How would you spend $40,000?

Hi GreenBuildingAdvisor community – I’ve been reading off and on for the past 12 months as we gear up to build our home. It’s simulatneously depressing and empowering to read through how much is required to properly build a home.
We’re pretty happy with the plans (the ones I’m including are not quite the latest – we’ll be adding a few windows and moving some interior walls around) but before we do the next round of changes – we need to make a decision about ICF or no ICF. It’s a $40,000 question for us.
So the question I’d like to share with you is – how would you spend $40,000? Would you do ICF and stick with all the other items that are specified as is? Or would you drop ICF and put $40,000 into other items? For each area – I have put down what is in the builder’s specifications now and what the alternate is (though there’s nothing limiting for alternative – it’s just what I have in mind now).
Thoughts?
Overall
– New, single family home
– Family – 2 adults, 5 children (11 years to infant)
– I work from home (I’ll take the attic office) and wife teaches music lessons from home
– Moving next to parents, intend to live out our years in this home
– Location: Leesburg, Virginia 20175 Zone 4: http://d.pr/i/1c4ww
– Lot is on pretty steep grade; 100% covered in trees right now
– No access to natural gas
– Planning on propane for cooking only
– Will install a Jotul F 500 http://jotul.com/us/products/stoves/jotul-f-500-oslo in family room (no outside air kit specified)
– Using town water/sewer
– 9 ft ceilings on all floors. No tall ceilings anywhere.
– Mostly Hardy Siding. Brick in some places.
Plans
See attached images for the floor plans/elevations. The sq feet below are estimates – I was using PlanGrid to measure.
– Basement (total) sq ft: 1,780
– Basement (finishing now) sq ft: 512
– Main level sq ft: 1,780
– Bedroom level sq ft: 1,780
– Attic sq ft: 180
– Total sq ft (finishing now): 4,252 sq ft
– Total sq ft (when basement finished including mechanical): 5,520 sq ft
Basement
– Specified: No slab insulation
– Alternate: ?
Basement walls
– Specified: Poured foundation + 2 inches Thermax (I believe R-13)
– Alternate: ICF Fox Blocks – foam on each side is 2.625″
Above grade walls
– Specified: R15 on 2×4 framed wall
– Alternate: ICF Fox Blocks – foam on each side is 2.625″
Attic
– Specified: Blown cellulose – burying the HVAC ducts
– Alternate: Condition the attic
Windows
– Specified: Andersen 400
– Alternate: Save money with Andersen 200 or go up to an Intus (just an example) ($ not known)
HVAC
– Specified: 2 zones heating/cooling with an air source heat pump. Right now spec’d for a code minimum HVAC.
– Alternate: VRF (Carrier Greenspeed or a Mitsubishi)
– Alternate: Not VRF but improved SEER than current specified
Ventilation
– Specified:
– No HRV
– Ceiling fans in attic office and bedrooms
– regular bath fans venting out roof
– Hood fan: Zephyr (400-600 CFM)
– Alternate:
– HRV: Venmar HRV ($ not known).
– Interested in not having separate bath fans. Builder not sure about this (humidity exhaust).
– Hood fan: lower CFM fan than specified (200-300)
Hot Water
– Specified: electric 80 gallon water heater
– Alternates:
– Heat Pump Water Heater 80 Gallon
– D’mand hot water recirculator
– EcoDrain (drain line heat exchanger). All three showers and upstairs sinks connect.
GBA Detail Library
A collection of one thousand construction details organized by climate and house part
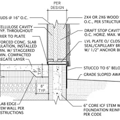
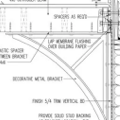
Replies
Dial it back, Sonny! Let's stick to construction issues, please.
Adam,
You mention that your above-grade walls will be 2x4 walls insulated to R-13. (You didn't tell us what type of insulation you will use.) Is that even legal?
