How to Determine if a Minisplit System is Right-Sized

We’re trying to troubleshoot a heating issue in California (Zone 3C), and wonder about the sizing of the two ducted mini split zones we have. Are they sized wrong?
Our house is from 1961. The second floor has baseboard heaters. The first floor was upgraded with a two-zone ducted mini split system from Carrier, with the head units in the crawl space under the house.
On the first floor, zone one covers the entry, living, dining, kitchen, laundry, and utility rooms, for a total of 1,450 sq ft. Zone two covers the master bedroom and bath, for a total of 350 sq ft. Both zones have 24,000 btu head units. That already seems odd, because the square footage is so different… Read on for, maybe, why it’s like that.
We set a fixed temperature of 67 all winter, day and night. We live in California where it gets down into the low 30s just a couple days a year. Our master bedroom zone has no trouble maintaining the set temperature. Our living area zone mini split maintains the temperature within half a degree as long as it stays above 45 or so at night. By the time it drops below 40 outside, it can’t keep up and it gets up to 5 or 6 degrees colder inside. It takes a few hours after sunrise to catch up, and even then it needs help from some sunshine.
First: is it normal for a right-sized mini split to fail to maintain temperature when it’s cold out?
We had a professional do a full Manual J load calculation and conclude that we need 42,000 btu for the first floor. (I tried to repeat the calculation with CoolCalc, and despite entering every single room one by one, my number was way off from that at 21,000 btu heating and 2.5 ton cooling. I don’t trust my numbers, because I’m not an HVAC professional.) So it seems like 48,000 for the two head units should be enough, overall, though I’m worried about how much difference there is in the square footage that’s covered.
One possible reason for the 24,000 btu unit for the master bedroom is that it has a really long duct run, and maybe having some extra air pressure helps with that?
About the ducts: The head units connect by flex duct to the vents. The duct runs are very long, traveling more than 50′ from the head units to the farthest vents. I guess the reason is that it was difficult to move the head units through the crawl space to get them any closer. It probably would be possible to put them closer if that would help.
So I guess the questions are:
* Is it possible that everything is actually fine, and we’re just new to mini splits and find it odd that the temperature drops an extra 5 degrees at night when it’s cold?
* Or does it sound like an undersizing problem, like maybe we should have a smaller head unit for the master bedroom, and a bigger one for the main living area? Carrier makes a 36,000 btu.
* Or might it be the length of duct runs that’s an issue, and if we could shorten them by 50′ that might fix it? Or something else?
Any thoughts appreciated!
GBA Detail Library
A collection of one thousand construction details organized by climate and house part
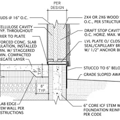
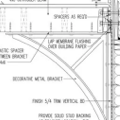
Replies
24000 btu for 1450 sqft is not too small, if the house has minimal insulation.
What are the models of your outdoor unit and indoor units? What is the distance between the outdoor unit and indoor unit? Do two indoor units share one outdoor unit?
(1) Long ductwork may be one possible root cause.
(2) If two indoor units share the one outdoor unit, If the distance between the outdoor unit and zone one indoor unit is longer than 25 feet, there will be some level of capacity loss. For instance, a 24000 btu unit may only cool or heat like 18000 btu unit. If the distance between zone two and outdoor unit is short, the capacity loss on zone one will be even more serious. In a multi zone mini splits, if an indoor unit that has much longer long line sets that other units, its cooling and heating capacity will be deteriorated.
My suggestion is that for zone one, install a small 3/4 ton or 1 ton unit (ducted or wall mounted or floor mount) at the right location. The location should chosen based on the layout of the house.
Do the two units share the same outdoor unit? If so, there might be an issue of providing enough of the outdoor unit's capacity to the unit that can't keep up.
One option to solve the problem might be to add a branch duct from the bedroom unit to supply the other space--not sure if that's reasonable with the duct lengths, etc.
But a nicer solution would be to look at where your heat loss is coming from and address that. For example you might have a lot of air leakage, which comes in at the ground floor and exits upstairs somewhere. That will make that ground floor heat load include heating all the incoming cold air for the whole house. Finding and sealing the major air leaks in at the bottom and/or out at the top can help.
