Hybrid interior wall insulation system

My background is custom home construction/historic preservation and restoration. I had a pre-fab 2 story garage/studio erected (Amish company out of PA.) on my property. 28 x 32 slab, 2 courses of concrete block perimeter. 1st floor framing is 2 x 6, 2nd floor is attic trusses w/14 ‘ open space (7’ ceiling height) the length of the building. I furred out the gable truss triangles on each end to create 2 x 6 bays for insulation.
At this point with all my “stuff” moved in I can’t bring a foam contractor in to shoot 2″ of polyiso in the walls. It would be a nightmare to empty the building at this point. My plan is to use 2″ of fiber-faced (not foil) polyiso foam board in the walls initially, so I can at least work comfortably in the building this winter, and then run all the wiring and then fill the remaining 3 1/2″ with Ruxol or hemp insulation or fiberglass. I’d cut the foam sheets 1/2″ light on all 4 sides and spray foam that 1/2″ gap for an airtight seal. The exterior is sheathed/sided with a one layer T-111 type product which came pre-painted. I’m in zone 6 or 6a in zipcode 12461. These are my questions:
* Is 2 ” of foam correct to abate the dewpoint inside the wall cavity once I have the entire 5 1/2″ filled?
*Is fiber-faced and not foil faced polyiso the correct choice?
*Should I treat the interior side of the sheathing with a vapor retarder or barrier?
* I’m thinking no polyethylene between the wallboard and the insulation to allow for moisture to migrate to the interior. Correct?
* Best technique/product for attaching the polyiso boards to the interior side of the sheathing?
*The top chords of the roof trusses are 2 x 8s. Best way to insulate that area? Pack it with polyiso foam boards (fiber-faced) tight up against the roof sheathing? There is a ridge vent, and ventilated soffits.
GBA Detail Library
A collection of one thousand construction details organized by climate and house part
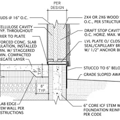
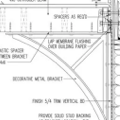
Replies
If you use foil-faced polyiso, then 2" would meet the IRC requirement (at least R-11.25) for using a class III vapor retarder, which can be a coat or two of latex paint. But if you use fiber-faced polyiso, it might be too vapor permeable (> 1.5 perms), so the IRC would require a class II vapor retarder instead. Kraft-faced batts would be a good choice.
Of course, those requirements are for houses occupied by a bunch of people who are cooking and showering. You have more leeway with a typical shop that is occupied only part of the day by one or two people, provided you're not using unvented propane heaters or doing something that puts a lot of moisture in the air.
Since you already have roof vents installed, I'd leave a decent vent space. You could put a 5-1/2" batt in the cavity and attach foil-faced polyiso to the underside of the top chords, taping the seams for air tightness.
I had suggested fiber-faced polyiso in the wall cavity thinking that the foil-faced with foil on both sides might somehow screw up the movement of moisture, but I don't know the mechanics of it and would defer to your recommendation of using foil-faced polyiso. Then does the need for a craft-faced batt to fill the rest of the cavity limit me to fiberglass, or are there other type batt insulations available with craft facing?
Re the 5 1/2" 2nd floor ceiling batts, are you recommending unfaced insulation of any specific type?
And, would 1/2" polyiso boards on the underside of the rafters be adequate, given this space is not a residence?
I assume those plastic air guides in the rafters bays should be used as well to discourage the insulation from laying against the underside of the roof sheathing.
Thank you for the advice on this project.
The foil facers on a piece of polyiso don't cause a problem with a double vapor barrier for the polyiso itself. For the purposes of a wall ASSEMBLY, polyiso is a vapor barrier because of that foil facer. Fiber faced polyiso can be better in some wall assemblies since it is somewhat vapor permeable whereas foil faced polyiso is not, because the foil facer is a good vapor barrier.