According to the 2012 IRC, a house in Climate Zone 4 needs R-20 wall insulation (or R-13 cavity plus R-5 continuous).
Martin,
My builder specified R15 for the above grade walls. I'd have to check on local code to answer the legal question. He planning to use 3-3.5 inches of open cell foam on the inside.
R-20 does seem like closer to what we should be aiming for.
Comments removed. It's still too early for wide acceptance of reality.
Sonny,
To answer your question - I suppose our tactical goals at this point are to increase the R values in the right places with the budget we have and keep it comfortable. Since we plan to live in this home a very long time - we'd like to reduce the amount of energy expenses long term. But from what I've read - return on investment calculations usually point to living in a tent.
I'll add that we've looked at adding PV to the roof - I should have the assessment back later this week - but I don't expect it to come back too favorably considering the location (shading). But we'll see.
The ICF wall is a high performance wall for your climate zone at about R23-R25 "whole wall R". It's also fairly ruggedized against hurricanes, if that's something you're willing to pay extra for. It is a sufficiently high performance wall in your climate that given sufficient performance on the rest of the house could hit Net Zero Energy with a PV array that fits on the roof.
Is the alternate wall R15 between 2x4s or R15 continuous sheathing over a 2x4/R13 type of wall? R15 between studs would come in at about R11 whole-wall, whereas R15 sheathing over 2x4/R13 is about R25 whole wall. That's a big difference, both in performance and cost. The 2x4/R13 + R15c.i. solution is also Net Zero worthy in your climate. A 2x4/R15 wall would be below IRC 2015 code min.
A GreenSpeed has a very limited modulation range which makes it difficult to size optimally for both heating and cooling, and they're expensive. You'll have more flexibility and lower up front cost with a Mitsubishi solution, but you can't really pick the solution just yet,since you havent' run the heat load numbers. Without the load numbers you can't even spec the code-min solution. A perfectly sized GreenSpeed can hit it's numbers if you keep the ducts inside of conditioned space, but an optimally sized Mitsubishi can sometimes beat it's numbers. An oversized GreenSpeed or Mitsubishi would be waste, since it wouldn't modulate much, but the wider modulation range of the Mitsubishi gives it a chance.
You have a basement for running ducts for the first floor level. Building a ceiling service chase under the insulation for the upper floor is more efficient than burying ducts in cellulose (which during the cooling season could end up with wet cellulose).
With the + shaped topology have 12 thermally bridging corners to deal with (not counting the bump out for the Jøtul). Try to reduce the footprint to no more than 8 (a T topology) or better yet 6 (an L topology).
Move the chimney to somewhere the center of the house, not the side. That will optimize the draft quality and heating functionality of the Jøtul. by putting it where it will heat the place more evenly. (Exterior chimneys are the WORST!)
Put 1.5-2" of EPS (R6.3- R8.4) under the slab, continuous with the interior EPS of the ICF. If not ICF, isolate the slab from from the foundation walls with 2" EPS that extends a few inches up the foundation wall before continuing with the 2" polyiso. Sub-slab foam fixes "musty basement smell", and mold issues in rugs or boxes resting on the floor. If you skip it, you'll probably regret it later. There is an energy benefit too, but the real reason is to make it a livable not-moldy space.
If the propane is for cooking only, you might be just as happy or happier with an induction range and electric oven. Induction ranges don't put out combustion products into the air until you burn something, and the cooktop surface itself doesn't get hot- the pans do. They're VERY easy to clean, and are far more efficient and responsive to control settings than old school electric ranges.
As drawn, you're on the south facing pitch of the hill, and there is both a south facing gable and a chimney on the southern exposure. If that side was a shed dormer instead of a gable end you would potentially have space for a decent amount of solar PV if you moved the chimney to the north side of the main ridge. A simpler shape with a single south facing roof pitch would give you even more space. At the 40 year learning curve and current installation rates, before 2030 PV will be the cheapest form of energy, bar none. Rooftop PV will still be more expensive than utility scale PV, but it'll be much cheaper than retail electricity. Even if you don't build out the solar today, new construction designed to be "Solar Ready" is a good idea (even mandated for new construction in some places.) This includes designing the roof with sufficient load capacity, and some amount of wiring (or pre-installed conduit for running wiring later.)