@hoverda, the models are:
Outdoor unit: Carrier 38MGRQ48E
Indoor units: Carrier 40MBDQ 24k
Yes, the indoor units share the same outdoor unit. Both indoor units are about 45 ft from the outdoor unit.
As for the insulation, it's not too bad -- except for about 150 sq ft of single pane glass picture windows. The other windows have been replaced with double pane low-E.
@charliesullivan, yes, the indoor units share the same outdoor unit. Both indoor units are about 45 ft from the outdoor unit.
And you made me realize I forgot an important detail. That main living area has an open staircase to the second floor. The upstairs is about 1,200 additional square feet. It's got baseboard heaters, but we tend to keep them off or set lower because they're expensive to run.
Last detail: there isn't much air flow coming through the vents in the living area. There are 6 vents coming off of that indoor unit. You can barely feel the air even with your hand right on top of the vent when it's on all the way. The bedroom zone has only two vents, and you can definitely feel the air flow. There don't seem to be any obvious leaks in the flex duct, but who knows?
It seems to me if you have 48,000 btu of heat and 1800 squ feet you should be able to heat the place with the window open if the equipment is working correctly. Start by measuring the air temp coming out of the units it should be more than 15° warmer than the room air if not have the units checked.
Walt
> we need 42,000 btu for the first floor.
Did I follow correctly? The Manual J said 42,000 for a zone and you installed 24,000 and are wondering why it can't keep up?
+1 on either ducting from the over-sized unit to the under-sized unit area (with a duct booster fan if needed) or installing another mini-split.
42000BTU is the heating load for a leaky 30 year old code min 1800sqft house in my neck of the woods (zone 5). No way that is correct. Even if we add in the 1200sqft of 2nd floor, it is sill on the high side.
You have two issues. The bedroom zone with its own 24k unit is way over sized. It can work but some of that capacity should have gone to the rest of the house. It would have been better to at least go for a 36k+12k combo.
The 2nd problem is your main floor unit is effectively heating 1450+1200 sqft. With an open staircase, generally the main floor unit does the bulk of the heating in a two story structure.
A 24k head should still be able to heat 2650 in your climate, so I'm guessing there are also some significant air leaks in the house. This would also explain why your main floor cools down overnight. Stack effect brings in cold air through the air leaks, you would have to put a silly amount of heat into the place to get any comfort in that situation.
I would look at air sealing the place first before troubleshooting any HVAC. This would most likely fix this issue but also save on your energy costs.
It also sounds like you have a distribution issue with the main floor unit. You should feel some flow out of the ducts. I would look for kinked pipes and loose connections. I'm not surprised you are seeing a lot of flow on the upstairs registers, after all you are trying to push around 1000cfm through a couple of pipes.
Thanks, everyone! I think I've got a few answers and suggestions.
To summarize:
1. Yes, the overall system should be sufficient to heat and cool the place.
2.. Seal up any air leaks in the house and see if that fixes it.
3. Measure the air temp coming out of the living room vents to make sure it's warm enough. (Done. Seems warm, just not much air flow.)
4. Measure the air flow coming out of the living room vents and if it's low, check for kinks or loose connections. (Not sure how to do this; might need a professional.)
5. 36k + 12k probably would have been better than 24k + 24k. (An expensive change :-)
6. The indoor units should be placed closer to the vents. (Probably possible.)
7. We could add an extra vent in the living area, connected to the duct from the bedroom unit, to balance them out. (This is possible.)
For everyone who offered ideas:
@walta100, thanks for the suggestion to measure the temperature coming out of the vents. It feels warm enough, so at least I can rule that out.
@jon_r, sorry if I wasn't clear. The Manual J calculation came out to 42,000 for the whole first floor -- which is the space covered by the two 24,000 btu indoor units, so 48k total. It's just that it's not split up into two equal-sized zones. It's 350 sq ft vs 1,450 sq ft (+ 1,200 more upstairs).
@1at, a leaky 30 year old structure sounds about like my house, haha. It's 60 years old with lots of single-pane glass. So maybe that 42k is about right.
Thanks, everyone! Happy New Year!
