How to use rigid foam insulation in roof space

Context: Central Pennsylvania. Want to convert vented (sofit and ridge vent) cathedral attic space into conditioned space. No plans to replace the roof. Roof cavities are 7.25″. Cost is important, but so is DIY-ability.
Plan so far: Cut and cobble XPS into cavities between trusses, sealing all the way to exterior wall. Assembly stack spray foamed in place:
1.25” ventilation
2 layers of 3” XPS
1.25″ ISO on inside face covering roof trusses
Comments: R~35-40 is lower than we want, so tempted to remove ventilation space. XPS R-value goes up in cold (crucial for us), but will it suffer in heat under a shingle roof? Will 1.25″ ventilation be enough to help with heat? ISO on inside of assembly avoids its R-value drop in cold, but will that risk trapping moisture in the assembly?
Another possible alternative:
1” ventilation
3.5” fibre-faced ISO OR 4″ double foil-faced ISO
3” XPS
1.25″ fibre-faced ISO on inside face covering roof trusses
Comments: R~35-45. Worried about R-value drop in cold, possible moisture issues from double foil face on ISO, and (as above) ISO on inside surface. Heat is fine for ISO, so maybe replace ventilation with more insulation?
The key questions about this are:
i. What boards to use? In what configuration?
ii. Is ventilation useful in this situation or not?
iii. should I consider blowing in cellulose between foam boards? How thick would my board vapor barrier have to be?
iii. how important is the inner layer for thermal bridging? Will using ISO here cause problems?
Thanks!
Mark
GBA Detail Library
A collection of one thousand construction details organized by climate and house part
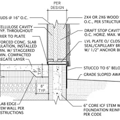
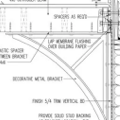
Replies
Mark,
The cut-and-cobble approach is not recommended for unvented roof assemblies. The likelihood of future air leaks with this approach is high; venting the assembly reduces the risk by providing a mechanism to help dry the sheathing.
The purpose of the ventilation channel is not to keep the assembly cool. The purpose of the ventilation channel is to reduce the chance of sheathing rot by providing a path for ventilation drying.
Your XPS won't get hot enough to cause any worries.
You might want to consider switching from XPS to EPS. EPS is more environmentally friendly. (The blowing agents used to manufacture XPS have a very high global warming potential.)
There won't be any moisture issues arising from the two facings on polyisocyanurate.
Don't overthink the question of layers, and what type of foam goes where. In general, including some type of rigid foam other than polyiso toward the exterior will improve cold-weather performance. But even when the weather is very, very cold, polyiso is still a useful insulation with an R-value that exceeds R-4 per inch. It's not worthless.
Including a continuous layer of rigid foam on the interior to address thermal bridging is an excellent idea.
Q. "How thick would my board vapor barrier have to be?"
A. I'm not sure what motivates this question. The cut-and-cobble method results in a low-permeance barrier -- and in any case, there isn't really any need for a vapor barrier in this assembly.
For more on vapor retarders, see Do I Need a Vapor Retarder?
For more on creating insulated sloped roof assemblies, see How to Build an Insulated Cathedral Ceiling.
Thanks, Martin, this is very helpful. The main reason for using XPS is that I found a supplier of used, cheap 2nd-hand XPS.
A side note: I agree with the GHG worry with XPS, and apparently they haven't switched to low GHG blowers yet (or at least Google doesn't know about it). Are there safe/good ways of retiring old XPS?
To reduce the worry about errors and moisture problems, maybe I should apply a very thin layer of spray foam to air seal the roof deck? Does it matter how thick? I was hoping to avoid that with the foam board / spray foam combination, but you're right, it would have to be perfect.
Mark,
If you are including a ventilation channel, you want the roof sheathing to be able to dry quickly. A layer of spray foam installed against the roof sheathing would retard drying -- so that approach is no good, unless you want to switch to an unvented assembly.
Yes, the idea would be, that we could remove the worry about air and moisture leaks through the assembly, and also increase our R-value, by replacing the ventilation with foam.
Or shouldn't I worry much, if we're putting ISO panels on the inside face of the assembly?
Mark,
The correct answer to your question is: If you want to install spray foam against the underside of your roof sheathing -- and I'm not saying it's a good idea -- in order to create an unvented roof assembly, then do it according to the rules.
In your climate zone (Zone 5), the code requires that the spray foam layer have a minimum R-value of R-20. (For more information on this code requirement, see How to Build an Insulated Cathedral Ceiling.) Closed-cell spray foam is less risky in this application than open-cell spray foam.
On the other hand, if you want to create some hybrid approach to an unvented assembly, using cut-and-cobble and spray foam -- what I call the "peanut brittle" approach -- you can. But that approach is riskier, and may not comply with the code.