Adam,
$40,000 seems like a lot to spend for the advantages of ICFs. If you decide to spend the $40,000 on energy upgrades, start by developing an airtightness plan -- and, ideally, by introducing a binding airtightness goal that your builder will meet and verify with a blower-door test.
Thank you Dana.
"whole wall R"
I'll read up on this.
"Is the alternate wall R15 between 2x4s or R15 continuous sheathing over a 2x4/R13 type of wall?"
Will investigate.
"Building a ceiling service chase under the insulation for the upper floor is more efficient than burying ducts in cellulose"
In this case (building a ceiling service chase on upper floor) - what insulation would you recommend? My builder originally had talked about doing a couple inches of closed cell foam in the attic.
I'll see what we can do about bringing the chimney inside. Are exterior chimneys the worst because they are a giant thermal bridge? Or because there is a lot of wasted heat during the winter?
Re: induction cooking - I'm all for it. I'll try talking my wife into it again. The oven we've picked out is electric. So we're really down to the stove.
For PV - we'll take a look at making that south facing roof more solar friendly.
Any thoughts on water heating?
If this is a "lifetime" house, ICFs are sort of a no brainer. Over the years, they'll save a tremendous amount of money compared to stick framing due to their inherently better durability, moisture resistance, airtightness, heat transfer performance, etc.
If you're hoping to save $40,000 somewhere, I know this isn't often a popular line of discussion, but have you considered downsizing the house a bit? at $100/sf, you can go with ICFs and still save that much just by removing 400 square feet, which only about a 7% reduction in square footage. I know you have 5 kids (congrats) and both work from home (congrats again!), but your current plan amounts to 788 square foot per person, which is quite a large number. I have a 4 person family in my 1300 square foot ranch, for a total of 325 square foot per person, less than half what you're budgeting for. I'm currently typing this from my home office, which is actually my master bedroom (it was unused during the day, so there was no reason to have a separate office room, I reasoned).
In no way do I mean this as a criticism of you or your plans; I'm only trying to point out that it may be possible to have a house that's just as delightful and meets your needs and wants just as well, but is 400 square feet smaller.
With a budget that is not unlimited, square footage is something consequential that you can reduce just a little bit to save a lot of money, especially in a big house like this. A small reduction will yield a big savings, and then you can use the higher-quality materials you're interested in.
I'll second Dana's recommendation for an induction range. I converted from gas and love mine.
Martin -
$40k for ICF does seem like a lot. I like Dana's comment about R15 sheathing over the currently proposed wall. I don't know what that would cost - but if it could get me close to the same R as an ICF wall, then I think I have my answer.
Regarding air tightness - I see "0.6 ach50" mentioned in Martins Pretty Good House Manifesto. Is that a reasonable target for a new home construction - whether we go with ICF or the more traditional approach?
On the easier to build front...
A 2x6/R20 cavity fill wall with 1.5" ZIP-R comes in at a respectable R20+ whole-wall after factoring in the thermal bridging, and won't require training unfamiliar crews on the art of exterior foam. The R20 cavity fill can be open cell foam, wet sprayed cellulose, (or even batts if your air sealing and batt installation crews are obsessive about it.) That would underperform the ICF by a bit, but it might give you the budget to upgrade the windows to more than make up the difference.
Windows in the U0.24-U0.28 range would be more comfortable in winter than a code-max U0.035. A U0.26-ish window with an SHGC of 0.35 or a bit higher for all windows except the west side would be close to optimal. This shouldn't be too expensive to hit. You can get there with Anderson 400s, but there may be better bang per buck options out there.