>"We had a professional do a full Manual J load calculation and conclude that we need 42,000 btu for the first floor. (I tried to repeat the calculation with CoolCalc, and despite entering every single room one by one, my number was way off from that at 21,000 btu heating and 2.5 ton cooling. I don’t trust my numbers, because I’m not an HVAC professional.)"
I trust your numbers way more than the HVAC so-called "pro" in this case. Akos has it right- that number is absolute crap, even with the 150' of single panes.
> It's just that it's not split up into two equal-sized zones. It's 350 sq ft vs 1,450 sq ft (+ 1,200 more upstairs).
So it's really 350' + 1450' + 1200' = 3000 square feet of total conditioned space? And you have a 2 ton cassette serving the 350' zone? (I R confoosed.)
My 2x4 framed sub-code 1920s antique is comparable the size of your house (2800' + 1600' of insulated but not fully-heated basement) and has a 99% heat load (at +5F outdoors, +70F indoors) of less than 40,000 BTU/hr. The 99% outside design temps in most of 3C CA are north of +30F- if you moved my house to a location with a design temp of +30F it would come in around 20,000 BTU/hr.
The 99% and 1% design temps for all CA cities and towns are listed here:
https://higherlogicdownload.s3.amazonaws.com/ACCA/c6b38bda-2e04-4f93-bd51-7a80525ad936/UploadedImages/Outdoor-Design-Conditions-1.pdf
So what are your actual design temps? Do they match the design temps used in the "professional" Manual-J?
>"So maybe that 42k is about right."
There is glass in those windows, right? I suspect even your 21K number is actually higher than reality, even with a very leaky or fully vented crawlspace.
Is it a vented crawl space? Is it a pier foundation with/without skirting? Air sealing the walls of the crawl space as well as the attic floor would dramatically lower the stack effect air infiltration that may induces comfort & temperature balance issues, especially if the first floor is getting cold. Warm air will otherwise leak out the top of the house (making the upper floors warm), but depressurized the crawlspace and lower floor, sucking air in. But even that isn't likely to boost the total load north of 40K, or even 30K. If it's truly that leaky it should be dead-easy to thottle it back to something sorta-reasonble.
The output capacity of a single 1.5 ton 38MAQB18R at your outside design temp is about 24,000 BTU/hr, and would probably cover the whole-house load:
https://ashp.neep.org/#!/product/33267
The 2-ton compressor in that series is good for about 30,000 BTU/hr, and would almost certainly cover the load:
https://ashp.neep.org/#!/product/33600
The 4-tonner is good for something like (a ridiculous) 45-50K at your likely design temp:
https://ashp.neep.org/#!/product/26252
If the system isn't keeping up it's likely to be improper duct design, or duct leakage.
FWIW: Adding low-E exterior storm windows to your existing windows will bring the performance up to current IRC code levels at a fraction the cost of replacement windows. That would lower both your heating and cooling loads by a good chunk . At 35F temperature difference the 150' of single-pane represents about 5250 BTU/hr of loss, and on cold nights there will be a noticeable draft of cool air cascading down the face of the glass inducting a bit of wind chill if sitting/sleeping next to the window. Adding low-E exterior storms would reduce that loss to about 1500BTU/hr, and the surface temp of the interior side glass would be more than 10F warmer at the 99% design condition.
A single hard coat low-E on the interior surface of the exterior glass also cuts the solar gain by about half, with very little change in visible light transmission. That combination of glazing also makes the windows net heat gainers when the outdoor temps are cooler than the indoors, despite the now lower peak solar gain.
In order of importance, the remediation to the house should be:
1: air sealing, concentrating on the leaks at both the top & bottom of the house. Big leaks come first (like vents in the crawl space, flue & plumbing chase that go through the attic, recessed lights pentrating the attic floor, band joist & foundation sill on your now-sealed crawlspace, etc.)
2: more air sealing
3: even MORE air sealing. which depending on the budget may include tightening up the windows with exterior storms. Window leakage around the sashes is pretty obvious stuff to fix, but less obviously the CASING TRIM around the windows is often higher leakage than the operable sashes themselves.
It might also include dense-packing cellulose over any batt insulation in the walls, also depending on the budget, which would be doing a bit more than #4 & #5:
4: Adding insulation where it's easy.
5: Upgrading windows.