If you were to use two sheets of foil faced polyiso with fluffy stuff in between, THEN you could have issues because of the double vapor barrier, but the double vapor barrier in this case would be each of the two SHEETS of polyiso, not the two FACERS on each sheet.
The purpose of vent baffles is to maintain an air space above the insulation and below the roof sheathing. By code, this vent space needs to be at least 1" deep (more is better).
The kraft facer on fiberglass batts is a vapor retarder. In assemblies where a vapor retarder is required, you can still use any kind of unfaced batt (mineral wool, denim, etc.), but you'd need to provide a seperate vapor retarder. This is what I like to do myself: I like to use mineral wool batts in the walls, but I then put a layer of Certainteed's MemBrain, which is a smart vapor retarder, over the inside of the studs behind the drywall. Since the layer of MemBrain is a vapor retarder, you can use unfaced batts in the wall.
Bill
I'm not recommending foil-faced over fiber-faced; either would work fine. They just have different vapor retarder requirements according to the IRC. I haven't heard of any other insulation type coming with Kraft facing, but not even Kraft-faced fiberglass is sold in my area, so I don't know for sure.
If I'm going to make a recommendation, it will be to fill the wall cavities with 5-1/2" batts and then apply polyio in full sheets on the interior of the studs. I think that will take less time than cutting and foaming the pieces in place. A 5-1/2 batt + 1" continuous polyiso will outperform the 2" cut-and-cobble + 3-1/2" batt. Even a 5-1/2" batt + 1/2" polyiso would do better. If the polyiso was foil-faced, it wouldn't need another vapor retarder, and you could tape the seams for a good air barrier. Otherwise, you could install poly sheeting for a vapor barrier and seal the edges for an air barrier.
Any type of batt will work thermally, but a denser batt and stiffer material like mineral wool will be easier to install without falling out right away. Or use Kraft-faced batts so you can staple them in place as you go. A layer of taped foil-faced polyiso underneath would make for a pretty good air barrier. Try to seal around all the truss webs as best as you can, but the vent space will take care of any moist air that does leak through. I can't say how much insulation would be adequate. You'll have to make a judgement call based on how often you'll be using the shop and how much you'll heat it. It would make sense to have the roof R-value be the same or slightly more than the wall R-value.
The roof vent baffles aren't really needed if you're careful not to push the batts in too far and block the vent. With 5-1/2" batts in a 7-1/4" space, that's not likely to happen. I don't really like the plastic baffles because they block vapor movement, and the whole idea of the vent space is to dry out moisture. Supposedly the plastic ones are okay if you leave big gaps between them, but I'd prefer a material that is more vapor open.
Thanks again Frank. Of course if my circumstances were different I would just fill the wall cavity with 5 1/2" of mineral wool, but I don't see being able to run all my electric in the near future, which is why I am choosing to use 2 " of polyiso foam board that will give me some indoor comfort in the winter while I run all my rough -in electrical. Then I can use 3 1/2" of mineral wool to flesh out the wall cavities. It was suggested by another that I use Certainteed's MemBrain behind the Sheetrock.
As regards the insulation for the roof, I like your suggestion of 5 1/2" of mineral wool in those 2 x 8 top chord truss members with a layer of rigid foam polyiso ( 1/2" or 1") on the underside of those 2 x 8 top chords. Am I correct that the foil-faced foam board, taped, would be fine for a vapor retarder in that situation? That combo in the roof batts should bring me close to the R value of the walls, I think, as per your recommendation.
Thanks again,
Al Tirella
Foil faced polyiso is a vapor BARRIER, not RETARDER. It would be fine under the rafters in a vented roof assembly though, and will help limit how much moisture can sneak it's way up into the assembly. I like to tape the seams with Nashua 324A foil tape when doing this.
My preference would be to define the the vent channel with furring strips and 1/4" waferboard though and not rely on the top of the batt. I have found that the top of the batt tends to be irregular when installed, and it's too easy to obstruct the vent channel. Mineral wool should be less of an issue in this regard than fiberglass, but it's still best to have something firm for the batt to press against to ensure the vent channel remains fully open.