Closed cell foam in the attic floor is a waste of foam, and 2" is twice too much. You don't need foam to air seal an attic floor, and the $2 per square foot for that R12-R13 would buy about R40-R50 worth of cellulose. Designing for R55-R60 open blown cellulose would be the best bang per buck, (and about right if you had Net Zero dreams) and takes 18" of depth, and weighs close to 2lbs per square foot. That's not a problem if it's supported by joists 16"o.c. but has to be factored into trussed roof designs. If you framed the upper floor a foot taller to accomodated a service chase, ring-shank nailing OSB to the bottom of the joists can be easily air sealed, and would support even R80 cellulose, no problem. You'd then install lighter framing below to support the ceiling under the service chase. This is a cost adder, but it puts all of the mechanicals inside of conditioned space, with far fewer penetrations of the pressure barrier (the OSB air barrier.)
Heating hot water in that climate with a heat pump water heater is a good idea. A heat pump water heater removes heat and humidity from the air, which limits the mold levels in the basement (assuming that's where you'd put it.) The a 4" x 48" or taller drainwater heat exchanger is a good idea for a showering family, even more so if using a water heater that has a slow recovery rate. The biggest Eco Innovation EcoDrain is the TD472B, a 4" x 72" that delivers nearly 60% return efficiency , but there are bigger Renewbility PowerPipe versions that do even better. The tallest and fattest one that fits is the "right" one, since the addition up front cost is more than made up for by the higher recovery efficiency. With 9' ceilings and a 2x10 joist you can probably fit a 4" x 96" in there. An R4-96 PowerPipe delivers close to 70% return efficiency @ 2.5gpm. See the attached copy of the apples-to-apples third party tested list of drainwater heat recovery models maintained by Natural Resources Canada.
Dana -
I'll take a look at those drainwater heat recovery models you mentioned.
I like the idea of just putting a bunch of cellulose in the attic. I'll have to read up on how to air seal the attic correctly.
Question - with the office up in the attic - how would you insulate the office walls? And above the office?
Oh - and if the second HVAC unit is up in the attic - isn't it a no-no to have it in an unconditioned space?
@Martin -
In https://www.greenbuildingadvisor.com/blogs/dept/musings/ten-ways-improve-new-home you said (it's been a few years now...):
"if you only reduce your air leakage rate down to 1.6 or 1.8 ac/h @ 50 Pa, your house will still be significantly tighter than most new homes."
Is 1.6 ac/h @ 50 Pa the air tightness I can reasonably aim for?
Adam- I'd aim for much better than 1.6ach50. This is a new house and should be very well air sealed. I'm just guessing, but I bet this house will cost well north of $1 million. For that sort of money, your builder should be fine with setting a contractual air sealing target. But, as was pointed out above, all those corners make air sealing more difficult, as well as more expensive.
Dana, you mention an attached copy of drainwater heat recovery data. I don't see an attachment. I am considering DWHR and have been looking for data.
Adam,
Ideally, you will contract with a builder who is familiar with air-sealing details, and has already build several homes that were tested with a blower door. Unless a builder has seen the results of blower door tests, I wouldn't trust the promises of the builder.
In your climate zone, the 2012 IRC requires that homes have an air leakage rate of 3 ach50 or less. Any leakier, and the home is illegal.
Hitting 0.6 ach50 may be tough for your design, because your design has multiple gables, bump-outs, and an exterior chimney -- in other words, it shows all the usual signs of being designed by someone who doesn't care much about energy efficiency. It's easier to hit 0.6 ach50 with a more compact design.
I don't see why you couldn't hit 1.0 or 1.5 ach50 -- but you need to hire a builder with a track record of blower door tests.
