they are saying they will replace our wood windows with Vinyl windows. This scared us off. So we decided to pay for it and get it done right.
I will try the BeOpt simulation this weekend. Thanks for the advice.
Walter: my goal is to make our house comfortable temperature and sound wise. The only insulation we have is the blown in fiberglass in the attic floor. The rest of the house is completely uninsulated. The windows are hot to the touch and rattle with the wind. When I use the thermal camera inside the house, the outer walls light up almost as brightly as the windows. Air sealing will not stop radiant heat from entering the living space, will it?
Air sealing will not stop radiant heat from entering, but with cellulose or high density fiberglass/rock wool the radiated heat transfer is but a tiny fraction of the heat getting through the wall or attic floor.
The windows are responsible for the largest amount of radiated heat gain or heat loss. But with air handler & uninsulated ducts above the insulation in the attic there is still radiated heat transfer from a hot roof deck to the ducts & air handler which increases the net load on the cooling system. That load gain can be substantially mitigated with radiant barrier & low-E paint. If the ducts & air handler are insulated to R6 or better it's probably not "worth it" to pay someone to install the radiant barrier products, but as a DIY it might be.