I would like opinions on my basement insulation plan

Hello all,
I plan to insulate and sort of half finish my concrete basement for use as a woodworking shop and playroom. Despite a perimeter drain and good gutters, grading etc., there is an occasional damp spot along the edge of the floor during heavy rains, but it is mostly dry.
The goal: to make the basement cozy (it’s cold; I’m in Massachusetts) and avoid the telltale musty smell of the thoughtlessly finished basement. I’m a somewhat ambitious DIYer, but I am not 100 percent confident in my scheme and would appreciate feedback, especially from Martin et al.
The plan: 2″ XPS on the walls, continuous, sealed with high-quality tape and/or spray foam. A little gap, then a metal stud wall with mildew-resistant drywall. Half-inch or 1″ XPS on the floor, covered with Baltic birch plywood screwed into the slab with Tapcons. Caulking between the sheets of plywood — and we’ll call that a finished floor for this industrial vibe. EMT wiring over the drywall. I plan to stop the drywall fairly high above the floor and perhaps use some sort of synthetic baseboards — like PVC? — as extra protection against moisture. No ceiling: just open joists.
On the whole, does this sound okay?
More specifically: is it okay to put the base plates of the wall directly on the concrete, leaving a little strip of uninsulated concrete on the floor between the wall insulation and the stud wall? Or should I run the floor insulation directly up to the wall insulation, and put the baseplates on top of that, or on top of the plywood.
Can I in fact get away with one layer of half-inch Baltic birch as a floor? I do not want to use two layers of tongue and groove plywood, as recommended elsewhere, partly because of head room and partly because it’s a lot to carry and install. Also I like the look of Baltic birch. And can the plywood go directly over the foam, or do I need sleepers?
Is 1/2″ foam on the floor good enough? I’m not going for perfection here, just a bit of warmth and a break between small amounts of migrating moisture and the plywood.
I should note that I already air sealed and insulated the rim joist.
Any thoughts much appreciated.
AL
GBA Detail Library
A collection of one thousand construction details organized by climate and house part
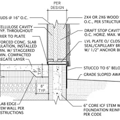
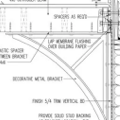
Replies
Alexander,
To me, there are two issues here:
1. How serious a problem is the "occasional damp spot along the edge of the floor during heavy rains"?
2. Is it better to install a strip of rigid foam under the bottom plate of your framed wall, or better to install the bottom plate directly on the concrete?
Question 2. is the easy one. Install a strip of rigid foam -- it's better.
Concerning Question 1: Ideally, you would address the water entry problem better before proceeding with your plan.The work is expensive, but it's worth describing: It's probably a good idea to install an interior French drain connected to a sump.
If you don't want to do that, there is a risk that when you get a very heavy rain, you'll have water entry and water damage.
Other than that, I see nothing wrong with your plan -- except for the fact that you mention using XPS instead of EPS. Most green builders avoid the use of XPS unless it is recycled. For more information on this issue, see Choosing Rigid Foam.
At 2" XPS doesn't deliver the R15 continuous thermal perforamnce needed to meet MA code-minimum. XPS also loses performance over time, falling to ~R8.4 (at full depletion) as it's climate damaging HFC blowing agents leak out.
A better bet (and cheaper) would be to use 2.5 - 3" of reclaimed or factory-seconds polyisocyanurate board (foil faced or fiber), which is avaiable at a VERY deep discount from multiple vendors in MA (Nationwide Foam in Framingham is the biggest, followed by Green Insulation Group in Worcester, but there are others.) The only detialing difference that has to change when switching to polyiso is to keep the cut edge off the slap, since it can wick moisture. If the basement has a flood history, stop the polyiso at the high-tide mark and continue with polystyrene,(the same vendors also have EPS and XPS), or slip an inch of rigid polystyrene under both the polyiso and the bottom plate. Insulating under the bottom plate mitigates the summertime potential for condensation on the steel framing by keeping it closer to room temperature than the slab temperature.
Don't use polyiso on the slab (to the moisture wicking issue) but polystyrene (either EPS or XPS) works fine.
Thanks much Martin. I'll look into the foam choice. As for the water entry, I should've mentioned I actually already have a French drain and sump. I think the damp spots are from water seeping in around the windows, which I hope I have/will address by cleaning out the window wells and keeping after the caulking. I know it should be bone dry for a year before I proceed, I just don't think I have the patience to endure another winter with what feels like a giant open refrigerator under my first floor. I figure if I do it myself, I can undo it myself, when the flood comes, or the pipe leaks, or whatever.
Thanks to you as well Dana. I think the code minimum in MA for basement walls is R10 continuous (http://energycode.pnl.gov/EnergyCodeReqs/index.jsp?state=Massachusetts), but that seems like good information about the reclaimed polyiso. Much appreciated.
Under IRC 2009 R10 would have made it, but IRC 2015 went into effect in MA as of August 2016 (over a year ago.) R15 c.i. become code-min for zone 5 way back at IRC 2012, but the Eight addition of the iRC had held firm to IECC/IRC 2009 R-values. The fully Ninth edition doesn't go into effect until later, but the R-values have already been updated to IRC 2015 as an amendment to the Eighth edition.
https://www.mass.gov/service-details/ninth-edition-of-the-ma-state-building-code
"Due to statutory obligations, the one exception to this message is that the 2015 IECC went into effect on August 12, 2016 as an amendment to the Eighth Edition."
The R-values under IRC 2015 can be found in this table:
https://up.codes/viewer/utah/irc-2015/chapter/11/re-energy-efficiency#N1102.1.2
See here for reasons to avoid foil faced polyiso on the walls. See here (fig 7) for alternative advice about preventing mold smell from damp concrete.
That's pretty weak tea for prescribing against using foil faced foam on the walls. Most of the reclaimers have acres of fiber faced roofing polyiso on hand though, which renders it somewhat moot. If the polyiso stops 6" from the slab (higher, if the high-tide mark is above 6"), that too renders the wall-drying issue moot.