Adam: Keep all HVAC equipment inside the pressure and thermal boundary of the house. The size of the HVAC needed to serve just the upper floor is a lot tinier than you might think. If you don't go crazy on west facing windows you'd probably be able to serve the entire bedroom level with a single 1-ton (1.5 ton max) mini-duct cassette unit. A mini-duct cassette can be installed in a 12" deep ceiling sevice cavity.
http://www.acdirect.com/media/catalog/files/Specs-SEZKD12.pdf
It can either be a separate unit (recommended, for efficiency) or a multi-split (if that makes the whole system cheaper or easier- usually not.) The air handlers in the Mitsubishi mini-duct cassettes aren't as beefy as the Fujtisus, but they're not terrible. The Fujitsu units can be installed vertically (say, in a compartment at the back of a closet, for easy service access), but the Mitsubishi's must be horizontal.
http://www.fujitsugeneral.com/PDF_06/Submittals/12RLFCD%20Submittal.pdf
Build out the office/storage attic walls to the same R value as the exterior walls. Take pains to make it air-tight with the rest of the conditioned space. Shoot for at least R40 in the ceiling of the attic room- 11-12" of cellulose above. The ceiling joists can probably be 2x6s- build up the exterior side framing to at least a foot above the ceiling level to accommodate that, burying the ceiling joists. (Without a dimensioned drawing it's hard to say how easy or hard that would be as currently designed.) The mini-attic space above the attic rooms should have good air access to the areas behind the kneewalls.
Reid: I should have checked to see if the drainwater heat exchanger attachment made it ( apparently not!?!) I don't have a copy of it on this machine (and I won't clutter this machine up by downloading it here either.) It can be downloaded directly from NRCan here:
http://oee.nrcan.gc.ca/pml-lmp/index.cfm?action=app.download-telecharger&appliance=DWHR
You can also search the NRCan listed drainwater heat exchanger list by various parameters here:
http://oee.nrcan.gc.ca/pml-lmp/index.cfm?language_langue=en&action=app%2Esearch-recherche&appliance=DWHR&attr=0
Adam,
While my house is very different than yours, I can identify with your quest to learn about and incorporate energy efficient building techniques into your home. There is a lot to learn on GBA and the people here can give you tons of good advice on everything from the overall design of your home to detailed HVAC specs. I'm just pointing this out to help you, but I think you face some challenges (that can be overcome):
it will be hard for you to absorb, process, and incorporate all this advice...certainly once construction starts and things move fast
the above will be magnified if your architect and/or builder aren't knowledgeable about energy efficient building, especially if they aren't open to major change
I/we may be wrong, but based on the initial design and specs, it's possible they aren't up to speed on energy efficient building
Whether for environmental or financial reasons, it sounds like you're open to making the home more energy efficient...which can also mean a healthier, more comfortable, and better built home. Since you're spending a lot of money and will live in the home long term, I'd highly recommend seeking out some kind of consultant to help you and your contractors. I think the money spent on this will pay for itself.
Some initial options would be to look into the Energy Star program (https://www.energystar.gov) or find a home energy rater/auditor/consultant (http://www.resnet.us/directory/search or http://www.bpihomeowner.org/find-a-contractor). While you may not want the house to be anywhere near passive house or net zero levels, seeking out consultants in those fields can also be a good start.
Other links/resources to get you started that I found through a search:
https://think-little.com/home/
http://leap-va.org
http://www.reauditors.com
http://greenhaus.wpengine.com/consulting-work/
Hope this helps.
Follow up question regarding the attic insulation. We need to be able to put a heat pump and the ERV in the attic. The builder plans to build an "insulated, conditioned box" around the heat pump and ERV. The ducting would then be buried under cellulose per: http://buildingscience.com/documents/building-science-insights/bsi-094-no-sweat and possibly cover the ducting in spray foam as seen in http://buildingscience.com/documents/insights/bsi-074-duct-dynasty
I know ducting in the attic is less than ideal - but I'd really like to keep the ducting simple - which we can do if it is up in the attic.
One thing to remember is that there is an attic office at the front of the office. If we went with cellulose in the attic - we'd plan to use spray foam around the office. This complicates the insulation in the attic...
