Huber Zip R-Sheathing with open cell insulation

I’m involved on a project where the insulation contractor would like to use closed cell spray foam insulation in our wall cavity in order to mitigate the risk of condensation. We were originally planning on using open cell foam. Climate zone is 5/4 Marine, project is on the coast.
The wall assembly is ;
– 1-1/2″ Huber Zip R-Sheathing
– 2×6 stud wall
– 5-1/2″ open cell spray foam insulation
– 1/2″ drywall
1. Are we at risk of condensation in our wall if we use the open cell insulation?
2. Would adding 1″ of closed cell spray foam mitigate the risk? We would then use 4-1/2″ of open cell to fill the cavity.
3. Is the ratio of rigid insulation to open cell insulation in the cavity acceptable?
Thank you!
GBA Detail Library
A collection of one thousand construction details organized by climate and house part
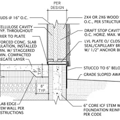
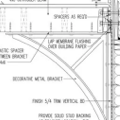
Replies
As long is the siding is mounted rainscreen style, with a vented air space (3/8" minimum) between the ZIP and the siding (or if it's inherently back-ventilated, such as vinyl siding) the assembly can use standard latex on drywall as the vapor retarder in marine zones 4 & 5.
Without the vented siding would take less than an inch of closed cell foam to provide sufficient dew point control for 4.5" of open cell foam in zone 4, and would be plenty in zone 5. But installing a 2-mil nylon smart vapor retarder under the wallboard with 5.5" of open cell foam would be cheaper, and at least as effective.
Installing an inch of foam (any type) on the exterior would be cheaper than an inch of closed cell foam, and would be sufficient dew point control for zone 4, and maybe zone 5 too, but the 2-mil nylon would be cheap insurance in marine zone 5. (In zone 5A & 5B you'd really need 2" of exterior foam to get by without the vapor retarder, but in 5C it might be enough. The specific local climate averages matter if you want to do it with just an inch of exterior foam and no interior side vapor retarder.)
Dana. Just to clarify, you are advising SG to skip the closed cell and just use open cell in combination with 2-mil nylon, correct? Wouldn't it be cheaper still to use dense-packed cellulose, assuming the ZIP is taped and detailed correctly?
Thanks, Dana. The project is located in Little Compton, RI - 02837.
We are using a 3/8" rainscreen so we're all set there.
I too would like to clarify, is the 1" of rigid insulation on the 1-1/2" Zip R Sheathing the 1" of insulation you are referring to or would we need an additional 1" of insulation? The sheathing is already installed.
Yes, skip the closed cell, go with the 2-mil nylon vapor retarder or a similar "smart" vapor retarder.
Half pound open cell foam is usually cheaper than dense packed cellulose in my neighborhood, but usually more expensive than damp sprayed cellulose. YMMV It wouldn't be insane to get it quoted several ways, since the performance will be about the same.
Cellulose is definitely "greener" from a total environmental impact point of view, but a full 5.5" of half pound open cell foam has less overall impact than an inch of closed cell foam blown with HFC245fa (the current industry standard.) Open cell foam is blown with water, and has about half the polymer per R of closed cell foam. The thermal bridging of the studs undercuts the additional performance of the higher R of that 1" of closed cell foam to negligible levels from a whole-wall R perspective (on the order of ~R0.5 net improvement.)
Back-ventilated siding is highly recommended in any marine zone climate, or in any zone 5 climate, with or without interior vapor retarders. With back ventilated siding you can safely skip the vapor retarder even in zone 5, but with a different siding configuration the vapor retarder would be mandatory in zone 5, and a good idea in zone 4.
I believe rainscreen construction AND vapor retarders are required by code in western British Columbia. Anything under 1 US perm meets the code definition of "vapour barrier" under Canadian codes, and 2 mil nylon meets that spec. But unlike 4-6 mil polyethylene, it becomes vapor open if the air in the cavity becomes humid enough to support mold, which allows the assembly to dry toward the interior if it ever needed to.