How to work with a developer to target lower infiltration rates in a multi-family project?

nick_vk
| Posted in General Questions on
I’m a member of an LLC that is well on the way to creating a multifamily housing project for our future residences (a cohousing project) in climate zone 4b. We are working with a local green-leaning developer who is bringing his own architect and will be hiring and overseeing a residential building contractor. We really like the developer/architect team and think they are our best option to complete the project. Due to post-COVID building prices and our group’s financial limitations, the developer’s initial proposal is a code-minimum conventionally-framed stick build with no exterior insulation targeting an ACH(50) of 5.0. Our group can live with code-minimum generally but I still hold out hope that we can get to a much lower air infiltration value without a huge cost increase.
From what I’ve read here I have the impression that the biggest cost of lowering infiltration rates is labor and attention to detail. If the air control layer is well-designed and construction can be paused for air-sealing work, could a dedicated team of owners can hire a blower door tester and do a few test/reseal/test cycles ourselves, thereby making up for any inexperience or lack of diligence on the part of the builder? And if that’s not realistic to do with 25 units, would it make more sense to look at the added cost at hiring an air sealing contractor?
Looking for advice about how to best approach the developer about this.
GBA Detail Library
A collection of one thousand construction details organized by climate and house part
Search and download construction details
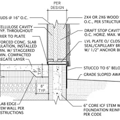
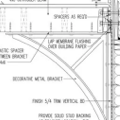
Replies
5 ACH 50 is an appallingly high amount of air leakage. Without knowing how big a unit is 5 ACH50 seems likely to be about 24” x 24” opening in each and every unit. The 5 ACH number is not a goal it is an unmissable bit of boiler plate for the contract.
Code minimum varies from location to location If your local code has been kept to date it may well be R42 attic and R24 walls. More likely it is 25 years behind the times and requires R19 attic and R4 walls.
Make them list the R values don’t let them hide behind the outdated local code.
What is the point of your foundation if you are going to build the worst building allowed by law AKA code minimum?
Walta
Thanks for your reply Walta. This project started more than 5 years ago and was going to be built at or near Passivehaus standards. The group got its first bids in early 2021, just after lumber skyrocketed, and the bids came in 30% higher than initially projected. We've been lowering our standards ever since to try to keep the project affordable for most of the group.
Our jurisdiction is using the 2018 IECC standards, so code minimum is R49 in the roof, R20 in the walls. Martin Holladay makes the case on this site that "Code Minimum is the New Green" basically because we can't afford to burn the extra carbon now to ideal buildings for the future . But making the buildings tighter isn't going to increase the carbon footprint the same way that adding 2 inches of exterior foam would. so that seems like the place to focus.
Have you gotten recent bids? I know lumber costs have come down but interest rates have skyrocketed. I disagree with Martin strongly on "Code Minimum is the New Green" and I know a number of other architects and buildings in the high-performance building space disagree. Insulation isn't something that often gets changed during a remodel and it is cheaper and less carbon intensive to install better insulation now then it is in the future. Also his article ignores the massive benefits of reduced HVAC sizing and thus refrigerant quantities in well insulated buildings. The carbon footprint of refrigerants is massive and reducing your HVAC system by at least 1 ton saves enough carbon to offset the impact of the additional insulation (you can analyze your project for yourself using this great tool that Skylar Swinford put together: https://passivehouseaccelerator.com/articles/now-available-beta-version-of-ocec-tool-developed-by-skylar-swinford )
You are on the right track with asking for better air tightness than 5 ACH50, which is horrible. It is easy to get to 3 or below these days without much effort and getting lower isn't a big ask, especially on larger multifamily buildings (with exceptions due to stuff like elevator and stair pressurization). If you go with an exterior sheathing system with integral WRB and warranty required seam sealing, ie ZIP system or Denselement, then it's even easier as long as the penetrations and openings are properly flashed and sealed.
Have you looked into using prefab wall panels or more modular type of construction? This is one way to get increased performance at a lower cost since it reduces on-site labor and time, thus lowering mobilization costs.
Another option would be looking at funding from sources like the IRA, state, county, and utility incentives for energy efficient construction to offset the costs. Also some lenders have lower interest construction loans for green projects. Some cities also provide permitting incentives for green building that can save permit costs or time on reviews.
If you and the rest of the owners had a goal of Passive House at the start, I think you all will be less than happy with the result if you go all the way down to code minimums. I would spend the time to research and exhaust all possible resources and avenues for finding cost savings and funding sources that will let you at least build a "pretty good" multifamily project if not full passive house.
Thank you. The discussion between the two viewpoints represented by Skylar and Martin is fascinating and important. In our situation, even with lumber prices down, we have members on the bubble of being able to afford the project, so it's hard to ask them to invest more upfront. (Maybe we can get creative and have members who are more flush finance the energy improvements for everyone and get paid back in savings on each member's utility bills.) And of course lowering the size of the HVAC system can offset insulation cost. Unfortunately exterior insulation is not standard practice here so builders are less familiar with it.