You may find Nate Adams' video primers (covering some of what's in his book chapters) a useful place to start:
http://www.natethehousewhisperer.com/home-comfort-101.html
http://www.natethehousewhisperer.com/hvac-101.html
http://www.natethehousewhisperer.com/hvac-102.html
He also has a YouTube channel covering relevant topics in much greater detail. While his service area is in a much cooler climate than yours (zone 5A), the principals remain the same.
Even though ridiculously oversized for your zone loads, the 4-ton 38MGRQ48E heat pump has a fairly good modulation range, and should be able to modulate down to something reasonable most of the time. While a more appropriately sized system for the real loads would be more efficient, the low end of the modulation range is still low enough for comfort.
Thanks, @DanaDorsett. Yes, the total house is about 3000 ft2. The downstairs is 1800, which is the area covered by the mini splits.
Design temperatures are 40 heating, 78 cooling. Very mild.
I spent a LOT more time on CoolCalc, and I can find no way to get the heating load as high as 42000 btu for the first floor. The HVAC pro did not share the Manual J calculation with me, just the final number.
If I assume the worst, and plug those values into CoolCalc, I get 26,669 btu for the whole first floor + upper hallway. The remaining upstairs rooms, which are separately heated, require another 12,991 btu. That comes to 39,660 btu to heat the whole house. We have a lot of windows, and some rooms have exterior walls on 3 sides.
Based on this, you (and others on this thread) are 100% correct. Our existing ducted mini splits should be way more than adequate. The bedroom zone is ridiculously oversized. It only needs 6,671 btu and it has 24k. The main living area is sized about right, with 24k when Manual J says 19,998 btu.
Sounds like we should invest in some air sealing. Right now the attic has only 6" of insulation, because the joists are 2x6s. The insulation isn't even stapled in place, and there's no air seal over it. Sounds like this is a good place to start.
The crawl space has several vents around the perimeter, with no insulation or air seal on the walls or under the first floor. This is another obvious area for improvement.
And we will look into upgrading the single pane glass. The single pane stuff is literally just sheets of glass held in place with caulk and wood trim. A local glass place can sell us double pane low-E and swap out what's there. Might be about the same price as storm windows, and keep the same style.
Deleted
Playing around on CoolCalc, I find some interesting things:
* lowering the air infiltration from "loose" to "semi-tight" could lower the heating load by 8,000 btu
* replacing the remaining single pane clear glass with double pane low-E could lower the heating load by 7,000 btu
Those numbers are for the whole house, so not all of it would count for just the living room zone. Still, it's a huge difference at 15,000 btu total. The benefits for cooling are just as substantial.
An update on this: when we installed our 2nd floor HVAC system, the installer took a look at our first floor unit. They identified 2 major problems that are fixable:
1. It's a 2-ton Carrier mini split. It has a static pressure setting, SP1 - SP4. The default is the lowest. The installer didn't change the default to a higher setting, which meant that there just wasn't enough pressure to deal with long duct runs. We changed the setting, and then the return air duct started whistling. That's the second problem.
2. The return air was inadequate. The system had two 8" flex ducts, but both were connected to a single stud bay, with a weird kink and angle at the base, and then constricted by an opening that's only about 11" x 3.5" at the bottom of the stud bay. Not enough air for a 2 ton air handler.
We hired an HVAC tech to move the air return to a different wall, and took over some space inside a closet, so that we could get a 12" return duct. That fixed the air pressure constriction, and the whistling noise is gone.
Even now, we probably don't have adequate return air. There are 6 supply registers, 4x14. The duct runs are very long, through an unconditioned crawl space. Two 8" returns (connected to a single 12" duct) is probably not enough.
We have a reasonable spot where we could put a second air return: we could cut through two adjacent stud bays with a 24x14 grille straddling them, and connect another 2 x 8" flex ducts. The location is closer to the air handler, so it's likely to pull in more air than the current return even by itself.
Given how long the duct runs are, and that it's not a very high static system, even adding another air return might not make a big difference. But seems like it can't hurt to add another air return. It costs a few hundred dollars here to have someone do it.
Has anyone added a second air return and seen a big improvement, even when there wasn't obvious noise at the first air return?