BTW, it's not hard to pull out a mineral wool batt to run some electrical cables and then reinstall the batt. I've done that several times myself in the past week or so without issue.
Bill
I missed the part about running the electric in the wall between the two insulation phases. There are a couple of other options you could consider. One is using surface-mounted conduit. Or if you don't like the look of that then you could run most of the wires in the ceiling and drop down the stud bays, minimizing the amount of insulation that has to be pulled out.
It is exceedingly difficult to "drop wire down the stud bays" if they have insulation batts in them. Fishing wires like that tends to snag the batts and pull them in all kinds of directions, and drill bits do the same. You want to be sure to run all your wires prior to installing the batts.
"Surface-mounted conduit" is usually "Wiremold". I've installed miles of that stuff. I will exert extreme amounts of effort to avoid using it.
It's not that difficult to install the wiring prior to insulating. If you can't do everything in the normal sequence, I'd "rough in" the electrical, which is pull the wires in and, ideally, mount the boxes, but leave the final connections and device (plug, switch, etc.) installation for later.
Bill
Yes, the insulation would have to be "pulled out", but only on the bays getting a receptacle. If Al has his electrical layout planned already then doing the rough-in ahead of time does make the most sense.
Deleted
I want to thank both Frank D and Bill Wichers for helping out with navigating the wall and ceiling insulation labyrinth for my project.
I don't want to clog up the airwaves much longer so I will layout what I think I should do for both the vertical wall and ceiling insulation assemblies based on what I learned from you both. The electrical rough in will happen after I install the 2" of polyiso in the wall cavities, so we don't need to be concerned with that anymore.
• Insulation in the top chord of the 2 x 8 roof trusses: 5 1/2" of mineral wool batts. That should leave approx. 1 3/4" of air gap for the venting. Bill, I like the idea of defining that space (you suggested furring strips and 1/4" flake board, but I am concerned about moisture getting trapped between the mineral wool and the underside of the flake board and not being in the rafter vent airflow path to get carried to the ridge vent. I'm leaning towards furring strips and something permeable like nylon screening, or 1/4" hardware cloth to create a 'stop' for the insulation topside. Then on the underside of the rafter chords 1/2" of foil-faced polyiso foam board with all seams taped with foil tape.
•1st floor vertical walls and 2nd floor gable end triangles:
2 coats of latex paint on the interior side of the sheathing /siding combo.
Then 2" of polyiso foam board ( I still need clarification whether to use foil-faced or fiber-faced, and what if anything in this assembly would need to change based on which one I use). Then 3 1/2" of mineral wool batts, then Certainteed MemBrain behind the 5/8" drywall.
Well, I think that's it and hopefully I haven't left anything out.
So it's just those couple of questions above that stand between me and a somewhat comfortable garage/studio/workshop. I'm anxious to get started.
Thanks again guys.
Another potential solution would be:
1. Insulate the existing wall cavity now, with the appropriate insulation. I'm not saying it is correct for your climate, but damp sprayed cellulose would be a nice solution for this situation. This gets the place insulated so you can work all winter.
2. Install 1" furring on the inside face of your framing.
3. Run all your electrical and plumbing using the 1" cavity created by the furring. For electrical boxes, run the Romex into it and seal the backside with putty pads before carefully carving out a bit of the cellulose and attaching the box to the studs.
4. Take MANY photos of where you run the electrical and plumbing because it won't be protected by metal plates and you will want to know where it is in the wall...there may be other, better solutions for dealing with this.
5. You could do a 2nd application of spray cellulose for an insulated thermal break before installing the gyp. This would also repair any places where you carved out the cellulose to install the electrical.
The benefit of the above is there is much less labor than the cut & cobble of the rigid insulation, and you get a thermal break at the framing.