In looking around for an Aeroseal contractor I ran across the 25L and 45L credits that builders can claim, so will be diving into that.
In an ideal world, we could find a builder that would welcome the chance to train his crew on air sealing, especially if we provided the HERS rater and the training. In our area the proof that you can achieve low ACH(50) values might be a real differentiator.
Your idea to have some of the members finance the energy improvements and get paid back on the savings is a novel one and a great creative potential solution to fund a better built project. There could be similar ways to leverage the unequal initial funds and amortize the payback once the project is built across the members so that the ones who put in more upfront capital cost have the security to know that they will get some of their money back. I think it will depend on the members and what each of their priorities are as there could be options to just invest the extra capital and only reap the benefits of lower energy bills, or balance the investments between everyone at a slow rate by tacking on a monthly fee to those who put in less capital, which then gets distributed to the members who fronted more money (ideally everyone would end up on a level total investment if that is desirable). Or if you can also put excess solar on the building in addition to lower energy performance, maybe you could pair that with some EV chargers that bill the users (visitors only) at a nominal rate and that income could go to pay back the investors.
There's lots of interesting opportunities with co-housing if you apply some out of the box thinking. I've attended a few presentations and conferences and talked to funders about interesting and unique ways to fund green projects since traditional lenders often don't properly take into account the green features.
If builders in your area aren't familiar with exterior insulation, all the more reason to look into pre-fab panelized systems like Collective Carpentry, BuildSmart, and others. Or go with 2x8 studs in your exterior walls instead of 2x6s and skip the exterior insulation. Not ideal but it could work in your climate.
Your suggested approach is good--use a blower door to find the holes, seal the holes, repeat. Here's a good overview on using a blower door: https://www.greenbuildingadvisor.com/article/using-a-blower-door-test-and-interpreting-the-results.
Getting to 5.0 ACH50 shouldn't be difficult at all. Getting to 3.0 ACH50 will take a bit of planning and diligence, but is still straightforward. Once you get that far, getting to 1.0 ACH50 or lower is mostly a matter of perseverance.
I don't design multi-families but those I know who do say that it's much easier to get them to Passive House performance levels than it is with single-family homes.
"I don't design multi-families but those I know who do say that it's much easier to get them to Passive House performance levels than it is with single-family homes."
The bigger the building, the lower the ratio of surface area to volume. Since ACH50 is expressed in terms of the volume of the house it makes sense that bigger houses are relatively easier to seal.
nick_vk,
To get the developer onside you will need to present a plan that shows the volunteer air-sealing will not interfere with the other trades, disrupt the usual sequence of construction, or prolong the build. That's where the conflict occurs, and that's what developers or builders are wary about when owners want to take part in the process.
I have to admit, my plan might be feasible for one or two units but to get 25 done without holding up the train is going to be tough. Hiring a professional team would allow for more reliable scheduling, though it still will stretch out the build some. Any thoughts on conventional sealing vs. AeroSeal if we cam afford to hire it out?
nick_vk,
Aeroseal is limited to gaps of a certain size. You may find it ineffective if there are large voids, and these will also disproportionately affect air-tightness.
1. Owners doing airsealing themselves might be beneficial, but the real problem comes in after you air seal and the builder is trying to finish, and the builder allows someone (electrician, other) to poke a hole somewhere. They only signed up for code min 5 ach, you worked hard to get it down to 3, so no problem for them if sparky cuts a hole, they will still meet 5 ach, and your added work will have been for naught. You need to hold the builder to an airsealing standard that the OWNER checks via an independent third party that the OWNER hires, at the END, after all work is done.
2. Environmental concerns are not the only reason to build a tight house. I can assure you from experience that a tight house is SOOOO much more comfortable to live in. I would not have believed the difference if I did not live in one.
3. Architectural design is one driver in how easy it is to get the house tight.
4. At the end of the day you need a builder who has done air sealing above code before, is willing, and has a clue. Most contractors hire their insulation subs to do the air sealing. I cannot begin to tell you how poorly trained, uninformed, careless and sloppy the insulation subs are, from their management down to the installers. Its discouraging, but that is how it is...
I think the only way to get this done on the cheap is to design in such a way that if built with minimal care, it will still be air tight. For example, you can spec sheathing with integrated WRB which must be taped anyways so you get the air sealing there for free.
There are lot of similar details that with a bit of careful design, it will get you to your goal without breaking the bank.
The hard part will generally be outdoor spaces, unfortunately there is no easy answer there except maybe a lot of spray foam.
I know there is a lot of AeroBarrier work in multi family which might be a good option. If you air seal individual units, along with reducing your ACH@50PA this also gets you tighter air seal between units which is a big bonus for indoor air quality and noise.
Thank you - glad to know that using Aerobarrier in multifamily is a known thing, That could increase the developer's comfort level with it. Certainly makes it reasonable to ask for.a bid.