Humidity management and wall/roof/floor insulation details

Hello and thanks in advance for your advice. This is an extension of an earlier thread on perm ratings.
The build site on the Big Island of Hawaii is at 4000′ elevation in a “nano-climate” cloud forest. See the attached JPG for stats on the typical day – high of 73-75, low of 55-57, with humidity ranging from 65% to 100%. Record lows can get down to 40 degrees F. Thermally, this is a very benign environment with little change across the seasons. No big R values needed here… let’s do big windows instead!
There are few houses in this specific area, and none that have really been impartially evaluated in any way. Meaning, just because the neighbor built a certain way – doesn’t mean that is an existence proof and I should copy it. Most of the construction in this region happens at a much lower/dryer/hotter elevation, so there is not a lot of local expertise to draw on for my build.
We will build with 2×6 framing, and pressure-treated plywood sheathing. It will be off-grid, so we need to be conscious of the ongoing cost of dehumidification. Proper air sealing is, of course, paramount.
My questions all revolve around sealing up the house against the humidity and managing any condensation risk. I’m going to probably break this subject into separate questions to focus on just one variable at a time.
With all the backstory behind us then, the first question is whether condensation is a significant risk or not.
Assuming we don’t do closed cell foam in$$ulation, the first condensing surface will be on the inside of the plywood sheathing. The condensation charts suggest that if the interior of my sheathing gets to 40 degrees, then to prevent condensation (with an interior temperature of 70 degrees), I’ll need to dehumidify to around 35% – on these exceptionally cold and relatively rare days, at least. For a typical day around 55 degrees, I’d only need to get to around 60% RH.
From my experience with occasional VRBO stays in the region, I am confident that I can affordably get to 60%. I’m not as sure about 35%. What if I don’t make so much PV power on those days, and only get to 50% RH?? I can always fire up the generator and burn gasoline/propane, but I’d prefer not.
It would greatly simplify construction and minimize costs if I could avoid any exterior foam sheet insulation, outside of the sheathing and behind the siding. And this insulation challenge is multiplied when you consider the underside of the pier/post area and the roof.
Wouldn’t it be nice if I could just “paint” the entire exterior envelope – the outside of plywood sheathing, top of roof sheathing, and underside of any T&G plywood flooring with a vapor barrier like Prosoco’s R-Guard VB. It’s all highly visible, and we could focus all our efforts on a high quality air/vapor seal. Anything inboard of this layer would dry to the inside.
I tend to think that this is the best solution, but I guess the big question is the decomposition risk of
“occasional” condensation on the inside of the sheathing, should I fail to hit my goal of 35% RH and end up at 50% for a couple days a year. The cellulose insulation would act as a bit of a buffer, absorbing to some degree any liquid water.
Am I insane for thinking I can pull this off?
Sincere thanks, Mark
GBA Detail Library
A collection of one thousand construction details organized by climate and house part
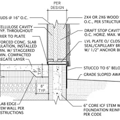
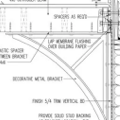
Replies
Mark,
You raise some interesting questions. My first reaction is, "Are you sure that you need space conditioning?"
For thousands of years, humans have lived in benign climates like the one you describe without any heating, air conditioning, or dehumidification. Especially since this house is off-grid -- why not try just living in it for a few years without any conditioning? Open the windows when you feel like it. Close the windows when you feel like it. Turn on a ceiling fan when you feel like it. I think that the house should operate just fine under those conditions.
Martin, thanks for your thoughts. In fact, I plan to build with no heating or cooling, save for a wood burning stove for the coldest days. But the humidity... that has to be managed. if you stay above 70%, you get all kinds of things growing that folks have put up with for thousands of years, but we're not OK with that. So, a whole house mainland style HVAC system, just injecting source air into wet areas and closets, instead of a curtain by windows. In fact, the more we dehumidify, the more we manage my concern about any condensation on the interior of the sheathing. Also, if i guess wrong, with a full HVAC system, I can always add supplemental heating/cooling as needed.
I'm pleased that my proposed approach has not triggered any huge concerns yet.
Anybody else see anything that they're uncomfortable with in my plan?
Thanks again, Mark
Mark,
The key to avoiding mold in a hot, humid climate is air circulation. (If you don't have air conditioning, you won't have cold surfaces, so mold and condensation are less likely to occur.) My guess is that louvered doors on your closets, and the occasional use of a fan, is all you need.
Martin, good point, Perhaps with my HVAC scheme, I can occasionally get away with just air circulation and save energy on dehumidification. There is however also the subjective comfort angle of a drier house. But I like your fallback position for when I might not be making as much PV power - just circulate the air.
Jon, excellent point about the interior of the sheathing being a bit higher than the outside temp - that certainly helps. The idea of heating the air and getting the natural reduction in RH is solid math, but its probably more expensive to heat the air (after a full air exchange) than it is to dehumidify it. But it raises a good point... that wood burning stove, combined with additional outside air, would tend to mitigate the risk of condensation on the cold days. Very much appreciate your thoughts on this.
> interior of my sheathing gets to 40 degrees...I'll need to dehumidify to around 35%
The interior side of your plywood will be warmer than 40F when it's 40F outside. How much depends on other insulation. Even warmer if the 40F doesn't last too long.
Unless you add moisture, the interior dew point (not %RH) will track the outdoor dew point. Say it's 40F outside with 100% humidity. Heat the air to 70F and it will automatically be ~35% RH - without dehumidification.
The bigger concern is warm weather - eg 70F and 90% RH for a week. That's when you need dehumidification. But it won't help the exterior side.
I expect that painting all wood surfaces with vapor retarding, mildew resistant paint would help in such a climate. See below for why porous surfaces are bad:
https://buildingscience.com/documents/building-science-insights/bsi-099-its-all-relative