The alternative that I'm favoring is a conditioned attic. I'm looking at about 2 inches of closed cell spray foam - but then need to decide how to get from the ~R-12 to R-60.
What would you recommend to go the rest of the way for a conditioned attic?
- Flash and batt?
- Can you put open cell foam under the closed cell?
- Another method?
Are you working with a designer? If so does that person have any experience with energy efficient construction?
I think ICF's are almost always not worth the money.
Are you SURE the $40k is an apples to apples comparison for the ICF vs stick frame? How did you come up with that figure?
Remember, with ICF you get the structural, framing, sheathing, vapor/air barrier, exterior insulation, interior insulation, ready for stucco/siding and drywall. Now take that and calculate the costs of wood/stick framing and then add all the above to that wall assembly. I REALLY think your $40k difference will actually drop down to around $20k +/-.
You mentioned Intus Windows. Did you get a quote for the triple pane windows? Just contact the rep in your area and they can give you a proposal.
Instead of guesstimating, get actual quotes.
Adam,
Q. "The alternative that I'm favoring is a conditioned attic. I'm looking at about 2 inches of closed cell spray foam - but then need to decide how to get from the ~R-12 to R-60."
A. According to building codes and building scientists, you need more than R-12 of vapor-impermeable insulation (closed-cell spray foam) to protect your roof sheathing from moisture problems in Climate Zone 4A. The code calls a minimum of R-15 for the spray foam layer.
If you increase the spray foam thickness to 2.5 or 3 inches, your plan can work. Once the closed-cell spray foam has cured, you can add air-permeable (fluffy) insulation to reach R-60. Lots of different insulation material will work, including cellulose, mineral wool, and fiberglass. Make sure that the fluffy insulation is in direct contact with the cured spray foam.
For more information on this work, see these two articles:
Creating a Conditioned Attic
How to Build an Insulated Cathedral Ceiling
@Martin -
I like that 3" of ccSPF. I've read the two articles provided and the thing I can't wrap my head around is how to get the "fluffy" insulation to be in contact with the cured spray foam? Do build a cavity and then spray in the fluffy insulation?
Adam,
I'd like to take the opportunity to repeat Brian P's advice in Comment #19: Your project would benefit from an energy consultant.
The usual method is to furr out the rafters (for example, by scabbing on framing members attached with plywood gussets) to create the rafter depth needed to hold the necessary insulation. The bottom of this furred-out framing cavity needs to be enclosed with drywall, OSB, or a membrane like InsulWeb. This creates a cavity of the proper depth to hold the insulation.
A discussion of this issue can be found in one of the articles I linked to (How to Build an Insulated Cathedral Ceiling). The advice can be found in the paragraphs that follow the heading, "Are my rafters deep enough?"
Martin -
I totally understand the advice to seek out an energy consultant. Even if we do - I want to investigate as much as I can and understand what is being proposed.
Thank you for these responses. It's a great resource even for noobs like myself.
If it's going to be R60 total instead of R49, the closed cell foam has to be a minimum of R18.36 to keep the same ratio. The ratio is what determines the average temperature and moisture content of the roof deck.
Putting 4" of polyiso above the roof deck with R35-ish fiber below would probably be cheaper than 3" of closed cell spray polyurethane foam (ccSPF) under the roof deck, and it would be higher performance due to the R20+ thermal break over the rafters. And unless the ccSPF is the water blown goods from Aloha Energy or the HFO blown stuff from LaPolla, it will have a hefty greenhouse gas footprint from the HFC245fa blowing agent (~1000x CO2 @ 100 years) , whereas polyiso is blown with pentane (~7x CO2).
Any of these solutions are quite a bit more expensive than R60 fluff on the attic floor, probably more expensive than building an air tight platform chamber to house the ducts & air handler.
Dana,
Good catch on the R-60 vs. R-49 issue.
Adam,
To read more about the issue that Dana is talking about, see Combining Exterior Rigid Foam With Fluffy Insulation.