How to tell if a contractor knows how to build air tight?

I’ve been reading a lot of the content in the blogs here and the recurring theme seems to be that the tighter you build the home the better the energy efficiency. However I’ve also seen indications of nightmares caused by homes having been improperly built thereby trapping in moisture and causing rot.
So my $10,000 question (hopefully not literally) is how do you determine if a contractor you’re considering hiring really knows how to properly build an air tight home?
What questions should you ask?
What things should you look out for in their answers that might tip you off that they may not truly know what they’re doing?
This part of the construction seems so critical to the efficiency of the home and it’s long term structural integrity that I really want to get it right…
thanks,
Jay H
GBA Detail Library
A collection of one thousand construction details organized by climate and house part
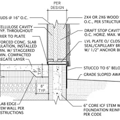
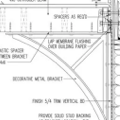
Replies
Great question, Jay. I look forward to the experts' advice as I'm in a similar spot as you are. But I'll share what I've been doing:
I check credentials, using their blogs, websites, etc (figuring that someone who professes to be 21st century building savvy probably has info about himself posted online ... speaking personally, someone who can't/won't promote that way is waving a red flag at me.) I contact the accrediting agencies and see if they're members -- locally, the builders I'd be interested in are, for example, members of RESNET, and EarthCraft.
I interview them -- they can talk fluently about what they do, and why, and have a list of references they are eager to share -- of course they wouldn't volunteer someone who was dissatisfied, but ....
And I tour their projects at different stages. I'm not at all qualified to spot a minor mistake but I can catch poor insulation or someone who says "ADA" but has unsealed, standard electrical boxes.
When I get closer to building, I'll try to contact some of the experts on here who are in the region to ask them if they've heard of them, know anything, etc. And I'll take their reputation in the local building community seriously as well as the opinion suppliers (eg, lumberyards) have of them. I liked it for example when I mentioned a name at the desk of a local yard and the old school guy on duty said "Oh yeah, he's a good guy. He uses all this new crap in his projects. We get it for him, but ..."
Nothing technical here obviously, but I'll watch the conversation here to see what specifics the experts have.
Regards,
Joe
For judging Airtightness alone
You could ask to see blower door test results.
And of course you know that good airtightness does not guarantee a good structure
It is just one of many components.
Hopefully you guys aren't also looking for the low bidder too!
To get a good, airtight shell, I'd start by making sure the plans are detailed with all of the measures you want taken. If you don't want 59-cent blue plastic electrical boxes, find the ones you do want and list them. If you want taped sheathing or EPDM gaskets or anything else, show it on the plans. Show specifically where everything goes. You certainly need experienced tradespeople to execute some of the details, but your chances are a lot better when the plans show everything you want done. I've tested some new construction in the past month or so... some of it pretty good, some of it not... and in no case were there air-sealing details on the plans.
And, look for someone who owns a blower door. Nothing changed my understanding more than buying a door and a few other things for my own use.
The flashing and other moisture management details are more commonly understood, but I would include those on the plans too.
All that--combined with an adequate budget--should get you there.
Jay,
Am I to assume that you have a good set of plans from a knowledgeable and experienced Architect or Designer, one who has provided you with a complete set of plans, including good framing, thermal bypass, moisture management and ADA details?
All of those details form your tight construction. 90% of and effective energy efficient, high performing building is in the details. You can teach almost any builder or subcontractor w/o the knowledge or experience with good sets of drawings than one without. So maybe your $20,000 question is if you are starting with a good Architect or designer and good set of drawings.
Great question - do the same to your potential builder - challenge him - ask him how he gets his air tightness - how many ACH he shoots for, how he controls moisture, etc. Ask if they have taken any classes on green building or building science. You seem to be on the right track.
You could also ask who his 3rd party rater is and contact them to get their opinion.
Great advice above by all - important to get the details on the plans.
Jay,
I will pass along a question from Dr. Joe over at Building Science Corp. - Doing the wrong things right is still wrong, right? Any builder can do wrong things really good, but the fact remains that wrong is still wrong no matter how perfectly it is executed. Dr. Joe follows this question by explaining the difference between quality assurance (knowing the right things to do) and quality control (making sure quality assurance is verified in the field and corrective action(s) are properly carried out). Third-party verification is always a plus.
This entire site is dedicated to improving the quality of the homes we build. Use this site for your own education (you should also check out buildingscience.com). An educated homeowner/homebuyer can work with a contractor to improve quality. A quality builder should not be offended by an educated client.
Details and testing are needed and valuable, but I would start with a contractor who understands and embraces integrated design. The integrated design process would include the owner, and, most importantly makes sure everyone is on the same page BEFORE the project begins - and everyone understands their stake in the outcome of the project. If you are unfamiliar with the ID process, study all you can about it. If you are having trouble finding detailed information, give me your email address and I will send you some information.
Jay,
Ask the builder, "Who does your blower-door testing?" Most builders use a local rater. Talk to the rater and ask about the builder's reputation, and ask how tight his or her homes are.
Ask the builder, "What were your blower-door results for the last three homes you built"? And ask to see the written results of the blower-door tests.
Needless to say, if the builder says something like, "Oh, I build real tight but I don't need to have my homes tested," find another builder.